Trois questions à Alexandre Romaine, spécialiste de la corrosion
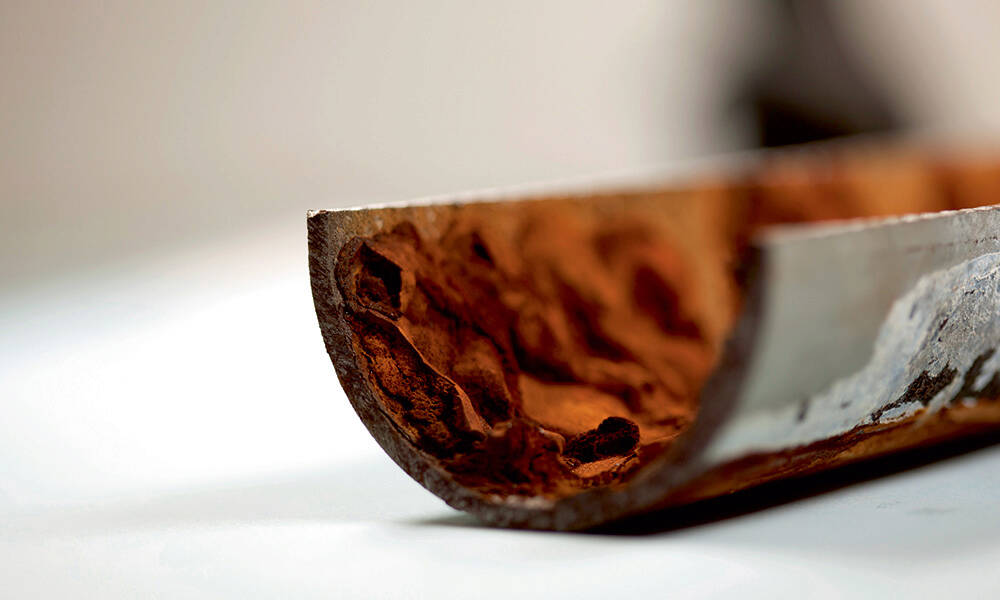
Quels sont les principaux dangers posés par la corrosion dans l’Oil & Gas ?
Alexandre Romaine : La corrosion est responsable d’une grande partie des défaillances matérielles de ce secteur. Les fluides agressifs contenant de l’hydrogène sulfuré (H2S) et le CO2 en sont une des principales causes. L’H2S entraîne, par exemple, une fragilisation des matériaux par l’hydrogène ce qui peut causer des ruptures. Néanmoins, la corrosion reste un processus complexe pouvant avoir de multiples origines dont il est crucial d’identifier la nature afin de prévenir des risques de rupture. Les soudures sont également fortement touchées par la corrosion dans ce secteur et nécessitent un intérêt particulier. Limiter ces effets tient d’un choix de matériau, du design, des process d’assemblages et de leur bonne exécution ou encore de l’utilisation des tubes (casing, tubing et line pipe). L’enjeu est double : identifier et qualifier les bons matériaux en conditions de fonctionnement afin de garantir la sécurité des installations, tout en réduisant les coûts de production.
Qu’en est-il de la prévention des risques de corrosion en phase de fonctionnement ?
AR : L’objectif ici est d’anticiper les problèmes et d’évaluer la durée de vie résiduelle des systèmes en place. La difficulté est que ces équipements sont souvent inaccessibles une fois installés, car ils sont en profondeur. Les méthodes de suivi les plus adaptées pour les installations existantes reposent alors sur du contrôle non destructif (CND). Par exemple, le recours à la radiographie ou aux ultrasons pour détecter les zones d’attaque de la corrosion sur les pipelines.
Cette inaccessibilité souligne aussi l’intérêt de mettre en place des systèmes de monitoring de la corrosion en temps réel. Pour cela, il est primordial de penser aux dispositifs de collecte de données en amont afin de tester leur adaptabilité au milieu d’usage.
Le secteur de l’Oil & Gas s’ouvre à l’exploitation de l’hydrogène. Quels sont les principaux enjeux et verrous à lever ?
AR : Industriellement, le retour d’expérience vis-à-vis de la tenue des matériaux en milieu hydrogène gaz et liquide est encore relativement faible. Les industriels ont besoin de nouvelles connaissances sur les interactions matériaux/hydrogène et d’éventuels revêtements barrières ainsi que des méthodes de contrôles et d’analyses de défaillance adaptées. Le secteur étant en pleine effervescence, il est possible de développer simultanément aux nouveaux dispositifs, des solutions de monitoring sur la détection et la caractérisation de ruptures propres à ce secteur.
Plus largement, il est nécessaire d’évaluer la possibilité d’adapter les systèmes existants à l’exploitation de l’hydrogène et de rechercher de nouveaux matériaux dédiés, les tester et normaliser ces nouvelles pratiques, en prenant en compte l’aspect économique. C’est un des objectifs de HyMeet, le programme stratégique du Cetim sur l’hydrogène qui associe un programme R&D ambitieux au service des industriels à un investissement de 25 millions d’euros. Ce projet majeur mobilise déjà près de 100 collaborateurs et s’appuie sur les 50 ans d’expérience et l’expertise pluridisciplinaire du Centre.
L’expert Cetim :
Alexandre Romaine est titulaire d'un doctorat en sciences des matériaux avec une spécialisation en corrosion et électrochimie. Il travaille comme ingénieur en corrosion et protection contre la corrosion au Cetim, principalement dans le domaine des matériaux métalliques. Il possède une expertise dans le suivi de la corrosion, l'analyse des conditions de service, les mécanismes d'endommagement par corrosion, la caractérisation morphologique, le choix des matériaux et de la protection contre la corrosion et l'analyse des défaillances.