Le dépôt ALD pour mieux contrôler l’épaisseur de films
Par Cedric Favre, Directeur et éditeur de Oberflächen Polysurfaces, Ingénieur HES
Le terme « ALD » (Atomic Layer Deposition) se traduit par dépôt par couches atomiques. C’est une technique utilisée en nanotechnologie et en science des matériaux pour déposer sur une surface des films minces de matériaux avec une précision atomique. Cette méthode, qui permet d’effectuer un contrôle très fin de l’épaisseur du film, est couramment utilisée dans la fabrication de semi-conducteurs, de revêtements protecteurs, en horlogerie et autres applications nécessitant des films de haute qualité.
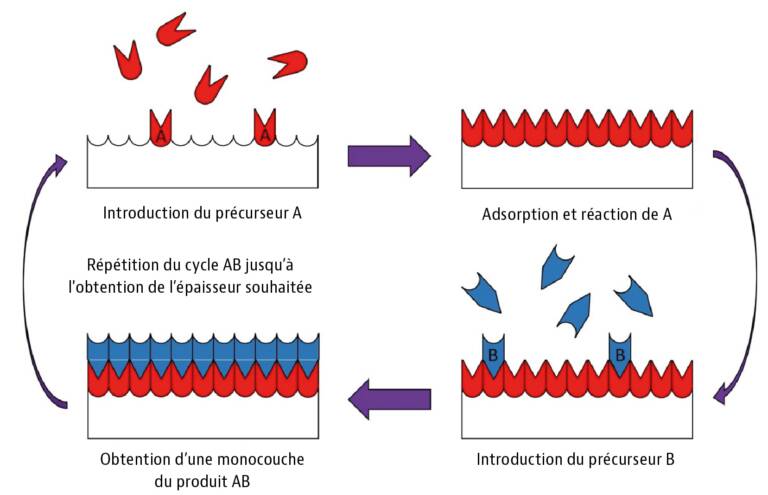
Schéma : Procédé ALD en quatre étapes.
Le dépôt par couches atomiques (ALD, pour Atomic Layer Deposition) est une technique avancée de dépôt chimique en phase gazeuse qui permet de créer des films extrêmement fins, généralement d’épaisseur nanométrique (10-300 nm), sur une surface donnée.
Ce procédé est particulièrement prisé pour sa capacité à produire des couches extrêmement uniformes, y compris sur des pièces de forme complexe dont la géométrie est irrégulière.
L’ALD fonctionne par l’application séquentielle de précurseurs chimiques en phase gazeuse. Chaque précurseur réagit avec la surface de manière autocatalytique, formant une couche monoatomique à chaque cycle. Ce contrôle précis de la réaction chimique permet de réguler l’épaisseur de la couche déposée avec une précision atomique. La température de dépôt est généralement comprise entre 100 et 300 °C.
L’un des principaux avantages du dépôt ALD réside dans la faible contrainte mécanique des films déposés. Contrairement à d’autres procédés de dépôt, l’ALD minimise les tensions internes dans la couche, ce qui réduit les risques de fissuration ou de délaminage. Cela est crucial pour les applications où l’intégrité du film est primordiale, comme dans les dispositifs électroniques, les semi-conducteurs, les revêtements optiques et les couches de protection.
De plus, le dépôt ALD est souvent utilisé sur des matériaux nécessitant une grande pureté et des propriétés spécifiques, électriques, optiques améliorées. Ce procédé est également adapté à la fabrication de nanostructures et de dispositifs à l’échelle nanométrique, où un contrôle précis de l’épaisseur et de la composition du film est essentiel.
Cette technologie se caractérise par sa capacité à déposer des traitements de manière uniforme, reproduisant avec une précision nanométrique la topographie de la surface. Les couches ALD répondent ainsi aux exigences les plus élevées de la microtechnique.
Ces traitements offrent une vaste palette de coloris et de nuances, avec une parfaite répétabilité, y compris sur des pièces dont les géométries tridimensionnelles sont complexes. En horlogerie, cette technique est très utilisée, surtout sur des composants internes (cadrans, aiguilles, indexes).
L’épaisseur nanométriques des couches déposées permet de préserver les décors mécaniques des surfaces. De plus, malgré leur grande stabilité chimique, les dépôts ALD, qui sont réversibles, garantissent une excellente protection contre la corrosion des substrats métalliques.
Comment déposer des revêtements ALD ?
Un précurseur A (des molécules contenant des atomes métalliques) est introduit dans l’enceinte sous vide, où il réagit chimiquement pour se déposer uniformément sur toute la surface de la pièce à traiter. Les atomes du précurseur A se greffent sur la surface grâce aux ponts O-H absorbés naturellement. Une fois que toute la surface est recouverte par des atomes métalliques, une purge à l’azote est effectuée pour chasser les restes du précurseur A ainsi que les produits annexes.
Un précurseur B (dans la plupart des cas : de l’eau) est ensuite ajouté, qui réagit avec les premiers atomes déposés pour former un composé, le plus souvent un oxyde métallique, comme Al2O3. Une deuxième purge à l’azote est effectuée pour chasser les restes du précurseur B ainsi que les produits annexes. Ce processus en quatre étapes constitue un cycle, qui est répété plusieurs fois jusqu’à atteindre l’épaisseur souhaitée.
Quelques inconvénients
Il existe cependant des inconvénients, le principal étant la faible vitesse du dépôt, car le procédé nécessite quatre étapes successives. C’est pour cette raison que les épaisseurs des couches ALD n’excèdent en général pas 300 nm. Pour compenser cet inconvénient, le dépôt ne nécessite pas de posages et peut se faire en vrac, ce qui permet de traiter un plus grand volume de pièces, surtout si elles sont de petite taille.
Les avantages de la technologie ALD sont les suivants :
• Conformité et uniformité parfaites
• Maîtrise précise de l’épaisseur du dépôt sur des géométries complexes (à l’échelle du nanomètre)
• Large variété de matériaux traitables (alliages cuivreux, titane, or, aciers, céramiques, plastiques, etc.)
• Densité élevée des dépôts
• Très bonne stabilité chimique
• Excellente couche barrière
• Procédé réversible
• Dépôts en mono et multicouches
• Complémentaire à d’autres technologies