État de l’art : de la tribologie à la nitruration en milieu liquide
Par Juliette Weisse, product manager, HEF Groupe, Hervé Gallien, development & industrialisation manager, HEF Groupe
Thibaud Troncin, product manager, HEF Groupe
Les enjeux tribologiques auxquels font face les industries se complexifient avec les différents développements technologiques amenés par une intensification de l’innovation. Aujourd’hui beaucoup d’acteurs cherchent des solutions à leurs problèmes dans des procédés nouveaux (nouvelle réglementation Euro 7, REACH et les alternatives au chromage dur, procédés plus respectueux de l’environnement…). Cependant, la nécessité de trouver des solutions à la fois viables et pérennes mènent parfois à rechercher dans les connaissances acquises, pour les perfectionner selon le contexte actuel. La progression des connaissances scientifiques de la maîtrise industrielle permet dans le cas de la nitruration en milieu liquide d’en faire une technologie d’avenir pour les problématiques tribologiques.
1. De la tribologie à la nitruration
La tribologie, littéralement la science étudiant les frottements, est plus largement le domaine d’étude des interactions entre surfaces solides en mouvement relatif. Ce domaine multidisciplinaire, développé à partir des années 1950, fait appel à de nombreuses disciplines comme le génie mécanique ou la science des matériaux. La terminologie tribologie recouvre, entre autres, tous les domaines du frottement, de l’usure et de la lubrification, qui peuvent être définis comme suit :
frottement : phénomène qui tend à s’opposer au mouvement d’une surface en contact avec une autre ;
usure : dégradation d’une surface qui se traduit par une modification de la géométrie, une perte de masse. On distingue plusieurs types d’usure, auxquelles s’intéresse plus particulièrement la tribologie :
- l’adhésion – le grippage
- l’abrasion – l’érosion
- le fretting
- la fatigue des surfaces
- la corrosion
- la tribo-corrosion ;
lubrification : ensemble des techniques permettant de réduire le frottement et l’usure entre deux éléments en contact et en mouvement l’un par rapport à l’autre.
Il est aisé de constater l’omniprésence de ces trois phénomènes au quotidien ; le frottement et l’usure sont inévitables, et pour y pallier, la lubrification est souvent nécessaire. Il est essentiel de relever que toutes ces interactions entre matériaux en mouvements relatifs interviennent au niveau des surfaces. C’est donc à ce moment-là que les phénomènes tribologiques peuvent être solutionnés.
Ingénierie des surfaces
L’ingénierie des surfaces désigne l’ensemble des savoirs et industries se rapportant à l’étude et aux moyens d’optimisation des surfaces, consistant à améliorer les propriétés fonctionnelles de ces surfaces.
Ces propriétés fonctionnelles, illustrées par la figure 1, ont un rôle capital dans l’industrie ; en 2017, elles représentent entre 8 et 9 % du chiffre d’affaires global de la sous-traitance industrielle du travail des métaux, et jusqu’à 15 % en comptant leur part dans les ateliers intégrés[1].
Le panel des industries concernées par l’ingénierie des surfaces est très large. Ainsi, les principaux secteurs d’activité sont la mécanique, l’automobile, l’énergie, l’aéronautique, le spatial, l’armement, le bâtiment, les travaux publics, le matériel électrique et le biomédical[1].
Traitements et revêtements
L’amélioration des propriétés techniques des surfaces s’opère par deux moyens : le traitement de surface et le revêtement de surface. Le revêtement consiste simplement à couvrir le substrat S avec un matériau d’apport A. Lors d’un revêtement, le matériau A et le substrat S ne réagissent pas, le A ne se diffuse pas dans le S et ne fait que le couvrir superficiellement.
Les traitements de surface, quant à eux, ne consistent pas seulement à apporter superficiellement un matériau. Ces derniers peuvent être classés en trois types distincts, comme l’illustre le tableau 1.
Chacun de ces types de traitement de surface regroupe de très nombreux procédés techniques apportant tous des propriétés différentes. Ainsi, par différents processus physico-chimiques modifiant la surface d’un matériau, les traitements de surface permettent de répondre aux enjeux tribologiques.
Traitements thermochimiques
Faisant partie intégrante des traitements thermiques superficiels, les traitements thermochimiques sont des procédés technologiques mettant en œuvre des réactions chimiques en relation avec la température. Par l’intermédiaire d’un milieu réactif, ces traitements par diffusion conduisent à des mécanismes de réaction superficielle et de diffusion d’un ou plusieurs éléments en profondeur. Ces différentes concentrations d’éléments diffusés conduisent à conférer des propriétés différentes aux surfaces des matériaux, leur but in fine étant d’augmenter les performances mécaniques des pièces traitées.
Comme illustré dans la figure 2, la diffusion d’élément A dans un matériau conduit à un profil de concentration progressif par palier. En extrême surface, l’élément A sera en importante concentration, dans la zone de diffusion sa concentration diminue progressivement jusqu’à disparaître.
Les éléments diffusés peuvent aussi bien être des métalloïdes (carbone, azote, bore) que des métaux (chrome, vanadium, aluminium).
La nitruration
La nitruration a été et continue d’être le principal traitement thermochimique qui, avec la nitrocarburation ferritique, représente le volume dominant des technologies de modification des surfaces industrielles.
Dans le langage courant, notamment à l’oral, le terme de nitruration englobe celui de nitrocarburation. Ce raccourci linguistique simplifie l’expression, mais porte parfois à confusion dans les esprits. Bien que différentes, la nitruration et la nitrocarburation restent très similaires dans leur procédé comme dans les fonctionnalités conférées. D’autres variantes de ces deux procédés existent sous la même appellation, comme le résume le tableau 2.
En effet, les procédés industriels de nitruration des alliages fer-carbone regroupent une famille de traitements ayant pour effet de convertir la surface en nitrures de fer (ou carbonitrures de fer). Ces traitements ont pour caractéristique commune de produire des structures dont l’archétype est le suivant :
une couche de combinaison composée de nitrures de fer en extrême surface dont l’épaisseur peut varier de 0 à 40 µm. Cette couche présente des caractéristiques particulièrement intéressantes, dont la dureté et les propriétés tribologiques[5] ;
une couche de diffusion, dont l’épaisseur typique est de quelques dixièmes de millimètre, dans laquelle l’azote est en solution interstitielle ou combinée sous forme de nitrures qui peuvent conduire, selon les éléments d’alliage présents dans l’acier, à des durcissements importants[5].
Ainsi, comme il est visible sur la figure 3, deux couches différentes sont ainsi créées du fait du processus de nitruration. Ces couches distinctes témoignent d’une propriété importante de la nitruration. Les procédés thermochimiques sont des traitements par diffusion[2]. Or, la nitruration est un procédé hybride, elle est à la fois un traitement par diffusion (couche de diffusion) et un traitement par conversion (couche de combinaison). Cette double propriété confère des avantages caractéristiques aux pièces traitées par nitruration[5 ou 6].
Les traitements de nitruration apportent de manière plus ou moins importante, selon les procédés et les matériaux traités, les caractéristiques suivantes :
dureté superficielle élevée ;
modification chimique par croissance d’une couche de combinaison ;
mise en précontrainte de compression de la surface.
Aussi, les propriétés qui en résultent sont principalement[6] :
augmentation de la résistance à la fatigue particulièrement en présence d’effets d’entaille et de concentrations de contrainte ;
amélioration de la résistance au grippage, au collage par adhésion et à l’usure par petits débattements, majoritairement grâce aux propriétés de la couche de combinaison ;
augmentation de la résistance à l’abrasion, par effet d’augmentation de la dureté ;
amélioration de la tenue à la corrosion après post-oxydation ;
augmentation de la tenue à chaud et résistance à l’adoucissement par revenu ;
perte de soudabilité.
Les traitements de nitruration possèdent également l’intérêt de ne pas nécessiter de reprise d’usinage après traitement, les déformations et gonflements sont minimes, les états de surface sont conservés ou maîtrisés[6].
Aussi, la possibilité de plusieurs finitions après traitement permet d’accentuer les caractéristiques conférées aux pièces traitées. Ces finitions peuvent être mécaniques ajustant l’état de surface (sablage, grenaillage etc.) ou des finitions chimiques pour améliorer l’aspect et la résistance à la corrosion.
Il existe trois principaux types de nitruration. Ceux-ci se distinguent par le milieux actif et l’agent diffusant en action dans leur procédé.
Milieu gazeux :
- Four sous atmosphère
- Four plasma ou ionique
Milieu liquide :
- Bains de sels ioniques fondus
La nitruration liquide
La nitruration liquide ou nitruration en bain de sels (SBN) est désignée ainsi, car elle s’opère dans des bains de sels ioniques fondus. Ainsi que le font les autres traitements thermochimiques de nitruration, les bains de sels, dans lesquels les pièces sont immergées, vont permettre de diffuser des atomes dans la surface. Cette diffusion d’atomes dans les mailles cristallines de la matière confère ainsi des propriétés mécaniques et tribologiques aux surfaces des pièces traitées.
Ces traitements sont parfois désignés sous le terme de « traitements en milieux liquides ioniques », dans la mesure où les réactions interviennent par réaction après décomposition en ions des composés présents.
Les traitements de nitruration sont encore largement utilisés industriellement par le monde. Aussi, par la diversité des traiteurs, les procédés technologiques varient en fonction des sels employés et de leur composition chimique. Les multiples recherches et développements effectués ont permis aux procédés de nitruration en milieu liquide d’évoluer au cours du temps.
Historiquement, la nitruration liquide était opérée dans des bains composés de cyanure. Ces bains, aujourd’hui désignés par l’adjectif « non-activé », procèdent tel que « aux températures de nitruration 500-550 °C, il est possible d’obtenir une réaction de nitruration à partir de la décomposition thermique d’un cyanure alcalin (potassium ou sodium). Les bains sont composés de 30 à 60 % de cyanure de sodium. »[6].
Ces traitements en bains composés à base de cyanure étaient réputés pour leur toxicité. Aussi, ces procédés archaïques n’étaient chimiquement pas optimisés, ce qui impactait souvent la qualité de traitement des surfaces.
Au cours des années avec les prises de conscience des enjeux sociétaux, en termes de santé et d’environnement, les procédés dangereux à base de cyanure sont peu à peu tombés en désuétude, remplacés par d’autres procédés.
Actuellement, ces procédés ne sont plus utilisés que par quelques acteurs mineurs récalcitrants. Depuis maintenant plusieurs décennies, l’industrie de la nitruration en bain de sels s’est très largement tournée vers les bains activés, dont le processus chimique est décrit par Leroux[6] :
« Les bains industriellement utilisés sont des bains à base de cyanate et de carbonate aérés par insufflation d’air. L’élément nitrurant est le cyanate CNO– qui se décompose suivant une double réaction de dismutation et d’oxydation :
Réaction de dismutation :
4CNO- → CO32- + 2CN-+2N
Réaction d’oxydation : 2CNO- + 02 → CO32- + CO + 2N
L’oxygène est apporté à la surface par l’air ambiant et par l’air comprimé introduit dans les bains.
Il s’y ajoute une réaction de carburation par le monoxyde de carbone produit :
CO → 1⁄2 O2 + C
L’essentiel des cyanures produits au cours de la réaction de dismutation est reconverti en cyanate directement par oxydation :
2CN- + O2 → 2CNO-
L’épuisement du cyanate aboutit à la formation de carbonate qu’il faut reconvertir en cyanate par régénération à l’aide d’un sel spécial, dont la nature exacte constitue le savoir-faire des procédés commercialisés sous les marques déposées. Le principe est d’utiliser un composé du type amine, comme l’urée, qui donnerait la réaction :
2 NH2 CONH2+CO32-
→ 2 CNO- + 2 NH3+CO2+H2O
Une de ces amines utilisées est le « melon », d’où le nom du procédé « melonite » employé aux USA. Cette réaction doit être contrôlée de façon à limiter les teneurs en vapeur d’eau et en ammoniaque dans le bain. La vapeur d’eau conduit à une augmentation du pouvoir oxydant du bain avec une tendance à former des oxydes avec les sels, entraînant une pollution du bain et une mauvaise qualité des couches (porosités importantes). L’ammoniaque NH3 augmente le pouvoir nitrurant du bain, mais favorise la croissance rapide des couches avec formation de porosités.
La couche de combinaison obtenue est majoritairement de structure Epsilon avec éventuellement, en limite de la zone de diffusion, une partie γ’, si le temps de traitement est prolongé ou dans le cas d’un refroidissement lent après le séjour dans le bain de nitrocarburation (elle correspond à un appauvrissement en azote par diffusion vers le cœur).
Comme le montrent ces descriptions chimiques, les procédés de nitruration liquide par bains activés (sels de cyanate) ne sont plus toxiques et néfastes comme pouvaient l’être les bains à base de sels de cyanure auparavant. De plus, la possibilité de conserver le milieu nitrurant d’une charge après l’autre , grâce à la régénération présentée ci-dessus limite grandement l’impact de la nitruration en milieu liquide sur les ressources naturelles.
2. Tribologie de la nitruration liquide
La nitrocarburation en milieu liquide est un procédé industriel mature. Des décennies de production ont permis d’en maîtriser les nombreux paramètres pour en faire un procédé robuste, stable et reproductible à grande échelle, tout en permettant une grande flexibilité pour obtenir les propriétés de surface souhaitées.
Les paramètres aisément ajustables sont :
le temps de traitement ;
la température de traitement ;
le type de finition.
Le couple de paramètres temps et température permet d’adapter le traitement à une large gamme de matériaux, des aciers bas carbone jusqu’aux aciers inoxydables en passant par les fontes.
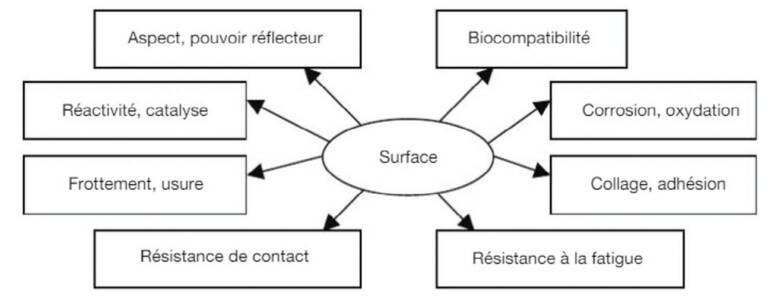
Figure 1 : Propriétés fonctionnelles d’une surface [1].
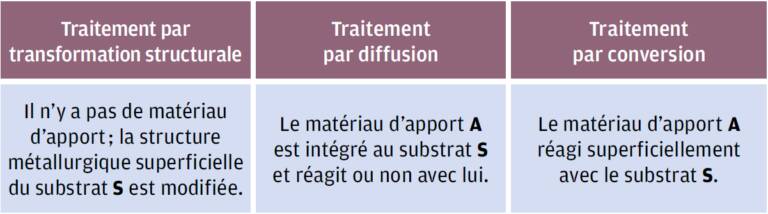
Tableau 1 : Les trois types de traitements de surfaces [2].
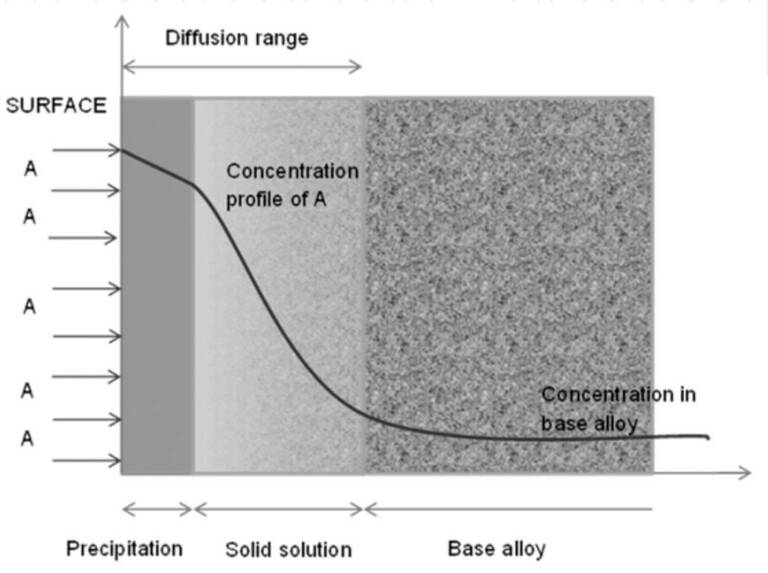
Figure 3 : Coupe d’une surface nitrurée. Attaque au nital, grossissement x500 [5].
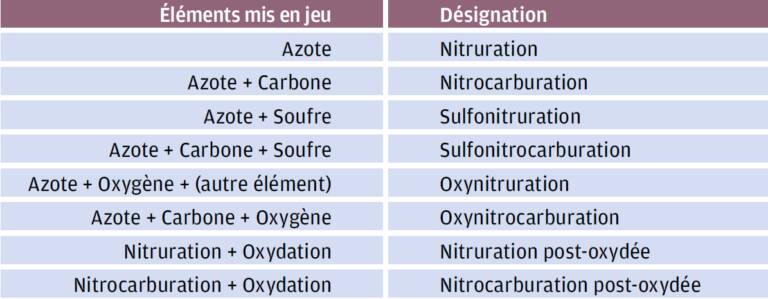
Tableau 2 : Désignation des procédés de la famille nitrurations selon les éléments mis en jeu [4].
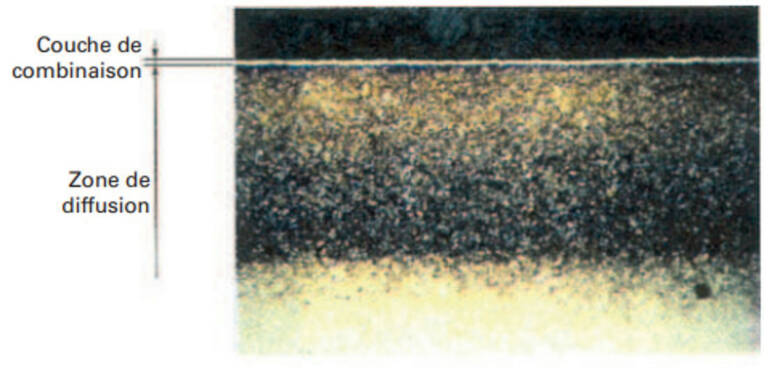
Figure 3 : Coupe d’une surface nitrurée. Attaque au nital, grossissement x500 [5].
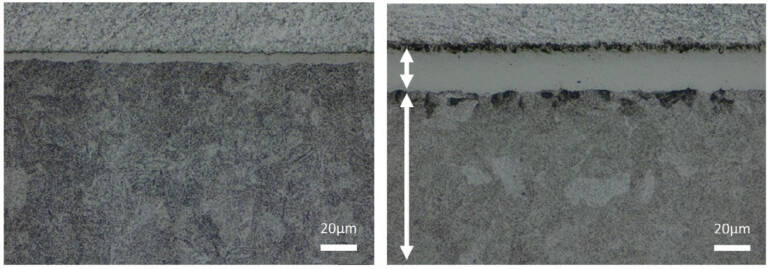
Figure 4 : Images métallographiques d’un acier 42CrMo4 QT nitruré à 630 °C pendant 30min (A) et 120min (B). Grossissement x500. Préparation : Nital 4 %.
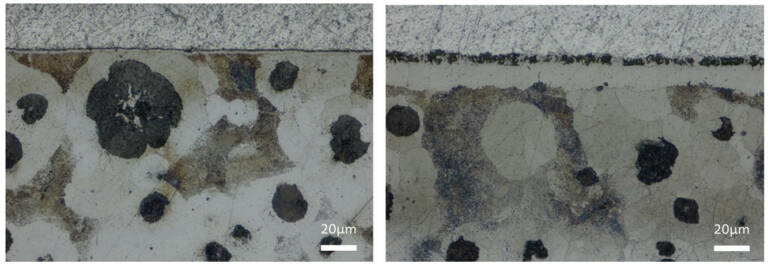
Figure 5 : Images métallographiques d’une fonte nitrurée à 630 °C pendant 30 min (A) et 120 min (B). Grossissement x500. Préparation d’échantillon : Nital 4%.
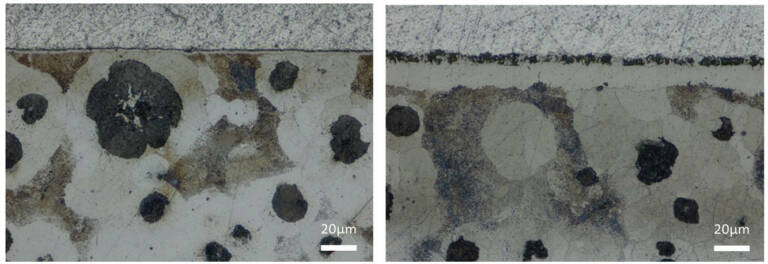
Figure 6 : Images métallographiques d’un acier XC38 nitruré à 630 °C pendant 30 min (A) et 120 min (B). Grossissement x500. Préparation d’échantillon : Nital 4 %.
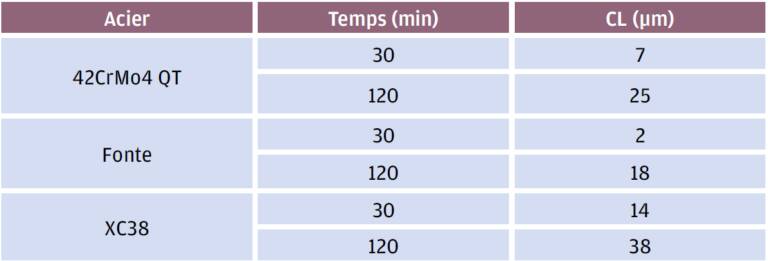
Tableau 3 : récapitulatif des épaisseurs de couches de combinaison en fonction du matériau et du temps.
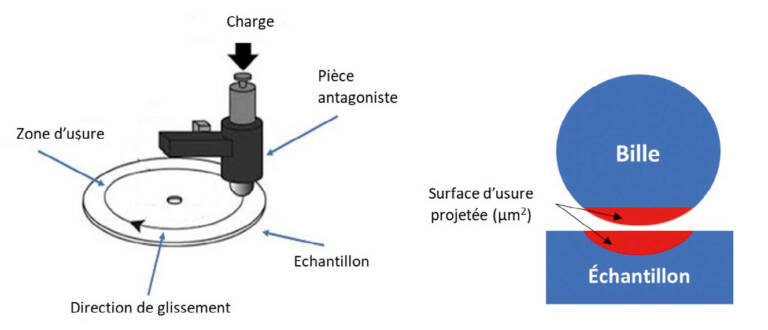
Figure 7 : schéma représentant l’essai de contact bille-plan pour mesurer l’usure des échantillons.
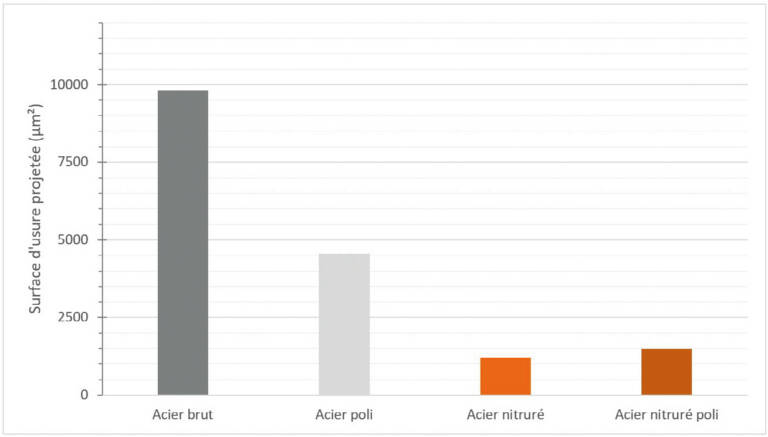
Figure 8 : Usure des différents échantillons
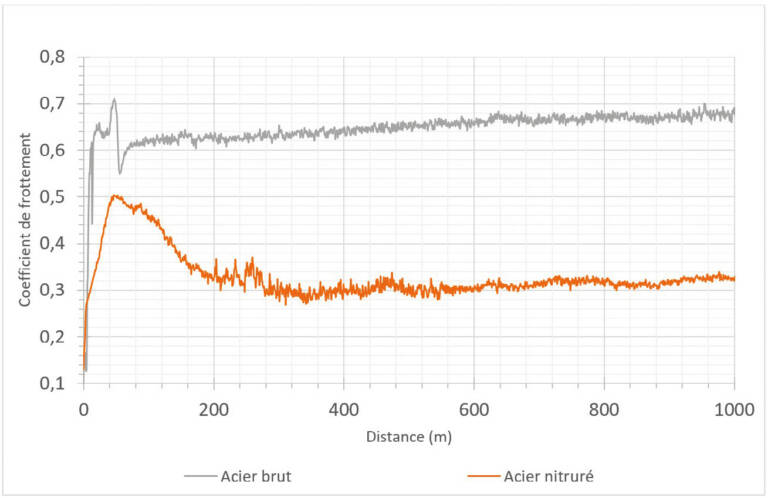
Figure 9 : Évolution du coefficient de frottement en fonction du nombre de cycles pour différents échantillons
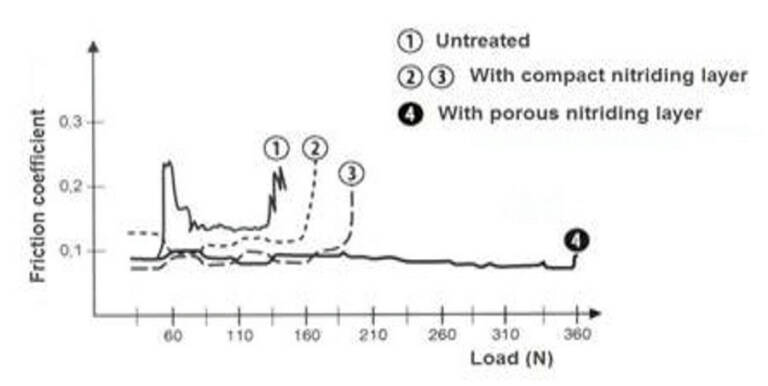
Figure 10 : Influence de la nature des couches de combinaison sur les performances en lubrification limite.[2]
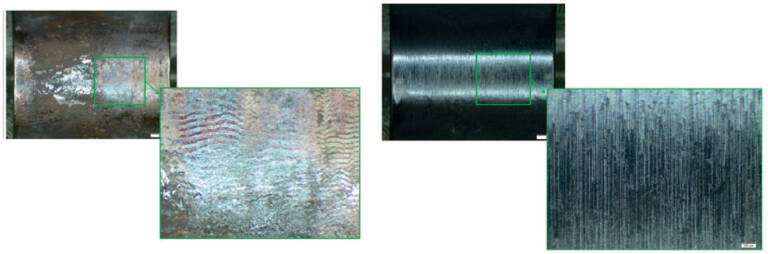
Figure 11 : Résultats des essais fretting corrosion, à gauche, l’acier trempé et à droite, celui nitruré.

Tableau 4 : Tenue en brouillard salin pour différentes finitions.
Ces deux paramètres vont influencer la vitesse de diffusion des atomes de carbone et d’azote à la surface du matériau. Cette vitesse de diffusion est propre à chaque matériau. En effet, plus un acier est allié, plus la diffusion d’azote est lente, car des éléments carburigènes tels que le chrome diminuent la vitesse de diffusion. Ceci est mis en évidence par les images métallographiques des figures 4, 5 et 6.
Les différentes épaisseurs de couches sont indiquées dans le tableau 3.
Comme démontré par les différentes couches obtenues ci-dessus pour des temps de traitement court comparativement à d’autre traitements thermochimiques, la nitruration en milieu liquide, par l’efficacité de son milieu nitrurant, offre une grande versatilité des résultats quel que soit l’acier concerné.
2.1 Résistance à l’usure et coefficient de frottement
La couche de combinaison a en grande partie un intérêt tribologique. Elle confère à la surface un coefficient de frottement bas pour de meilleures propriétés de glissement et donc une réduction considérable de l’usure.
Des essais comparatifs sur des échantillons nitrurés ont été faits avec des échantillons bruts. L’acier choisi pour ces essais est un 30CrNiMo8. Grâce à ces mesures, il est aussi possible d’évaluer l’influence du polissage et donc de la rugosité.
Les tests pour mesurer l’usure ont été réalisés via un calcul de pression de contact bille-plan (voir figure 7). L’usure est mesurée sur l’échantillon et également sur la pièce antagoniste. Les mesures des coefficients de frottement sont faits via un calcul de pression de contact cylindre-plan. La distance utile de frottement est de 2cm et les résultats sont présentés sur la figure 9.
D’après la figure 8, l’usure d’un acier brut est 8 fois plus importante que l’usure d’un acier nitruré. La force appliquée durant le test est de 2,5 N. De ce fait, la nitruration liquide prouve son grand intérêt pour les applications tribologiques et l’augmentation de la durée de vie des pièces traitées.
D’après la figure 9, les 200 premiers mètres peuvent être considérés comme une distance de rodage avant stabilisation du coefficient de frottement. Une fois stabilisé, le coefficient de frottement est deux fois plus important pour un acier brut que pour un acier nitruré. Cela permet un meilleur glissement et donc une usure moindre. La charge utilisée pour ce test est de 5N.
2.2 Propriétés tribologiques
La nitruration en milieu liquide permet d’obtenir une couche poreuse (du type e) avec d’excellentes propriétés anti-grippage. En effet, en régime de lubrification limite, les couches disposant d’une certaine porosité présentent des performances supérieures à celles obtenues avec des couches compactes, comme le présente la figure 10, et donc une durabilité plus importante. La nitruration liquide consiste donc en une solution possible aux problèmes de fatigue superficielle des contacts soumis à un glissement important.[2]
Exemple du fretting corrosion :
Des essais réalisés sur un acier 42CrMo4 permettent d’illustrer la très bonne résistance de la nitruration liquide. Un échantillon a subi une trempe par induction d’une épaisseur de 1,8 mm, l’autre échantillon a été nitruré d’une épaisseur de 0,2 mm. L’effort appliqué est de 500 daN avec une fréquence d’oscillation de 8 Hz. Le nombre de cycles est de 57 600. Les images prises à la fin du test (figure 11) montrent bien la présence d’oxydes à la surface de l’échantillon trempé, alors que celui nitruré présente uniquement des traces d’usures classiques.
2.3 Résistance à la corrosion
Une des propriétés recherchées par le traitement de nitruration est la résistance à la corrosion. Pour l’exemple d’un acier C45 avec une couche de combinaison de 20 µm, la tenue en brouillard salin (ISO 9227) est d’environ 24 heures. Il y a, cependant, des moyens d’améliorer de façon conséquente cette valeur.
Après nitruration il est possible de réaliser une post-oxydation, créant une fine couche d’oxyde de fer à la surface (1 à 3 µm). Cette étape va permettre d’atteindre des valeurs autour de 72 heures le brouillard salin.
Un autre paramètre à prendre en compte pour la tenue à la corrosion est l’état de surface de la pièce. Une rugosité faible Ra <0,3 µm permet d’obtenir de meilleurs résultats. Il en va de même pour la porosité. Une porosité importante de surface va diminuer la résistance à la corrosion.
Le tableau 4 résume les ordres de grandeur de tenue en brouillard salin pour différentes finitions après nitruration en milieu liquide.
Ces mesures ont été réalisées dans une enceinte brouillard salin suivant la norme ISO 9227 et dans les conditions détaillées dans la figure 13.
Avec une finition « grasse », la tenue à la corrosion est garantie pour de nombreux aciers. Il existe cependant deux familles de matériaux ferreux pour lesquelles la résistance à la corrosion reste limitée même après nitruration :
les fontes : en effet, les nodules ou lamelles de graphite présents en surface ne permettent pas de diffusion et empêche donc une protection uniforme de la surface. Des recherches sont actuellement menées pour améliorer la résistance à la corrosion ;
les aciers inoxydables : la couche de passivation est altérée durant l’étape de nitruration. Il n’est donc pas aisé de retrouver les mêmes propriétés anti-corrosion que pour un acier inoxydable brut. Cependant, lorsque l’opération de nitruration est effectuée, elle permet d’apporter des propriétés de résistance à l’usure bien plus importantes.
Les paramètres et avantages de la nitruration en milieu liquide ne se limitent pas à ceux présentés ici. La résistance à la fatigue, au grippage, la rétention d’huile sont également améliorés grâce au traitement.
Conclusion et ouverture
Grâce à ses propriétés versatiles et à sa richesse de plusieurs décennies de développements industriels, la nitruration liquide a su se perfectionner et s’adapter pour répondre aux exigences de nombreux secteurs (aéronautique, énergie, automobile, équipement de construction, armement).
Les développements industriels, appuyés sur des recherches et des processus d’amélioration continue, ont permis d’allier les intérêts techniques et économiques en combinant une maîtrise accrue du procédé et de ses paramètres à la grande flexibilité d’opération des procédés et la grande variété des caractéristiques techniques obtenues.
De nos jours, les industries, et en particulier du traitement thermique de surfaces, doivent travailler sur leur impact environnemental majoritairement lié aux consommations de matières premières et de ressources (eau, énergie).
Actuellement, des programmes, menés par un acteur du secteur, permettent de recycler les effluents des procédés de nitruration liquide pour les transformer en consommables directement réutilisables sur ligne de traitement. La figure 14 illustre le modèle d’économie circulaire dans le cas de la nitruration liquide. Le recyclage des effluents permet de réduire drastiquement l’extraction des matières premières, mais également de diminuer la consommation d’eau et les transports. Aussi, le volume de déchets ultimes est réduit de manière considérable et des recherches sont menées afin de complètement tendre vers le zéro déchet ultime sur les lignes de nitruration liquide.
Cette avancée permet ainsi aux technologies de nitruration liquide de s’inscrire dès à présent dans un cycle d’économie circulaire, permettant de combiner les intérêts tribologiques à ceux économiques et environnementaux que recherchent les industriels.