Apports du vide à l’élaboration des métaux et alliages et à leur traitement à l’état solide
Par Yves Bienvenu, MinesParisTech, Centre des Matériaux, UMR CNRS 7633
Les traitements des métaux et alliages par le vide se sont développés au fil des années. Les apports du vide sont notables. Article paru précédemment dans le n°397 de Traitements et Matériaux, septembre 2009.
Le « vide » fait partie de l’arsenal des procédés d’élaboration de nombre de métaux et alliages depuis le milieu du 20e siècle. Les unités sidérurgiques produisant des produits plats de qualité (très bas carbone ou bas hydrogène, oxygène…) peuvent traiter plus de la moitié de leur carnet de production d’acier liquide (c’est-à-dire des millions de tonnes/an) sous vide. Pour les autres métaux produits en (moindre) masse comme le cuivre, l’aluminium, les traitements par gaz neutres ou même réactifs semblent préférés actuellement. Pour le zinc et le magnésium, les pressions de vapeur saturantes élevées de ces métaux peuvent être mises à profit industriellement avec des procédés de réaction ou évaporation/condensation. Cette contribution n’a pour ambition que de présenter simplement (graphiquement quand c’est possible) quelques aspects fondamentaux (s’appuyant sur les thermodynamiques de l’équilibre entre phases et des solutions condensées ainsi que sur les cinétiques de réaction impliquant une phase gazeuse) et de présenter quelques « briques technologiques ». L’application considérée sera surtout l’apport du vide à l’élaboration à haute température (avec une comparaison à un traitement par « gaz neutre »).
Déplacements des réactions entre phases par le vide en pyrométallurgie
La plupart des métaux sont extraits de leurs oxydes (même si certains métaux sont surtout disponibles à l’état de sulfures, un grillage permettant de se ramener au cas des oxydes). Le premier diagramme de données thermodynamiques auquel il convient de se référer est un diagramme d’énthalpie libre de Gibbs, standard de formation des oxydes en fonction de la température, dit « de Ellingham » (figure 1). L’extraction d’un métal se fait par déplacement de l’oxygène lié au métal par un autre élément comme le carbone plus avide d’oxygène pour former CO et/ou CO2. L’utilisation de ce diagramme se fait donc en comparant deux courbes, celle relative à l’oxyde métallique que l’on souhaite réduire et celle relative au réducteur que l’on souhaite mettre en œuvre (bien souvent le carbone). Le diagramme nous indique alors la température à laquelle la réaction standard de réduction (pression des gaz : 1 atm, phases condensées pures et à leur état stable à la température considérée) peut se faire à l’équilibre. La place encore prépondérante du carbone en métallurgie extractive au 21e siècle peut simplement se justifier par la singularité des courbes relatives à l’oxydation de C en CO ou en CO2 qui interceptent la plupart des autres et aussi par la relative disponibilité du carbone. Il est également possible de tirer du diagramme la quantité de chaleur liée à la réaction et l’effet de l’activité du métal ou de son oxyde ou celui des pressions partielles des gaz.
Sur la figure 1, quelques indications ont été superposées sur le développement de la métallurgie à travers les âges. L’homme a en effet utilisé d’abord les métaux qu’il trouvait à l’état natif, les moins oxydables (vers le haut de la figure 1), Au, Ag, Cu… et dont il exploitait la ductilité pour les mettre en forme à l’état solide. L’âge du bronze suppose la maîtrise simultanée de températures de l’ordre de 1 000 °C pour la réduction/fusion de la charge métallifère riche en Cu et celle du charbon de bois comme réducteur. Un pas de géant est franchi dans « l’âge du fer » peu avant la Renaissance avec l’évolution des bas fourneaux en hauts fourneaux et l’utilisation de l’énergie des chutes d’eau pour souffler de l’air. L’amélioration des échanges thermiques permet d’atteindre 1 500 °C et la fusion des phases condensées dans le bas de la cuve avec une bonne séparation fonte/gangue pour une production de masse (1). D’autres « petits » pas complètent le développement du haut fourneau, comme l’adoption du coke de charbon et le développement de la conversion de fonte en aciers par puddlage puis au convertisseur. L’aluminium (bientôt suivi par les métaux les plus avides d’oxygène, ceux vers le bas de la figure 1) doit attendre la maîtrise de l’électrolyse de l’alumine en solution dans la cryolithe vers 950 °C avec les inventions de Héroult et de Hall dans la deuxième moitié du 19e siècle. L’âge du vide dans l’industrie apparaît encore plus tard, vers le milieu du 20e siècle. La maîtrise, pour des réacteurs de grand volume des technologies du vide, a contribué à élaborer avec une meilleure qualité et parfois plus économiquement les alliages les plus performants mais n’a pas permis de produire des métaux que les autres procédés ne permettaient pas d’élaborer vers l’année 1950.
Cette digression historique sur fond de thermodynamique étant faite, revenons à l’illustration de la thermodynamique des équilibres entre phases et au diagramme d’Ellingham en particulier des apports du vide dans l’élaboration des métaux (figure 2). Une illustration de cet effet est particulièrement importante dans le cas de l’extraction du magnésium par pyrométallurgie (les autres procédés étant basés sur l’électrolyse de chlorures de magnésium). Contrairement à la pyrométallurgie du fer, celle du magnésium n’est pas une carbothermie mais une métallothermie (utilisation d’un autre métal comme réducteur).
L’extraction du magnésium de son minerai dolomitique, carbonate mixte de magnésium et de calcium selon le procédé Magnétherm a été développé par Péchiney dans les années 1950 pour des unités produisant de l’ordre de 15 000 t/an. Dans un réacteur le minerai est porté à haute température, 1 550 °C, sous vide (jusqu’à 0,7 kPa) en présence d’un réducteur, en général un composé du silicium (ferrosilicium en général) et d’un fondant (aluminate de calcium) chauffé électriquement (figure 3). La réduction produit alors le magnésium vapeur qui est condensé à l’état liquide dans un second réacteur moins chaud, communiquant avec le premier (2). La courbe en pointillés de la figure 2 traduit l’effet d’un abaissement de la pression partielle de Mg avec abaissement du point de vaporisation et déplacement de l’équilibre de réduction global (somme algébrique de deux réactions du diagramme d’Ellingham).
Formule, voir pdf
L’abaissement de la pression « tire » la réaction vers la gauche selon le principe du déplacement de l’équilibre. Le fait que SiO2 soit combiné à CaO concourt aussi au déplacement. Cette réaction, contrairement à ce que suggère la formule ci-dessus est en fait une réaction liquide (ferrosilicium)/liquide (laitier saturé en MgO)/vapeur. La productivité est dictée par l’agitation et aussi par la puissance de chauffage. Le magnésium produit par le procédé Magnetherm est affiné pour éliminer les impuretés calcium et silicium. Le même type d’effet de la pression partielle exprimé par la réaction [1] existe pour tous les métaux relativement volatils, le zinc en particulier.
Traitement du métal liquide par le vide avant coulée
Les applications les plus impressionnantes en termes de capacité et productivité des installations et les plus récentes se situent dans le traitement de l’acier liquide. Après avoir illustré les bases thermodynamiques et cinétiques, nous aborderons les différentes technologies et essaierons de comparer traitement par le vide et par les gaz neutres. Ces opérations appartiennent à ce qui est appelé métallurgie secondaire, en séquence avec les convertisseurs à l’oxygène ou les fours de fusion électrique qui gagnent en productivité en étant déchargé des missions les plus délicates, comme la mise a la nuance, l’élimination d’éléments indésirables (dont les gaz dissous et les inclusions d’oxydes et de sulfures) et le réglage de la température avant coulée continue (3,4). L’introduction de la métallurgie secondaire dans le dernier quart du 20e siècle rajoute une brique technologique mais réduit les coûts de fonctionnement en diminuant le taux de déclassement et de recirculation des coulées de métal liquide, en donnant de la souplesse entre les ateliers de conversion à l’oxygène et les coulées continues et surtout en permettant de diminuer le temps de cycle des convertisseurs ou four électrique dont la mission se limite à la conversion ou à la fusion. Les réactions de dégazage sous vide et les transferts métal laitier contribuent respectivement aux réductions des teneurs en C, H, N, O, P et S. La nécessité de dégazer les aciers est illustrée par la variation de la solubilité des éléments H et N en fonction de la température dans les variétés allotropiques du fer en fonction de la température (figure 4). L’hydrogène rejeté à la solidification de l’acier dans le liquide peut former des soufflures dans le solide, phénomène commun aussi pour le cuivre. La métallurgie secondaire, constitue la dernière chance d’élimination de H et N avant la coulée et c’est sous vide que se pratique cette élimination à l’interface métal liquide/atmosphère.
L’équilibre entre atmosphère et métal liquide (ou solide) sous forme de loi de Sievert, loi d’action de masse associée à la réaction de dénitruration 1/2 N2 <-> N s’écrit :
Formule, voir pdf
où % N désigne la teneur massique en azote en solution dans le métal et PN2 la pression partielle d’azote dans l’atmosphère résiduelle (idem pour H). La valeur de la constante keq décroit avec la température et elle peut s’obtenir facilement de la figure 4 qui regroupe les données relatives à l’azote et à l’hydrogène (3). Les cinétiques de dénitruration et déshydrogénation dépendent de l’aire d’interface métal liquide/atmosphère, du renouvellement du liquide sous cet interface et aussi de la qualité de cette interface (présence ou non de tensioactifs qui immobilisent les sites de transfert). Pour la déshydrogénation, une loi cinétique du premier ordre peut être écrite :
Formule, voir pdf
où A et V sont l’aire d’interface vide/bain et le volume du bain, %Heq la teneur en hydrogène en solution en équilibre avec l’atmosphère résiduelle du vide (négligeable devant % H pour l’essentiel du traitement) et kcin une constante cinétique proportionnelle à la racine carrée du produit de la diffusivité de l’hydrogène dans le bain (environ 10-3 cm2/s) et du taux de renouvellement d’un élément de volume de liquide sous l’interface (5). Le taux de renouvellement peut être accru par brassage du bain par injection de gaz inerte.
L’oxygène dans un acier non calmé (désoxydé par Al ou Si+Mn) ne peut s’éliminer sous vide que par formation d’oxydes gazeux, CO, selon la réaction de décarburation/ désoxydation :
Formule, voir pdf
avec la constante d’équilibre associée (relation de Vacher-Hamilton) :
Formule, voir pdf
La réaction est plus complexe que la dénitruration car deux éléments sont couplés et la cinétique est limitée par la germination des bulles dans le métal liquide et leur croissance qui peut aussi dépendre de la présence de tensio-actifs (S et O) dissous dans le métal liquide. La remontée des bulles et leur éclatement à la surface n’est pas un frein. La loi cinétique (du premier ordre) peut s’écrire pour la teneur en carbone dissous %C par exemple suivant la forme différentielle :
Formule, voir pdf
La constante cinétique pour la décarburation dépend aussi de la teneur en oxygène et de celle en soufre (pour la qualité des interfaces bulles/acier liquide) (6,7). La variation de la teneur en oxygène est liée à celle du carbone par les coefficients stœchiométriques de la réaction [4]. La teneur en oxygène de l’acier sauvage à la versée d’un convertisseur est de l’ordre de 0,05 % en équilibre avec une teneur du même ordre en oxygène dissous. Par dégazage sous vide, on obtient en quelques minutes moins de 0,02 %, teneur qui peut être encore abaissée par une faible addition d’aluminium (5).
Les installations de vide dans les plus grands sites sidérurgiques permettent de traiter des poches d’acier liquide de 300 t. Le vide est actuellement réalisé par des systèmes à venturi (éjecteurs de vapeur) dont le bilan énergétique est variable suivant le contexte des sites mais un fabricant de pompes « sèches » annonce pouvoir faire face aux débits de gaz et au niveau de pression requis avec des gains énergétiques par rapport aux éjecteurs à vapeur. De nombreuses variantes technologiques pour exposer la surface du métal liquide sous vide sont décrites dans (4,8) :
• poche entière sous vide, l’étanchéité étant réalisée par un couvercle et un joint d’étanchéité sur la carcasse métallique de la poche ou poche placée dans un caisson sous vide de grand volume,
• poche avec recirculation, une partie du métal est aspirée par le vide hors de la poche dans un réacteur annexe sous vide relié à la poche par deux jambes, la circulation étant assurée par injection de gaz neutre dans une jambe (figure 5). La vitesse de recirculation peut atteindre 150t/min et plusieurs m/s dans les « jambes » (5,8).
Les pertes thermiques d’une poche de métal de grande capacité à 1 600 °C représentent plus de 2 °C/min et elles doivent être compensées par des températures de coulée du convertisseur plus élevées ou par un système de réchauffage à 5 °C /min au moins par arc électrique, par induction ou par aluminothermie, c’est-à-dire la réaction exothermique entre une addition d’aluminium et une injection d’oxygène. Le vide se fait jusqu’à 100 Pa par des éjecteurs de vapeur. Le procédé RH (Rhurstahl-Heraeus, figure 5) est cher en investissement et en coût de réfractaire mais l’aire d’interface liquide/atmosphère est grande et propre, le métal est fortement agité sous vide, donc les traitements sont rapides et limitent les pertes de métal par éclaboussures en les confinant dans le réacteur sous vide.
Comparaison des traitements sous vide et par injection de gaz neutres des métaux liquides
Le traitement par le vide n’est pas la seule option pour activer les réactions de dégazage en métallurgie secondaire. Le brassage par injection de gaz neutre permet, comme le vide, au sein des bulles, de disposer d’une pression partielle de N2, H2 ou CO relativement faible par dilution à l’argon de l’azote, de l’hydrogène et du CO dans les réactions [2] et [4]. Le brassage par bullage (introduit par des bouchons poreux en fond de poche ou par lance immergée) a l’avantage de bien homogénéiser le métal et aussi d’accélérer les transferts métal/laitier (pour les impuretés S et P). Une comparaison technico-économique doit être faite dans chaque contexte. Très schématiquement, les investissements nécessaires aux installations de traitement seraient nettement moins élevés pour les gaz neutres mais le coût du consommable gaz serait sans commune mesure à celui du vide. Les installations les plus récentes combinent d’ailleurs vide et bullage de gaz neutre. Le brassage par gaz neutre commence dans les dernières minutes de la conversion pour les aciers peu alliés. Pour les aciers inoxydables, le soufflage de gaz neutre dans un rapport 3/1 par rapport à l’oxygène en fin d’affinage AOD (argon oxygen decarburizing) décarbure sans trop oxyder le chrome. La réaction [4] est d’ailleurs facilitée dans le cas des aciers inoxydables austénitiques par un coefficient d’activité du carbone de l’ordre de 3 (1 pour les aciers au carbone). Des teneurs en carbone inférieures à 0,02 % sont obtenues couramment en AOD (9). La décarburation sous vide est aussi possible pour les aciers inoxydables dans une installation VOD (vacuum oxygen decarburizing). L’oxygène peut être soufflé à la surface du bain jusqu’à une pression partielle de 0,2 atm et dans la mesure où la teneur initiale en carbone ne dépasse pas 0,5 %, les teneurs finales peuvent atteindre 0,005 %. Les fonderies d’acier inoxydables, malgré les tailles modestes des poches peuvent aussi investir dans une installation VOD, moins coûteuse qu’un AOD (6).
Les exemples précédents des applications du vide à l’affinage avant coulée se rapportent à l’acier liquide. Des exemples assez proches et récents peuvent être trouvés pour le cuivre mais à des échelles de dizaines et non de centaines de tonnes. L’aluminium se traite aussi avant coulée, pour la déshydrogénation et l’élimination du sodium en premier lieu, mais par l’action de gaz neutres. La localisation du traitement est dans un chenal peu profond et la technologie est par brassage/bullage (autrefois du chlore, maintenant des gaz neutres) avec des rotors immergés.
Vide et procédés émergents de traitements à l’état liquide
Le fait de pouvoir hisser par le vide un bain d’acier liquide (ou de cuivre) de plus de 1 m permet des recirculations de liquide dans des procédés totalement continus en métallurgie des non-ferreux. Des réacteurs (certains en milieu oxydant, d’autres en milieu réducteur ou sous vide) et décanteurs en cascade utilisent la gravité pour les écoulements des uns aux autres et l’élévation par le vide et l’entrainement gazeux pour des boucles de recirculation. Actuellement des développements de procédés d’extraction simultanée du titane et du fer de l’Ilménite ainsi que pour le cuivre, le plomb et le zinc (par vaporisation dans l’élévateur à métal et condensation dans un réacteur annexe) sont prometteurs avec des économies d’énergie par rapport aux procédés discontinus (10).
Un autre apport intéressant (mais plus vraiment récent) du vide est celui de la refusion sous vide dans des fours à arc à électrode consommable (procédé VAR). Ce procédé est indispensable pour les éponges de titane, à la fois pour la mise en forme et en structure et pour l’affinage du métal permis par l’exposition à un bon vide de gouttelettes de liquide refondues par l’arc puis du bain de liquide en cours de solidification. Les lingots peuvent mesurer 600 mm de diamètre et peser plus de 5 t (11). Le procédé VAR s’applique au zirconium, aux superalliages et aciers de haute performance.
Traitement d’un métal solide sous vide
Nous nous limiterons aux réactions d’évaporation/condensations qui sont parfois voulues et souvent subies lors d’un traitement thermique d’un métal solide en four en nous appuyant sur un article de synthèse de l’A3TS (12). Un alliage constitué d’éléments désignés par l’indice i est à l’équilibre avec une atmosphère ou chaque élément constitutif est présent avec une pression partielle Pi, produit de l’activité (ai, de l’élément i dans l’alliage, échelle dite de Raoult (13), par la pression de vapeur saturante de l’élément pur à son état standard à la température de l’alliage (figure 6).
Formule, voir pdf
Les éléments stables sous forme gazeuse ne se trouvent pas sur la figure 6 mais le cas de l’azote et de l’hydrogène dans le fer solide est traité par ailleurs dans la figure 4. Si on s’intéresse à la cinétique des échanges entre une atmosphère résiduelle de four, caractérisée par une température et des pressions partielles, Tres et Pires et un solide, toujours pour un élément i, en considérant les flux d’atomes ou molécule en masse (masse molaire Mi) par unité de temps et de surface libre du métal selon la relation dite de Hertz-Knudsen (14) qui doit beaucoup aux travaux de Langmuir et à la théorie cinétique des gaz :
Formule, voir pdf
Le coefficient a désigne la fraction des sites de surface disponibles pour les échanges d’évaporation condensation, c’est-à-dire les sites non occupés par des molécules ou atomes de gaz neutre ou d’oxygène adsorbés. Sur une facette cristallographique seuls les sites en bordures de cette facette sont véritablement actifs. Le coefficient a qui dépend de la cristallographie locale dépasse rarement 0,3. L’équilibre d’évaporation-condensation est atteint quand Ji = 0 pour tous les éléments de l’alliage polyconstitué. Si Tres et Pires caractéristiques de l’atmosphère sont égaux aux paramètres physiques correspondants de l’alliage, on vérifie que les flux net sont bien nuls (équilibre thermodynamique). S’il existe un point froid dans l’environnement de l’alliage dans le four, la température Tres sera abaissée et un flux net des éléments les plus volatils s’établira de la surface de l’alliage vers le point froid. Dans les échanges entre un métal et son environnement-four non homogène en température, il convient de prendre en compte les angles solides sous lesquels le métal « voit » les différents éléments (comme dans les échanges radiatifs de chaleur). Les flux de la relation [8] deviennent faibles quand l’atmosphère résiduelle est non négligeable (0,1 atm), car il se forme alors autour du métal une couche limite de gaz à l’équilibre avec l’alliage et la cinétique des échanges est alors contrôlée par la cinétique de diffusion gazeuse dans la couche limite. L’activité thermodynamique de l’élément i à considérer est celle de la surface du matériau qui peut diminuer avec le temps si le flux net est négatif. Cette situation est l’opposée de celle rencontrée dans la cémentation gazeuse des couches superficielles dont les aspects fondamentaux sont traités dans une publication de l’A3TS, (14). La diffusion à l’état solide des éléments i entre cœur et surface de l’alliage intervient alors sur une épaisseur caractéristique d’environ 2(Dit)0,5 où Di , en m2/s, est le coefficient de diffusion apparent de l’élément i dans le solide et t, en secondes, le temps de traitement isotherme. Remarquons que l’énergie d’activation de l’évaporation-condensation est bien supérieure à celle de la diffusion dans le solide, ce qui explique que l’appauvrissement superficiel en élément volatil devient plus marqué avec la température.
Pour les aciers, l’hydrogène est, semble-t-il, le seul élément pouvant être dégazé à l’état solide dans des traitements thermiques longs de près de 12 h en « couveuse » (de 150 °C à 300 °C sous air ou azote) car la diffusion de H à l’état solide est compatible avec une élimination sur quelques cm à partir d’une surface libre et sa cinétique d’évaporation est 8 fois plus rapide que celle du fer à une température donnée. Cette pratique est essentiellement limitée aux rails dont les longueurs standards les plus courantes sont 36 et 80 m. On imagine la taille des « couveuses » disponibles seulement en quelques exemplaires en Europe et on comprend la difficulté d’assurer le vide.
Pour les cuivreux, la dézincification thermique des laitons est observée lors de traitements en four-cloche de recuit statique de recristallisation de bandes laminées à chaud. Pour éviter les problèmes liés à l’oxygène dans les alliages de cuivre, l’atmosphère est légèrement oxydante (15). Le zinc évaporé entre les spires plus ou moins jointives réagit avec l’oxygène et appauvrit l’atmosphère résiduelle en cet élément, mais la couleur superficielle des bandes est affectée par la dézincification et peut être restaurée à froid par un décapage acide.
Pour les alliages d’aluminium, l’utilisation industrielle du vide est rare. Au laboratoire, lors de sa mise en solution à 535 °C en bain de sel et dans une ampoule scellée sous vide (sans oxydation), l’alliage 6061 avec 0,8 % de Mg renforcé par des plaquettes d’alumine subit des pertes en Mg notables sur quelques mm (figure 7) Cette perte s’interprète selon l’effet d’une évaporation-condensation de Mg et par la diffusion à l’état solide de Mg (12,16). Le flux de diffusion de Mg à l’état solide calculé est cependant 100 fois inférieur au flux calculé par l’équation de Langmuir (premier terme de [8], l’évaporation, en tenant compte de l’activité de Mg mais avec a = 1). Ceci est dû au fait que l’ampoule est d’un volume fini et que la condensation est non négligeable (deuxième terme de [8]).
L’évaporation/condensation explique aussi la carburation dans les fours sous vide à résistance de graphite (nécessairement plus chaudes que la charge), ce qui ne pose pas de problèmes pour les carbures cémentés ou les aciers à outils mais en pose pour d’autres. La pression de vapeur saturante de C, de l’ordre de 0,1 Pa à 2 000 °C est en effet suffisante pour carburer les pièces traitées car sa diffusivité est élevée dans l’atmosphère et dans le solide.
Des réactions plus complexes de l’alliage avec l’atmosphère résiduelle des fours conduisent à la formation de composés volatils comme les sous-oxydes de Mo, W, Cr et SiO (12). Pour les atmosphères riches en halogénures, on peut citer des réactions avec formation d’halogénures volatils (cas important en pratique pour les lampes à halogènes ou pour certains traitements de surface en phase vapeur).
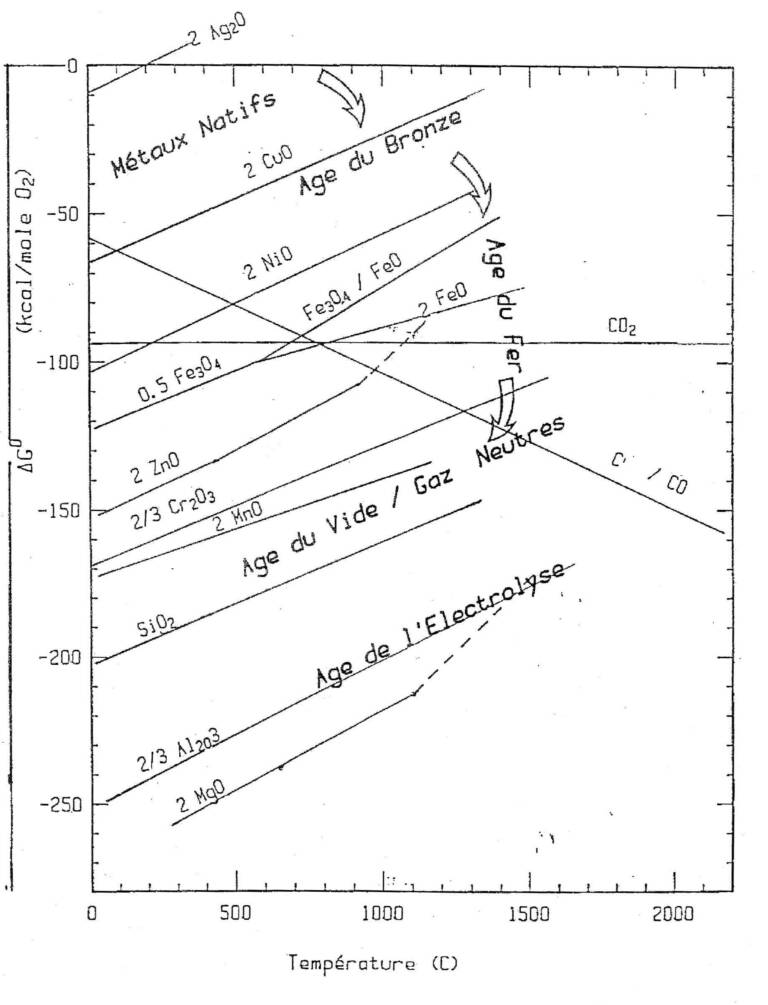
Figure 1 : Diagramme d’Ellingham pour les oxydes d’une sélection d’éléments d’intérêt en métallurgie extractive, énthalpie libre standard DG0 de formation des oxydes (pour une mole d’oxygène) en ordonnée et température en abscisse. On notera les courbes relatives à l’oxydation de C en CO et en CO2 qui se singularisent en intersectant les autres ; ce qui, combiné avec la disponibilité à ce jour du carbone, justifie le développement des métallurgies extractives basées sur le carbone.
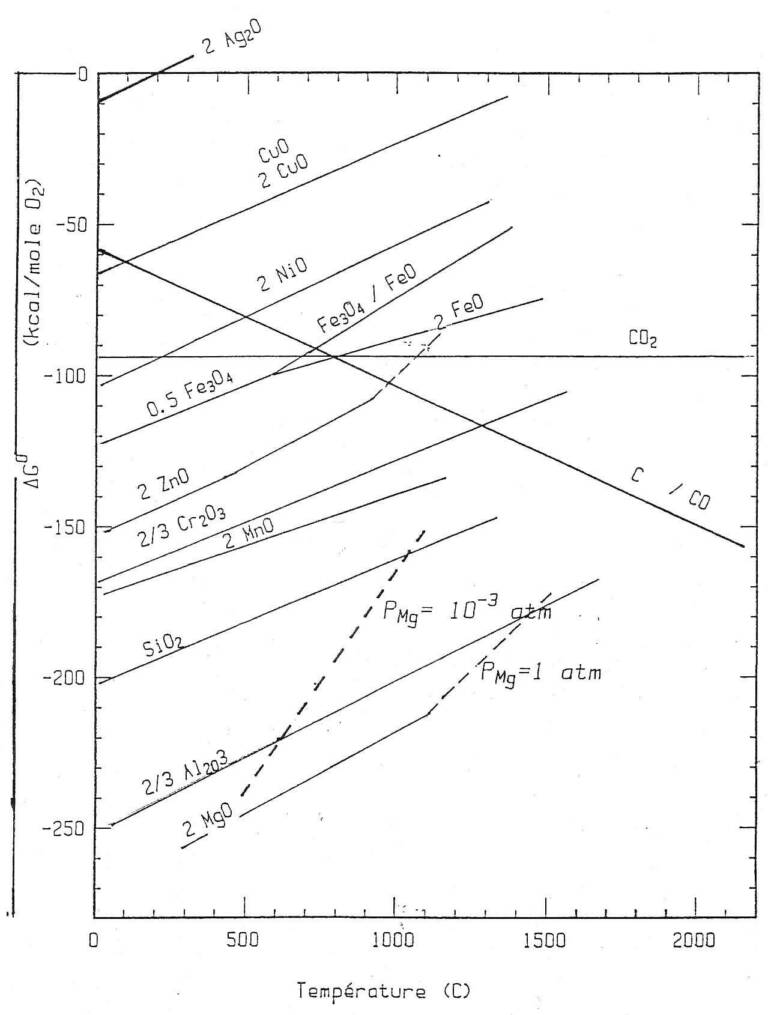
Figure 2 : Diagramme d’Ellingham d’après les Techniques de l’Ingénieur M 1630. L’effet de l’abaissement de la pression de magnésium par le vide est illustré. Grâce au vide, le silicium peut déplacer Mg de son oxyde à des températures moyennes (autour de 1 000 °C contre plus de 1 500 °C sans le vide). Ceci constitue un exemple de métallothermie.
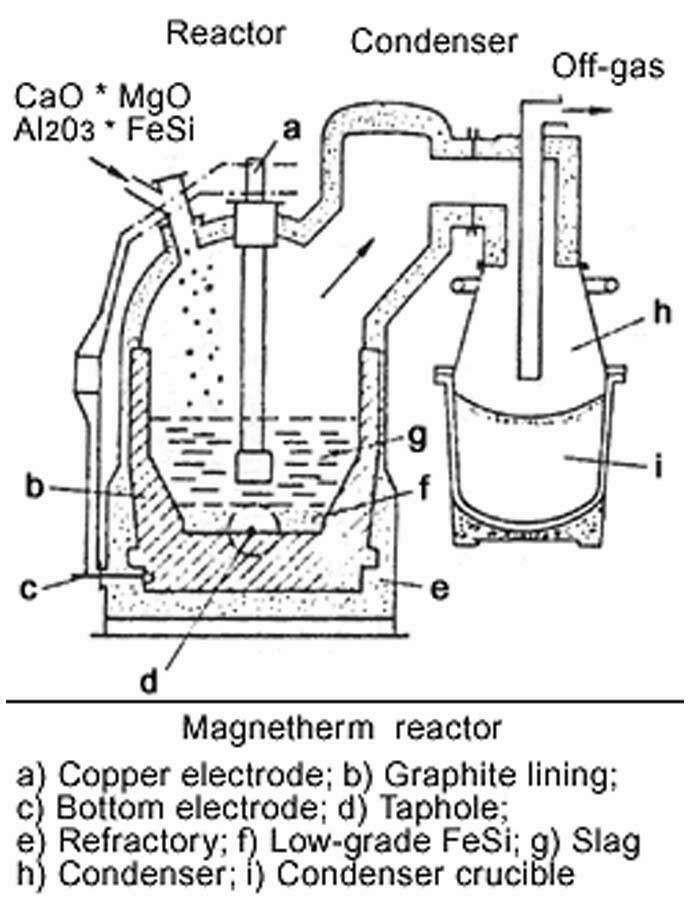
Figure 3 : Schéma du procédé Magnetherm de production du magnésium par métallothermie sous vide. Le procédé développé par Péchiney et adopté dans différents sites a produit plus de 60 000t/an. www.magnesium.com
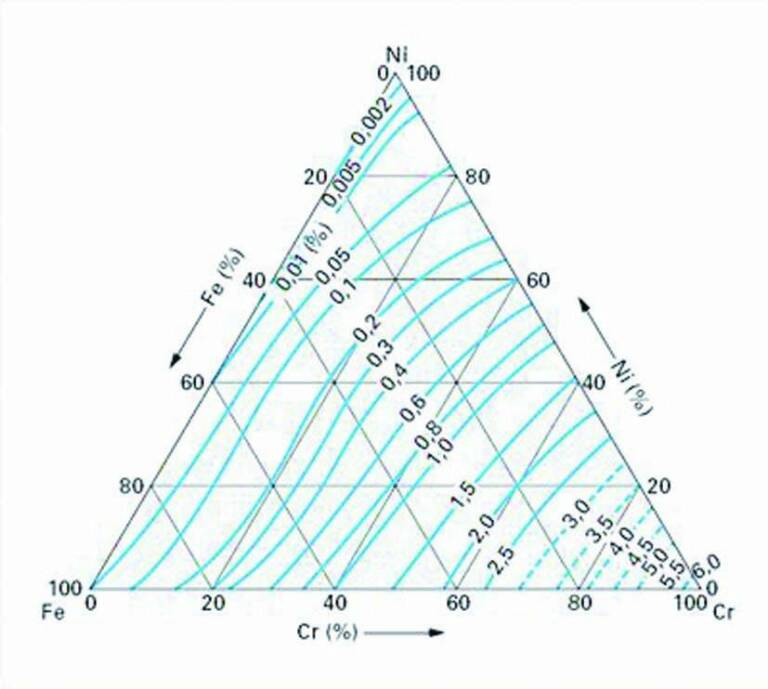
Figure 4 : Solubilité des gaz hydrogène et azote dans le fer en fonction de la température extrait des Techniques de l’Ingénieur (3).
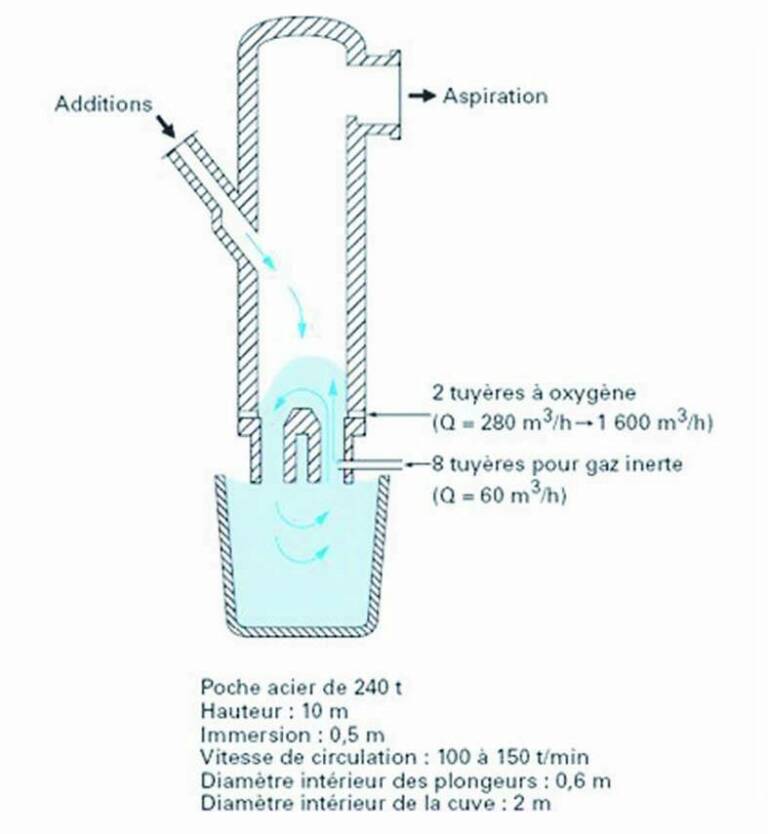
Figure 5 : Un exemple schématique d’installation d’acier liquide sous vide : technologie RH-OB de Arcelor-Dunkerque extrait des Techniques de l’Ingénieur (4).
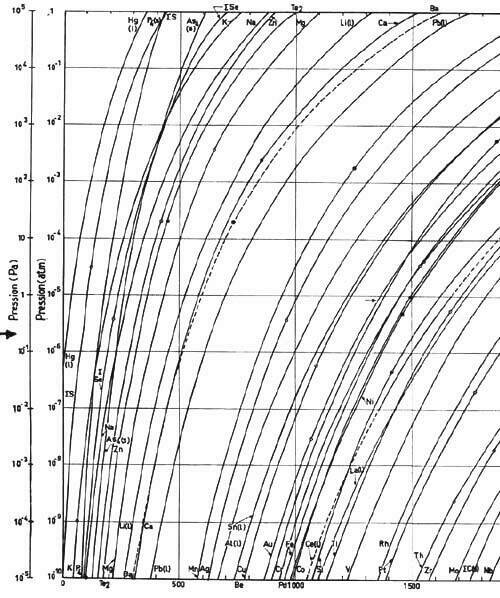
Figure 6 : Pression de vapeur saturante de certains éléments en fonction de la température d’après Les Techniques de l’Ingénieur (13).
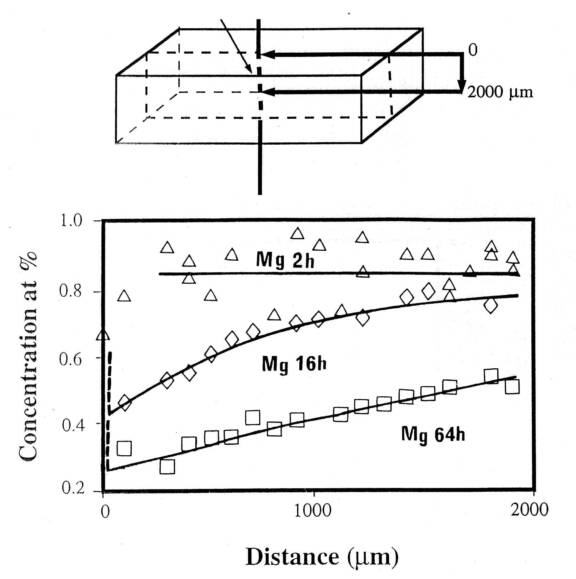
Figure 7 : Profil de la concentration en magnésium d’un composite 6061/alumine en fonction de la position dans une plaque homogénéisée en ampoule sous vide à 535 °C pendant différentes durées. Analyses à la microsonde de Castaing à l’école des mines de Paris.
Bibliographie
(1) G. Giauque, histoire des aciers au carbone, Le livre de l’acier, G. Béranger, G. Henry et G. Sanz, Technique et Documentation (1994), pp3-10.
(2) P.H. Galvin, la métallurgie du magnésium, Techniques de l’ingénieur, Fascicule M 2350, (1994).
(3) M. Olette, C. Gatellier et G. Lamarque, métallurgie secondaire, Techniques de l’Ingénieur, Fascicule M 7 750, (1998).
(4) M. Olette, C. Gatellier et G. Lamarque, métallurgie secondaire, outils et procédés, Techniques de l’Ingénieur, fascicule M 7 752 (2009).
(5) N.-J. Themelis, Transport and chemical rate phenomena, Gordon and Breach Publ. Basel, (1995).
(6) D. Balloy, J.C. Tissier, J. Dairon, S. Dorlencourt et J. Ninin, Fonderie et Fondeur d’Aujourd’hui, n° 7-8,(2005), pp 28-37.
(7) J. Dairon, S. Dorlencourt, D. Balloy, J.C. Tissier et J. Ninin, Fonderie et Fondeur d’Aujourd’hui, n° 9, (2005), pp 26-39.
(8) P.-V. Riboud et H. Gaye, fusion et affinage des aciers, Le livre de l’acier, G. Béranger, G. Henry et G. Sanz éditeurs, Technique et Documentation (1994), pp1159-1184.
(9) P. J Cunat, affinage des aciers inoxydables, Techniques de l’Ingénieur, Fascicule M 7 760, (2001).
(10) N.-A. Warner, JOM, 60, 10, (2008), pp14-22.
(11) Y. Combres, mtallurgie et recyclage du titane et de ses alliages, Techniques de l’Ingénieur, fascicule M 2355 (1997).
(12) Y. Bienvenu et K. Vieillevigne, Traitement thermique, n° 362, avril 2005 pp 29,33.
(13) C. Gatellier, A. Rist, P.-V. Riboud et M.-F. Ancey-Moret, equilibres thermodynamiques en sidérurgie, Techniques de l’Ingénieur, fascicule M 1730 (1974).
(14) W-L. Winterbottom et J.-P. Hirth, the vaporization kinetics of silver in condensation and evaporation of solids, Proceedings of an international conference, Dayton, Ohio, (1962), E. Ruthner, P. Goldfinger et J.-P. Hirth éditeurs, Gordon & Breach, New York, (1964).
(15) D.-E. Tyler, wrought copper and copper alloy products, in Metals Handbook 10th edition, vol. 2, ASM Intl, Metals park, Ohio, USA 1990.
(16) V. Massardier, P. Kerdelhue, P. Merle et J. Besson, experimental study of the interaction of magnesium with the reiforcement in AlSiMg alloy / alpha alumina platelet composites, materials science& Engineering, A 191 (1995), pp 267-276.
Pour en savoir plus : www.magnesium.com http://www.impeller.net/magazine/news_en/doc4032x.asp
Perspectives
Le vide peut déplacer les équilibres de réduction de composés de métaux volatils (Mg, Zn…) avec pour résultat une diminution de températures réaction de quelques centaines de degré et une diminution des équivalents carbone des procédés d’extraction ou des kWh. à ce jour, l’usage qui a été fait de cette possibilité est encore modeste avec au plus quelques centaines de milliers de tonnes de métal produites par an dans le monde.
Le traitement des métaux liquides sous vide avant coulée, essentiellement des aciers, mais aussi la quasi-totalité des alliages de titane intéresse plus de 200 Mt/an. Même si cette métallurgie secondaire est coûteuse en énergie (électrique), elle induit des gains en réduisant les taux de recirculation de coulées, en augmentant la productivité des ateliers en amont déchargés de l’affinage final et en créant un tampon entre l’amont et l’aval (coulée continue). Les gains les plus significatifs autorisés par le vide sont au niveau de l’utilisateur final par une amélioration des performances, un allongement des durées de vie (caisse en blanc automobile) et parfois un allègement.
Dans le recyclage des métaux les réactions d’évaporation condensation peuvent être mises en œuvre pour séparer les plus volatils (zinc des ferrailles). Les possibilités du vide comme ascenseur à métal liquide conviennent aux procédés continus complexes adaptés au recyclage et au traitement de minerais mixtes en permettant des boucles de recirculation dans une succession de réacteurs et décanteurs.
La couleur du vide serait-elle donc le vert ? Cet article ne permet pas de trancher mais il indique des gisements d’économie de carbone équivalent.