Four pour la cémentation profonde basse pression
Par Sylvain Bissel, Fours Industriels BMI, France
La cémentation est un traitement thermochimique qui vise à augmenter la dureté superficielle en diffusant du carbone dans la pièce traitée et en la trempant. Leur résistance à l’usure par frottement, aux impacts et à la fatigue est alors améliorée. Selon l’application, la profondeur efficace de cémentation doit être adaptée. Les pièces de grande taille soumises à de fortes charges, telles que dans l’industrie minière ou les éoliennes, sont soumises à de fortes pressions de contact. Par conséquent, elles nécessitent des profondeurs de cémentation supérieures à la profondeur affectée par ces pressions de contact.
La cémentation profonde consiste en des profondeurs de cémentation allant de 2,5 mm à plus de 4 mm. Le présent travail montre les résultats de la cémentation basse pression profonde réalisée dans nos fours de trempe à l’huile sous vide avec le procédé multi-boost à l’acétylène ALLCARB®, y compris le four vertical de trempe à l’huile sous vide V64THC adapté aux pièces de très grandes dimensions.
1. Cémentation sous vide
1.1. Traitement thermique sous vide
Le traitement thermique sous vide présente de nombreux avantages par rapport à un traitement thermique sous atmosphère. Chaque cycle de traitement, quel que soit le four et le procédé, commence par une purge par le vide à 0,1 mbar au minimum. Ce vide permet de s’assurer que tout oxygène, humidité et autres contamination extérieur sera supprimé de l’enceinte.
Ainsi, l’oxydation agressive des pièces, constatée lors des traitements thermiques en bain de sel ou en four atmosphérique notamment, n’a pas lieu. Les pièces cémentées présentent un aspect gris légèrement mat.
1.2. Types de cémentation
La cémentation est généralement réalisée sur des aciers à faible teneur en carbone et faiblement alliés, voire non alliés. La température de cémentation est réglée de manière à ce que l’acier soit en phase austénitique. En effet, le carbone est plus soluble dans l’austénite que dans la ferrite. Les différents procédés de cémentation peuvent être classés selon la manière dont le carbone est introduit dans les pièces.
Pour la cémentation par enrichissement gazeux, on distingue :
La cémentation sous atmosphère, qui est effectuée dans un four à atmosphère contrôlée.
La cémentation basse pression, qui est effectuée dans un four sous vide avec une pression de gaz de cémentation de quelques millibars.
Il existe, de manière plus marginale, de la cémentation plasma ou de la carbonitruration par bain de sel.
Le tableau 1 résume les arguments pour une comparaison entre la cémentation en atmosphère et la cémentation sous vide[1]. Tout en consommant moins de gaz et d’énergie électrique, la cémentation sous vide présente des avantages en termes de performance. L’utilisation de basses pressions rend les surfaces métalliques plus réactives.
De plus, l’acétylène (C2H2), utilisé dans ce travail comme gaz de cémentation, ne contient pas d’oxygène. L’oxydation indésirable et le désalliage des pièces traitées sont donc évités. De plus, dans le cas rare où les pièces sont fortement alliées, la pression de cémentation ainsi qu’une pression partielle en azote lors des phases de diffusions permet d’empêcher toute sublimation des éléments d’alliages sensibles.
1.3. Cémentation basse pression à l’acétylène
Au contact de l’acier à haute température, l’acétylène se dissocie en carbone et en hydrogène[2]. Le carbone résultant réagit avec le fer des pièces en acier et forme des carbures. Il est ensuite diffusé dans la matrice de l’acier (figure 1).
Basée sur cette alternance de génération de carbures et de diffusion du carbone, la cémentation sous vide consiste en deux étapes réalisées une seule fois (mono-boost) ou répétées (multi-boost) :
Boost : injection de gaz pour enrichir les surfaces des pièces en carbone. Dans cet article, le gaz utilisé est l’acétylène (C2H2).
Diffusion : diffusion du carbone de la surface vers le cœur des pièces traitées (aucune injection de gaz pendant cette étape).
L’avantage du séquençage multi-boost réside dans la possibilité d’apporter uniquement la quantité nécessaire de carbone pour cémenter la pièce à chaque séquence. Cela permet d’optimiser la consommation de gaz de cémentation et d’éviter la saturation en carbone et le dépôt de suie sur les pièces traitées.
2. Four vertical de trempe huile sous vide type V6_THC
2.1 Présentation
La famille V6_TH est composée des fours verticaux bi-chambres de trempe à l’huile sous vide, conçus pour le traitement de grandes charges à l’image de trains d’atterrissage, de composants hydrauliques et d’outillage pour les engins de travaux publics. La chambre de chauffe peut être maintenue à une température définie entre les traitements. La mobilité de chambre de chauffe permet le chargement de pièces volumineuses au-dessus de la chambre de trempe par pont roulant.
La porte étanche à l’intérieur garantit une interaction nulle avec les vapeurs d’huile, ce qui aide à atteindre des niveaux de vide élevés.
Lorsqu’ils sont équipés de l’option ALLCARB® pour la cémentation basse pression, ces fours sont nommés V6_THC (figure 2).
2.2. Chambre de chauffe
La chambre de chauffe est composée d’une enceinte chaudronnée en double paroi refroidie à l’eau. Le traitement thermique est réalisé dans une chambre composée d’une ossature en acier, d’une isolation thermique en laine minérale ou panneaux de feutre graphite, d’un revêtement intérieur en CFC et d’un ensemble d’éléments chauffant en graphite. Cette chambre de traitement permet de diminuer les pertes thermiques vers la double paroi. La double paroi refroidie à l’eau assure la tenue au vide et l’étanchéité de la zone de traitement.
Des thermocouples suivent la température en différents points de la zone de traitement assurent les fonctions de régulation de température et la sécurité surchauffe de la charge et de l’équipement. Due aux éléments mobiles du four et aux transferts automatiques de la charge entre le four et la chambre de trempe au cours du cycle de traitement, la charge ne peut pas être instrumentée de thermocouples avec liaison filaire. Il existe toutefois des solutions de suivi de température non filaire.
2.3 Chambre de trempe à l’huile
Le four est équipé en standard d’une chambre de trempe huile sous vide avec chauffage d’huile à température régulée jusqu’à 80°C avec brasseurs pour améliorer l’efficacité et l’homogénéité de la trempe. Pour permettre le chargement de la charge dans la chambre de chauffe en production et l’intervention lors les opérations de maintenance, l’huile est transférée automatiquement entre la chambre de trempe et une cuve de stockage étanche.
La trempe est réalisée dans l’huile avec pression partielle d’azote au-dessus du bain d’huile, en atmosphère protégée. Le temps de transfert de la charge entre la chambre de chauffe et l’immersion complète dans l’huile de trempe est de l’ordre de 20 à 25s.
2.4 Intégration à une ligne de traitement thermique
Il est possible d’intégrer ce four à une ligne de traitement thermique automatisée par sa conception mobile. Cette ligne de traitement thermique peut comprendre le nettoyage des pièces, la trempe à l’huile, la trempe au gaz surpressé, avec ou sans cémentation, et des fours de revenu.
(Figure 3 et tableau 2)
3. Matériaux et méthodes
3.2. Cémentation multi-boost ALLCARB®
ALLCARB®, le procédé de cémentation multi-boost à l’acétylène, permet à l’utilisateur de définir automatiquement les paramètres de la recette de cémentation multi-boost. Pour ce faire, l’utilisateur choisit une nuance d’acier dans une liste, une température de cémentation, une profondeur efficace de cémentation, une teneur en carbone de surface souhaitée et la zone de charge à cémenter (figure 4). À partir de ces données d’entrée, ALLCARB® définit le nombre de séquences boost-diffusion et leurs durées respectives. Il est également possible d’injecter de l’H2 lors de la première séquence de cémentation, que ce soit en mode automatique (ALLCARB®) ou en mode manuel (figure 4).
Afin d’améliorer la flexibilité des paramètres d’entrée fournis par l’utilisateur et de simplifier son utilisation en général, l’assistant ALLCARB® est actuellement en cours de mise à jour. La version actuelle d’ALLCARB® couvre de manière fiable (Fig. 4) : o Des températures de cémentation allant de 860 °C à 980 °C ; o Des profondeurs de cémentation de 0,4 mm à 1,8 mm ; o 6 nuances d’acier de cémentation usuelles (AFNOR) : 20NCD2, 16NC6, 12NC12, 16NCD13, 16MC5 et 25CD4.
2.3. Nuances
Les résultats présentés dans cet article sont centrés sur des échantillons et des pièces fabriqués en une nuance d’acier nouvellement ajoutée à la version améliorée d’ALLCARB® : le 18CrNiMo5. Chaque cycle présenté a été défini avec cette nouvelle version, en utilisant la profondeur de cémentation et la température de cémentation comme paramètres d’entrée.
Le cycle affiché dans la figure 5 a été défini pour une profondeur efficace de cémentation de 3,6 mm et une température de cémentation de 1 000 °C.
Remarque : cet article se concentre sur les séquences de cémentation basse pression. Cependant, ces séquences font partie d’un traitement thermique plus global. Le traitement montré dans la figure 5 inclut des étapes de préchauffage avant d’atteindre la température de cémentation, ainsi qu’un refroidissement naturel et un maintien à la température d’austénitisation avant la trempe à l’huile.
3. Résultats
3.1. Cémentation profonde
La figure 6 montre un profil de dureté d’une pièce traitée selon le cycle de la figure 5. Le début de la courbe ne révèle aucune baisse importante de dureté due à l’austénite retenue.
La profondeur de cémentation mesurée (à 550HV0.2) est de 3,62 mm, ce qui est proche de la profondeur ciblée de 3,6 mm. Cette profondeur de cémentation se traduit par une dureté superficielle macro de 62,5 HRC avant revenu.
Les versions agrandies des images de microscopie optique a, b et c de la figure 6 sont présentées dans la figure 7 La microstructure est composée de martensite de la surface au cœur, et les images sont en accord avec le profil de dureté.
La teneur en carbone diminue avec la profondeur.
Pour faciliter l’analyse de ces images, la figure 8, issue du travail de Maki et al., représente de manière schématique les lattes de martensite dans un acier Fe-C simple en fonction de sa teneur en carbone[3].
3.2. Effets de la température de cémentation
Afin de mettre en évidence l’effet de la température de cémentation sur la dureté et la microstructure résultantes, trois traitements sont définis avec la nouvelle version d’ALLCARB®. La profondeur de cémentation visée est de 2,5 mm et trois valeurs de température sont testées (tableau 3). La profondeur de 2,5 mm est choisie pour réduire la durée des tests. En effet, les séquences de cémentation pour atteindre une profondeur de 3,6 mm à 1 000 °C ont nécessité plus de 19 heures (figure 5 et tableau 3). Pour une nuance d’acier donnée et une profondeur de cémentation donnée, plus la température de cémentation est basse, plus le temps de diffusion du carbone est long. En effet, pour une profondeur ciblée de 2,5 mm, la durée de cémentation à 930 °C est plus de deux fois supérieure à celle à 980 °C (tableau 3).
La température de cémentation n’a pas affecté la précision des séquences de cémentation déterminées par ALLCARB®. Pour les 3 températures testées, la profondeur de cémentation obtenue est inférieure de moins de 0,1 mm à la valeur ciblée (tableau 3 et figure 9).
Les profils de dureté sur la figure 9 montrent peu de différences d’une température à l’autre. Aucune tendance claire n’est observée. Étant donné que les valeurs de dureté les plus élevées sont obtenues à 960 °C, la possibilité d’un optimum de température de cémentation doit être étudiée plus en détail. Le profil de dureté après la cémentation à 930 °C est inférieur aux 2 autres profils à chaque point de mesure.
Enfin, aucune différence significative n’est observée pour les microstructures obtenues (figure 10). Elles sont également proches de celle obtenue à 1 000 °C pour une profondeur de 3,6 mm (figure 7).
4. Conclusion
Le processus amélioré de cémentation multi-boost à l’acétylène, ALLCARB®, offre la possibilité de définir automatiquement des cycles de cémentation pour des profondeurs élevées et à différentes températures de manière fiable et stable. n
Références
[1] HERRING, D.H., Pros and Cons of Atmosphere and Vacuum Carburizing. Industrial Heating, pp. 45–48.
[2] SUGIYAMA, M., ISHIKAWA, K., Vacuum carburizing with acetylene. Advanced materials & processes, 1999, 155(4).
[3] MAKI, T., TSUKAZI, K., TAMURA, I., The morphology of microstructure composed of lath martensites in steels. Transactions of the Iron and Steel Institute of Japan, 1980, 20(4), pp. 207-214.
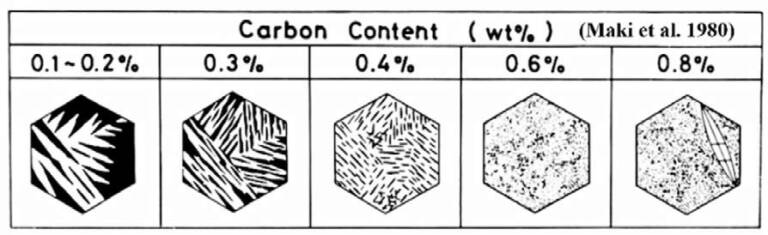
Figure 8 : Représentation schématique des lattes de martensite (blanc) dans les aciers Fe-C avec différentes teneurs en carbone[3]
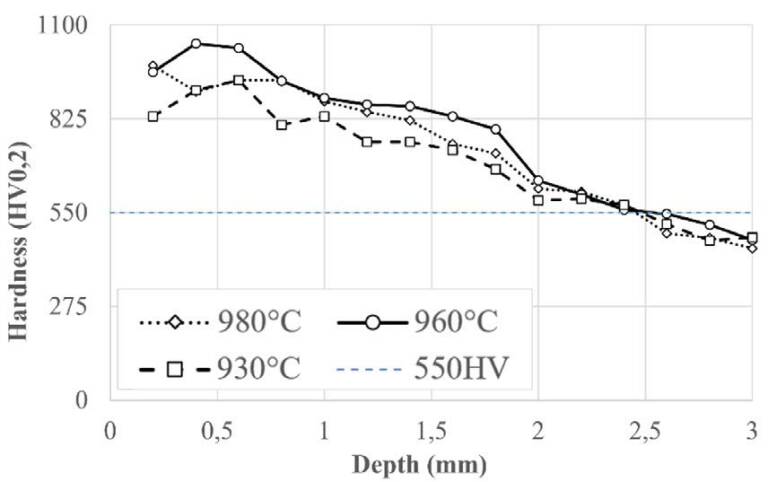
Figure 9 : Profils de dureté de trois pièces cémentées à une profondeur de 2,5 mm à différentes températures
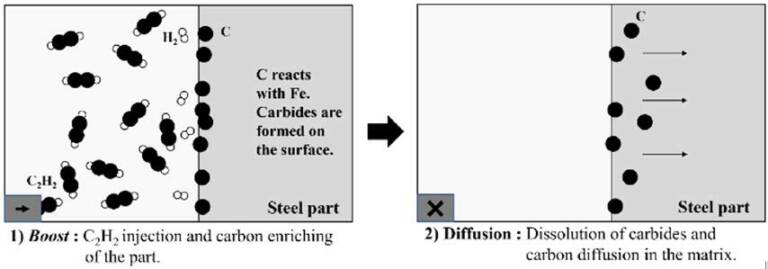
Figure 1 : Représentation schématique de l’enrichissement en carbone et de la diffusion lors de la cémentation basse pression avec de l’acétylène.
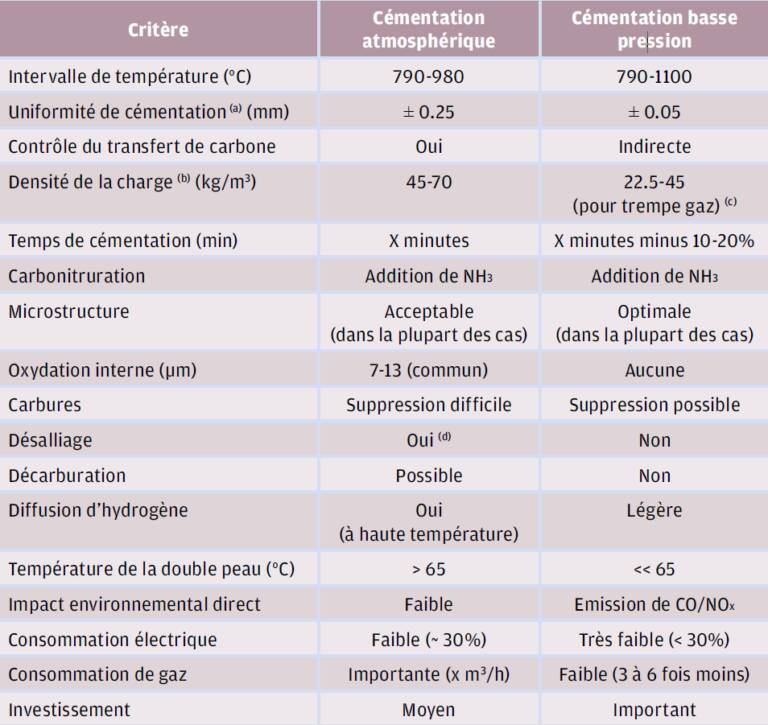
Tableau 1 : Comparaison entre cémentation en atmosphère et basse pression[1]
(a) Les processus de cémentation en atmosphère et sous vide diffèrent généralement en ce qui concerne le moment où les additions de gaz sont introduites. Cela a le plus grand impact sur l’uniformité de la couche. Dans la cémentation en atmosphère, le gaz enrichissant est généralement ajouté après le rétablissement du point de consigne du four. Selon la masse et la configuration de la charge de travail, un différentiel de température important peut exister entre différents endroits de la charge de travail. Dans le cas de la cémentation sous vide, une période de stabilisation est intégrée au cycle pour permettre à la charge de travail d’atteindre la température de cémentation avant les additions de gaz
b) La densité de charge dans l’équipement de cémentation sous vide est souvent limitée en raison de l’utilisation de chambres de trempe à haute pression de gaz.
c) Dans cet article, les fours BMI utilisent la trempe à l’huile et ne sont pas concernés par cette limitation.
d) En raison de l’oxydation à la surface de la pièce.

Figure 2 : Four vertical de trempe à l’huile sous vide de la famille V6_THC de BMI
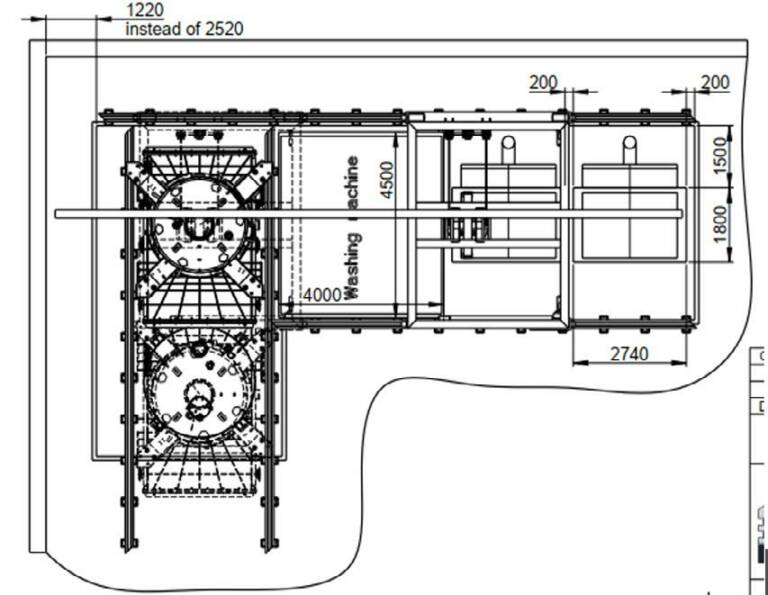
Figure 3 : Ligne de traitement thermique
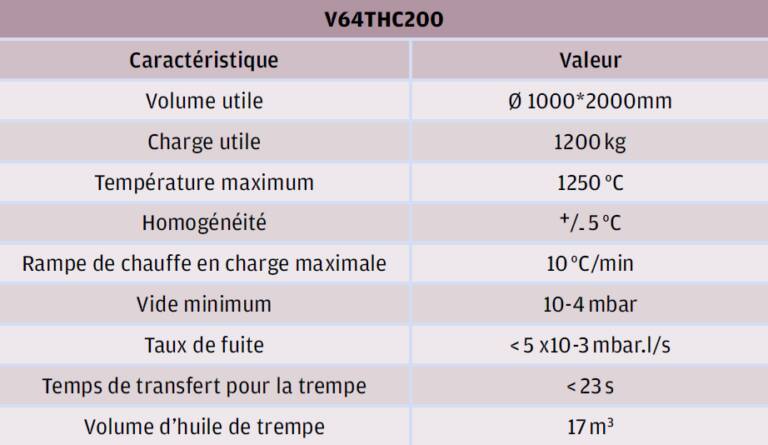
Tableau 2 : Caractéristiques du four
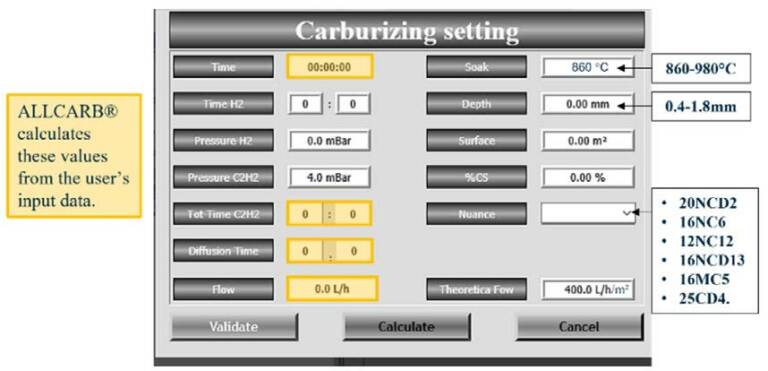
Figure 4 : Interface actuelle de ALLCARB®
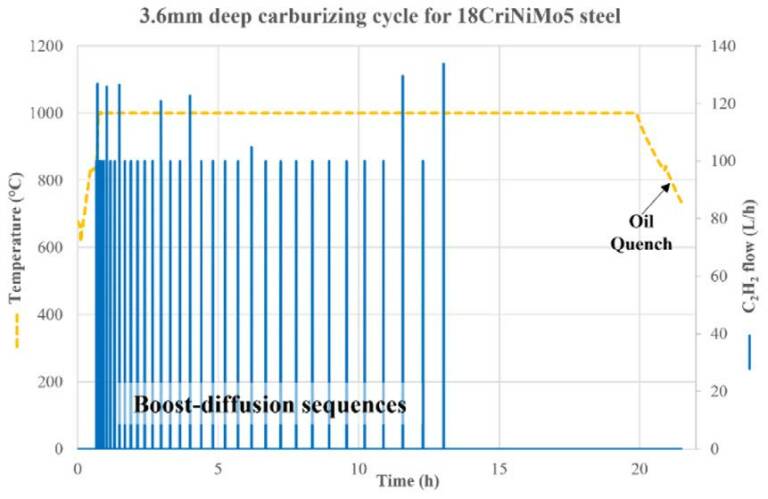
Figure 5 : Cycle de test sur 18CrNiMo5 avec ALLCARB® pour une profondeur de 3,6mm
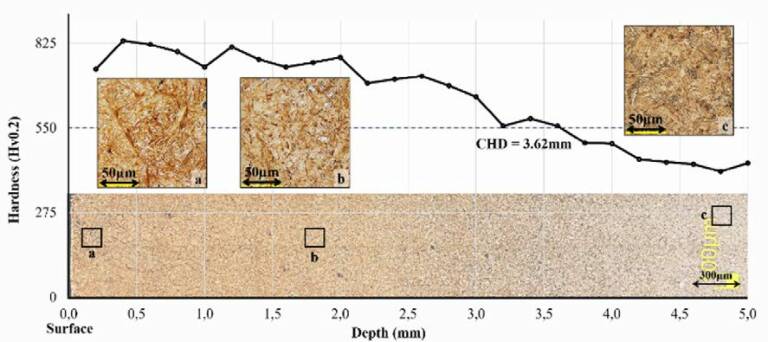
Figure 6 : Profil de dureté d’une pièce après cémentation profonde de 3,6mm
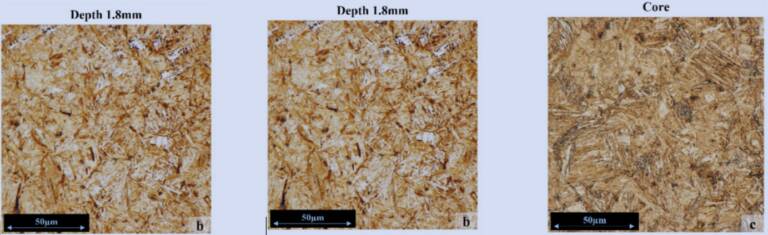
Figure 7 : Microstructures à différentes profondeurs en microscopie optique
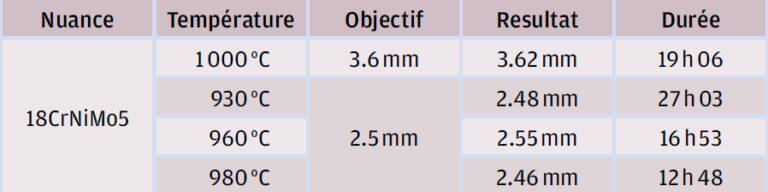
Tableau 3 :Données complémentaires sur les temps de cémentation
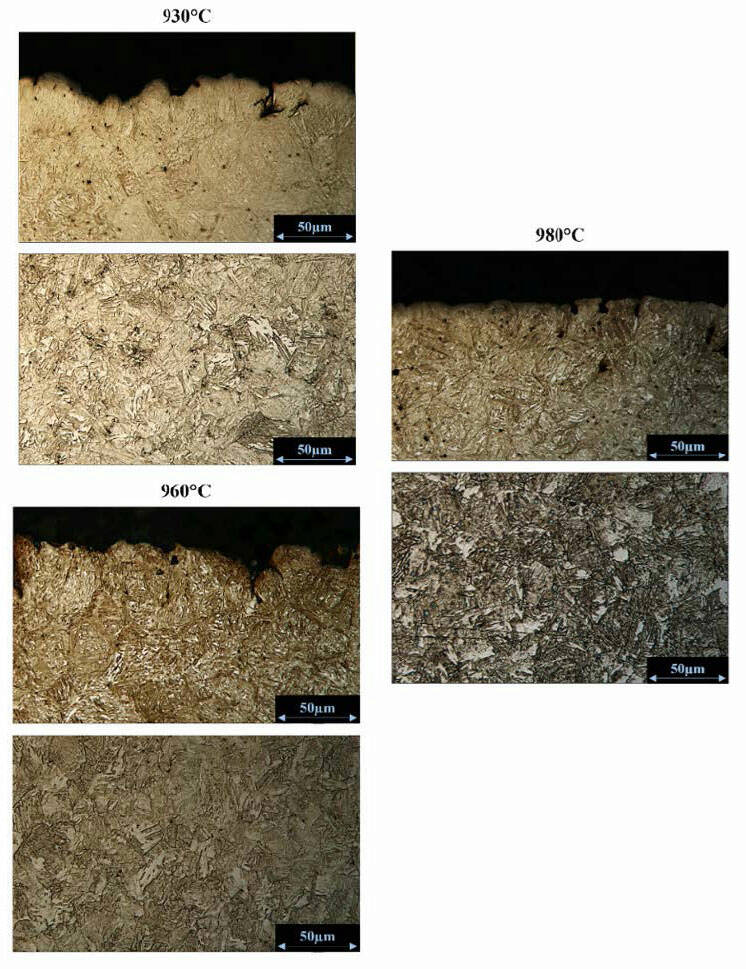
Figure 10 : Microstructure (près de la surface et du cœur) de trois pièces cémentées à une profondeur de 2,5 mm à différentes températures (microscopie optique)