La trempe sous presse
Par Aurélie ACHILLE (FORVIA), Alexandre FLEURENTIN (METALLO CORNER)
Développée depuis les années 1970, la trempe sous presse a pris son essor via la combinaison de deux facteurs essentiels : la maîtrise du dimensionnel des pièces par l’élimination ou la limitation maîtrisée des déformations après traitement thermique couplée à l’expansion et à la facilité de mise en œuvre de l’automatisation. Effectivement, si une part des déformations géométriques après trempe est prédictible par simulation, une autre part reste difficile à anticiper. C’est dans ce contexte que la trempe sous presse prend tout son sens. Mais que signifie cette technique et comment procède-t-on ?
L’utilisation de la trempe sous presse est adaptée à des pièces de formes complexes à haut niveau de sollicitation sur aciers même fortement chargés en carbone, aciers cémentés ou carbonitrurés, aciers à outils ou encore alliages non ferreux comme les alliages d’aluminium. Les pièces couramment trempées sous presse sont les bagues de roulement et les pièces d’engrenage tels que les pignons coniques, les manchons et arbres.
Cette technologie s’applique à des pièces de révolution (Cf. figure 1) sensibles aux déformations ou lorsque les tolérances dimensionnelles et géométriques sur produits finis sont très resserrées.
Principe
La trempe sous presse consiste à maintenir la pièce à tremper dans un outillage simple ou complexe durant un cycle de trempe défini et programmé afin de limiter ou d’annihiler les déformations géométriques usuellement obtenues après cette opération. Le cycle de refroidissement est réalisé de façon unitaire et est par conséquent répétable d’une pièce à l’autre.
La circulation du fluide de trempe autour de la pièce maintenue dans l’outillage entraîne un refroidissement uniforme, contrôlé et reproductible. L’optimisation des débits et des vitesses du fluide de trempe évite la formation de bulles ou de poches gazeuses (caléfaction). La microstructure après trempe est constituée d’une martensite fine et homogène, meilleur compromis dureté/résilience.
La force extérieure exercée sur la pièce, par l’intermédiaire d’un montage, permet de corriger voire d’empêcher les écarts de forme. Ces montages sont des supports sur lesquels reposent la pièce, des systèmes d’appui pour exercer la force contrôlée sur la pièce et un outillage ou mandrin. Ces derniers peuvent être de 3 types : fixe, extensible ou lamellaire en fonction de la pièce et de la précision recherchée.
Déroulement de la trempe sous presse
Le déroulement de la trempe sous presse est décrit par Marie-Anne Métais [1] sur des baladeurs de la façon suivante : dès son positionnement dans la presse de trempe, la pièce est prise sur un mandrin qui s’introduit dans le diamètre intérieur de la pièce. La partie supérieure du montage de trempe s’abaisse, la pièce se trouve alors dans un espace confiné. Un vérin hydraulique permet l’application d’une pression définie et adaptée sur le pourtour de la pièce par l’intermédiaire de l’outillage. La pièce est alors maintenue sans déformation possible et est prête à subir la trempe.
Un réservoir localisé dans le bâti de la presse fournit l’huile de trempe qui traverse les plaques de fond et de positionnement ainsi que le système d’appui des pièces par des ouvertures ou des perforations pour permettre l’aspersion de la pièce dans le montage de façon la plus homogène possible. L’huile reflue dans le réservoir par des ouvertures localisées dans la cloche de trempe. Durant toute l’opération de trempe, la pièce est resserrée sur le mandrin.
Lorsque l’opération de trempe est finie, le vérin d’éjection descend pour faire sortir le mandrin vers le bas et permettre l’éjection de la pièce, la cloche de trempe remontant postérieurement.
Lignes de trempe sous presse
Les lignes de trempe sous presse sont des lignes complètement automatisées multipostes consacrées en majorité à la grande série. Un exemple d’une chaîne industrielle (Renault Dacia au Portugal, Séville en Espagne et Pitesti en Roumanie) est proposé par Claude Hannote [7] dans son intervention d’octobre 2006 à Bordeaux intitulé « trempe sous presse sur les baladeurs – retour d’expérience pour le choix d’une technologie et d’un investissement » (Cf. figure 2).
Les lignes sont composées de [2] :
- Un magasin dont le chargement des pièces s’effectue en automatique ou en manuel ;
- Un manipulateur (préhenseur ou autre) qui achemine d’une part, les pièces (ou les palettes avec les pièces) non traitées vers le four et d’autre part, les pièces (ou palettes avec les pièces) austénitisées avec ou sans enrichissement vers la presse de trempe. Le temps de transfert entre la sortie du four et le positionnement de la pièce sous presse doit être court afin de limiter au maximum la baisse de température. Il est possible de sortir les pièces encore chaudes (150/200°C) et de terminer le refroidissement des pièces en trempe libre dans le bac d’huile afin de libérer le montage plus rapidement ;
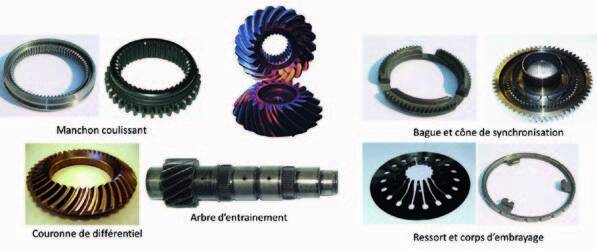
Figure 1 : Exemples de pièces trempées sous presse.
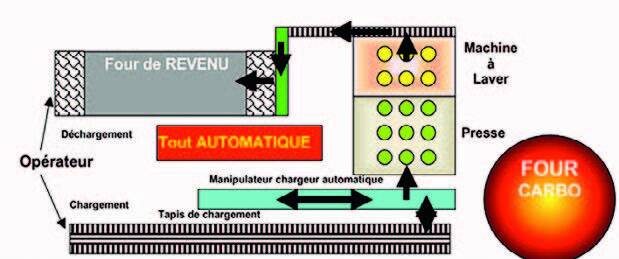
Figure 2 : Exemple d’installation de trempe sous presse industrielle chez Renault. Troisième investissement chez Renault Dacia à PITESTI en Roumanie tout automatisé (en commande).
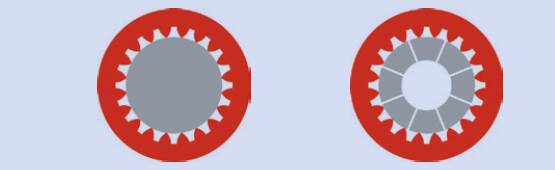
Figure 3 : Présentation d’un mandrin fixe et d’un mandrin à expansion [8].
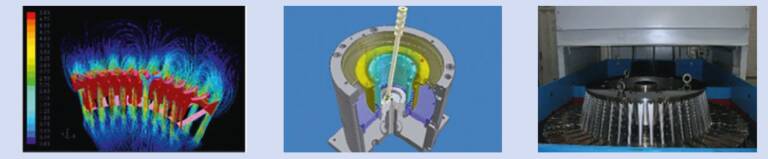
Figure 4 :Modélisation des flux thermiques et conception assistée d’un procédé de trempe sous presse [4].
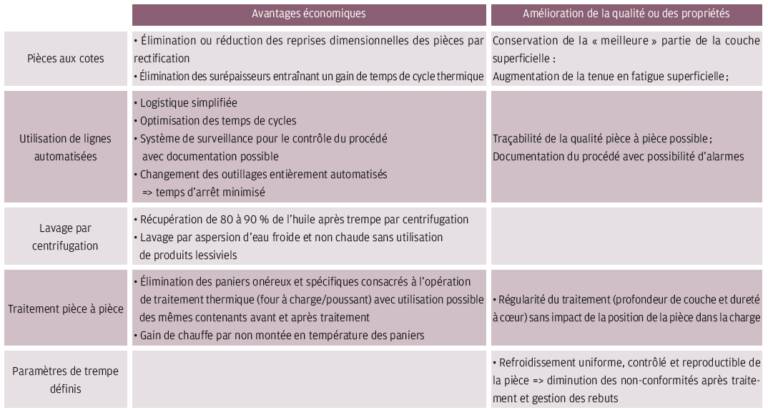
Tableau 1
- Un four à petits rouleaux sous atmosphère, tournant, annulaire ou autre dont la fonction est de réaliser l’austénitisation et/ou le cycle d’enrichissement en fonction de la profondeur de diffusion souhaitée ;
- Une presse de trempe sous presse à multi-stations enfermant la pièce dans un montage pour maintenir la pièce aux cotes pendant la trempe à l’huile froide ;
- Une machine à laver à force centrifuge permettant d’obtenir en fin de cycle des pièces propres et sèches. Le nombre de stations de la machine à laver est identique à celui de la presse. Le lavage s’opère en 2 temps : la centrifugation et l’aspersion d’eau et d’air comprimé sur la pièce. Ce processus s’opère sous cloche de protection. Dans un premier temps, les pièces sont en rotation sur un plateau support pourvu de fentes radiales pour éliminer au maximum le surplus de liquide. Dans un second temps, une pulvérisation d’eau froide, les pièces étant toujours en rotation, entraîne le détachement des gouttelettes d’huile restante. Enfin, un soufflage à l’air comprimé à l’aide de buses finit de sécher les pièces ;
- Un four de revenu si nécessaire.
Le type d’installation choisi dépend :
- Du type de traitement thermique désiré : trempe, cémentation, carbonitruration, nitruration… ;
- De la forme de pièce et de sa sensibilité à la manipulation durant le process ;
- Le mode de chargement ;
- Le nombre de stations de la presse ;
- Le type de lavage ;
- La nécessite ou non d’un revenu.
Selon les exigences et la forme des pièces, elles peuvent être trempées sur mandrin lisse (fixe ou extensible) ou mandrin denté, avec prise sur le flanc de la dent ou à fond de dent (Cf. figure 3).
Les différents types de fours utilisés
Les fours réalisant les opérations de chauffe, avec ou sans diffusion antérieures à l’opération de trempe sous presse, sont adaptés à la grande série pour une optimisation des coûts et de la logistique associée grâce à une automatisation avancée de lignes multipostes. Il existe 3 grandes catégories : les fours à petits rouleaux sous atmosphère, les fours à sole tournante et les fours annulaires.
Four à petits rouleaux sous atmosphère
Le four à petits rouleaux sous atmosphère est généralement destiné à l’austénitisation avant trempe pour des temps de maintien inférieurs à 1 heure. Il peut atteindre une capacité de plusieurs pièces toutes les 20 secondes. Les difficultés d’utilisation résident dans la face d’appui minimale des pièces qui doit être d’au moins 40 mm afin de pouvoir véhiculer les pièces dans le four et dans la réalisation du transfert précis des pièces à l’endroit de prélèvement par le préhenseur. Ceci implique un dispositif de chargement du four et de la presse avec utilisation de glissières, de taquets, de centreurs…, pour guider et réorienter les pièces afin d’approvisionner la presse.
Four à sole tournante
Le four à sole tournante est plutôt destiné à des opérations de cémentation ou de carbonitruration allant de 0,3 à 0,6 mm de profondeur de diffusion. La sole supporte les étages de palettes sur lesquelles sont placées des pièces unitairement ou en pile les unes sur les autres. Le pas correspond à un segment. Les pièces sur les palettes sont donc chargées et déchargées du four par un manipulateur au niveau de la porte guillotine du four dont l’ouverture est réduite afin de limiter les entrées d’air pouvant nuire aux résultats après traitement thermique. La capacité du four dépend de la profondeur de diffusion recherchée, de la vitesse de rotation du four, du nombre de secteurs et d’étages. Elle peut aller de 3 à 6 pièces toutes les 40 secondes.
Four annulaire
Le four annulaire, utilisé pour les traitements thermochimiques, cémentation ou carbonitruration, est un bon compromis entre les fours tournants et poussants. En effet, il possède des zones séparées qui permettent une optimisation du cycle d’enrichissement jusqu’à 30 % pour des profondeurs diffusées supérieures à 0,6 mm. Il repose sur la rotation d’un anneau d’un diamètre supérieur à celui d’une sole tournante (ex : 9 m) ; l’entrée et la sortie des pièces s’effectuent dans la même zone. La capacité du four est fonction de la vitesse de rotation et du nombre d’étages disponibles dans le four. D’autres types de four peuvent également être utilisés tels que le four poussant (déplacement des pièces sur un plateau pas à pas posé sur des rails et actionné par un vérin de poussée) ou encore le four sous vide via des développements spécifiques.
La maîtrise du procédé
La maîtrise de la déformation finale de la pièce dépendra après trempe sous presse de nombreux facteurs cités par Arthur C. Reardon [3] qui peuvent être plus ou moins compensés par des optimisation process. Les plus importants sont :
- La qualité et l’historique du matériau à partir desquels la pièce a été fabriquée ;
- L’historique thermique antérieur et la distribution des contraintes résiduelles à l’intérieur de la pièce ;
- Les contraintes thermiques et de transformations déséquilibrées induites par la trempe ;
- Le temps de transfert entre le four d’austénitisation et la trempe ;
- Le type, l’état, la quantité et la température du fluide de trempe ;
- La direction et le dosage sélectif de l’écoulement du liquide de trempe sur la pièce ;
- La durée de la trempe à différents débits ;
- L’emplacement des différents points de contact sur le composant pour appliquer les charges externes ;
- L’ampleur des charges appliquées pour maintenir la géométrie ;
- La conception, l’installation et l’entretien de l’outillage de trempe ;
- La méthodologie de pulsation.
Pour certaines pièces présentant des différences importantes de rapport surface/volume, il est nécessaire, afin d’obtenir des gradients de températures et de contraintes les plus uniformes possibles, de diriger de façon sélective le flux du liquide de trempe vers les sections les plus épaisses tout en limitant le refroidissement dans les zones les plus fines. Cette technique permet ainsi de réduire les niveaux de déformation induits par la transformation.
Si l’outillage est correctement conçu, la direction de l’écoulement de l’huile sur le composant peut être ajustée pour obtenir les meilleurs résultats :
- Ouvertures allongées à la sortie pour restreindre le flux d’huile ou complètement ouverte pour maximiser le flux ;
- Présence de plusieurs anneaux con-
centriques et fendus dans les matrices inférieures pouvant être tournées pour assurer un écoulement total ou restreint de l’huile sur la face interne de la pièce ;
- Présence de segments temporisés pendant le cycle de trempe pour faire varier le débit d’huile et la durée afin d’établir une « recette de trempe » bien définie pour une conception de pièce spécifique.
Le débit de l’huile doit être ajusté pour être suffisamment rapide au départ et ainsi empêcher la caléfaction. Il peut ensuite être diminué.
La vitesse de trempe doit être maîtrisée et optimisée. Si elle est trop faible, des transformations indésirables ainsi que des variations de dureté seront observées. A contrario, si elle est trop rapide, des tapures de trempe et/ou des déformations inacceptables pourront survenir.
La température de l’huile utilisée pour procéder à la trempe sous presse varie de 25 °C à 75 °C. Toutefois, il est préconisé de ne pas dépasser 60 °C pour éviter d’endommager les joints d’étanchéité de la machine utilisée pour contenir l’huile de trempe.
L’entretien correct et régulier de l’huile de trempe ne doit pas être négligé. En effet, au fur et à mesure de l’utilisation de l’huile, les additifs se dégradent progressivement et des particules fines peuvent s’accumuler au cours du temps et ce, même si l’huile est filtrée en continu. Cela peut occasionner une augmentation de la drasticité de l’huile et donc entraîner des modifications de résultats métallurgiques après trempe.
Un système de pulsation peut être également utilisé pendant la trempe afin de maintenir la géométrie de la pièce et de minimiser les déformations. La fonction d’impulsion réduit périodiquement la pression exercée (ex toutes les 2 secondes) par les matrices interne et externe offrant à la pièce le loisir de se contracter normalement lors de son refroidissement tout en conservant la géométrie souhaitée. Sans cela, les contraintes induites par friction entre l’ensemble de la matrice et le composant ne lui permettraient pas de se contracter normalement en refroidissant.
Avantages de la technologie
Les avantages de la technologie [4] sont décrits dans le tableau ci-contre : Avantages économiques et amélioration de la qualité des pièces via l’utilisation de la trempe sous presse.
Conclusion
La trempe sous presse est un procédé qui, par la distribution uniforme et répétable de la dureté pour chacune des pièces traitées, un niveau minimal de déformation ainsi qu'une réduction substantielle des procédures de finition supplémentaires, augmente la qualité des produits finaux (élimination des rebuts et contrôles supplémentaires) tout en présentant des avantages économiques intéressants.
Même si les progrès dans le domaine de la simulation du procédé sont encourageants, l’importance de l’expérience et des compétences humaines dans la mise au point des installations reste primordiale.
Il existe néanmoins des outils d’aide à la simulation numérique des flux et transferts thermiques. Des logiciels de modélisation tels que CFD (Computational Fluids Dynamics) ou MNF (Mécanique des fluides numériques) peuvent être utilisés pour optimiser l’outillage de la trempe sous presse (Cf. figure 4). Ces outils permettent des simulations sur des pièces de révolution de plus en plus grandes (e.i. engrenages pour éoliennes).
Bibliographie
[1] « Intégration de la trempe sous presse sur pièces circulaires dans une installation entièrement automatisée », Marie-Anne METAIS, Traitement & Matériaux, Mars-Avril 2013, N°421.
[2] « Les presses destinées à la trempe sous presse », André MULOT, Traitement Thermique, Août-Septembre 2002 ; N°341.
[3] « Press quenching and effects of prior thermal history on distorsion during heat treatment », Arthur C. REARDON, Gear technology, March-April 2014, pp. 50-53.
[4] « Les lignes automatiques de trempe sous presse », A. MULOT – T. STRENG – A. ROSNER, Traitement Thermique, Mars 2004, N°353.
[5] « Effect of hardenability and press quenching on distorsion of crown wheels », A. STORNVINTER – H. KRISTOFFERSEN – A. OLOFSSON – K. BIWERSI – S. HAGLUND, Thermal process modeling 2014 : Proceeding from the 5th International conference on thermal process modeling and computer simulation, June 16-17, 2014, pp. 149-155.
[6] « Trempe sous presse de pièces circulaires », Thomas Streng, présentation HEESS / MTC dans le cadre de la commission fluides et systèmes de trempe de l’A3TS, 2022.
[7] « La trempe sous presse sur des baladeurs », Claude HANOTTE, Traitement & Matériaux, Avril 2007, N°378.
[8] « High Quality Fixture Quenching Fixture Types, Levels of Automation and Machine types », STRENG, Th.1, HEESS, K.1, JURETZKO, H. 1, presentation HEESS GmbH & Co KG, Lampertheim, Germany