Traitements thermiques localisés (2e partie)
Par Guy Murry, ingénieur-conseil
Conférer aux aciers des propriétés particulières au voisinage de leur surface, tel est l’objet des traitements thermiques localisés. Dans la première partie de cet article parue dans le numéro 387 du mois de mai, le durcissement par trempe après chauffage superficiel a été décrypté. Reste à présenter ici les traitements thermiques qui modifient la composition du métal au voisinage de sa surface.
Parmi les traitements thermiques ayant pour objet d’améliorer les performances mécaniques des pièces sollicitées principalement au voisinage de leur surface et d’accroître ainsi, par exemple leurs performances mécaniques en flexion et/ou torsion, leur endurance en flexion et/ou torsion, leur résistance à l’usure, leur tenue à la fatigue-roulement sous fortes charges, tout en conservant à cœur une ductilité qui assure la sécurité du fonctionnement, nous nous intéressons ici aux traitements thermochimiques qui font intervenir des modifications de la composition du métal au voisinage de sa surface.
Les traitements thermochimiques
Dans son acceptation générale, cette locution signifie « traitements thermiques effectués dans un milieu convenablement choisi pour obtenir une modification de la composition chimique de la surface du métal de base par échange avec ce milieu ». Il faut noter que cette définition sous entend que les modifications de composition chimique intéressent une profondeur plus ou moins grande sous la surface et qu’elles sont réalisées au cours du traitement thermique qui va donner à la pièce ses propriétés d’emploi. Les plus utilisés de ces traitements ont pour objet principal de modifier dans une couche superficielle la capacité de durcissement de l’acier de telle sorte qu’après traitement ce dernier présente une plus grande dureté superficielle. Ce sont ces traitements qui feront l’objet de cet article qui n’évoquera pas les traitements (plus superficiels) destinés à améliorer les qualités de frottement pour augmenter la résistance à l’usure ou ceux réalisés pour accroître la résistance à la corrosion.
D’une manière générale, pour augmenter la capacité de durcissement de l’acier, on l’enrichit en carbone qui est l’élément de base pour durcir le fer, en élément(s) capable(s) de former des carbures, mais aussi en azote, autre élément susceptible de former des précipités très durcissant et en élément(s) capable(s) de former des nitrures.
L’enrichissement de la couche superficielle se fait ici par diffusion à l’état solide et met donc essentiellement en jeu les éléments susceptibles de diffuser dans le fer dans des conditions industrielles c’est-à-dire à des températures pas trop élevées (pour ne pas altérer le métal de base) et en des temps pas trop longs (pour rester économiquement faisable). Ces exigences imposent le choix d’éléments qui diffusent « facilement » dans le fer à savoir ceux qui passent en solution solide d’insertion soit le carbone et l’azote. Les éléments « carburigènes » ou « nitrurigènes » qui passent en solution solide de substitution seront introduits dans l’acier au moment de son élaboration car leur diffusion (lacunaire) imposerait des conditions industrielles exorbitantes.
Nous allons donc nous intéresser, dans ce qui suit, aux traitements thermochimiques suivants :
La cémentation, traitement thermochimique avec enrichissement superficiel en carbone.
La nitruration, traitement thermochimique avec enrichissement superficiel en azote.
La carbonitruration et la nitrocarburation, traitements thermochimiques avec enrichissement superficiel en carbone et en azote.
étant entendu que les traitements ainsi définis comportent trois aspects :
L’apport de l’élément (carbone ou azote) à la surface extérieure de ce qui sera la couche que l’on veut créer. Pour que cet élément puisse participer à l’enrichissement, il est nécessaire qu’il soit apporté en surface à l’état atomique ce qui exige que ses atomes soient “libérés” par une réaction à laquelle sera soumis un composé qui les inclus.
L’enrichissement de la couche superficielle qui doit être durcie. Cet enrichissement fait intervenir la diffusion de l’élément (carbone ou azote) dans l’épaisseur à partir de la surface ce qui demande que celui-ci soit soluble dans le fer pendant la création de la couche enrichie.
Le conditionnement de la couche enrichie pour provoquer son durcissement. Ce peut être le fait d’un traitement thermique ou celui d’une opération conjuguée avec l’enrichissement.
La cémentation
Pour que la couche enrichie puisse se former, on vient de préciser que les conditions opératoires doivent être telles que le carbone soit soluble dans l’acier pendant la création de celle-ci. En se référant au diagramme
d’équilibre Fe-C (figure 1), on constate que cette exigence ne peut être satisfaite que si le fer est à l’état austénitique (à l’état α la solubilité du carbone est au mieux de 0,022 % ce qui est largement insuffisant). L’acier devra donc être échauffé à des températures supérieures à Ac3 et maintenu à celles-ci pendant toute la diffusion.
• L’apport de carbone
Les réactions chimiques susceptibles de libérer du carbone à la surface d’un acier peuvent être mises en jeu à partir de composés gazeux ou liquides. On utilise ainsi, comme “ porteur de carbone ” :
• Le monoxyde de carbone à l’état gazeux qui va libérer du carbone en se décomposant selon la réaction : 2 CO <-> C + CO2
Le monoxyde de carbone pouvant provenir :
* d’une réaction, à la température de cémentation, entre du charbon de bois et du carbonate de baryum (cémentation en caisse fermée).
* d’un générateur endothermique brûlant un hydrocarbure saturé (méthane, butane, propane) avec un apport insuffisant d’oxygène, la réaction de libération du carbone étant alors complétée par l’intervention de l’hydrogène (avec du méthane par exemple) :
2CO + CH4 <-> 3C + 2 H2O
* du craquage d’un mélange d’azote et de méthanol injecté dans le moufle du four de cémentation :
CH3OH <-> CO + 2H2
* du craquage de méthane injecté, avec une certaine proportion d’air, dans le moufle du four de cémentation :
2CH4 + O2 <-> 4H2 + 2CO
• Un hydrocarbure injecté dans un four à vide (cémentation basse pression) et qui se dissocie : CH4 € 2H2 + C
* du carbure de silicium dissous dans un mélange fondu de chaux et de carbonate de sodium :
3Na2CO3 + SiC <-> Na2SiO3 + 2Na2O + 2CO2 + 2C
* du carbure de calcium dissous dans un mélange fondu de chaux et de chlorure de calcium.
• L’enrichissement en carbone
Les différents procédés de cémentation sont pilotés de telle sorte que la quantité de carbone présente dans les premières couches atomiques superficielles du métal soit constante. C’est ainsi qu’avec les procédés de cémentation en phase gazeuse on parle de “ potentiel carbone ” exprimé à l’aide de la teneur en carbone d’un feuillard de fer pur cémenté jusqu’à l’équilibre dans les conditions choisies. C’est à partir de cette situation que l’enrichissement en profondeur va se faire par diffusion du carbone. Celle-ci va donc engendrer un gradient de teneur en cet élément dans le sens perpendiculaire à la surface, gradient souvent décrit à l’aide de la formule suivante tirée des lois de la diffusion :
Cp = Co + (Cs – Co) x {1 – erf [p / (2x√Dx√t)]}
avec
Cp = concentration (%) en carbone à la distance p de la surface
Co = concentration (%) en carbone dans le métal de base
Cs = concentration (%) en carbone à la surface
p = distance (cm) à la surface
t = durée du maintien en température (s)
D = coefficient de diffusion du carbone
(cm² / s) = Do x Exp(-Q/RT)
Do = facteur de fréquence (cm²/s) on peut retenir 0,162 (cm²/s)
Q = énergie d’activation (J/mole) on peut retenir 137 800 J/mole
R = 8,314 (J/K.mole)
T = température (K)
erf (x) = fonction erreur dont le tableau 1 donne quelques valeurs
Ces formulations permettent, comme il vient d’être dit, de décrire les gradients de teneur en carbone dans la profondeur. La figure 2 en donne des exemples relatifs à la cémentation d’un acier à 0,18 % de carbone dans des conditions de température et de durée du traitement diverses mais toujours avec un potentiel carbone de 0,8 %. Ces formulations permettent aussi d’écrire :
1 – [(Cp – Co) / (Cs – Co)] = erf [p / (2x√Dx√t)]
Cela peut conduire à la détermination du terme W = p / (2x√Dx√t) dont la valeur sera estimée à partir du paramètre Z caractérisant le résultat visé :
Z = 1 – [(Cp – Co) / (Cs – Co)]
Et cela par utilisation inversée des tables donnant les valeurs de la fonction erf. Cette détermination conduira alors à une relation entre les trois paramètres p, D et t :
p = W x 2 x √D x √t
Cela montre qu’à résultat visé constant
(Z = Cte), la profondeur (p) caractéristique de la zone enrichie est, toutes choses égales par ailleurs, proportionnelle à √t, et que l’on peut comparer en termes de température et de durée les conditions d’obtention d’un certain enrichissement en carbone (p = cte, Z = cte et donc W = cte) à l’aide de la relation :
D x t = (p / 2 x W)2 = cte
La figure 3 en donne un exemple.
Pratiquement, il est généralement conseillé de réaliser cette opération d’enrichissement à des températures comprises entre 880°C et 980°C (aux plus hautes températures de cet intervalle pour les aciers non ou faiblement alliés et aux plus basses pour les aciers alliés).
• Le durcissement de la couche
L’apport de carbone dans la couche superficielle ayant pour objectif de permettre un durcissement important, il est donc logique de transformer cette dernière en martensite. Ce résultat sera obtenu à l’aide d’une opération de trempe qui est réalisée :
Soit directement à la fin de l’enrichissement en carbone (trempe directe) en profitant du fait que l’acier est alors à l’état austénitique. Si la température de cémentation est très supérieure à la température limite de stabilité de l’austénite la trempe directe peut être précédée d’un refroidissement lent jusqu’à cette dernière température (souvent comprise entre 770°C et 840°C).
Soit après refroidissement du métal et ré-austénitisation ultérieure (double trempe). le premier refroidissement est alors assez lent et confère à l’acier une structure peu durcie qui permet notamment des reprises d’usinage.
Lors de la trempe, la transformation martensitique se développe dans l’intervalle de température compris entre la température Ms (début de la transformation) et la température Mf (fin de la transformation), toutes deux très dépendantes de la composition chimique de l’acier et surtout de sa teneur en carbone. On écrit :
Ms (°C) = 539 – 423(C%) – 30,4(Mn%)
– 17,7(Ni%) – 12,1(Cr%) –7,5(Mo%)
et Mf (°C)= 650 – 2Ms(°C)
La figure 4 décrit ces variations en fonction du principal facteur, la teneur en carbone (l’effet mineur des éléments d’alliage, pas pris en compte ici, est à l’origine de la dispersion des résultats). On constate que, si la teneur en carbone est supérieure à 0,35 %, la transformation martensitique est inachevée après un arrêt de la trempe à la température ambiante (un traitement par le froid à – 100 °C / - 150 °C ne laisse subsister de l’austénite résiduelle que si C% > 0,55 environ).
Or, ici, la cémentation à créé un gradient de teneur en carbone qui induit donc un gradient de température Ms et un gradient de température Mf. La figure 5 donne un exemple de ces évolutions dans le cas d’un acier non allié à 0,18 %C cémenté à 900 °C pendant 5 heures avec un potentiel carbone maintenu à 0,8 %. Dans ces conditions
on constate que les niveaux de la température Mf conduisent à distinguer une première zone O qui plonge jusqu’au cœur et, dans laquelle, la teneur en carbone est restée celle du métal de base. Là où les conditions de refroidissement et la trempabilité le permettent la transformation martensitique se développera à relativement haute température (avec un risque d’auto-revenu pendant la fin du refroidissement).
La couche enrichie peut, elle, être fractionnée en trois zones :
Une première sous-couche (zone A) dans laquelle la transformation martensitique se développe dans des domaines de température dont la limite basse reste supérieure à la température ambiante. A la fin de la trempe (arrêtée à 20 °C) la transformation est donc achevée.
Un ensemble de deux couches (zone B + zone C) dans lesquelles la transformation martensitique se développe dans des domaines de température dont la limite basse est inférieure à la température ambiante. A la fin de la trempe (arrêtée à 20 °C) la transformation n’est donc pas terminée et il subsiste de l’austénite non transformée. Dans la zone B la transformation martensitique peut être achevée au cours d’un traitement par le froid effectué immédiatement après la trempe. Ce traitement permettra aussi de poursuivre la transformation dans la zone C (sans l’achever toutefois).
En chaque point de la couche cémentée la transformation martensitique débute, si la trempabilité le permet, lorsque la température locale est égale à Ms(très dépendante de la teneur en carbone) au point considéré. La figure 6 donne un exemple des évolutions couplées de ces paramètres (cas d’un acier allié au CrNiMo à 0,23 %C cémenté à 900 °C et trempé à l’huile). On constate que la transformation martensitique ne débute pas à l’extrême surface mais à la limite to entre la couche cémentée et le métal de base.
Dans la couche cémentée la température Ms est plus basse que celle du métal de base. Elle ne sera atteinte qu’après un refroidissement plus long et d’autant plus long que la zone considérée sera proche de la surface plus riche en carbone.
Dans le métal de base de la sous-couche, la température Ms est celle de ce dernier. Elle reste donc invariable en profondeur. Elle sera atteinte après des refroidissements d’autant plus longs que la profondeur sera plus grande.
Ainsi donc la transformation martensitique débute à la profondeur limite de la couche cémentée et progresse dans deux directions : sûrement vers la surface de la pièce et éventuellement, vers le cœur de la pièce si la trempabilité le permet.
Mais pour que la transformation martensitique donne le durcissement maximum, il est nécessaire aussi qu’elle ne soit pas précédée d’une formation de bainite et/ou de ferrite et perlite. Le refroidissement lors de la trempe doit donc être suffisamment rapide pour faire en sorte que la loi de refroidissement ne traverse que le domaine martensitique du diagramme TRC et évite les domaines où se forment la bainite, la perlite et/ou la ferrite. Autrement dit la loi de refroidissement en un point où doit se former la martensite doit être plus rapide que la loi critique de transformation martensitique LM et donc le critère ∆t700/300 de la loi de refroidissement doit avoir une valeur inférieure à celle du paramètre DtM de la loi critique de transformation martensitique. à titre d’exemples le tableau 2 donne des valeurs de ce dernier paramètre pour quelques aciers de cémentation ainsi que pour ces mêmes aciers enrichis en carbone car l’augmentation de la teneur en carbone accroît beaucoup la valeur du paramètre ∆tM. Confrontées, à titre d’exemples, aux niveaux des paramètres ∆t700/300 des lois de refroidissement de cylindres lors d’une trempe à 900°C dans une huile très agitée (voir tableau 3), ces données montrent que les conditions d’obtention d’une structure martensitique dans la couche cémentée sont assez facilement satisfaites dès lors que l’acier est légèrement allié (pour de petites pièces les aciers non alliés peuvent souvent être utilisés).
Il ne faut pas oublier ici que l’enrichissement en carbone a provoqué un abaissement de l’intervalle de température (Ms à Mf) dans lequel se déroule la transformation martensitique de telle sorte que cette dernière n’est pas achevée lors de l’arrêt de la trempe à la température ambiante (figure 4) et qu’il peut être utile de réaliser un traitement par le froid (lequel ne permettra pas toujours de transformer toute l’austénite résiduelle). Ce traitement par le froid doit satisfaire à certaines conditions : être effectué au plus tôt après la trempe et avant tout revenu, ne pas être brutal (le refroidissement ne doit pas être trop rapide pour limiter le risque de tapure) et viser une température limite basse de – 150 °C avec un maintien de l’ordre de 1 heure environ.
Le durcissement par trempe après cémentation peut être suivi in fine d’un revenu généralement réalisé entre 150 °C et 200 °C. On admet que cette opération, qui abaisse sensiblement la dureté superficielle (voir plus avant) diminue la fragilité de la couche durcie et abaisse ainsi les risques de fissuration lors d’une rectification ultérieure.
• Les transformations du métal de base
Pendant toute la durée de l’enrichissement en carbone le métal de base est maintenu à la température choisie pour réaliser l’apport de carbone, il est donc à l’état austénitique et selon le niveau de cette température (si elle est élevée) il peut être le siège d’un grossissement des grains d’austénite. Ce processus est susceptible d’affecter ses propriétés mécaniques. Pour le combattre on dispose des moyens suivants :
Abaisser le plus possible la température de cémentation.
Mettre en œuvre des aciers dits “calmés à l’aluminium” c’est-à-dire des aciers ayant reçu une addition d’aluminium lors de leur élaboration. Cette addition provoque la précipitation de fines particules intergranulaires de nitrure d’aluminium qui gênent le grossissement des grains d’austénite dans la mesure où la température reste inférieure à 1 000 - 1 050 °C (température de début de dissolution des nitrures d’aluminium).
Effectuer une double trempe, la première constituant un traitement d’affinage structural.
Lors de la trempe, l’acier de base se transforme aussi dans les conditions de refroidissement imposées par le processus opératoire qui, cela a déjà été mentionné, comporte le plus souvent une trempe à l’huile agitée. Pour assurer un bon soutien de la couche durcie il peut être intéressant de faire en sorte que la transformation provoque alors la formation d’une structure bainitique (ou éventuellement bainito-martensitique). Cette évolution dépendra essentiellement de la trempabilité du métal de base que l’on peut prendre en compte ici en s’intéressant aux deux paramètres :
• ∆tM, paramètre caractérisant la loi LM loi critique de transformation martensitique (loi la plus lente qui ne provoque que la transformation martensitique).
• ∆tB, paramètre caractérisant la loi LB loi critique de transformation bainitique (loi la plus lente qui provoque encore la transformation bainitique en évitant toute formation de ferrite et perlite).
Pour parvenir à une structure bainitique il faut donc que, l’acier de base soit tel que, dans la masse de la pièce, le ∆t700/300 correspondant aux conditions de trempe retenues soit compris entre ∆tM et ∆tB. Pour illustrer ce propos le tableau 4 donne des ordres de grandeur de ces deux derniers paramètres pour différents aciers de cémentation tandis que le tableau 5 donne, lui des ordres de grandeur des paramètres ∆t700/300 correspondant à des cylindres de divers diamètres trempés à l’huile très agitée.
On voit qu’il est possible de trouver des aciers de cémentation alliés (et même peu alliés) aptes à se transformer en bainite (ou en un mélange de bainite et de martensite) lors de la trempe qui achève la cémentation. Le critère de choix étant ∆tB qui doit être plus grand que le paramètre ∆t700/300 caractéristique du refroidissement dans la zone considérée.
• Les conditions opératoires habituelles
Le plus souvent, la cémentation se fait entre 880 et 950 °C. Pour accélérer les réactions d’apport et de diffusion du carbone dans l’acier, on opère parfois entre 950 et 1 050°C sur des aciers qui conservent un grain fin à ces températures (aciers “ calmés ” à l’aluminium notamment). L’épaisseur de la couche cémentée varie avec la destination et le volume de la pièce. Les épaisseurs importantes, de 0,8 à 1,8 mm ou plus, sont réservées à des pièces devant résister à l’usure et à des pièces de forte section. Pour les pièces de moyenne et faible sections, tels les engrenages d’automobiles, des épaisseurs de 0,2 à 0,8 mm sont généralement suffisantes.
• Les résultats obtenus
Les résultats d’une cémentation s’apprécient le plus souvent à l’aide de mesures de dureté permettant de tracer la courbe :
dureté = f (profondeur à partir de la surface)
La figure 7 en donne un schéma de principe qui montre que cette courbe peut être considérée comme divisible en trois parties :
La première qui se place dans la zone AA’B et décrit les évolutions de la dureté depuis la surface jusqu’à une profondeur généralement faible. Elle correspond au domaine le plus enrichi en carbone et de ce fait la structure y est généralement austéno-martensitique, la teneur maximale en austénite résiduelle étant localisée à l’extrême peau. Les niveaux de dureté résultent de la compétition entre le durcissement dû au carbone présent dans la martensite et l’adoucissement provoqué par l’austénite résiduelle. Si la teneur en carbone est élevée en surface (Mf est alors très basse) la courbe A’B est montante, traduisant l’effet prépondérant de l’austénite résiduelle (qui est alors abondante) et dont la proportion diminue depuis A’ jusqu’à B (la teneur locale en carbone diminue dans la profondeur). Si, au contraire, la teneur en carbone est moins élevée (Mf est plus haute) la courbe A’B est descendante, traduisant alors l’évolution du durcissement de la martensite qui décroît depuis A jusqu’à B selon la diminution de la teneur locale en carbone. La figure 8 décrit un aspect particulier des effets dûs à l’austénite résiduelle en comparant la courbe A’1B tracée après trempe directe d’un axe en acier C16 cémenté et la courbe A’2B tracée après trempe directe et traitement par le froid. On voit que la transformation de l’austénite résiduelle apporte un complément important de durcissement mais qu’elle n’est pas complète puisque la courbe A’2B est encore montante. On constate aussi qu’après trempe, il subsistait de l’austénite résiduelle jusqu à une profondeur de l’ordre, dans le cas présent, de 0,8 mm. L’influence de l’austénite résiduelle peut encore être illustrée en confrontant les courbes AB et A’B tracées (figure 9) soit après trempe directe d’un axe cémenté en acier C16 soit après double trempe (à 830 °C ou à 770 °C). Les deux doubles trempes conduisent à des niveaux de dureté plus élevés car les austénitisations à 825 °C et 775 °C ne permettent pas de mettre tout le carbone en solution et, de ce fait, il subsiste moins d’austénite résiduelle (Mf est moins basse). Il est intéressant de remarquer ici que la double trempe avec ré-austénitisation à 775 °C donne une dureté en peau de 900HV insensible à un traitement par le froid ce qui permet de considéré que la teneur superficielle en carbone est bien ajustée pour donner le durcissement maximal en absence d’austénite résiduelle.
La deuxième partie BC (figure 7) de la courbe HV=f(profondeur) décrit les évolutions de la dureté locale telle qu’elle résulte de la teneur locale en carbone et des conditions de refroidissement lors de la trempe qui, selon la trempabilité locale de l’acier, lui conféreront une structure martensitique ou bainito-martensitique. Les conditions de refroidissement de la couche cémentée varient peu entre sa surface et sa base (la profondeur de la couche est relativement petite) comme cela a déjà été indiqué (voir tableau 3) ce qui rend la courbe BC très dépendante de la teneur locale en carbone.
La troisième partie CD (figure 7) de la courbe HV=f(profondeur) concerne le métal de base non enrichi en carbone qui a été austénitisé et qui a subit le refroidissement imposé par la trempe finale, Selon ce dernier et selon la trempabilité de l’acier, sa structure pourra être ferrito-perlitique, ferrito-bainitique voire bainito-martensitique.
En pratique, on admet le plus souvent que la couche cémentée atteint le maximum de dureté après trempe lorsque la teneur en carbone en surface est voisine de l’eutectoïde, c’est-à-dire de l’ordre de 0,7 à 0,9 %. Elle contient systématiquement de l’austénite résiduelle ce qui peut justifier un traitement par le froid. La dureté après trempe se situe alors aux environs de 800 à 900 HV. Un revenu de “détente” (150/200 °C) après trempe est parfois effectué pour améliorer la ténacité de la couche durcie. La figure 10 montre qu’un tel réchauffage abaisse sensiblement la dureté de cette dernière d’environ 10 %.
La masse de la pièce, pauvre en carbone, conserve après trempe (et selon sa trempabilité) une structure bainitique ou perlito-bainitique, douce et tenace qui soutient la couche durcie et assure la sécurité de fonctionnement. L’interaction des propriétés complémentaires entre surface et sous-couche permet donc de réaliser des pièces à la fois dures en surface, tenaces à cœur et peu fragiles. Leur endurance est accrue par l’existence en surface de contraintes de compression.
• Points particuliers
– L’oxydation interne
Lorsque la cémentation implique du monoxyde et du dioxyde de carbone, des oxydes de certains éléments d’alliage peuvent se former en surface des pièces traitées et, éventuellement, précipiter dans les joints des grains de l’austénite après diffusion intergranulaire de l’oxygène. Les éléments d’alliage qui participent le plus à ces formations sont le manganèse, le titane et le chrome.
Cette oxydation interne n’intéresse qu’une faible profondeur (15 mm au maximum) mais suffit à diminuer très sensiblement la résistance à la fatigue.
Pour maîtriser ce phénomène on peut mettre en œuvre un procédé de cémentation à très bas oxygène, choisir des aciers contenant peu de Cr, de Mn et de Ti (aciers au Ni, Mo), procéder à une double trempe avec surépaisseur au départ et reprise d’usinage avant la deuxième austénitisation.
– Les déformations et les contraintes résiduelles
La trempe qui intervient après l’enrichissement en carbone engendre des déformations qui, comme cela a déjà été indiqué dépendent des gradients de température et des décalages chronologiques des transformations. Mais ici le gradient de teneur en carbone ajoute encore aux décalages chronologiques. De ce fait et compte tenu de la variété des pièces traitées, chaque traitement devient un cas particulier. Pour limiter l’ampleur des déformations générées par la trempe on peut recourir (en sus des précautions habituelles) aux moyens suivants :
– Abaisser la température du métal avant la trempe en limitant, dans la mesure du possible, la température de cémentation et, s’il reste une marge, en refroidissant l’acier tout en le conservant à l’état austénitique. Cette dernière procédure peut provoquer une précipitation de carbures des éléments carburigènes éventuellement présents dans l’acier et, par voie de conséquence, affaiblir son pouvoir durcissant.
– Brider les pièces pendant le refroidissement et, notamment, les placer dans une presse à tremper.
– Tremper les pièces dans un huile chaude afin de provoquer une diminution des gradients de température avant ou pendant la transformation martensitique. La température de l’huile doit être ajustée ; en général elle est comprise entre 150 °C et 200 °C.
Par ailleurs, dans la plus part des cas, on constate après traitement qu’au voisinage de la surface l’acier est soumis à des contraintes résiduelles de compression (la figure 11 en donne un exemple) qui améliorent sa résistance à la fatigue. La présence d’une petite proportion d’austénite résiduelle participe aussi parfois à cette amélioration. Mais, par contre, un revenu, en provoquant une contraction volumique irréversible, peut avoir un effet contraire en diminuant les contraintes résiduelles de compression. n
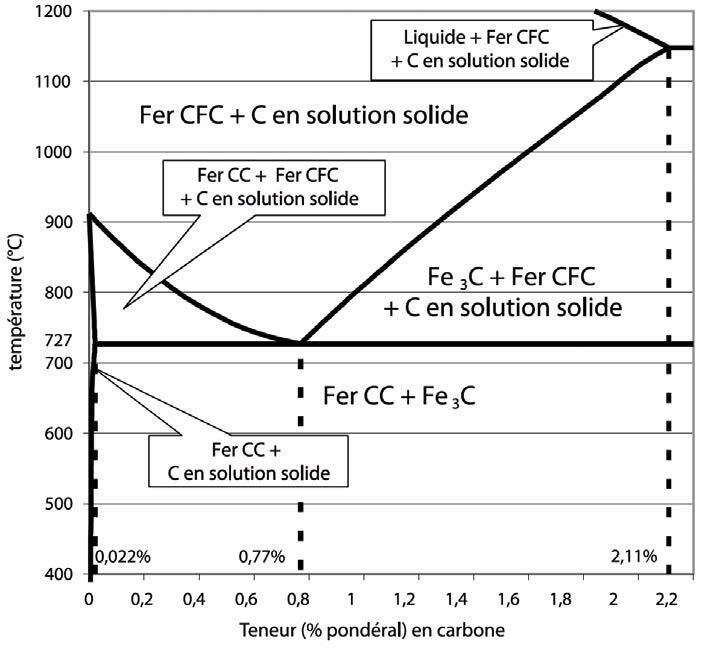
Figure 1. : Partie du diagramme d’équilibre Fe-Fe3C relative aux aciers.
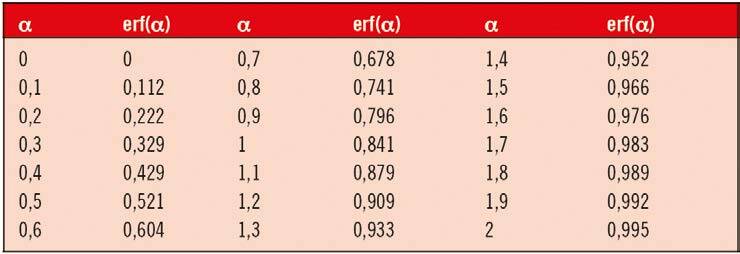
Tableau 1. : Valeurs de la fonction erf(α).
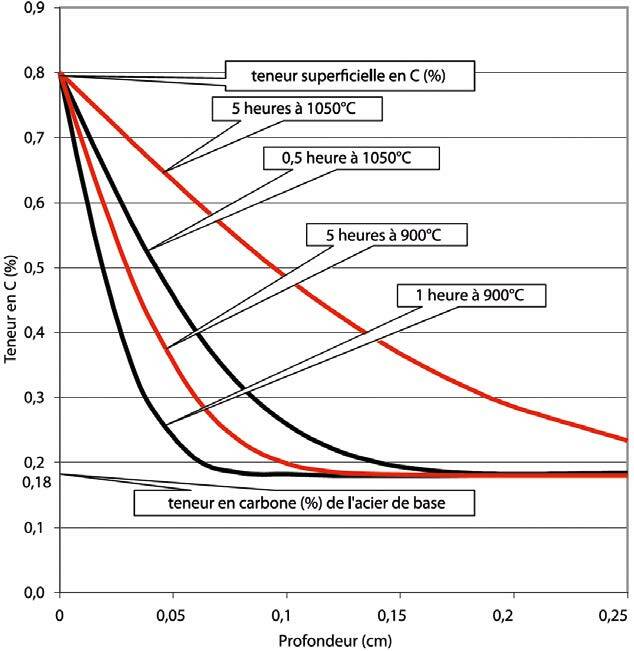
Figure 2. : Exemples de descriptions du gradient en carbone crée dans différentes conditions de cémentation d’un acier non allié à 0,18%C avec un potentiel carbone de 0,8 %/.
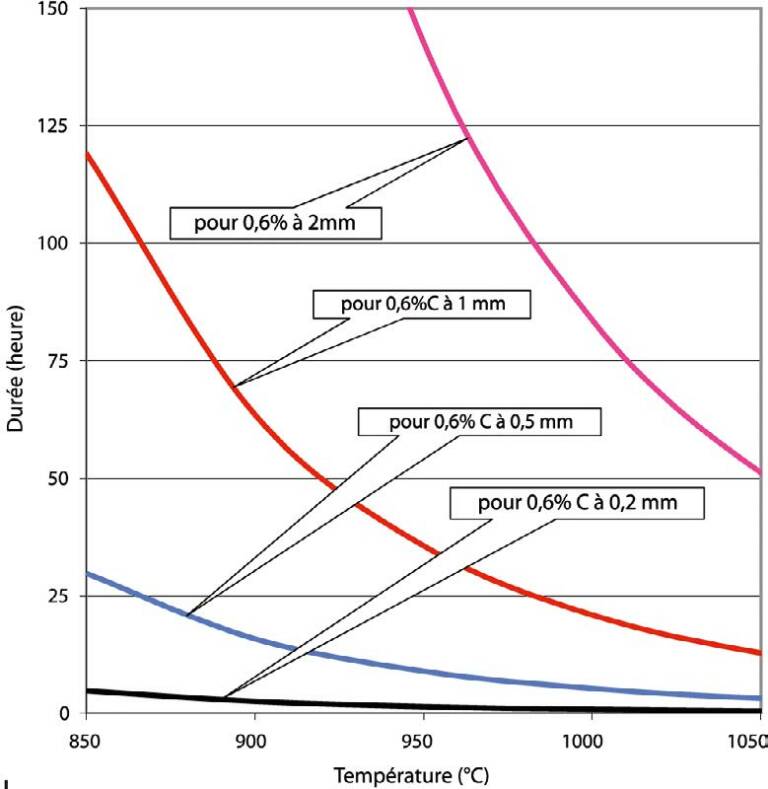
Figure 3. : Exemple de graphique illustrant la relation entre température et durée de cémentation (cas d’un acier non allié à 0,2 % C et potentiel carbone maintenu à 0,8 %).
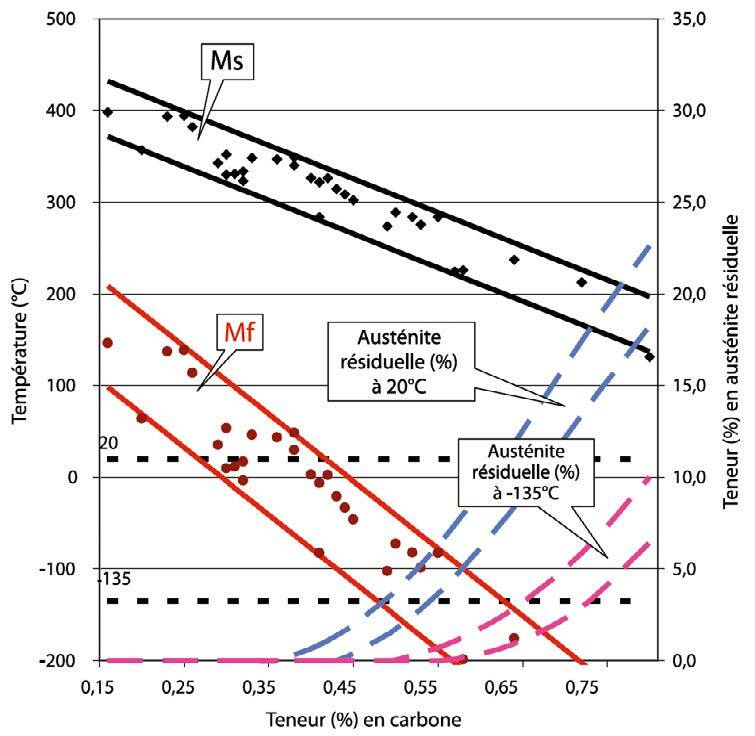
Figure 4. : Domaine de développement de la transformation martensitique et proportions d’austénite résiduelle subsistant à 20°C et à -135°C en fonction de la teneur en carbone.
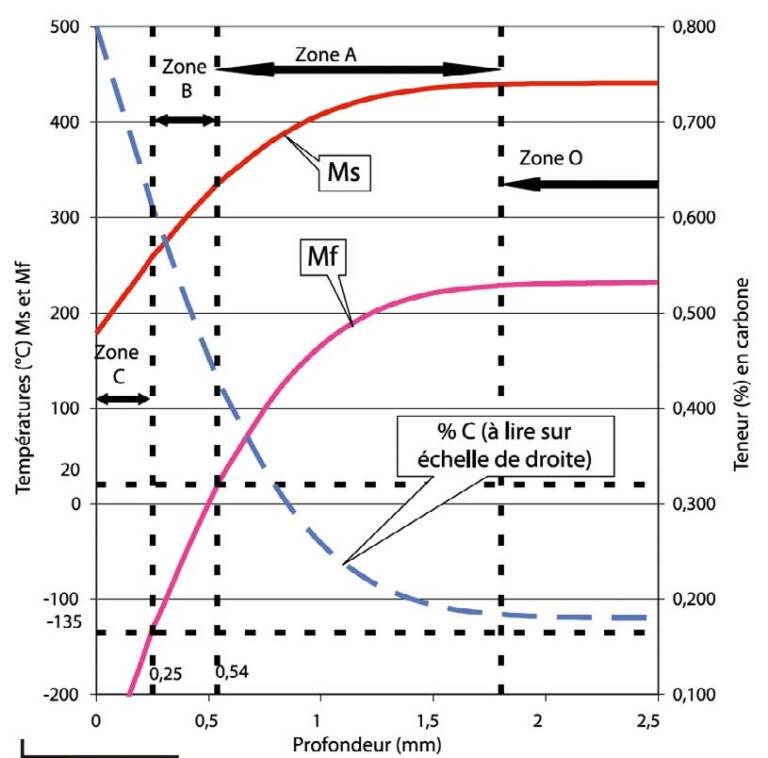
Figure 5. : Exemple d’évolutions du domaine de la transformation martensitique en fonction de la profondeur dans la couche cémentée (acier non allié à 0,18 %C, cémentation avec potentiel carbone de 0,8 %).
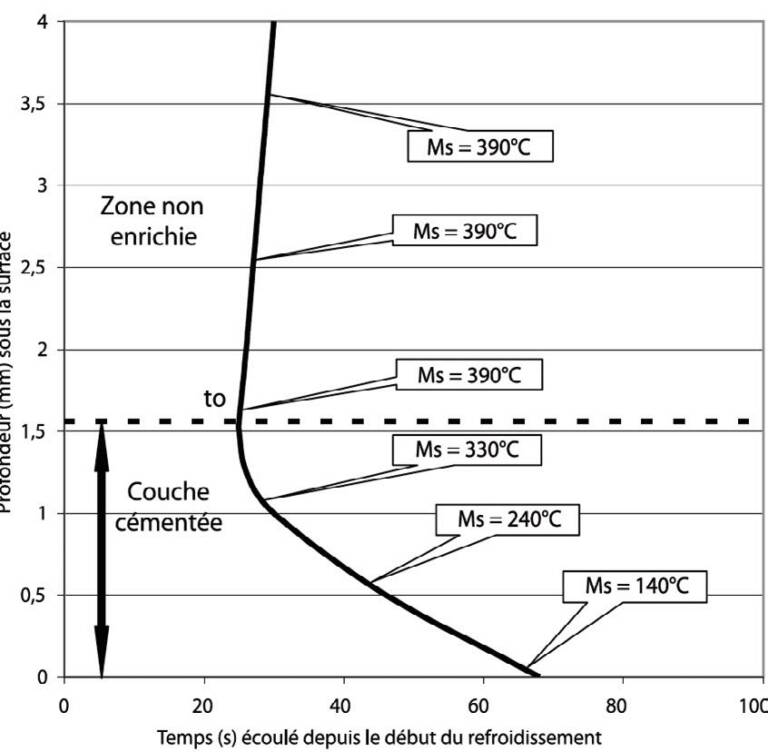
Figure 6. : Exemple de description de la chronologie des débuts de la transformation martensitique.
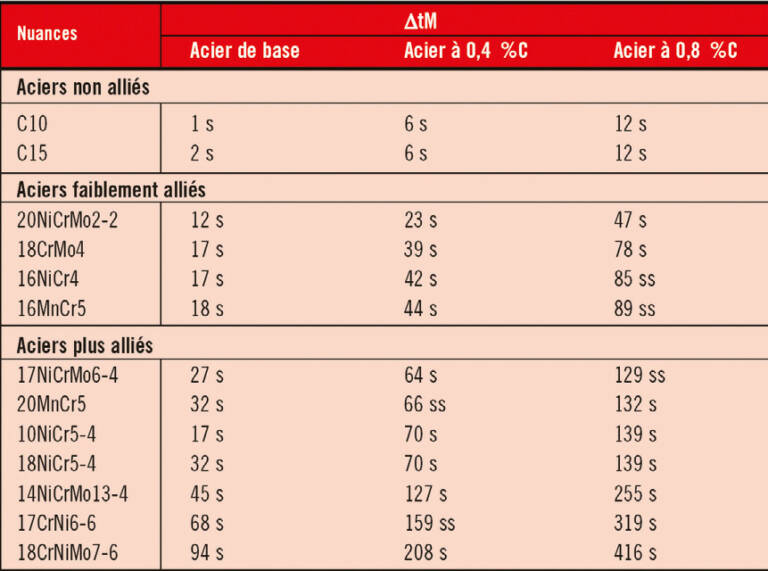
Tableau 2. : Ordres de grandeur de la valeur du paramètre ΔtM pour des aciers de cémentation.
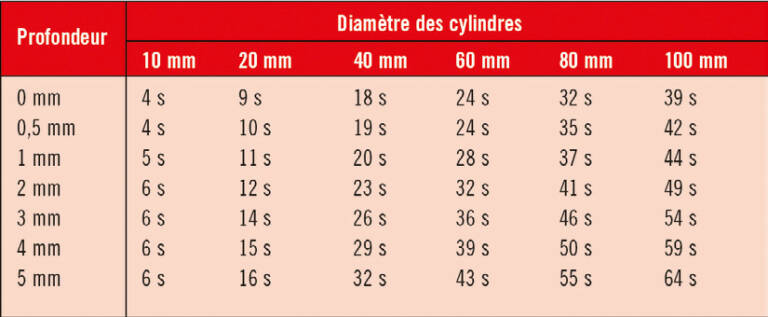
Tableau 3. : Ordres de grandeur de la valeur de Δt700/300 (s) en fonction de la profondeur (mm) à partir de la surface de cylindres de différents diamètres trempés à 900°C dans une huile très agitée.
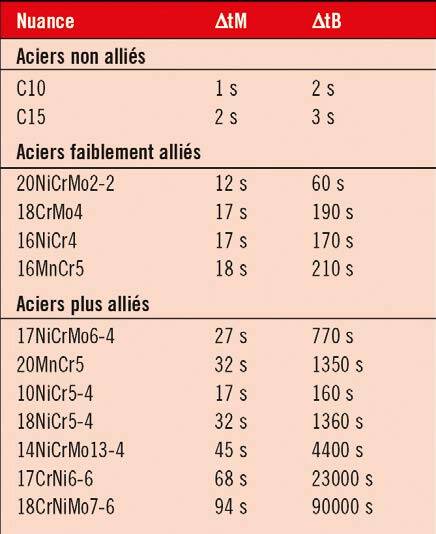
Tableau 4. : Ordres de grandeur de la valeur des paramètres ΔtM et ΔtB pour des aciers de cémentation.
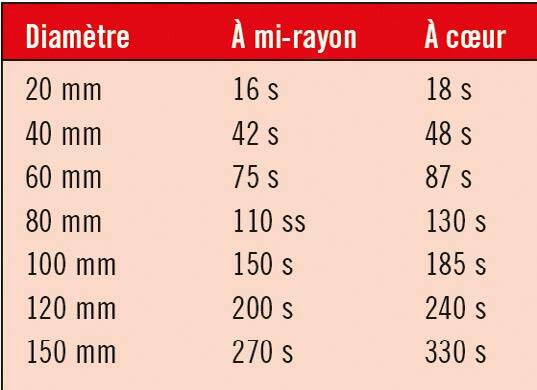
Tableau 5. : Ordres de grandeur du paramètre Δt700/300 (s) lors de la trempe à 900°C de cylindres de différents diamètres dans une huile très agitée.
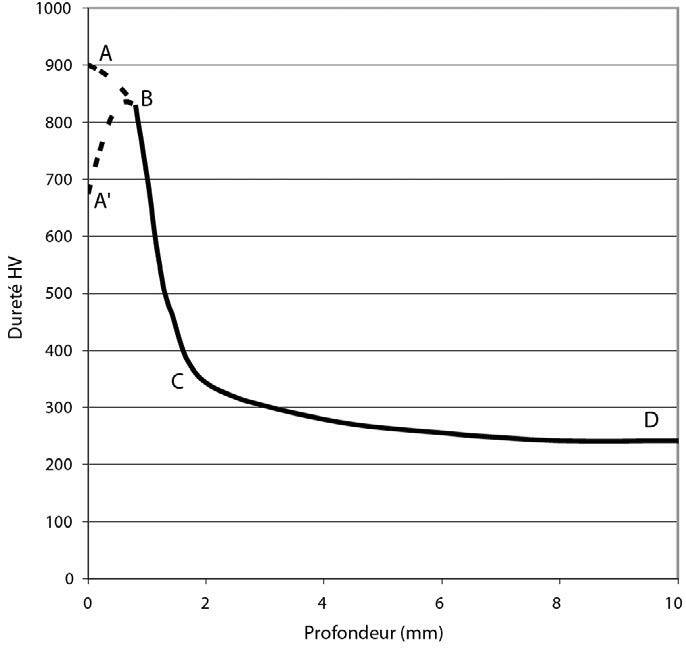
Figure 7. : Exemple de description des évolutions de la dureté en profondeur.
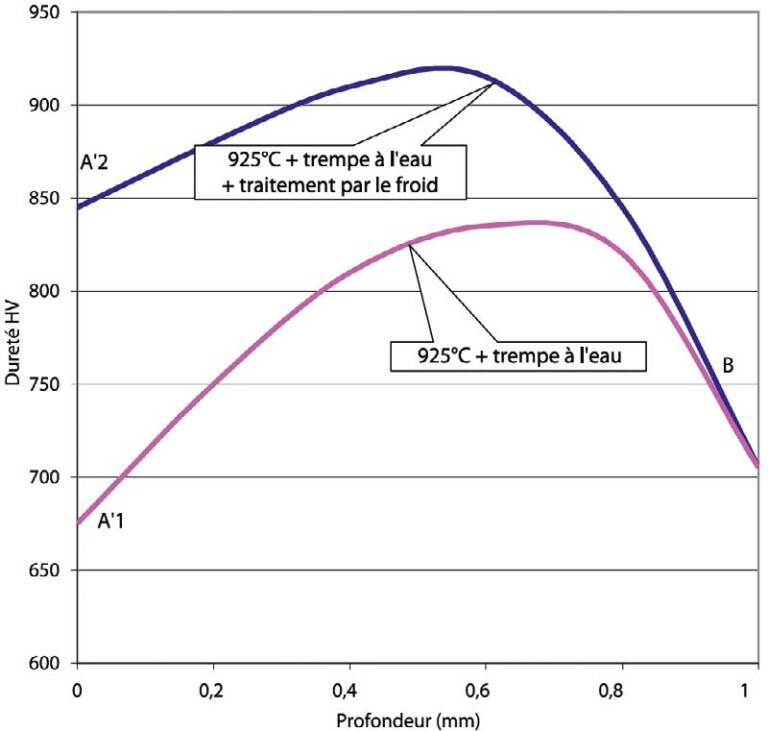
Figure 8. : Exemple illustrant l’effet d’un traitement par le froid sur la courbe dureté/profondeur.
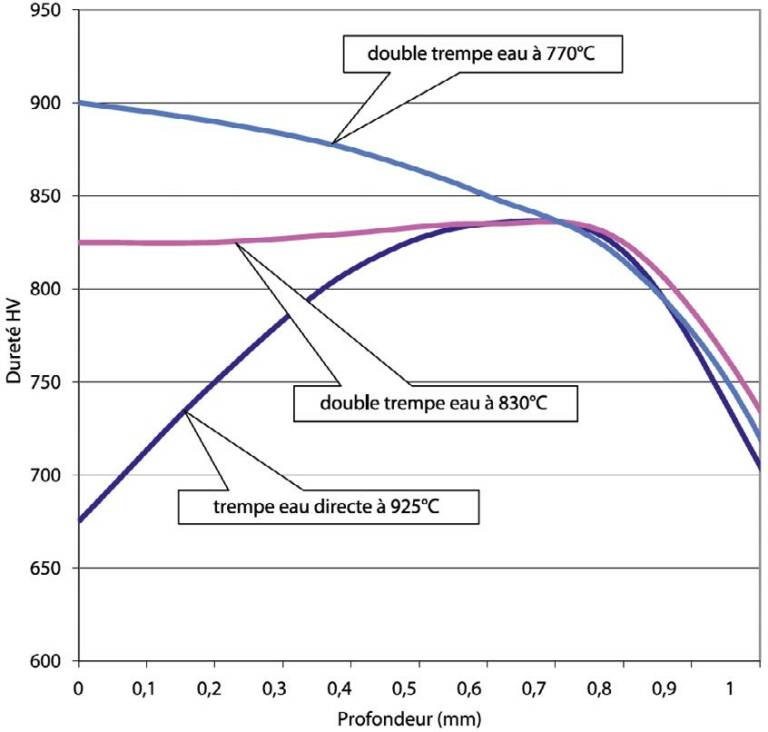
Figure 9. : Exemple illustrant l’effet d’une double trempe sur la courbe dureté/profondeur
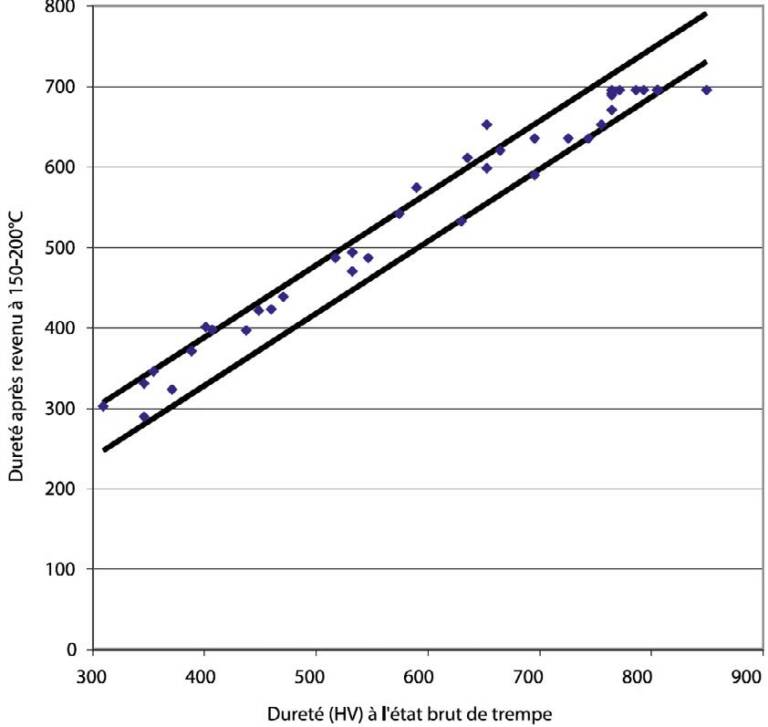
Figure 10. : Influence d’un revenu à 150/200°C sur la dureté de la zone durcie.
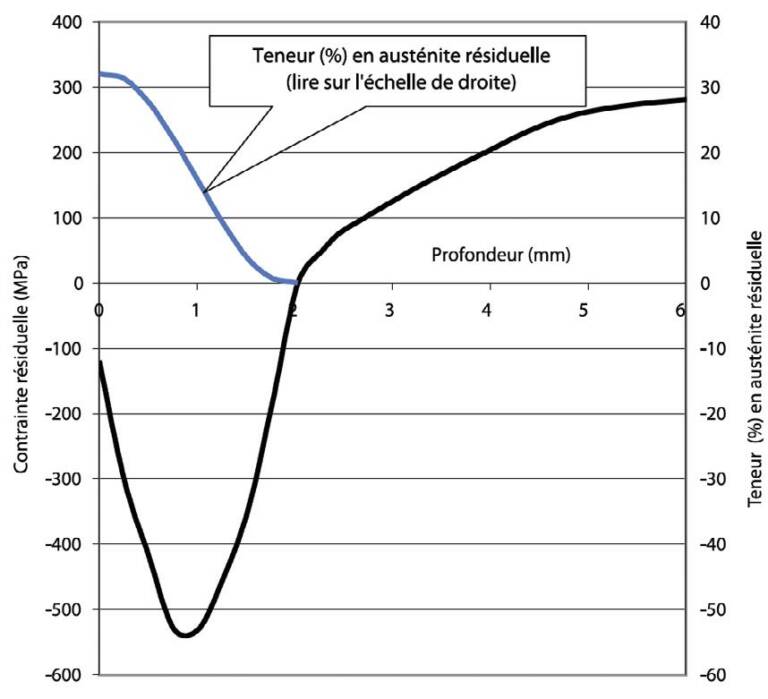
Figure 11. : Contraintes résiduelles et teneur en austénite résiduelle après cémentation et trempe à l’huile très agitée d’un cylindre de 15 mm de diamètre en acier du type 20NiCrMo2-2.