Traitements thermiques superficiels : comparaisons et matrices de choix
Par Claude Leroux, Ingénieur conseil
Renforcer les performances mécaniques d’une pièce. Un objectif atteignable via les traitements thermiques superficiels tels que la nitruration, la nitrocarburation, la cémentation, la carbonitruration ou encore le durcissement par trempe après chauffage superficiel. Mais comment faire le bon choix ?
Nitruration, nitrocarburation, cémentation, carbonitruration et durcissement par trempe après chauffage superficiel : ces traitements font partie des traitements thermiques superficiels dont le but est de renforcer les performances des pièces mécaniques. Ils apportent de la dureté superficielle, un durcissement en profondeur et des contraintes résiduelles de compression en surface. Le choix de ces traitements repose sur la connaissance de leurs performances face aux sollicitations des pièces mécaniques sur lesquelles ils sont susceptibles d’être appliqués. S’ajoutent à ces critères de conception des critères industriels se rapportant à la mise en œuvre de ces traitements en termes de coût, de facilité de mise en œuvre, de choix des matériaux. Après avoir listé les principales sollicitations concernées, ce texte se propose de fixer un certain nombre de critères de choix.
Sollicitations des pièces mécaniques
Les pièces mécaniques ont besoin d’être résistantes à l’usure, à la fatigue, au chocs, aux effets de la température, à la corrosion, au frottement des surfaces. En rappeler le sens est toujours utile pour mieux choisir les moyens d’y parvenir.
Usure
Ce terme très général peut intégrer tous les modes de détériorations y compris la fissuration par fatigue. En fait on sous-entend généralement par usure un endommagement de la surface. On mesure d’ailleurs l’usure par perte de poids et perte de cotes. Cet endommagement peut résulter de différents processus.
• Abrasion par effet du milieu de fonctionnement. On parle d’usure par un troisième corps dont la nature (forme, dureté) et le mode de circulation conduit à une abrasion par égrènement du ou des substrats en contact. Typiquement, cette usure se rencontre lors d’un fonctionnement dans un milieu abrasif contenant par exemple du sable (cas des excavations). Une telle usure ne s’arrête jamais, les solutions les plus résistantes sont celles qui apportent le maximum de dureté et celles qui offrent une structure contenant des éléments très durs comme les carbures. Les durcissements superficiels retardent ce type d’usure jusqu’à ce que la couche durcie soit consommée.
• Frottement contre un antagoniste de dureté plus élevée et d’état de surface défavorable. Le processus de rodage parfois recherché correspond à ce type d’usure. Pour qu’il y ait rodage, c’est-à-dire une faible usure par érosion ou par déformation plastique jusqu’à obtenir une adaptation des deux surfaces par amélioration des états de surface, il doit y avoir un écart de dureté entre les deux surfaces, la plus rugueuse étant la moins dure. Dans cette configuration, la surface la plus dure et de meilleur état de surface contribue à user la surface la plus tendre qui prend alors l’état de surface de son antagoniste. Cette description se résume dans la règle « faire frotter du bois dur sur du bois tendre ». Toutefois une condition doit être respectée, c’est celle d’une évacuation rapide des débris émis par une lubrification efficace ou des vidanges fréquentes pendant la phase de rodage faute de quoi l’usure de type troisième corps intervient. Si les états de surfaces sont inadaptés, si la lubrification est insuffisante, si la surface la plus rugueuse est la plus dure, l’usure se poursuit.
• Erosion et ou érosion/cavitation. L’érosion provient de la circulation d’un fluide à grande vitesse véhiculant des particules abrasives, elle se rencontre notamment sur les composants hydrauliques travaillant à haute pression avec des huiles insuffisamment propres ou mal filtrées. La cavitation résulte de l’emprisonnement de fines bulles de gaz dans un fluide et de l’implosion de ces bulles au contact de la surface produisant un arrachement de matière. Les particules ainsi émises vont amener une usure par érosion. S’il n’y a que la cavitation seule, la surface prend un aspect caractéristique d’usure par piqûres. Ce phénomène se rencontre sur les hélices de propulsion dans l’eau. Sur les composants hydrauliques l’érosion/cavitation provient d’un défaut de gavage.
Adhésion (adhésion-grippage) ou usure par jonctions intermétalliques
Des jonctions intermétalliques entre les deux matériaux antagonistes peuvent intervenir par suite de la destruction des couches protectrices de type oxydes. Au contact des mailles cristallines sous l’effet des pressions de travail des températures très élevées se développent et des jonctions se produisent qui, selon leurs caractéristiques mécaniques, peuvent se déchirer soit à l’interface d’origine soit avec arrachement et transfert de matière d’une surface vers l’autre. Les structures hexagonales dont les énergies de cohésion sont plus faibles que les structures cubiques sont moins sensibles à l’adhésion. On peut parler de micro-grippage.
Déformation plastique – fluage
Si les contraintes triaxiales de compression sont suffisamment élevées pour provoquer le fluage du métal comme on peut l’observer sur des dentures d’engrenages cémentées trempées, nitrurées ou trempées superficiellement où l’ensemble de la couche durcie a flué sans se rompre par suite d’une dureté insuffisante de la sous-couche ou d’une couche durcie insuffisamment profonde. Ce phénomène s’amplifie grandement avec l’élévation de la température qui s’accompagne d’un affaissement des caractéristiques mécaniques.
Petits débattements
Les petits débattements ou contacts vibratoires sont à l’origine de différents dommages (on considère que ce type d’usure est le principal dommage des pièces mécaniques) :
• Production de poudre rouge par corrosion de contact (ou fretting corrosion). Elle résulte de micro-déplacements générés le plus souvent par des effets vibratoires en relation avec le niveau de serrage des surfaces en contact en milieu aéré. Elle conduit dans un premier temps à l’adhésion, au grippage rendant la démontabilité difficile, à l’usure par émission de débris et éventuellement à la fissuration par fatigue sous l’effet d’un processus de corrosion/fatigue. En milieu non aéré, il n’y a pas production de poudre rouge mais l’adhésion se produit néanmoins.
• Matage ou martelage rencontré typiquement sur les emmanchements cannelés.
• Brinilling ou formation d’empreintes résultant de contacts permanents sous certaines fréquences, comme on peut le rencontrer sur des roulements à billes immobilisés en rotation (cas du transport des véhicules roulants).
La fatigue
La fatigue (ou endommagement avec la durée de fonctionnement) peut prendre la forme d’une :
• Fatigue massive sous l’effet des sollicitations et de leur spectre de répartition (flexion, torsion, traction, cisaillement répétées, alternées, ondulées, combinées…).
• Fatigue superficielle rencontrée avec les contraintes de roulement (dites contraintes hertziennes) développant un cisaillement superficiel en sous-couche. L’intensité de la contrainte de cisaillement croît à partir de la surface pour atteindre une valeur maximum à une profondeur en relation avec le module d’élasticité du matériau déterminant une empreinte de déformation élastique et la valeur de la pression de contact (figure 10). La valeur de la contrainte de cisaillement est égale à 0,3 fois la pression de Hertz et la localisation de la profondeur de cisaillement maximum est égale à 0,8 fois la demi-largeur de l’ellipse de contact. La courbe d’évolution de cette contrainte de cisaillement s’établit par calcul.
Chocs
Les chocs sont en relation avec la ténacité du matériau. La tenue aux chocs révèle la sensibilité à la rupture par chocs.
Les effets de la température
Ils conduisent au fluage et à la fatigue thermique.
Le frottement des surfaces
Les effets multiples (rodage, broutage, usure, grippage) résultent de la nature des matériaux, des états de surface, des conditions de fonctionnement : pression, vitesse, lubrification qui déterminent le coefficient de frottement. Le dommage le plus spectaculaire et le plus définitif est le grippage. Il est lié à une véritable soudure des matériaux des surfaces. Cette soudure se produira si la dissipation d’énergie est élevée (effet majeur du produit Pression ¥ Vitesse) et si les matériaux présentent un domaine de solubilité. Il est évident que ce phénomène comme beaucoup d’autres interactions superficielles sera résolu par interposition d’un film isolant les surfaces en contact comme cela se produit dans le cas d’une lubrification continue ou l’existence d’un film assurant l’insolubilité des matériaux comme cela se réalise avec une couche de combinaison obtenue par nitrocarburation.
Corrosion
Elle revêt différentes formes. La protection contre la corrosion peut faire intervenir des systèmes de protection cathodique ou sacrificielle (le potentiel du système de protection est inférieur au substrat) ou de protection anodique étanche (le potentiel du système de protection est supérieur au substrat, il faut donc garantir une étanchéité parfaite pour ne pas corroder le substrat au profit de la protection).
Caractéristiques requises pour répondre aux sollicitations
Les caractéristiques mécaniques mesurées généralement par des essais mécaniques telles que Rm, Re, A%, Résilience, K1C, interviennent sur la résistance à la fatigue et la résistance aux chocs.
La dureté reliée directement à la résistance, principalement la dureté superficielle avec la nature de la structure métallurgique conduisant au niveau de dureté, est le principal facteur de résistance à l’usure.
La nature physico-chimique de la surface : détermine le comportement au grippage, à l’usure par petits débattements, à la corrosion… Les gradients des caractéristiques en profondeur à partir de la surface sont nécessaires à la résistance à la fatigue de surface.
Le comportement thermique de la solution affecte la résistance et usure à chaud.
Le choix d’un traitement superficiel est destiné globalement à :
1. Obtenir une dureté superficielle élevée sur une certaine profondeur. Le choix de la profondeur durcie doit répondre à différents critères :
• Si l’usure ne peut pas être évitée, ce qui est souvent le cas, il faut se poser la question de la valeur de l’usure acceptable. Si la profondeur intervient sur la durée vie fonctionnelle : à partir de quelle profondeur d’usure la pièce devient hors d’usage ?
Un moule pour objets en béton, des plaques de blindage de grenailleuses pourront accepter des usures de l’ordre du mm, la cémentation sera donc plus adaptée que la nitruration.
Des tiroirs de distributeur hydraulique ne pourront accepter aucune usure la nitruration sera un bon choix. Si la remise en état par rectification est envisagée sans effectuer un nouveau traitement thermique, comme dans le cas des cylindres de laminoirs, il faut garantir le niveau de dureté requis à la nouvelle cote, la trempe superficielle sera le bon choix.
• Dans le cas d’une recherche de résistance à la fatigue massive, le choix de la profondeur est plus complexe, il repose le plus souvent sur l’expérience et sur des règles empiriques du type « profondeur durcie sur un axe soumis à des contraintes de flexion cisaillement, égale à 10 % du diamètre ». Dans le cas de concentrations de contraintes, il est envisageable de superposer aux répartitions des contraintes déterminées par éléments finis le régime des contraintes résiduelles estimé. Généralement on teste des solutions validées après essais de fatigue au banc.
• Dans le cas des contraintes de Hertz (roulement) il est facile de calculer la répartition du gradient des contraintes de cisaillement. Après avoir déterminé le niveau de résistance en fatigue par cisaillement de la limite conventionnelle de couche traitée, on détermine la profondeur nécessaire en croisant les valeurs données par le traitement et la répartition des contraintes (figure10).
La valeur de la profondeur de cisaillement impose implicitement le type de traitement à choisir, une profondeur de l’ordre du 1/10 mm permet de choisir parmi les traitements thermochimiques alors qu’un cisaillement profond conduit à ne pouvoir choisir que les solutions de trempe superficielle.
2. Concilier résistance superficielle – résistance à cœur – résistance aux chocs : dans ce cas le choix de la nuance d’acier est essentiel. La résistance à cœur est obtenue soit par un traitement préalable (nitruration, trempe superficielle) soit lors du traitement superficiel lui-même (cémentation, carbonitruration).
3. Mettre la surface en compression, la superposition d’un gradient résiduel de compression à un gradient de service en traction conduit à un régime dans lequel les contraintes s’ajoutent algébriquement. Les contraintes de traction dommageables se trouvent ainsi réduites. Les traitements superficiels de type cémentation, nitruration (figures 11 et 12), durcissement par trempe superficielle ont précisément pour effet de mettre les surfaces traitées en compression.
Parmi ces conditions s’ajoutent la facilité de mise en œuvre proprement dite et la disponibilité du procédé incluant l’usinabilité du matériau employé (niveau de carbone, structure et dureté), les possibilités d’épargnes, les possibilités de reprise après traitement, l’aptitude aux finitions (rectification, traitement de surface…) et la reproductibilité des variations dimensionnelles, après traitement. Le tableau 1 ci-dessus compare les principales étapes des différents traitements.
Le plus souvent la nitruration aura lieu sur un état trempé-revenu. Si ce traitement est effectué avant ébauche, il y a lieu de faire une stabilisation pour relaxer les contraintes au stade de l’ébauche proche de l’état final. Si la trempe et le revenu sont réalisés sur ébauche ce traitement tient lieu de relaxation des contraintes. Les températures de revenu et/ou de stabilisation doivent être compatibles avec la température et le temps de nitruration.
La rectification d’une couche nitrurée est plus délicate que pour les couches cémentées. La plus faible profondeur des couches nitrurées limite l’épaisseur de rectification.
Les durcissements par trempe superficielle se font autant sur des états recuits que sur des états trempés revenus sous réserve de limiter le niveau de résistance à des valeurs de l’ordre de 1200 MPa (à déterminer selon la nuance d’acier).
Ce sont naturellement les états recuits et spécialement après recuit isotherme qui sont les plus favorables à l’usinage. Pour les nitrurations et trempes superficielles, il est fréquent d’employer des aciers dans un état thermomécaniquement contrôlé (aciers à dispersoïdes). Les déformations, problème majeur des traitements thermiques, sont en relation avec la reproductibilité des paramètres de traitement et des opérations en amont (le matériau et sa mise en œuvre) et les variations volumiques en relation avec les transformations métallurgiques. Les variations les plus importantes sont obtenues avec la cémentation et la carbonitruration qui conduisent à des martensites ayant les plus grandes teneurs en carbone. La profondeur intervient bien évidemment. Des masses importantes de pièces de précision sont cependant utilisées sans retouche après carbonitruration peu profonde comme les engrenages de boîtes de vitesses d’automobile. Pour les traitements de nitruration et nitrocarburation dans lesquels il n’intervient pas de transformations de phases, les variations dimensionnelles sont très faibles si la mise en œuvre a été bien faite. Seul le gonflement de la croissance des couches de combinaison doit être pris en compte, il est de l’ordre de 30 % de l’épaisseur de cette couche. Une couche de combinaison de 20 µm conduit à un gonflement par face de 6 µm soit 12 µm au diamètre.
Choix, conditions et propriétés
Le tableau 4 propose des pistes pour choisir les matériaux (aciers, fontes graphitiques, alliages de titane) et les traitements adéquates.
On observe que ce sont les nitrurations et nitrocarburations qui offrent le choix le plus large.
Le tableau 5 présente les conditions et mécanismes métallurgiques rencontrés sur les aciers dans le cas d’une cémentation carbonitruration, nitruration ou trempe superficielle.
Le tableau 6 fait état des propriétés et des performances obtenues sur les aciers et le tableau 7 dresse celles récoltées sur aciers faiblement alliés.
Les tableaux 6 et 7 et la figure 12 résument les principales propriétés des différents traitements. Les performances mécaniques sont en faveur de la nitruration, la différence se fait principalement par les possibilités de profondeurs durcies. La gamme nitruration est plus lourde que celle des autres traitements mais les risques sont moindres. Il faut insister sur les propriétés de la couche de combinaison. Ces propriétés ouvrent des applications particulières. Elles ne sont toutefois pas toujours exploitées comme dans le cas, des engrenages ou des vilebrequins où le traitement est appliqué exclusivement pour la tenue en fatigue. Dans ces derniers cas, les nitrurations sont profondes et les surfaces sont rectifiées après traitement.
Propriétés particulières de la couche de combinaison des nitrurations et nitrocarburations
La surface n’a plus de caractère métallique, elle devient alors :
• non soudable,
• résistante au grippage, celui-ci résultant précisément d’un mécanisme de solubilité des matériaux antagonistes,
• résistante au collage à chaud : trouvant une application intéressante dans le cas des outillages de forge à chaud, de fonderie d’injection d’aluminium,
• une barrière thermique d’où une amélioration du comportement des outillages à chaud.
Elle présente par ailleurs une dureté élevée, apportant une bonne résistance à l’usure et au frottement, un coefficient de frottement faible sous forte charge et un potentiel électrochimique fortement cathodique apportant une résistance élevée à la corrosion, si les conditions d’étanchéité sont réunies.
Application spécifiques des nitrurations et nitrocarburations non couvertes par la cémentation ou par la carbonitruration
• Sur les outillages pour travail à chaud, les propriétés de la couche de combinaison apportent un effet de barrière thermique, une résistance au collage et à la fatigue thermique.
• Dans les cas de frottement avec risques de grippage, la couche de combinaison apporte ses propriétés de non soudabilité donc de bonne résistance au grippage.
• Dans les cas de besoins de dureté très élevée (> 800 HV).
• Dans les cas de recherche de faible coefficient de frottement (propriétés de la couche de combinaison).
• Lors de la recherche d’une tenue à la fatigue et à l’usure en conditions de température élevée (200 à 500 °C).
• Résistance à la corrosion (propriétés cathodiques de la couche de combinaison).
• Bonne aptitude aux systèmes duplex avec revêtement PVD.
Possibilités de traitements duplex
Il est fréquent d’envisager de superposer à un traitement thermique superficiel un revêtement de type revêtement électrolytique ou PVD ou de combiner différents traitements.
Les revêtements électrolytiques se heurtent à la sensibilité des couches durcies au décapage chimique avant traitement qui risquent d’être plus sensibles au dégagement d’hydrogène spécialement pour les couches chargées en azote (nitrurées, ou carbonitrurées). Dans le cas des nitrocarburations ou nitrurations il convient d’éliminer préalablement la couche blanche.
Les revêtements PVD doivent tenir compte de la température d’adoucissement du traitement préalable qui globalement ne doit pas excéder 200°C pour les couches cémentées, carbonitrurées et trempées par induction. Sur les couches nitrurées il faut veiller à se situer environ 50°C en dessous de la température de nitruration. La couche blanche doit être éliminée.
Le durcissement superficiel par trempe peut être un moyen de durcissement des couches cémentées. La cémentation est alors réalisée sans trempe et le durcissement effectué après chauffage par induction permet de sélectionner facilement les zones à durcir.
Le chauffage par induction peut être utilisé comme moyen de recuit localisé des couches cémentées ou carbonitrurées.
Le durcissement après chauffage par induction a pu être utilisé en combinaison avec les nitrurations ou nitrocarburations, soit après, soit avant, nitruration.
Un chauffage par induction après nitrocarburation permet d’obtenir un durcissement en profondeur tout en conservant les qualités de la couche de combinaison. Il conviendra de vérifier le comportement de cette couche vis à vis de la fissuration lors de ce chauffage et trempe. Un procédé a été utilisé avec succès dans les années 50-80 : le sulf-HF combinant un traitement de sulfonitrocarburation (sulfinuz) utilisé sur des cylindres, des glissières et engrenages de machines-outils.
Un chauffage par induction avant nitruration sera partiellement adouci par la température voisine de 550 °C mais il tiendra lieu d’un renforcement par trempe et revenu en sous-couche. Cette solution a été appliquée sur des patins de culbuteurs de moteurs d’automobile.
Matrices de choix entre les traitements
Les facteurs de décisions technico-économiques sur pièces en acier pour des performances comparables sont présentés dans le tableau 11.
1. Investissement : il est en défaveur de la cémentation qui requiert des installations à haute température.
2. Nuance d’acier : les écarts proviennent de la composition chimique nécessaire pour assurer la trempabilité et la dureté de la couche durcie. La recherche de duretés élevées lors de la nitruration nécessite des aciers riches en éléments d’alliage.
3. Traitement préalable : dans le cas de la cémentation, il se résume aux recuits type isotherme. Pour les deux autres, il peut y avoir un traitement de trempe et revenu ou aucun traitement.
4. Usinage : l’usinage d’une nuance à l’état trempé revenu entre 850 et 1100 MPa réduit nécessairement la facilité d’usinage donc la productivité. On doit envisager d’employer des nuances à usinabilité améliorée si cela est compatible avec les sollicitations. C’est un des handicaps de l’application en grande série de la nitruration sur aciers alliés.
5. Préparation surface : avant traitement thermochimique, il est indispensable de réaliser un dégraissage voire une pré-oxydation. Avant trempe superficielle seule la recherche d’absence de fumées lors du chauffage justifie un dégraissage.
6. énergie : entre cémentation et nitruration les écarts de température se traduisent par des besoins horaires en énergie différents, le chauffage au gaz souvent utilisé en cémentation est exclu en nitruration. Mais les écarts de cinétiques peuvent ramener les consommations au même niveau pour des performances en service équivalente. Le chauffage par induction fait appel à des besoins en puissance beaucoup plus faible même si le traitement s’effectue pièce à pièce.
7. Gaz - milieu réactif - consommables : l’emploi d’ammoniac ou de sels en nitruration ou nitrocarburation est un facteur de coût qui n’apparaît pas avec la nitruration assistée plasma. Il faudrait ajouter les facteurs de contraintes environnementales.
8. Cadence : elle dépend beaucoup du type d’installation. Prenons par exemple des pignons de boîte de vitesse traités dans un four continu à une file, la cadence horaire pour un durcissement de l’ordre de 0,5 mm est compris entre 1000 et 2000 pièces / heure. En nitruration il faudrait une batterie de 4 à 6 fours de grande capacité (2000 kg de charge) pour faire l’équivalent). en trempe superficielle (sous réserve que les profils de trempe souhaités puissent être obtenus) les cadences pourraient être par machine de 250 à 350 pièces/heure.
9. Potentiel défauts : les traitements de cémentation ou carbonitruration ont un potentiel de défauts de microstructure, en nitruration il existe également mais il est moindre et nécessite un suivi moins rapproché. En trempe superficielle il y a un risque de dérives du profil trempé et de tapures.
10. Finition après traitement : selon les exigences la finition par rectification peut-être prévue après chaque type de traitement. En nitruration les variations géométriques étant faibles, il est fréquent de ne pas faire de reprise après traitement. Beaucoup de pièces trempées par induction ne sont pas reprises après traitement car leur précision ne l’exige pas.
Conclusion
Comme dans toute démarche de choix, beaucoup d’arguments avancés peuvent être discutés. Le choix relève toujours de considérations fonctionnelles, circonstancielles et économiques variables d’une entreprise à l’autre qui peuvent amener à des écarts.
Conférence prononcée lors du séminaire Air Liquide-Bodycote les 9 et 10 octobre 2008.
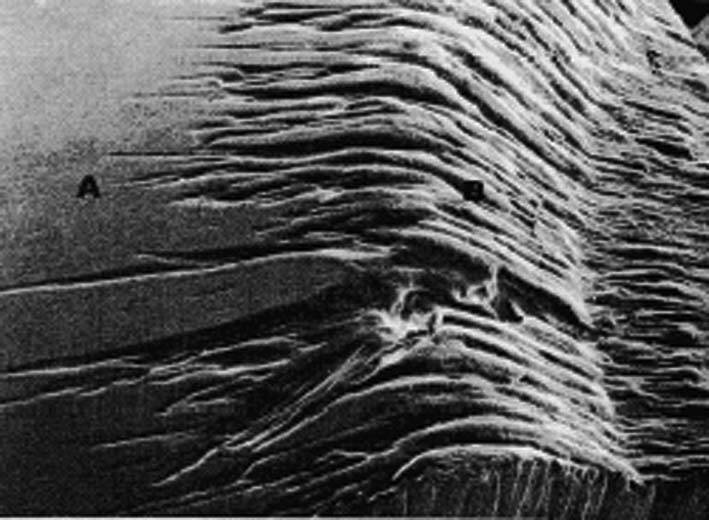
Figure 1. Aspect d’une usure par érosion.
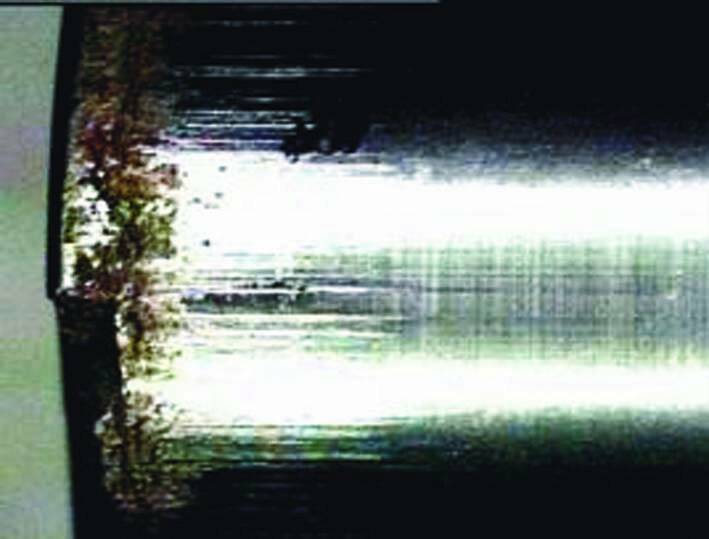
Figure 2. Aspect d’une adhésion.
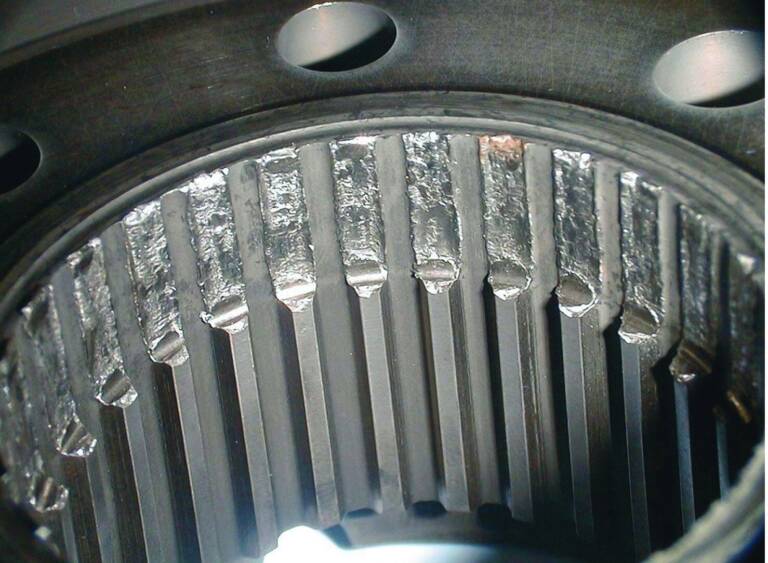
Figure 3. Aspect d’un matage de cannelures.
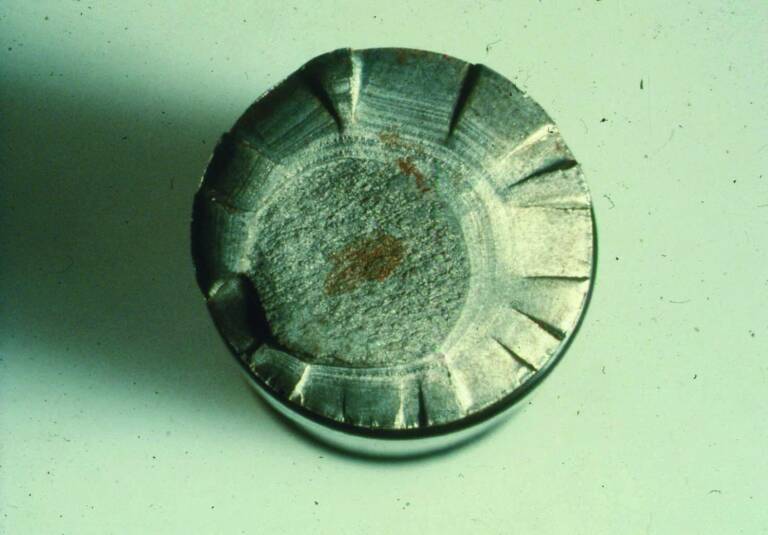
Figure 4. Fatigue en flexion rotative d’un arbre à épaulement (concentration de contrainte).
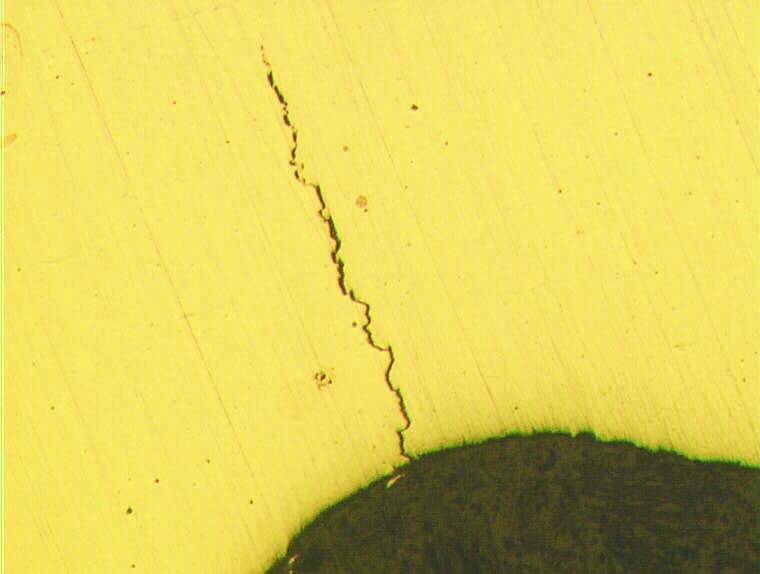
Figure 5. Fissuration en fatigue par flexion au pied de dent d’un engrenage.
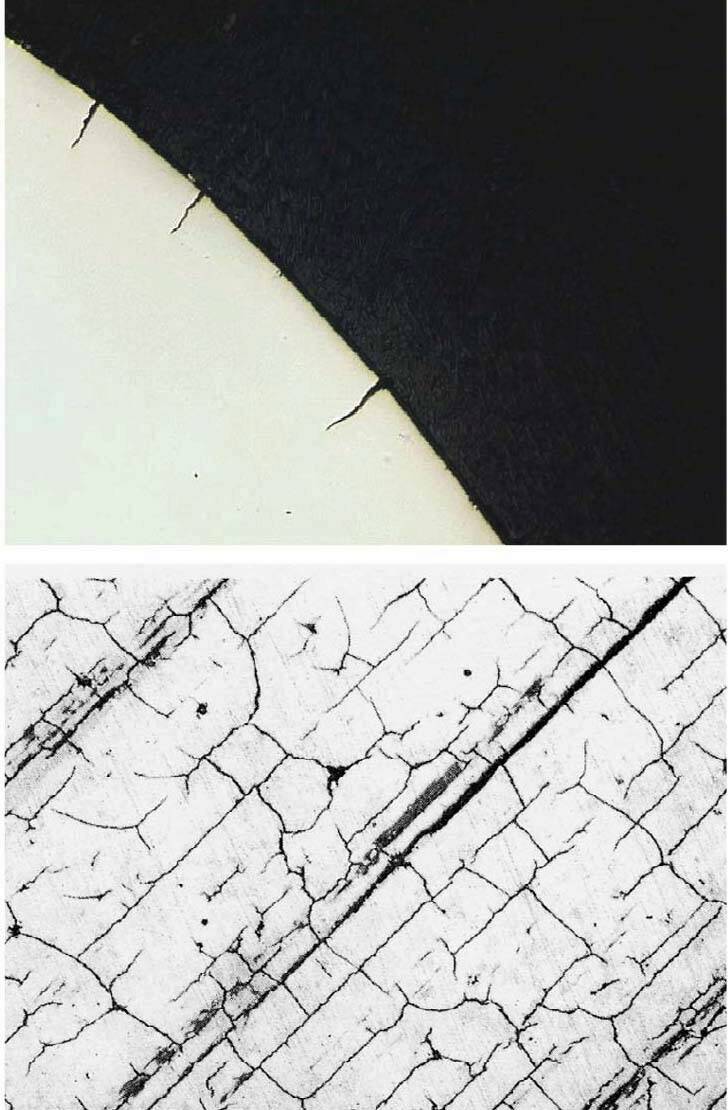
Figure 7. Aspect de la fissuration à chaud par fatigue thermique.
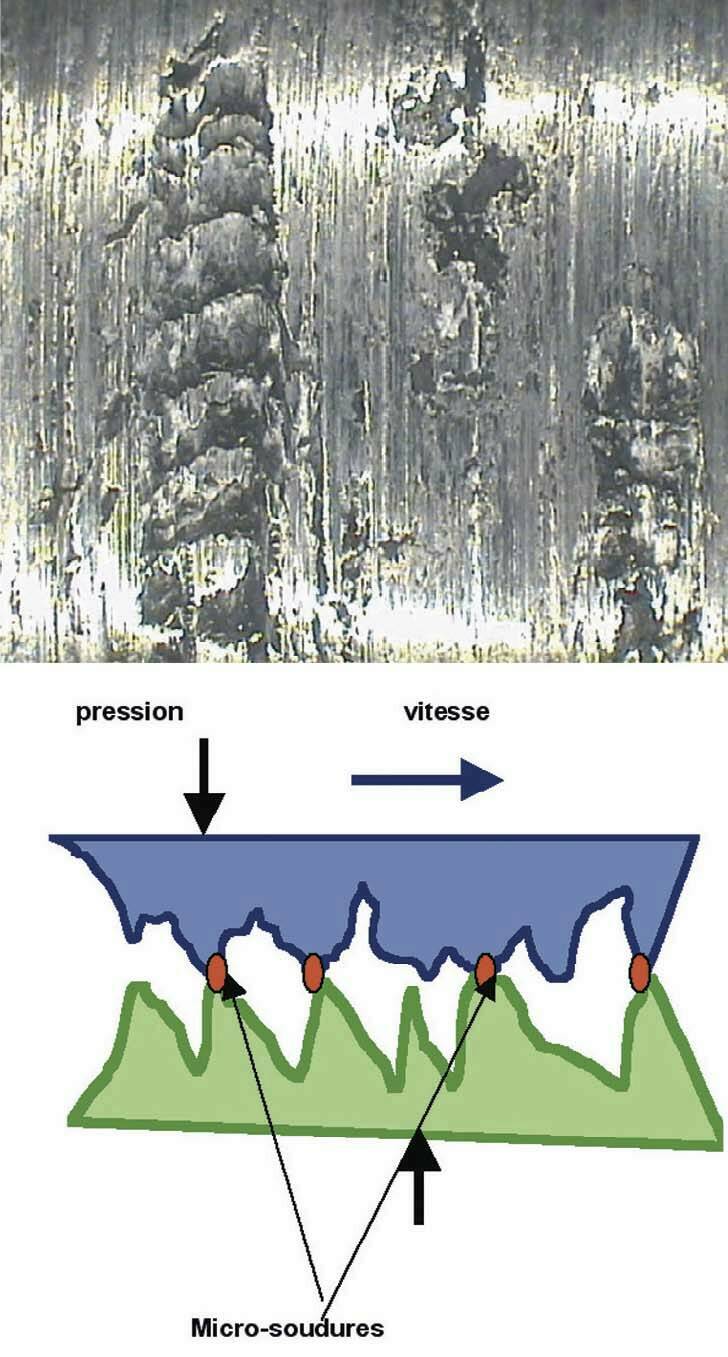
Figure 8. Aspect et mécanisme du grippage.
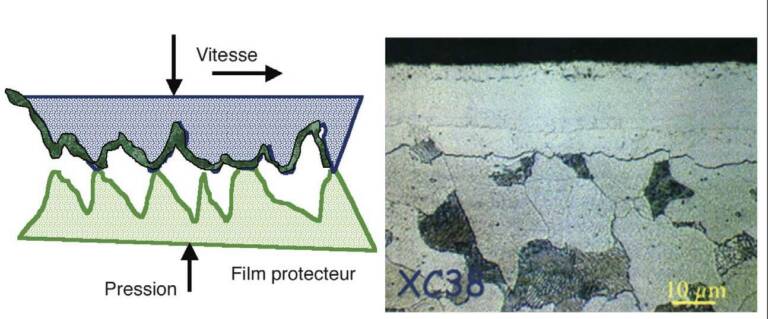
Figure 9. Mise en place d’une protection sur la surface par création d’une couche de combinaison dans le cas d’une nitrocarburation ayant converti le caractère métallique en céramique.
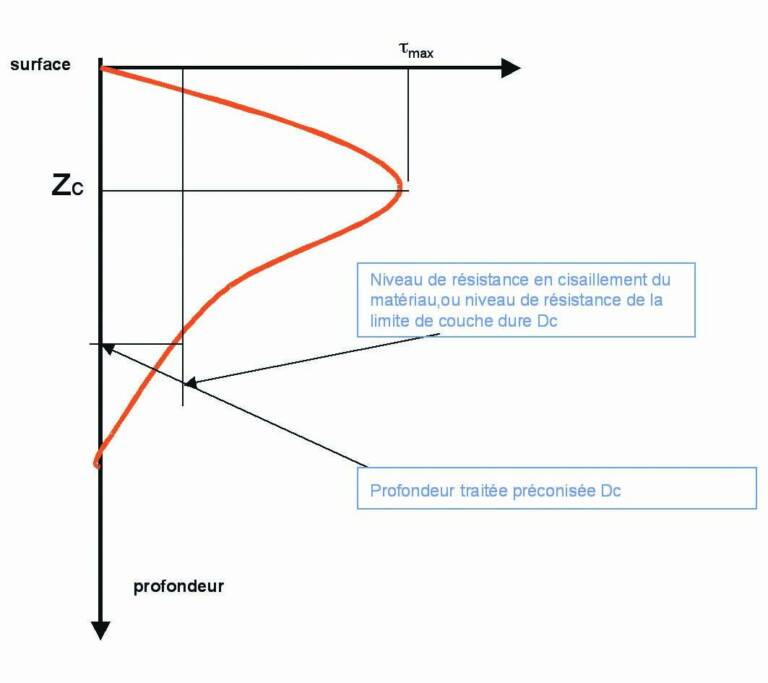
Figure 10. évolution du cisaillement en contact roulant et détermination de la profondeur durcie.
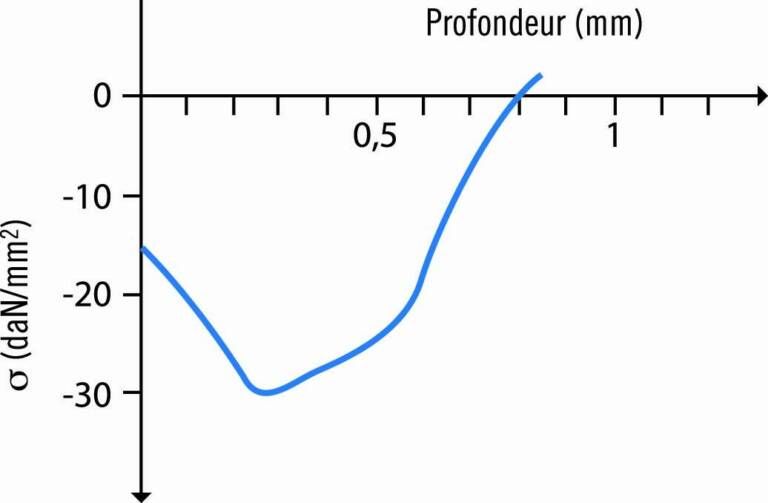
Figure 11. Teneur en carbone dans la couche cémentée 0,6 % en masse. épaisseur conventionnelle de cémentation 0,4 mm.
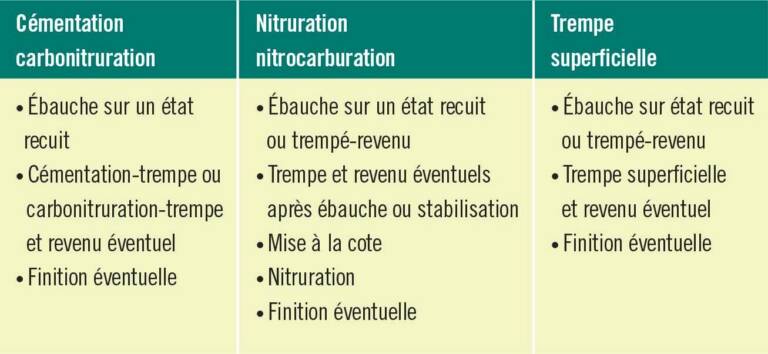
Tableau 1. Principales étapes des traitements.
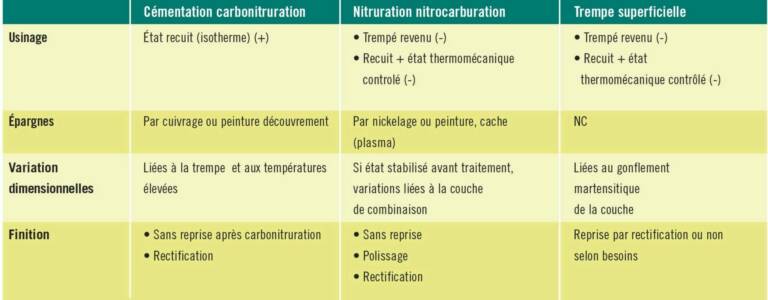
Tableau 2. Conditions de mise en œuvre des traitements thermiques superficiels.
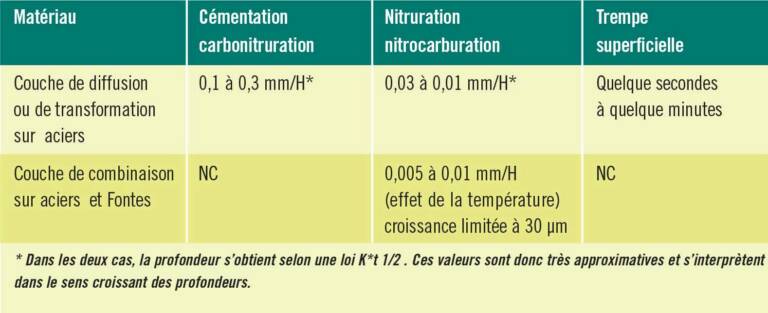
Tableau 3. Cinétiques des différents traitements.
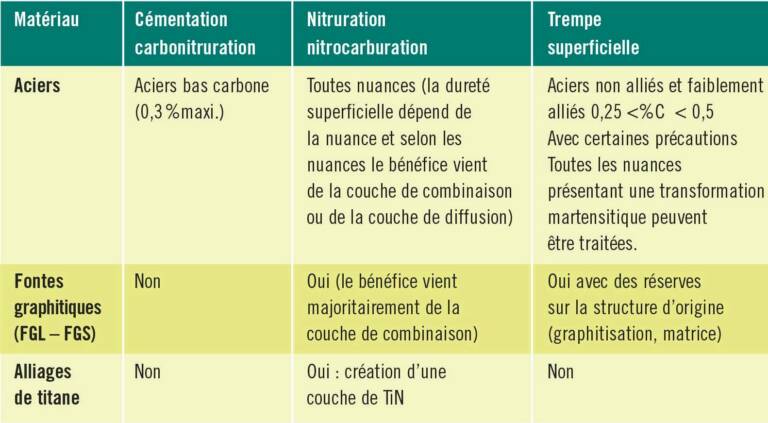
Tableau 4. Choix des matériaux pour application des traitements.
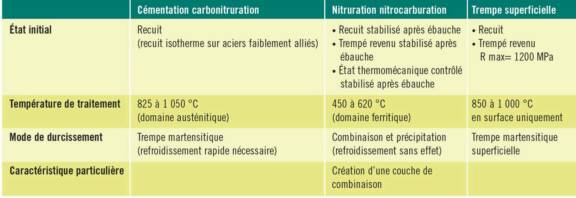
Tableau 5. Conditions et mécanismes métallurgiques sur acier.
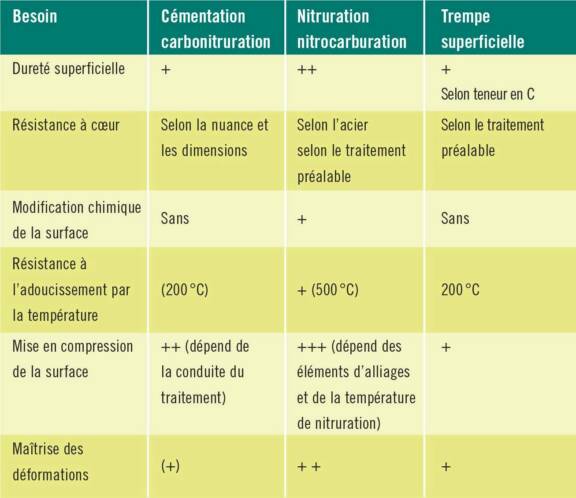
Tableau 6. Synthèse des propriétés obtenues.
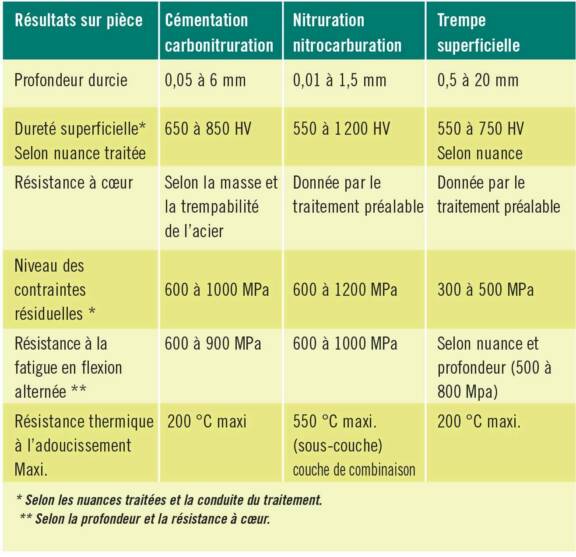
Tableau 7. Performances sur aciers faiblement alliés.
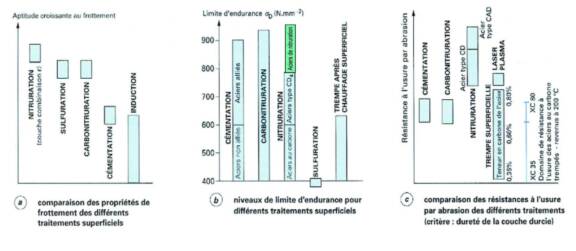
Figure 12. Principales propriétés d’emploi des traitements superficiels (extrait des Techniques de l’ingénieur).
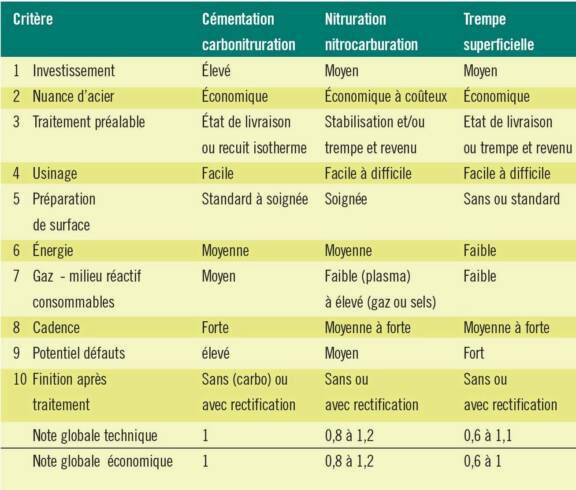
Tableau 11. Estimation des facteurs technico-économiques de chaque famille de traitement.
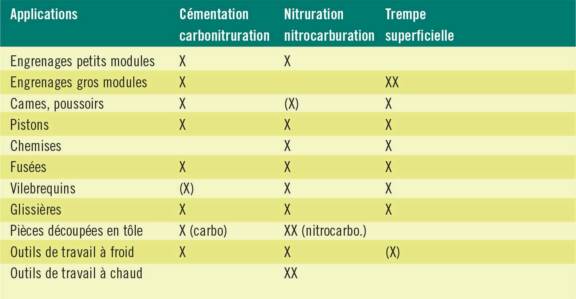
Tableau 9. Exemples d’applications types.
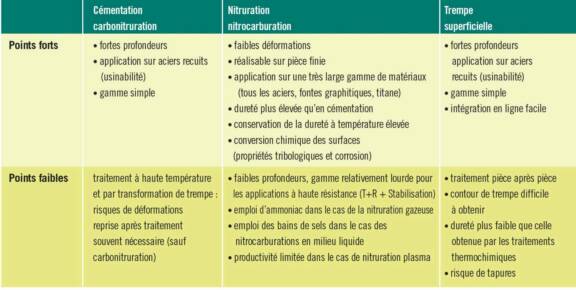
Tableau 10. Points forts et points faibles des traitements.