Les particularités métallurgiques des aciers à outils (2/2)
Par Guy Murry, Ingénieur-conseil
Après avoir étudié les particularités métallurgiques des aciers à outil pour travail à froid (numéro 395, mai 2009), nous nous intéressons dans cette seconde partie à celles des aciers à outil pour travail à chaud.
Dans le groupe des aciers à outils alliés pour travail à chaud, la norme NF EN ISO 4957 place neuf nuances assez diverses dont la teneur en carbone est comprise entre 0,25 et 0,6 % et dont la spécificité réside dans le fait qu’elles sont alliées avec des éléments carburigènes comme le montre le tableau 1. Cette particularité permet de leur conférer par revenu à une température supérieure à 450 °C une dureté élevée suffisamment stable à chaud pour satisfaire les exigences du type de travail considéré ici.
Ces nuances sont caractérisées par leur capacité de durcissement que l’on peut quantifier en prenant en compte leur teneur en carbone et leur dureté à l’état trempé et revenu (tel que figurant dans la norme) et leur trempabilité vérifiée, selon la norme, à l’aide d’une mesure de dureté sur un échantillon type traité selon les conditions imposées. Le tableau 2 rassemble ces données.
En complément, le tableau 3 regroupe des indications complémentaires utiles au métallurgiste.
Ces données permettent de noter que :
les aciers présentés ont, compte tenu de leurs teneurs en éléments d’alliage, des trempabilités suffisantes pour que cette caractéristique ne pose généralement pas de problème,
après arrêt de la trempe à la température ambiante, la teneur en austénite résiduelle ne dépasse pas 10 %,
la transformation martensitique est pratiquement terminée après trempe suivie d’un refroidissement à - 130 °C.
En ce qui concerne le revenu, la norme décrit les variations de la dureté en fonction de la température à laquelle il est réalisé. Un exemple en est donné à la figure 1 qui fait bien apparaître les différents domaines de transformation structurale (avec rappel de ce que seraient ces évolutions avec un acier non allié à teneur comparable en carbone) :
à basse température (< 250 °C) précipitation du carbure e (Fe2,4C) accompagnée d’une faible baisse de la dureté (identique en absence d’éléments d’alliage), l’effet adoucissant de la précipitation est partiellement compensé par l’effet durcissant dû à la finesse des précipités,
au-dessus de 250 °C et jusqu’à environ 500 °C le carbone précipite sous forme de cémentite substituée (Fe,M) 3C assez fine qui met en jeu les éléments carburigènes (surtout Cr et W) mais aussi Mn et provoque un durcissement d’autant plus important que les teneurs en ces éléments sont élevées (d’où l’écart avec l’acier non allié),
au-dessus de 500 °C le début de coalescence de la cémentite substituée engendre un adoucissement qui est partiellement compensé par le durcissement secondaire dû à l’échange du carbone qui permet la précipitation des carbures des éléments carburigènes. Cette évolution maintient la dureté à un niveau relativement élevé favorable à la tenue mécanique à chaud.
Le tableau 4 donne des ordres de grandeur des duretés ainsi accessibles.
Pour assurer une bonne tenue mécanique lors du travail à chaud, il est nécessaire de stabiliser l’état structural en exécutant un revenu à une température sensiblement supérieure à la température de travail afin que le fait de porter l’acier à cette dernière température n’engendre pas un processus de revenu supplémentaire qui abaisserait la résistance mécanique de l’acier. La figure 2 décrit, à titre d’exemple, et pour un acier du type X40CrMoV5-1 trempé et revenu à 550 °C, ce que sont les évolutions de la dureté mesurée à la température ambiante après des réchauffages à différentes températures. On voit qu’ici la température de travail ne devrait pas dépasser 500/525 °C. Ces résultats permettent aussi d’interpréter les variations de la résistance à la traction d’un tel acier en fonction de la température qu’il atteint en service (figure 2). Au-dessous de 500/550 °C, la résistance à chaud est légèrement abaissée (d’une manière réversible) essentiellement par une plus grande facilité de glissement des dislocations. Au-dessus de 500/525 °C, le glissement et la montée des dislocations deviennent de plus en plus faciles, le fluage peut se développer et la structure commence à coalescer.
Les particularités métallurgiques des aciers rapides
Le groupe des aciers rapides dans la norme NF EN ISO 4957 comporte 16 nuances dont la spécificité réside dans le fait qu’elles sont alliées avec des éléments carburigènes comme les aciers alliés pour travail à chaud mais en proportions plus importantes. Ces aciers sont dits « rapides » car ils sont les « descendants » des aciers dits « à coupe rapide » créés par les métallurgistes américains à la fin du 19e siècle et au début du 20e siècle, aciers qui permirent d’augmenter grandement les vitesses de coupe. Le tableau 5 rappelle les teneurs moyennes en carbone et en éléments carburigènes des nuances définies par la norme NF EN ISO 4957. Il indique aussi quelle valeur prend le paramètre « tungstène équivalent » utilisé pour caractériser l’effet global dû aux additions d’éléments carburigènes. La figure 3 met en évidence la relation qui existe entre ce paramètre et la teneur en carbone.
Il faut rappeler ici que, avant la création de la norme NF EN ISO-4957, il était fréquent d’utiliser la dénomination « acier semi rapide » pour désigner des aciers dont le paramètre « tungstène équivalent » prenait une valeur inférieure à 20 %. Les performances de ces aciers à outils étaient plus faibles que celles des aciers dits simplement « rapides ». On retrouve trois de ces nuances dans la norme NF EN ISO-4957, à savoir : HS0-4-1 HS1-4-2 et HS3-3-2.
La figure 3 montre à quel point elles sont (par rapport à leurs teneurs en carbone) moins chargées en éléments carburigènes et se trouvent, de ce fait, moins performantes. Nous ne les prendrons pas en compte dans ce qui suit.
Les compositions chimiques des aciers rapides définis par la norme NF EN ISO-4957 sont telles que le carbone n’est pas totalement soluble dans l’austénite à l’état solide. Lors des traitements comportant une austénitisation, il subsistera donc des carbures non dissous dispersés dans une matrice austénitique. Ces carbures peuvent être de trois types :
1. Carbures de chrome plus ou moins substitués en fer, molybdène, tungstène du type M23C6.
2. Carbures de tungstène et de molybdène plus ou moins substitués en fer du type M6C.
3. Carbures de vanadium du type V4C3.
Ces nuances sont caractérisées par leur capacité de durcissement que l’on peut quantifier en prenant en compte leur teneur en carbone et leur dureté à l’état trempé et revenu (tel que figurant dans la norme) ainsi que leur trempabilité vérifiée, selon la norme, à l’aide d’une mesure de dureté sur un échantillon type traité selon les conditions imposées.
A noter que leur trempabilité est telle que ce paramètre ne pose pas de problème dans la très grande majorité des cas pratiques. Le tableau 6 rassemble ces données.
Pour un acier donné la composition chimique de la matrice, les types de carbures, leurs proportions et leur composition chimique dépendent des conditions d’austénitisation qu’il faudra ajuster pour optimiser les performances des outils.
Le tableau 7, à titre d’exemple, décrit les évolutions, en fonction de la température d’austénitisation, de la composition chimique de la matrice d’un acier du type HS6-5-2C à l’état brut de trempe. Ce tableau donne des ordres de grandeur de certaines propriétés de cette même matrice. A titre de comparaison, le tableau 8 apporte les mêmes informations pour un acier du type HS18-0-1 austénitisé à 1 275 °C.
On constate que la composition de la matrice en fait un acier allié à teneur en carbone assez élevée et dont la trempabilité est assurée notamment par la teneur en chrome. Compte tenu du haut niveau des températures d’austénitisation (1 180 à 1 220 °C pour l’acier HS6-5-2C, 1 275 pour l’acier HS18-0-1) il subsistera de l’austénite résiduelle après trempe martensitique comme le montre le tableau 9. Un traitement par le froid peut en transformer une partie mais nous allons voir que le revenu va jouer ici un rôle particulier.
Le tableau 10 décrit l’évolution, en fonction de la température d’austénitisation, des proportions des différents types de carbures non dissous présents dans un acier du type HS6-5-2C à l’état brut de trempe.
On voit que, dans l’exemple cité ici (acier du type HS6-5-2C), la mise en solution des carbures de type M23C6 se fait assez facilement à des températures relativement basses (≤ 1 000 °C). Par contre celle des carbures des types M6C et M4C3 ne commence qu’au-dessus de 1 150 °C et elle ne s’achève pas à l’état solide. Le résidu solide constitue les carbures non dissous. Selon la température d’austénitisation, la composition de ces carbures peut aussi évoluer parfois. C’est ainsi, par exemple, que dans un acier du type HS6-5-2C le carbure M4C3 peut s’enrichir en vanadium lorsque la température s’élève au dessus de 1 200 °C.
En ce qui concerne le revenu après trempe martensitique des aciers rapides, la norme prescrit un double revenu c’est-à-dire la réalisation de deux cycles comportant chacun chauffage et maintien à la même température suivi d’un refroidissement jusqu’à la température ambiante. Cette procédure (compte tenu du domaine de température dans lequel les revenus sont réalisés) provoque le revenu de la martensite formée lors de la trempe mais elle engendre aussi une évolution particulière de l’austénite résiduelle qui, pendant le maintien à la température lors du premier revenu, est le siège d’une précipitation de carbures qui la désature (on dit que l’austénite résiduelle est « sensibilisée » ou « déstabilisée »). De ce fait l’austénite résiduelle est appauvrie en carbone et en éléments d’alliage. Sa température Ms (dite alors M’s) se trouve donc relevée et, lors du refroidissement qui clôt le premier revenu, elle se transforme en martensite (dite alors « secondaire »). Il devient donc nécessaire de stabiliser la structure à l’aide d’un revenu supplémentaire, le deuxième évoqué ci-dessus. Il faut noter ici que certains praticiens préconisent l’exécution de trois, voire quatre revenus successifs (surtout avec les aciers rapides au cobalt) pour transformer toute l’austénite résiduelle.
En fait, comme le montre la figure 4 pour un acier HS6-5-2, il peut parfois suffire de deux revenus dans la mesure où leur température est bien choisie.
Pour sa part la norme NF EN ISO 4957 décrit les variations de la dureté en fonction de la température à laquelle ce double revenu est réalisé. Toutes les courbes dureté = f (température de double revenu) passent (comme le montre la figure 5) par une valeur maximale de la dureté qui correspond à une gamme de température de revenu comprise entre 525 °C et 575 °C. La pratique courante est de retenir une température comprise dans cet intervalle en tenant compte du fait que le choix d’une température proche du haut du domaine permet de diminuer un peu la fragilité de l’outil.
Notons que la principale action qui détermine les propriétés d’usage des aciers rapides est le traitement thermique mais que, dans ce cadre, la température d’austénitisation est le facteur prépondérant. Les figures 6 et 7 illustrent ce fait en prenant en compte les capacités de coupe de forets en aciers des types HS1-18-1 et
HS6-5-2 trempés et doublement revenus à différentes températures. La capacité de coupe est ici caractérisée par la somme des longueurs des trous percés dans un acier C70 recuit (dureté 200/220 HBW) avant usure des forets.
Enfin, on peut ajouter ici une mention relative à un traitement particulier des aciers rapides qui consiste à réaliser l’austénitisation à des températures de l’ordre de 1 050 à 1 150 °C sans changer les conditions de revenu. La résistance à l’usure à froid ou à tiède est alors renforcée par la présence d’une forte proportion de carbures non dissous tandis que la ténacité est augmentée. n
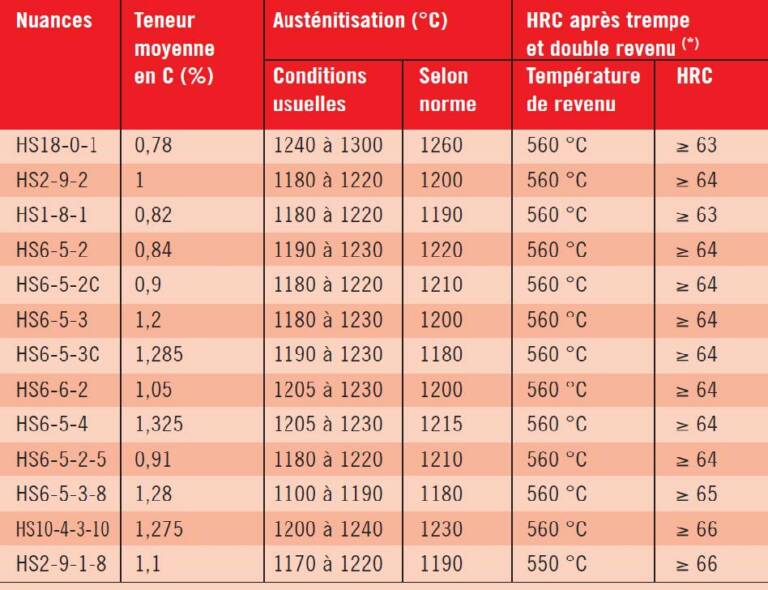
Tableau 6 : Niveaux de dureté des aciers rapides après trempe et revenu sur échantillon type selon norme NF EN ISO 4957. (*) Selon conditions imposées par la norme NF EN ISO 4957.
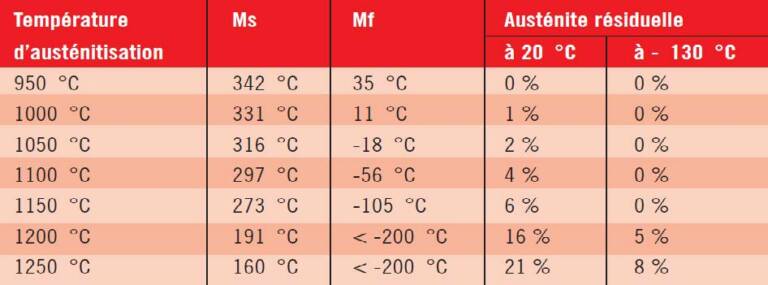
Tableau 9 : Ordres de grandeur de certaines caractéristiques de la matrice d’un acier HS6-5-2C après austénitisation à différentes températures.
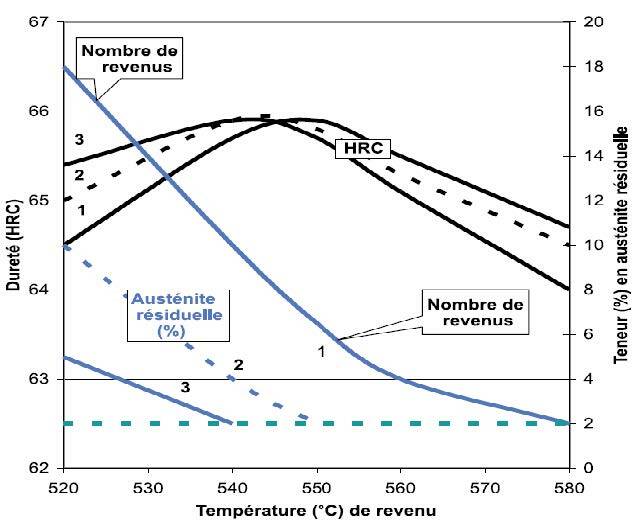
Figure 4 : Influences des températures et du nombre de revenus sur un acier du type HS6-5-2.
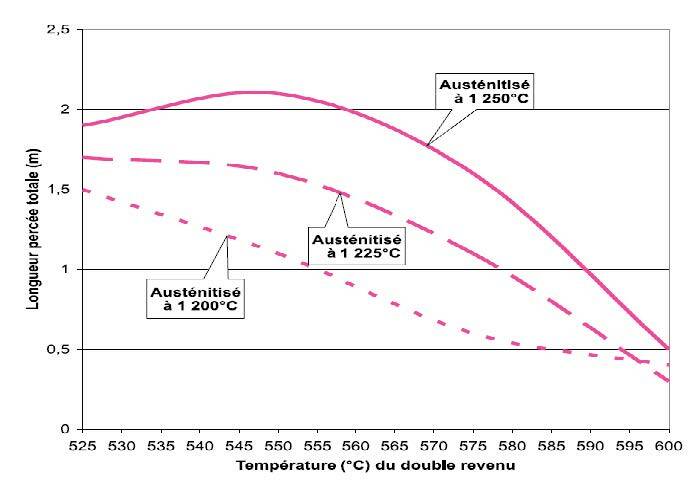
Figure 7 : Longueur totale percée avant usure par un foret en acier HS6-5-2 trempé
à 1 200, 1 225 ou 1 250 °C
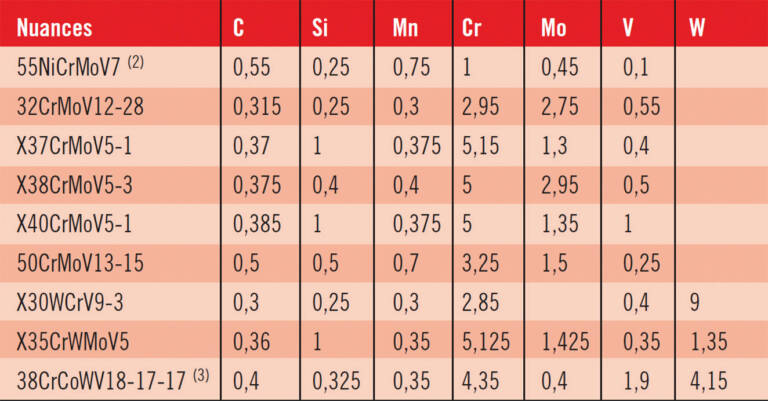
Tableau 1 : Composition chimique moyenne (%) des aciers alliés pour travail à chaud selon NF EN ISO 4957 (1).
(1) Pour toutes les nuances S £ 0,030 % et P £ 0,030 %. (2) 1,50 £ Ni % £ 1,80. (3) 4,00 £ Co % £ 4,5.
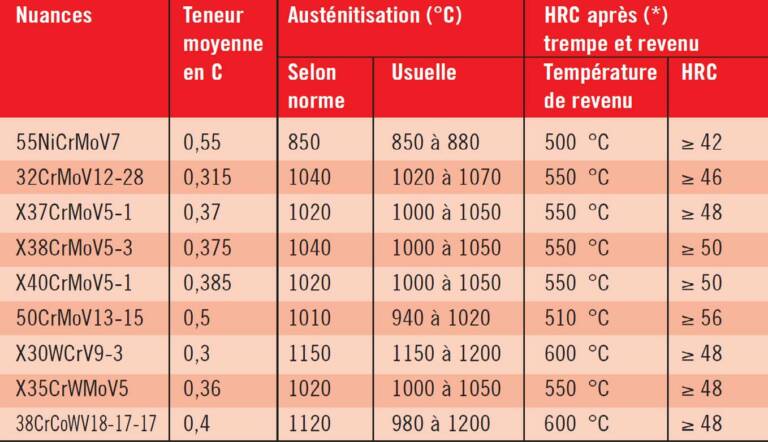
Tableau 2 : Niveaux de dureté des aciers alliés pour travail à chaud après trempe et revenu sur échantillon type selon norme. (*) Selon conditions imposées par la norme NF EN ISO 4957.
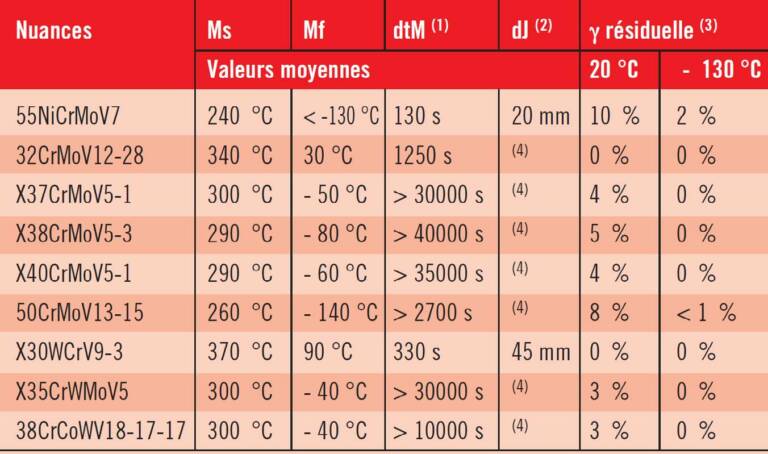
Tableau 3 : Ordres de grandeur de certains paramètres spécifiques. (1) Paramètre %t700/300 correspondant à loi critique de transformation martensitique. (2) Distance à l’extrémité refroidie de l’éprouvette Jominy du point qui se refroidit selon la loi critique de transformation martensitique. (3) Teneur (%) en austénite résiduelle après trempe martensitique arrêtée à 20 ou –130 °C. (4) dJ > 70mm.
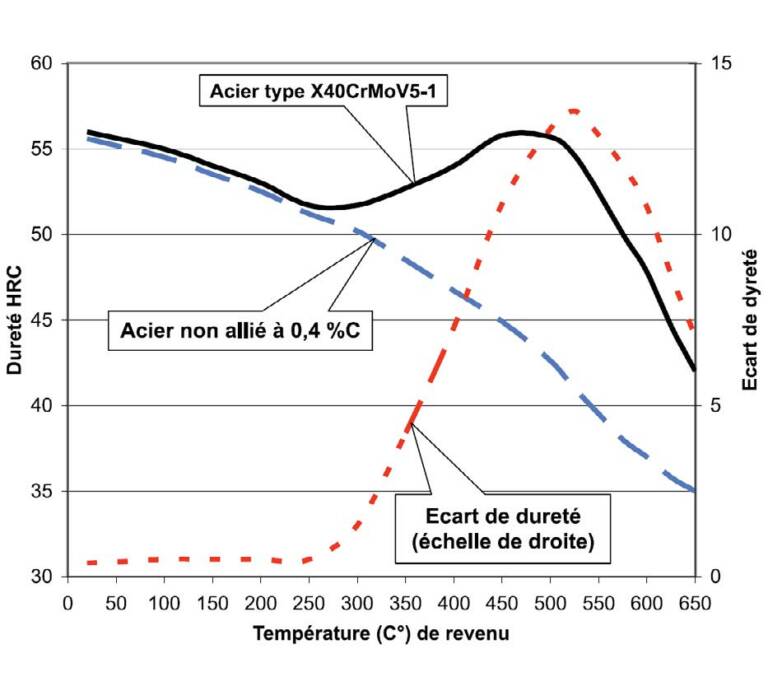
Figure 1 : Dureté d’un acier du type X40CrMoV5-1 après trempe et revenu.
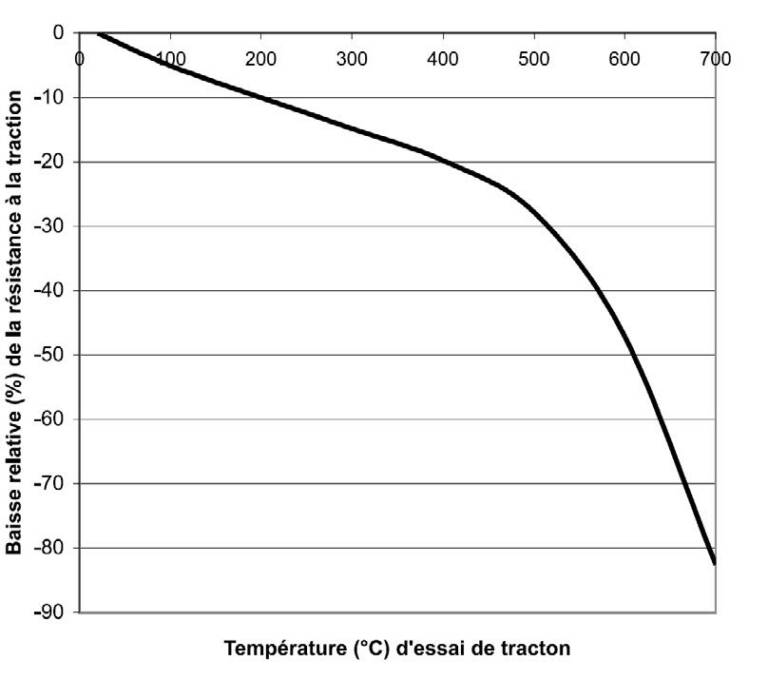
Figure 2 : Ordres de grandeur des évolutions de la résistance à la traction à chaud d’aciers à outils pour travail à chaud des types à 5 % de chrome.
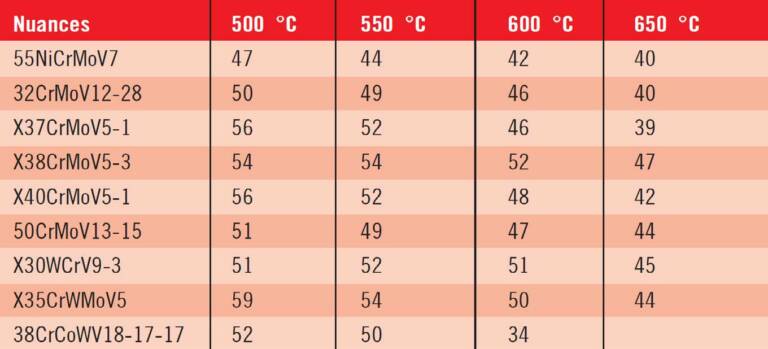
Tableau 4 : Ordre de grandeur de la dureté HRC après trempe et revenu (1 heure).
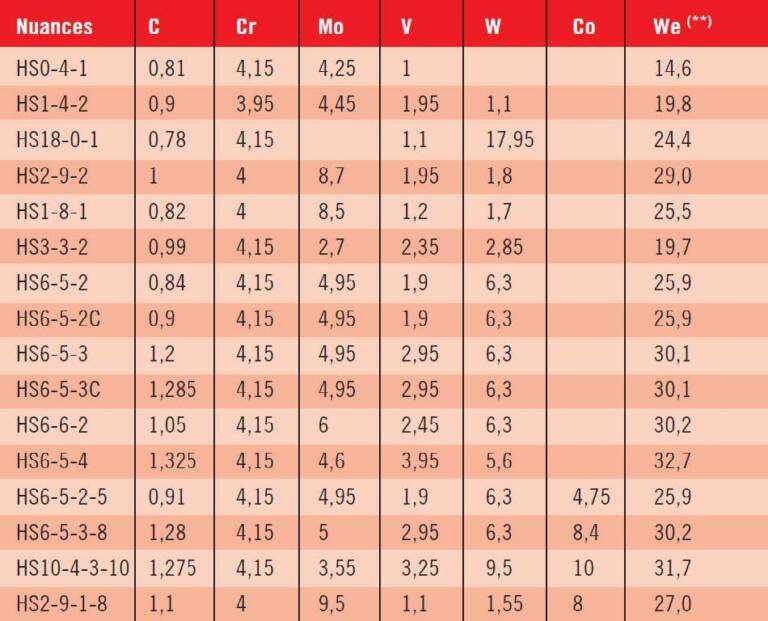
Tableau 5 : Composition chimique moyenne (%) des aciers rapides selon NF EN ISO 4957 (*). (*) Pour toutes les nuances S ≤ 0,030 %, P ≤ 0,030 %, Mn ≤ 0,40 %.(**) We = 0,5*(Cr %)+(W %)+2*(Mo %)+4(V %).
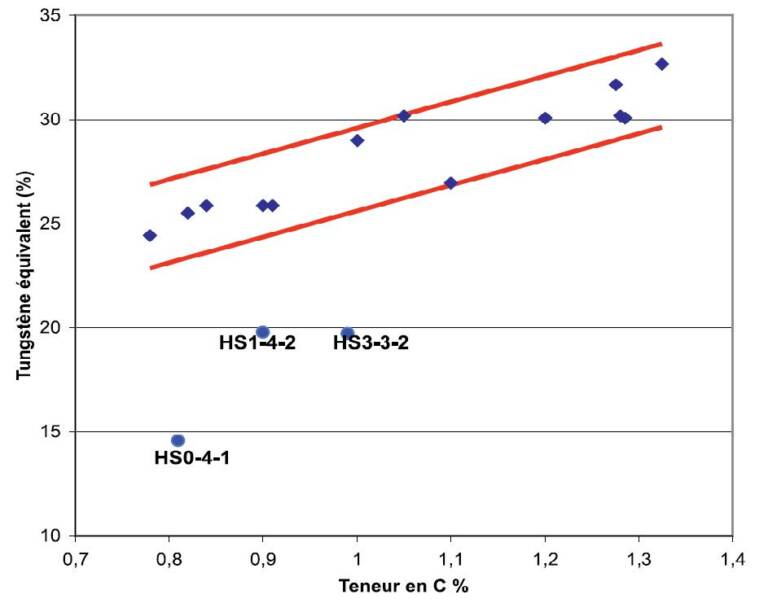
Figure 3 : Relation entre We et la teneur en carbone.
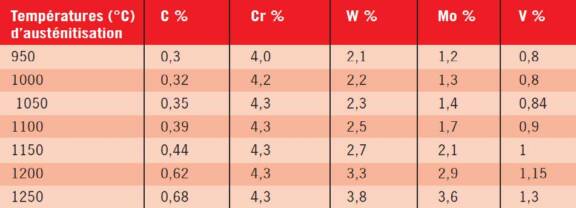
Tableau 7 : Ordres de grandeur de la composition chimique (% en poids) de la matrice d’un acier HS6-5-2C après austénitisation à différentes températures.
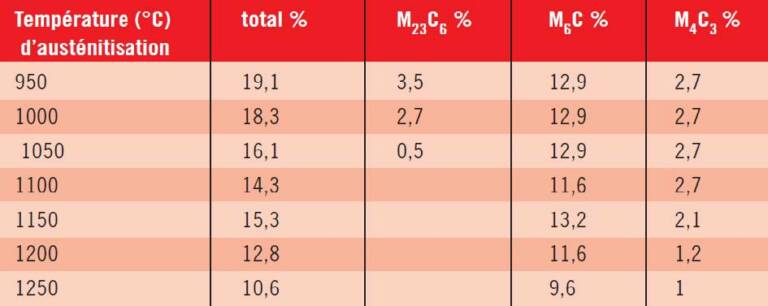
Tableau 10 : Proportions (%) pondérales des carbures non dissous après austénitisation d’un acier HS6-5-2C à différentes températures.
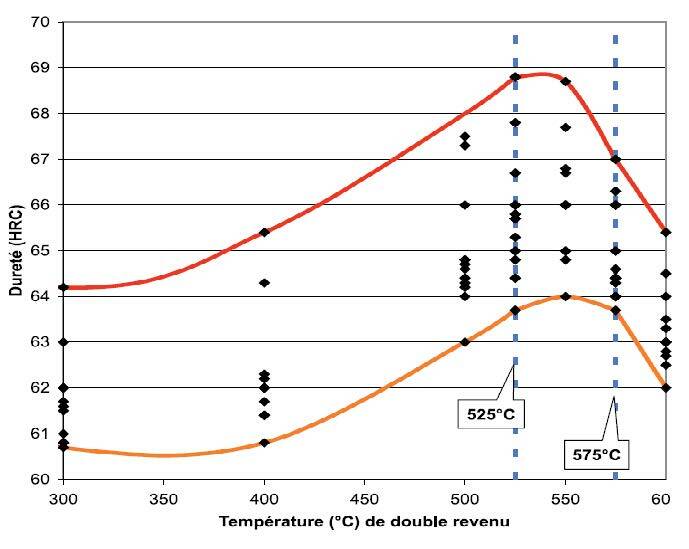
Figure 5 : évolutions de la dureté des aciers rapides en fonction de la température
de double revenu selon la norme.