Optimisation des performances tribologiques des revêtements carbonés par texturation au laser pulsé
Par Constant Rieille(1), Christian Nussbaum (1), Sylvain LeCoultre(2), Josef Zürcher (2)
(1)Beat Neuenschwander, (2)Haute école spécialisée bernoise (BFH)
Un post-traitement au laser a été effectué sur différents revêtements DLC (diamond-like carbon). Les surfaces ainsi obtenues comprennent, d’une part, le revêtement non texturé et, d’autre part, des points traités au laser à la surface permettant d’améliorer leurs performances tribologiques, soit par une réduction du coefficient de friction grâce à une micro-/ nano-texturation limitant la surface de contact et facilitant le glissement, soit par un durcissement local ou par une lubrification locale à la surface.
Les revêtements à base de carbone sont utilisés dans divers secteurs industriels, tels que l'automobile, les machines-outils, l'énergie, l'aérospatiale, l'électronique et les dispositifs médicaux. Les revêtements comme le diamant ou les DLC (diamond-like carbon) améliorent la résistance à l'usure grâce à leur extrême dureté et à leur inertie chimique attribuées à leur structure de liaisons covalentes du type diamant (sp3).
En revanche, le graphite ou GLC (graphite-like carbon), de faible dureté, possède un bas coefficient de friction en raison des faibles forces intermoléculaires entre ses feuilles hexagonales hybridées sp2 pouvant glisser les unes sur les autres lors du contact tribologique.
Les revêtements DLC, qui constituent une vaste famille, sont généralement produits à l'aide des technologies de déposition physique en phase vapeur (PVD) ou de dépôt chimique en phase vapeur assisté par plasma (PECVD). Ils sont habituellement classés en fonction de leur teneur en sp2 (liaisons du type graphite), sp3 (liaisons du type diamant) et hydrogène (figure 1).
L'industrie microtechnique, avec les systèmes micro-électromécaniques (MEMS), l’horlogerie et les outils de coupe, porte un intérêt croissant pour les revêtements à hautes performances tribologiques, notamment les DLC, très utilisés dans ces industries.
Parmi les performances recherchées, figurent une grande résistance à l’usure, permettant à un système mécanique d’être utilisé plus longtemps ; un coefficient de friction faible pour limiter l’énergie nécessaire à fournir le travail mécanique ; un coefficient de friction stable pour prédire l’usure du revêtement et éviter les défaillances imprévisibles de machines, de pièces ou d’outils.
Dans cette étude, un traitement laser, nommé « texturation laser », a été appliqué sur différents revêtements DLC. Les performances tribologiques des surfaces non texturées et texturées au laser ont été comparées.
Méthodologie et résultats
Les revêtements DLC et GLC suivants ont été déposés :
Carbone amorphe hydrogéné, a-C : H (DLC-1) déposé par PECVD dans l’entreprise PLATIT AG (Selzach). Il contient plus de 10 % de phase diamantée (liaisons sp3) et possède une nanodureté de 25 GPa
Carbone amorphe tétraédrique, ta-C (DLC-2) déposé par PVD-arc chez PLATIT. Il contient plus de 40 % de phase diamantée (liaisons sp3) et possède une nanodureté de 40 GPa.
Carbone graphitique GLC (le contenu de liaisons sp3 <10 %, nanodureté 10 GPa) par PVD sputtering, dépôt réalisé par la Haute école spécialisée bernoise (BFH).
Ces revêtements, d’épaisseurs comprises entre 0,8 et 1 µm, ont été déposés sur des pastilles en acier rapide (HRC 60), polies avec une rugosité Ra <0,01 µm.
Pour la texturation laser, deux sources laser ont été utilisées : un laser nanoseconde (τ = 1,4 ns, λ = 515 nm, densité d’énergie F = 0,42 J/cm2) et un laser femtoseconde (τ =400 fs, λ = 1030 nm, densité d’énergie F = 0,5 à 1,7 J/cm2). Les densités d’énergie des lasers ont toutes été choisies de manière à obtenir une rugosité de 200 ± 25 nm sur tous les échantillons. Les têtes laser des deux sources ont permis de choisir l’espacement des pulses laser dans l’orientation X et Y de manière à modifier la densité de la texturation à la surface des revêtements pour en étudier l’influence. Les spots laser à la focale sont de taille 21 ± 2 µm pour le laser nanoseconde et 26 ± 2 µm pour le laser femtoseconde. La figure 3montre deux exemples de topographies obtenues sur des échantillons GLC texturés.
Après texturation, les échantillons ont été soumis à des tests tribologiques sur le tribomètre MFT 2000 (Rtec-Instruments) de la BFH. Deux partenaires tribologiques statiques ont été choisis pour répondre à différentes applications. Le premier a été une bille en acier 100Cr6 (AISI 52100), diam. 6 mm, polie (Ra=0,02 µm), non revêtue. Les conditions de test tribologique ont été les suivantes : vitesse 3,5 cm/s, charge 2 N, sans lubrifiant, distance parcourue 5 km, température 22 °C, humidité relative 37 %. Le but a été d’étudier la réduction du coefficient de friction et de l’usure grâce à la texturation.
Le deuxième partenaire statique était un pion en laiton (CuZn) au plomb (Pb < 0,09 %), diam. 6 mm, non poli (Ra = 3,3 µm), non revêtu. Les conditions de tests étaient similaires. Le but a été d’étudier la réduction du coefficient de friction et du collage (transfert de matière du laiton sur le revêtement DLC).
En comparant l’échantillon a - C : H (DLC-1) non texturé et texturé par un laser (nanoseconde et femtoseconde), on a pu immédiatement observer une réduction du coefficient de friction lors du test tribologique dans le cas où une texturation laser a été appliquée à la surface du revêtement pour un recouvrement de texturation de 16 % (chaque spot laser était espacé de 40 µm dans l’axe de scanner en X et Y). Cette réduction est particulièrement notable pour la texturation au laser nanoseconde, qui présente un coefficient de friction abaissé d’un facteur deux par rapport à un échantillon non texturé, notamment après 1 km de distance parcourue, et se maintenant jusqu’à la fin du test tribologique (figure 2).
Les échantillons ont été analysés au microscope optique, puis au microscope interférométrique avec la lumière blanche, dans le but de déterminer l’usure du revêtement après le test tribologique. La figure 4 montre l'état de la surface du revêtement après les tests tribologiques. En mesurant la hauteur du sillon d’usure, l’usure moyenne de l’échantillon texturé au laser nanoseconde s’élève à 0,2 µm, l’usure de l’échantillon texturé au laser femtoseconde s’élève à 0,4 µm, tandis que l’usure de l’échantillon non texturé s’élève à 0,5 µm. La texturation laser peut donc agir comme un post-traitement visant à réduire l’usure et le coefficient de friction.
Le taux de recouvrement des spots laser à la surface du revêtement semble aussi exercer une influence sur le comportement tribologique, notamment du point de vue de l’usure. La figure 5 montre l’usure obtenue pour un taux de recouvrement laser de 16 %, comparée à celle d’un échantillon a-C : H non texturé. À noter que 50 % de recouvrement signifie que chaque spot laser est espacé de 20 µm d’un autre spot dans l’axe X et de 40 µm dans l’axe Y). Pour 100 % de recouvrement, les spots sont espacés de 20 µm dans les axes X et Y).
En comparant la morphologie d’un spot laser sur la surface du DLC en dehors du sillon d’usure tribologique avec un pulse laser se trouvant à l’intérieur du sillon d’usure, il est possible de voir que même après 5 km de test, le spot laser est toujours visible à la surface (figure 6). Cela signifie que l’effet de la texturation laser perdure jusqu’à la fin du test.
Des résultats similaires ont été obtenus avec les échantillons GLC, avec une tendance à la réduction de l’usure et du coefficient de friction.
À ce stade, deux hypothèses pourraient expliquer la diminution du coefficient de friction et de l’usure. La première se base sur un effet géométrique, soit la diminution du coefficient de friction par une diminution de la surface de contact de la bille avec la surface du revêtement. La deuxième concerne un effet chimique basé sur une transformation de la chimie de surface induite par le laser. En effet, le carbone possède de nombreux états métastables, comme le graphite, le diamant, le carbone amorphe et le graphène. Déjà à partir d’une densité d’énergie du laser de 0,3 J/cm2, il est possible d’induire une graphitisation d’un revêtement DLC[1].
Le graphite est connu pour être un très bon lubrifiant solide appliqué à de nombreux partenaires statiques, comme l’acier. Ce faisant, la texturation pourrait agir comme un promoteur de liaisons sp2 lubrifiant localement le contact tribologique. Dans le cas de revêtements graphite (GLC), une piste pourrait expliquer la diminution de l’usure dans le cas de la texturation laser : la formation de nanodiamants à l’intérieur du volume exposé au faisceau laser. Ce mécanisme de conversion, encore mal compris, pourrait faire intervenir un principe de trempe rapide qui si elle l’est suffisamment, serait capable d’induire des contraintes locales supérieures à 10 GPa, des conditions permettant la conversion locale de graphite en diamant[2], améliorant ainsi la résistance à l’usure.
Les tests tribologiques effectués avec les pions en laiton CuZn à faible teneur en plomb ont, quant à eux, montré une tendance à la réduction des effets de collage en présence d’un DLC ta-C texturé par un laser femtoseconde comparé à l’échantillon non texturé. En effet, une image optique de l’état de la surface après le test tribologique de 500 m (figure 7), expose une surface noire très adhérente à la surface, drastiquement réduite dans le cas du revêtement texturé. Une analyse par microscopie électronique à balayage (MEB), couplée à l’analyse chimique (EDX), révèle que cette surface noire est le résultat d’un transfert de matière du pion (laiton CuZn) sur le revêtement DLC ta-C (figures 8c et d). De plus, l’analyse révèle que les spots marqués par le laser à la surface du revêtement ont été préservés du transfert de laiton sur le revêtement (collage) ce qui pourrait participer à la réduction de la surface de collage (figure 8e).
La réduction des effets de collage est également observable sur le graphique 8 représentant l’évolution du coefficient de friction de revêtement ta-C texturé et non texturé. Ce dernier montre que la texturation laser a un impact clair sur la réduction des effets « stick - slip » ‒ en français « adhérence - décollement ».
Conclusions et perspectives industrielles
Cette étude a permis d’explorer le comportement tribologique de revêtements de carbone amorphe hydrogénés (a-C : H), de carbone amorphe tétraédrique (ta-C) et de carbone graphitique (GLC) non texturés et texturés par laser nano ou femtoseconde. Les résultats montrent que la texturation laser réduit significativement le coefficient de friction et l’usure des revêtements a-C : H (DLC-1) et GLC.
Une réduction notable du coefficient de friction d’un facteur deux a été observée pendant le test tribologique de 5 km contre une bille en acier 100Cr6 sur un échantillon a-C : H (DLC-1) texturé au moyen d’un laser nanoseconde. De la même façon, sur ce même échantillon, l’usure finale du revêtement a pu être réduite de moitié.
Deux hypothèses sont proposées pour expliquer ces améliorations : un effet géométrique, réduisant la surface de contact tribologique, et une transformation chimique induite par le laser, probablement la graphitisation du revêtement DLC, assurant une lubrification sèche lors du contact tribologique.
Les tests avec des pions en laiton CuZn ont révélé une réduction des effets de collage, avec une meilleure stabilité du coefficient de friction pour les échantillons ta-C texturés. Ces résultats suggèrent que la texturation laser peut améliorer les performances tribologiques des revêtements DLC et GLC, offrant ainsi des perspectives intéressantes pour des applications industrielles nécessitant une faible friction et une résistance à l’usure. Aujourd'hui, nous travaillons au sein de l’institut ALPS de la BFH, à l'étude des paramètres de traitement laser et à la compréhension des mécanismes d'interaction entre le faisceau laser et les surfaces, dans le but d'améliorer les performances tribologiques de revêtements. n
Bibliographie
[1] Dorner-Reisel, A., Engel, A., Svoboda S., Schürer C., Weißmantel S. (2020). Laser structuring of hydrogenated DLC scaffolds : Raman spectroscopy and nanotribology. Diamond and Related Materials, 108, 107787.
https://doi.org/10.1016/j.diamond.2020.107787
[2] Nian, Q., Wang, Y., Yang, Y. Direct Laser Writing of Nanodiamond Films from Graphite under Ambient Conditions. Sci Rep 4, 6612 (2014).
https://doi.org/10.1038/srep06612
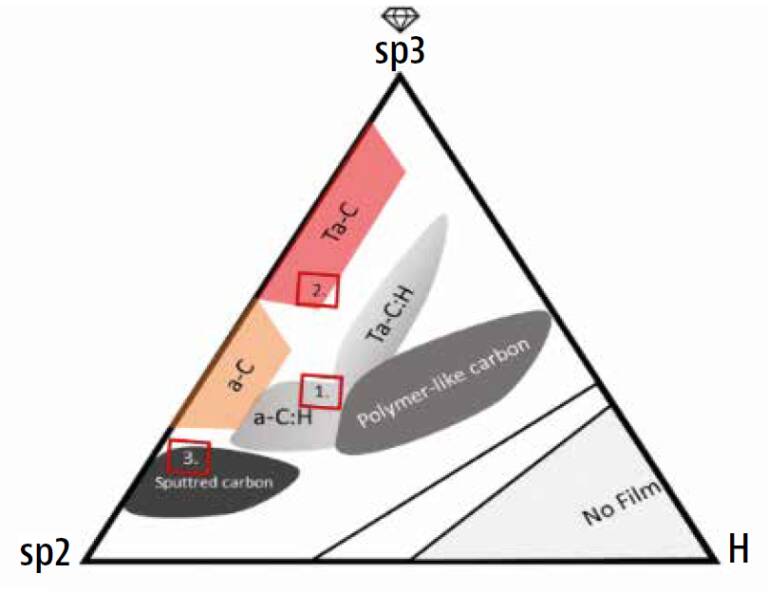
Figure 1.
Diagramme ternaire des revêtements DLC (diamond-like carbon).
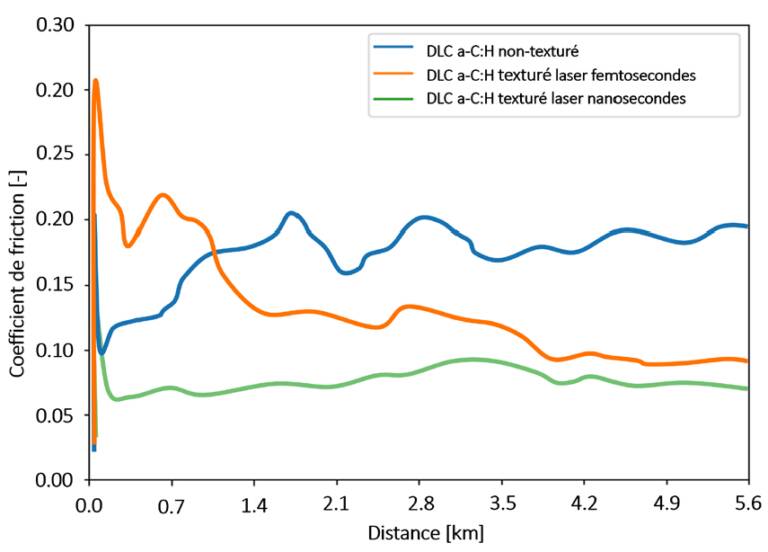
Figure 2.
Évolution du coefficient de friction du carbone amorphe hydrogéné a-C : H (DLC-1) non texturé (en bleu), texturé par laser femtoseconde (en orange), texturé par laser nanoseconde (en vert).
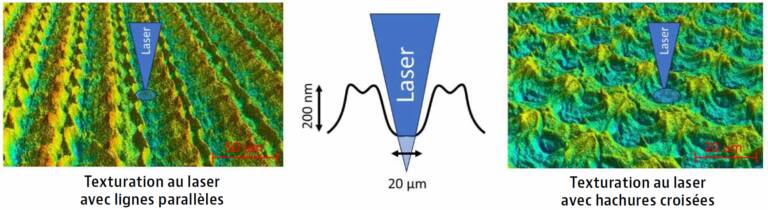
Figure 3.
Topographie de surface de revêtements GLC texturés : texturation laser avec lignes parallèles (à gauche), morphologie typique d'une impulsion laser avec hauteur des textures (au centre), texturation laser avec des lignes hachurées (à droite).
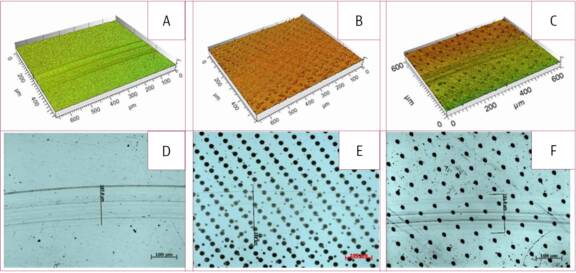
Figure 4.
Topographie des surfaces des revêtements a-C : H (DLC-1) après un essai tribologique à sec contre l’acier 100Cr6 (distance parcourue 5 km). Images par microscopie interférométrique : a) non texturé, b) texturé au laser nanoseconde,
c) texturé au laser femtoseconde. Images par microscopie optique :
d) non texturé, e) texturé par laser nanoseconde,
f) texturé par laser femtoseconde.
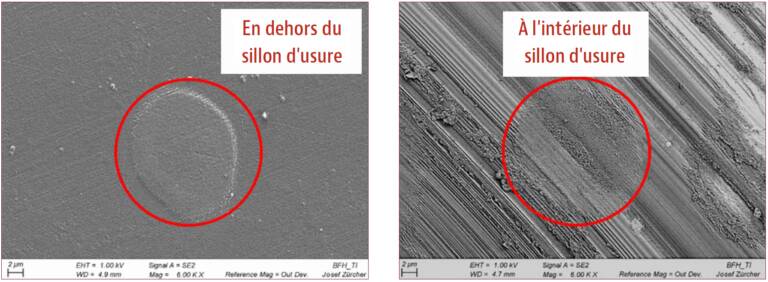
Figure 5.
L’usure (5a) et les coefficients de friction (5b) des revêtements DLC et GLC.
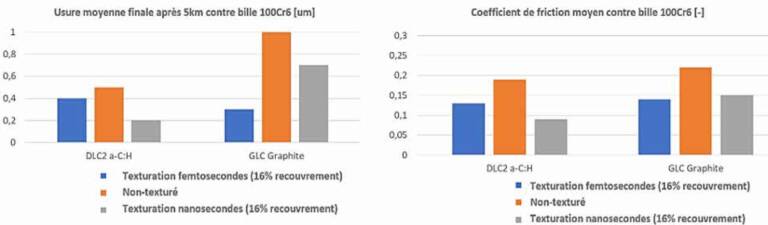
Figure 6.
Images par microscopie électronique à balayage (MEB) d'une empreinte laser nanoseconde à l'extérieur d'un sillon d’usure tribologique (à gauche) et à l'intérieur de celui-ci (à droite).
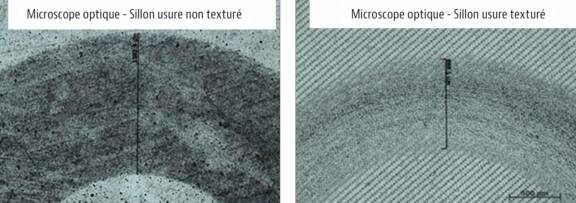
Figure 7.
Image au microscope optique de la trace d'usure du pion en laiton après essai tribologique : ta-C (DLC-2) non texturé (7a), ta-C (DLC-2) texturé au laser femtoseconde (7b).
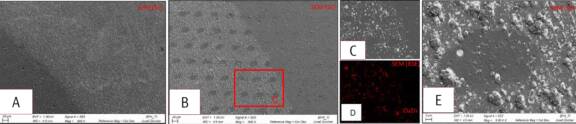
Figure 8.
Analyse MEB de la trace d'usure du DLC ta-C. a) trace d'usure du ta-C non texturé ;
b) trace d'usure du ta-C texturé ; c) zoom sur la trace d'usure du ta-C texturé ; d) cartographie par analyse chimique EDX de la trace d'usure ; e) spot laser femtoseconde isolé sur la surface du revêtement ta-C
(DLC-2) texturé.
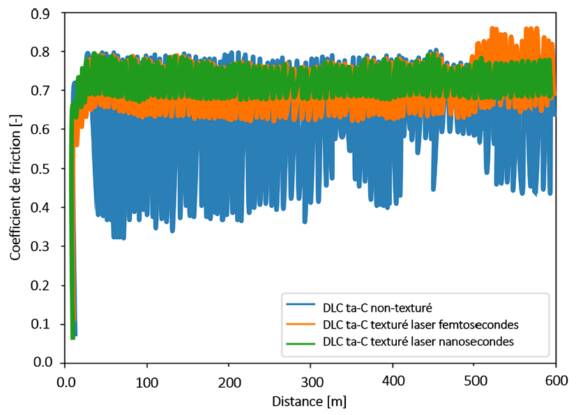
Figure 9.
Évolution du coefficient de frottement du ta-C (DLC-2) non texturé (bleu), texturé par laser femtoseconde (orange), texturé par laser nanoseconde ( vert ).