La technologie de revêtement au chrome (III), une solution innovante
Le recours aux composés du chrome hexavalent (CrVI), couramment utilisés pour la réalisation de revêtements chromés, est désormais encadré par le règlement REACH. Soucieuse de réduire son impact environnemental, l’équipementier automobile ZF LIFETEC a modernisé son procédé de galvanisation par un système de pointe utilisant le chrome trivalent. Cette innovation a été déployée en 2023 grâce à un partenariat étroit avec la société Dr.-Ing. Max Schlötter GmbH & Co. KG, chargée de la conception et de la mise en œuvre des modifications techniques requises.
La ceinture de sécurité, équipement obligatoire dans les véhicules neufs en Allemagne depuis 1976, est un élément indispensable dont la fiabilité contribue à sauver des vies chaque jour. Les composants métalliques utilisés doivent répondre à des exigences strictes en matière de résistance mécanique et de stabilité à long terme. Le procédé traditionnel consiste alors à appliquer des revêtements de nickel et de chrome par voie électrolytique pour protéger les surfaces.
Les voitures sont généralement équipées de ceintures de sécurité à trois points. « Ces systèmes de sécurité nécessitent des composants métalliques à la fois robustes et capables de résister durablement aux aléas climatiques. Et des critères esthétiques très exigeants doivent être rigoureusement appliqués », explique Thomas Haberfellner, directeur des opérations chez Dr.-Ing. Max Schlötter GmbH & Co. KG.
Les composants sont revêtus d’un dépôt électrolytique de nickel-chrome et, pour une meilleure protection, partiellement recouverts de plastique. La surface fonctionnelle en nickel-chrome subit en effet de fortes contraintes de corrosion et de frottement pendant l’utilisation.
En adoptant des systèmes basés sur le chrome (III), ZF LIFETEC (Alfdorf) a anticipé les futures réglementations européennes sur les produits chimiques, offrant ainsi un soutien précoce à l’industrie automobile. L’entreprise s’appuie sur l’expertise de la société Dr.-Ing. Max Schlötter GmbH & Co. KG qui, depuis de nombreuses années, étudie et développe des systèmes d’électrolytes basés sur le chrome trivalent. Ces électrolytes offrent une véritable alternative aux systèmes traditionnels au chrome (VI) pour ces applications.
De la matière première à la finition haut de gamme
Avant le revêtement, les pièces métalliques sont soumises à un traitement de précision comprenant estampage, ébavurage, trempe et grenaillage (ou tribofinition). Le processus de polissage par tribofinition utilisé chez ZF LIFETEC permet à la fois de réduire les durées des cycles et de préparer les surfaces à un revêtement galvanique optimal. Les lignes de galvanisation entièrement automatisées assurent le dégraissage, le nickelage et le chromage final des pièces, afin de garantir une excellente résistance à la corrosion et un aspect esthétique irréprochable.
Optimiser les résultats grâce aux procédés au chrome (III)
Pour tirer pleinement parti des avantages des procédés au chrome trivalent, il a fallu effectuer des tests approfondis et adapter les équipements afin d’obtenir les mêmes propriétés que les revêtements précédents. Schlötter propose le tout dernier système au chrome (III) : le bain de chrome SLOTOCHROM BC 4130.
L’aspect visuel des revêtements obtenus en production de série est identique à celui des revêtements au chrome (VI).
« La conversion au système au chrome trivalent a été un pas essentiel pour assurer la pérennité de notre production », souligne Harald Häfele, responsable du département Surfaces chez ZF LIFETEC.
Défis techniques et solutions
L’adoption du nouveau système au chrome (III) a nécessité plusieurs ajustements techniques au niveau des installations. Pour garantir la stabilité et la fiabilité du processus, nous avons par exemple installé un échangeur d’ions sélectif pour le traitement du bain et un dosage automatique de ses composants. Par ailleurs, un traitement électrolytique complémentaire permet d’obtenir des couches suffisamment passives pour atteindre la résistance à la corrosion requise.
Production innovante et éco-responsable
Depuis septembre 2023, ZF LIFETEC a intégré à son processus de production les bains de chrome SLOTOCHROM BC 4130 et le procédé de post-traitement SLOTOCHROM DR 2340 pour la finition des pièces métalliques. Répondant en tous points aux exigences fonctionnelles et esthétiques, cette technologie se fond parfaitement dans l’infrastructure actuelle, et permet une transition efficace. « L’excellente collaboration avec Schlötter a été déterminante pour la réussite de ce projet », souligne Harald Häfele. En optant pour cette transition, ZF LIFETEC accompagne ses clients dans leur démarche environnementale tout en poursuivant ses propres objectifs de développement durable.
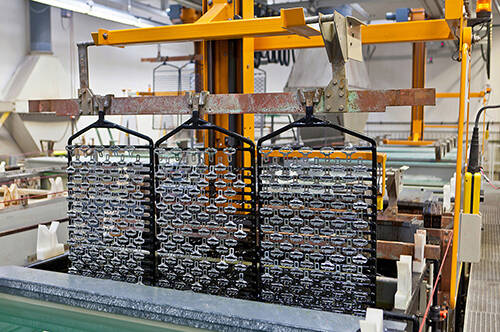
Photo 1. L’entreprise Schlötter est aujourd’hui l’un des leaders mondiaux de la galvanotechnique.
ZF AG, spécialiste de la sécurité passive
ZF AG est l’un des plus grands équipementiers automobiles au monde, spécialisé dans les technologies de transmission et de châssis et les systèmes de sécurité active et passive. Situé à Alfdorf, près de Schwäbisch Gmünd, le siège mondial de ZF Passive Safety Systems, fort de plus de 1 600 collaboratrices et collaborateurs, développe et fabrique des systèmes de retenue, notamment des ceintures de sécurité, pour la plupart des constructeurs automobiles. La production annuelle de pièces pour les systèmes de sécurité passive s’élève à environ 40 millions d’exemplaires.
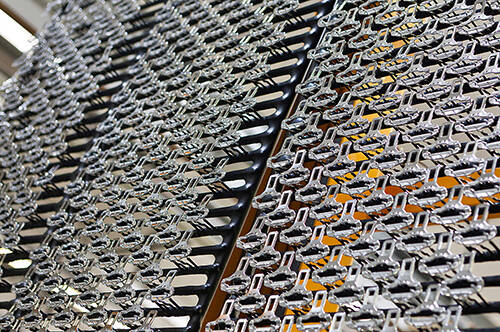
Photo 2. L’aspect visuel des revêtements obtenus en production de série est identique à celui des revêtements au chrome (VI).
Dr.-Ing. Max Schlötter GmbH & Co. KG, 110 ans de galvanotechnique
Fondée il y a plus de 110 ans, Dr.-Ing. Max Schlötter GmbH & Co. KG est une entreprise familiale dirigée par la quatrième génération et spécialisée dans la recherche et le développement. Née d’un laboratoire électrochimique, l’entreprise est aujourd’hui l’un des leaders mondiaux de la galvanotechnique. Schlötter est un acteur international présent à Geislingen (Allemagne), Pershore (Royaume-Uni), Naas (Irlande), Norrköping (Suède), Singapour, Wuxi et Dongguan (Chine) ainsi qu’à Taipei (Taïwan). Les domaines d’expertise de l’entreprise couvrent le développement de procédés de galvanoplastie, la fabrication de produits chimiques de process et la construction d’installations de galvanisation. Le siège social de Geislingen emploie actuellement environ 180 personnes.