Un moyen de détection rapide de la rupture fragile
Un nouvel appareil de mesure de précision permet des essais C-body en moins de 180 secondes. Cela a été rendu possible grâce à un inhibiteur pour les processus de décapage développé avec l’aide d’un nouveau banc d’essai.
Le marché des pièces de fixation exige de plus en plus des matériaux à haute résistance, et une attention particulière doit être portée à la fragilisation par l’hydrogène possible lors de leur électrodéposition. En effet, avec l’augmentation de la résistance des matériaux, le risque de rupture fragile induite par l’hydrogène augmente également. Les méthodes d’essai utilisées jusqu’à présent nécessitent des cycles d’essai de plusieurs jours. C’est pourquoi la société familiale Max Schlötter, en collaboration avec iChemAnalytics, a développé un banc d’essai qui réduit le temps d’essai à quelques minutes seulement. Pour la première fois, jusqu’à 20 échantillons d’essai C peuvent être testés simultanément, en seulement 180 secondes. Ce test repose sur un essai de charge mécanique où les courbes de force-déplacement sont enregistrées. Les cellules de mesure individuelles sont dotées de programmes de mesure spécifiquement paramétrables qui peuvent être appelés en parallèle. Grâce aux capteurs de force haute résolution et aux courbes de mesure très précises, des valeurs caractéristiques de haute qualité peuvent être générées de manière reproductible et utilisées comme base pour le développement ultérieur des processus et des produits internes. Cela a permis à Schlötter de redévelopper le dégraissant de décapage SLOTOCLEAN BEF 1790.
Un test fiable en 3 minutes
Les propriétés des aciers à haute résistance sont de plus en plus optimisées pour devenir plus légers et plus résistants, par exemple. La protection contre la corrosion cathodique appliquée par électrodéposition est souvent utilisée pour offrir à ces aciers la meilleure protection contre la corrosion. « Une étape de décapage doit être réalisée lors du prétraitement de la pièce pour obtenir la meilleure adhérence possible du revêtement », explique Michael Zollinger, l’un des directeurs généraux de la société familiale Max Schlötter.
Les oxydes et les échelles sont éliminés dans le processus, ce qui donne une surface métalliquement sans défaut pour le processus de revêtement ultérieur. Si l’acide utilisé dans le décapage attaque le matériau de base, de l’hydrogène est également produit sous forme atomique. Des processus physiques peuvent provoquer la recomposition de certaines parties de cet hydrogène pour former de l’hydrogène moléculaire non diffusible à la surface, ou le faire diffuser dans le matériau.
Le stockage de l’hydrogène atomique affaiblit la structure métallique. Selon l’alliage, la pièce peut éventuellement devenir fragile et, dans le pire des cas, cet état sous contrainte peut conduire à ce qu’on appelle une rupture fragile.
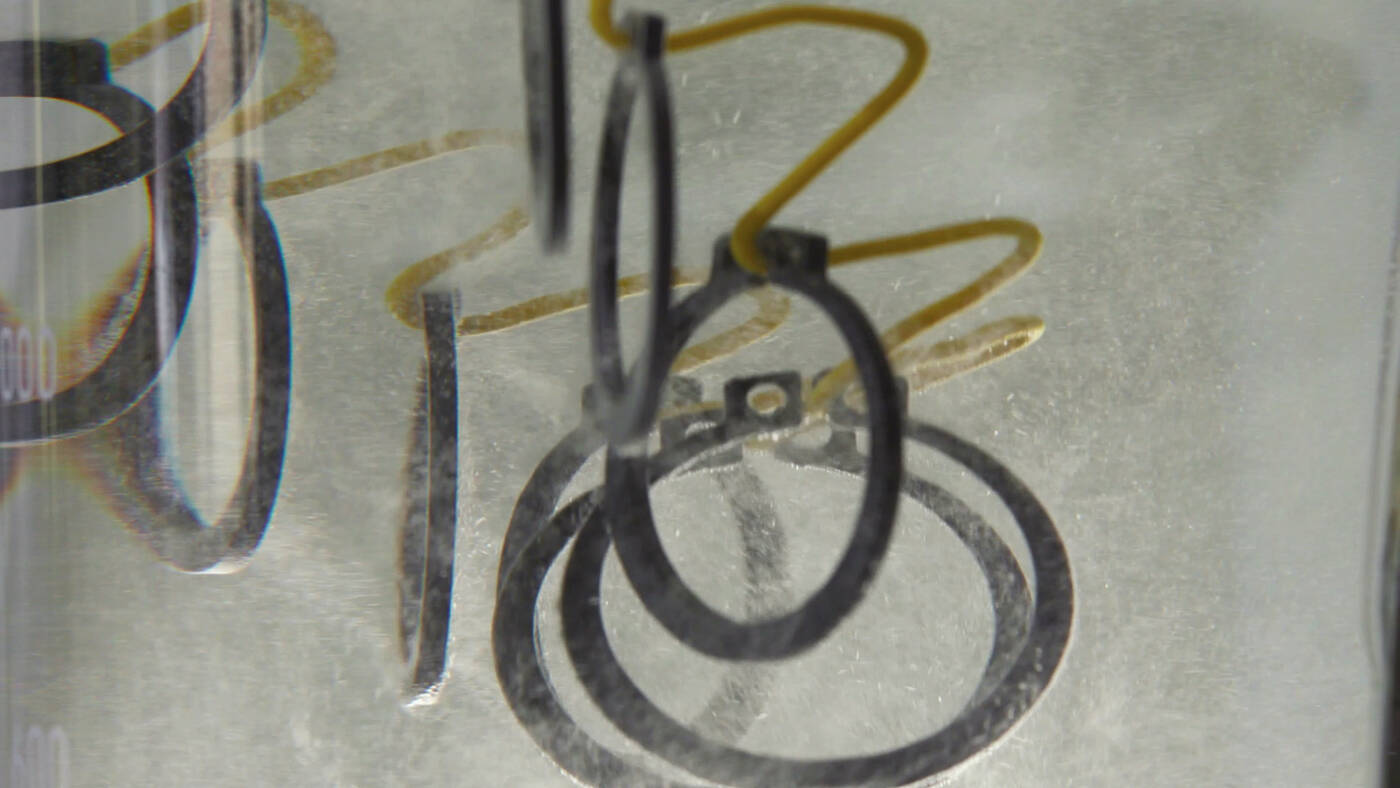
« Le prétraitement et le revêtement ultérieur de composants en acier à haute résistance avec une résistance à la traction supérieure à 800 MPa posent donc régulièrement la question, tant aux entreprises spécialisées qu’aux utilisateurs, de savoir quelle peut être la concentration maximale d’hydrogène dans le composant pour éviter les dommages matériels. À ce jour, malgré de nombreuses publications scientifiques, aucune méthode d’essai conviviale en cours de processus n’a été établie pour l’utilisateur en pratique ; de telles méthodes sont longues et compliquées », estime Michael Zöllinger.
Le dispositif de mesure de précision WSRME TWIN développé par la compagnie Max Schlötter, en collaboration avec iChemAnalytics, utilise des échantillons de forme en C pour détecter les modifications de l’état du matériau qui peuvent survenir, par exemple, en raison de la déformation par un métal liquide, de la dureté, de la trempe ou de la fragilisation par l’hydrogène.
Les tests comparables prenaient autrefois plusieurs jours. Mais grâce à la conception spéciale et au concept de test précis, cela ne prend maintenant que deux à trois minutes. Cela permet aux fabricants de processus et aux revêtisseurs contractuels d’intégrer de manière indépendante un travail conforme aux normes ainsi qu’un véritable suivi des processus et de l’assurance qualité dans leur propre production, sans avoir à dépendre de prestataires de services d’essai externes.
Jusqu’à 10 cellules de mesure
La structure discrète contient deux ouvertures de champ d’essai ainsi que plusieurs entraînements électriques avec une avance réglable pour mettre en œuvre de manière précise les niveaux de charge souhaités des procédures d’essai. Selon la variante, jusqu’à 10 cellules de mesure peuvent être équipées d’un maximum de 20 échantillons en forme de C, qui peuvent être mesurés en parallèle et indépendamment les uns des autres. Selon les besoins, des échantillons de test spécifiquement adaptés aux composants ou aux processus peuvent également être fabriqués et utilisés.
Plusieurs options de charge et de positionnement sont simultanément disponibles pour l’opérateur, allant de la charge par étapes contrôlée par la force ou la distance à des temps de maintien définis avec un taux d’étirement constant. Cela permet d’économiser beaucoup de temps qui serait autrement nécessaire pour les tests successifs. Au cours de ce processus, certaines valeurs caractéristiques sont automatiquement déterminées et surveillées, résultant des méthodes de mesure librement sélectionnables.
En même temps, des capteurs de force haute résolution et une mesure précise du déplacement garantissent une qualité optimale des données. « La sélection et le suivi des procédures d’essai sont très simples : tous les paramètres peuvent être réglés et appliqués via l’écran multi-touch intégré », affirme Zöllinger.
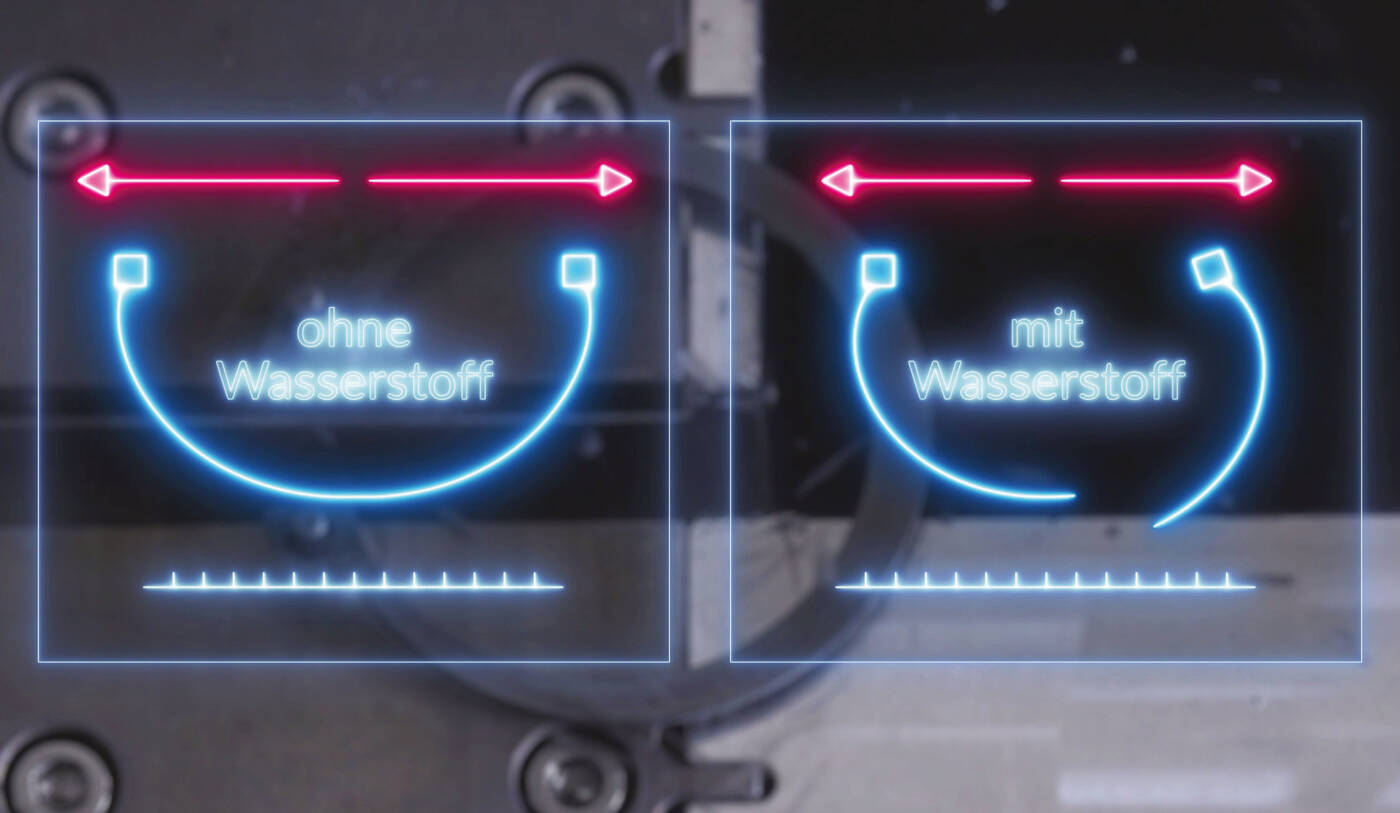
Grâce aux algorithmes d’évaluation intégrés, contrôlés par un microprocesseur, l’appareil de mesure est capable de mesurer ou de calculer de nombreuses valeurs caractéristiques spécifiques au matériau, telles que la transition du comportement élastique et plastique du matériau, la déconsolidation du matériau induite par l’hydrogène, ainsi qu’un indice de déformation spécifique au matériau (DI) pour le processus. Les valeurs de mesure et caractéristiques générées dans le processus sont automatiquement liées et stockées avec d’autres métadonnées telles que les prétraitements et les états du matériau. « Une grande signification statistique est obtenue grâce aux essais parallèles sur plusieurs stations de mesure en même temps. Cela permet de tirer des conclusions précieuses sur la manière dont la qualité des composants ou la composition de l’acier de départ peuvent être améliorées pour la seule usinabilité », explique Thomas Haberfellner, responsable de l’unité commerciale Chimie et développement de nouveaux marchés chez Max Schlötter.
Base de données pour le développement des processus
Toutes les valeurs mesurées sont stockées dans une base de données et peuvent être importées dans des programmes tels que Microsoft Excel. Ces résultats peuvent aider à développer des produits spécifiques aux clients ou à optimiser le portefeuille existant, tels que les ajouts aux bains de revêtement (par exemple, pour l’électrodéposition) ou de nouveaux additifs de bain (par exemple, des inhibiteurs de décapage).
Max Schlötter utilise déjà avec succès le banc d’essai, à cette fin, dans sa propre recherche et développement. Les résultats, accessibles rapidement avec la nouvelle technologie de mesure, ont permis de développer le dégraissant de décapage SLOTOCLEAN BEF 1790 en interne, avec une nouvelle génération d’inhibiteurs. Cela permet non seulement de maximiser la valeur d’inhibition, mais aussi de minimiser la tendance liée au processus à la fragilisation par l’hydrogène, tout en triplant plus que la durée de vie du décapage par rapport aux systèmes de première génération. Cela contribue activement à la préservation des ressources et réduit l’empreinte carbone dans le domaine de l’électrodéposition contractuelle.
« Le dispositif de mesure de précision WSRME TWIN rend non seulement les essais en cours de processus pour la fragilisation par l’hydrogène facilement accessibles à tous les fabricants et revêtisseurs contractuels. L’enregistrement de paramètres polyvalents et l’évaluation automatisée aident également à réduire les coûts de processus à long terme grâce à la sélection ciblée des matériaux, à l’optimisation des paramètres de traitement thermique et à l’utilisation de produits chimiques conformes aux exigences », résume Michael Zöllinger.