Le four à pot automatisé
Par Christian Lidin, directeur technique SOLO Swis
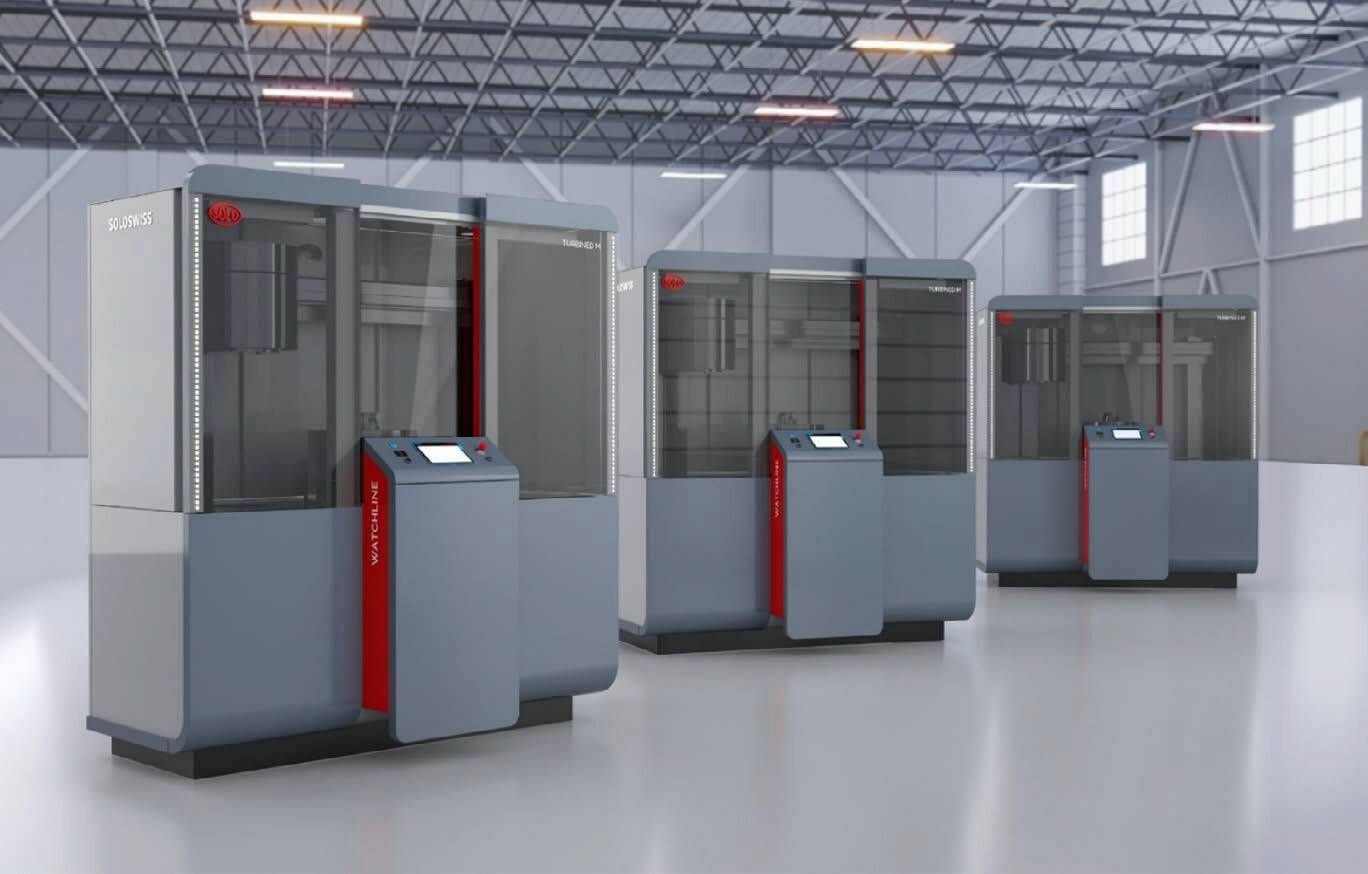
Les progrès dans le domaine de la métallurgie et du traitement thermique des alliages métalliques et autres procédés ont conduit au développement de nouvelles technologies, parmi lesquelles les fours à pot SOLO Swiss avec transferts automatiques. Ces équipements représentent une évolution significative au regard des méthodes traditionnelles en assurant le contrôle des processus de traitement.
Les alliages métalliques sont des matériaux essentiels dans de nombreux secteurs. Leurs propriétés mécaniques, thermiques et chimiques sont fondamentales pour garantir des performances optimales aux produits finis. À cela s’ajoutent les techniques de traitement thermique, telles que le durcissement par précipitation, le recuit, le revenu, et le vieillissement, qui ont pour objectif d’ajuster ces propriétés pour répondre aux applications spécifiques. Les fours à pot avec transferts automatiques pour le refroidissement constituent une plateforme technologique avancée permettant de réaliser ces traitements de manière efficiente et reproductible. La précision et la qualité des matériaux traités sont primordiales dans les métiers de l’horlogerie, du médical et de l’électronique. Les composants employés dans ces domaines doivent souvent être fabriqués avec des tolérances extrêmement strictes et des caractéristiques spécifiques, afin d’assurer leur fiabilité et leur performance. Le four à pot, avec sa capacité à garantir un contrôle de la température et à maintenir une atmosphère stable, est un outil pour atteindre ces exigences élevées. Les fours à pot SOLO Swiss permettent de traiter divers matériaux, tels que les métaux précieux, les alliages spéciaux et les composés chimiques, utilisés dans la fabrication des montres, des instruments médicaux et des composants électroniques. Ils assurent une uniformité de traitement et minimisent les contaminations, garantissant des produits de qualité.
SOLO Swiss, a décidé de faire évoluer sa gamme de fours à pot afin de répondre aux contraintes de qualité des pièces traitées, de plus en plus demandées dans l’horlogerie, le médical et l’électronique. Ces derniers utilisent une grande panoplie de nuances d’acier, chacune nécessitant des conditions de traitement spécifiques afin d’atteindre les propriétés désirées.
Les nouveaux modèles sont conçus pour offrir un contrôle thermique plus précis, une meilleure efficacité énergétique et une durabilité accrue. Ces améliorations permettent de traiter diverses nuances d’acier et alliages, assurant à chaque type de matériau le traitement optimal pour maximiser ses performances.
En outre, les nouveaux fours dotés de transferts automatiques permettent de traiter les matériaux en continu, y compris la nuit et sans assistance. Grâce à ces innovations, les fabricants peuvent garantir une conformité aux normes les plus strictes de qualité et de performance pour chaque pièce traitée.
1. Objectifs du traitement thermique lié aux fours à pot
Les principaux objectifs du traitement thermique réalisé avec des fours à pot sont :
Amélioration de la dureté : augmenter la résistance à l’usure des pièces mécaniques.
Renforcement de la ténacité : augmenter la capacité des matériaux à absorber l’énergie sans se fracturer.
Amélioration de la ductilité : augmenter la capacité des matériaux à se déformer sans se casser.
Réduction des tensions internes : éliminer les contraintes résiduelles qui pourraient provoquer des déformations ou des fissures.
Amélioration de la résistance à la corrosion : augmenter la durabilité des matériaux dans des environnements corrosifs.
2. Types de traitements thermiques
Les procédés de traitements thermiques effectués dans des fours à pot comprennent, entre autres :
• Le Recuit :
Objectif : adoucir le matériau, augmenter sa ductilité et éliminer les tensions internes.
Processus : chauffage du matériau à une température spécifique suivie d’un refroidissement lent et contrôlé à l’intérieur du pot.
• Le Revenu :
Objectif : réduire la fragilité du matériau après une trempe, augmentant ainsi sa ténacité tout en conservant une partie de la dureté obtenue.
Processus : chauffage à une température modérée, suivi d’un refroidissement contrôlé, sur la pièce trempée préalablement.
• La Normalisation :
Objectif : uniformiser la structure microcristalline du matériau pour améliorer ses propriétés mécaniques.
Processus : chauffage à une température spécifique suivi d’un refroidissement à l’air à l’intérieur du pot.
• Le Brasage :
Objectif : assembler des pièces en faisant fondre un métal d’apport entre elles.
Processus : chauffage des pièces et du métal d’apport à une température suffisante pour faire fondre ce dernier et créer une liaison forte et durable entre les pièces.
• La nitruration/nitrocarburation :
Objectif : améliorer la dureté de surface et la résistance à la corrosion en diffusant de l’azote à la surface du matériau.
Processus : chauffage du matériau dans une atmosphère riche en azote à une température relativement basse sur une période prolongée.
La nitruration de l’acier conduit à la formation de nitrures de fer tels que le nitrure de fer γ’ (Fe4N) et le nitrure de fer ε (Fe₂₋₃N).
Fe+N→Fe4N (nitrure de fer γ’)
2Fe+3N→Fe2N (nitrure de fer ε)
• L’Oxydation :
Objectif : créer une couche d’oxyde protectrice sur la surface du matériau pour améliorer la résistance à la corrosion ou pour donner un aspect esthétique.
Processus : chauffage du matériau dans une atmosphère contrôlée qui favorise la formation d’une couche d’oxyde uniforme.
3Fe+2O2→Fe3O4
4Fe+3O2→2Fe2O3
• Le Séchage :
Objectif : éliminer l’humidité ou les solvants des matériaux, souvent utilisés pour préparer des composants avant un traitement supplémentaire.
Processus : chauffage du matériau à une température spécifique pour évaporer l’humidité ou les solvants de manière contrôlée.
• Le Dégazage :
Objectif : il peut être adopté pour dégazer les matériaux, éliminant les impuretés et les gaz résiduels qui pourraient être nuisibles.
Processus : le matériau est chauffé à une température élevée dans un four, souvent au-delà du point de fusion pour les métaux, afin de libérer les gaz dissous. Avec un temps de maintien qui dépend du type de matériau et de la quantité de gaz à éliminer.
3. Importance des fours à pot
Les fours à pot sont particulièrement adaptés dans de nombreux secteurs industriels pour leurs capacités spécifiques de traitement thermique, notamment :
Aéronautique : pour produire des composants légers et résistants.
Automobile : pour améliorer la performance et la durabilité de certaines petites pièces.
Électronique : pour ajuster les propriétés des matériaux semi-conducteurs et autres composants critiques.
Horlogerie : pour garantir la précision et la durabilité des composants horlogers, notamment les ressorts, les axes, les engrenages, les vis, etc.
Médical : pour améliorer la biocompatibilité et la durabilité des implants, des instruments chirurgicaux et autres dispositifs médicaux.
Bijouterie : pour le recuit des métaux et le brasage des composants afin d’assembler des pièces complexes de manière durable.
4. Pourquoi le développement d’un nouveau four à pot automatisé ?
Cette innovation vise à répondre à plusieurs besoins critiques dans le traitement thermique des matériaux. L’objectif principal est de concevoir un équipement capable de fournir des conditions thermiques précises et homogènes de manière automatisée, améliorant ainsi la qualité et la répétabilité des traitements thermiques. Ce four est destiné à offrir de meilleures performances grâce à des technologies avancées de contrôle de la température et à une automatisation accrue des processus. Les améliorations spécifiques attendues de ce nouveau four à pot automatisé par rapport aux technologies existantes incluent :
• Précision et stabilité de la température
Intégration de capteurs de température haute précision et de systèmes de contrôles avancés pour maintenir des conditions thermiques stables et homogènes. Réduction des variations de température à l’intérieur du pot, garantissant une distribution thermique uniforme.
• Automatisation et efficacité
Système de contrôle entièrement automatisé permettant de programmer et de réguler les cycles thermiques sans intervention humaine, augmentant ainsi l’efficacité et la reproductibilité des processus. Réduction des erreurs humaines et amélioration de la sécurité opérationnelle.
• Efficacité énergétique
Utilisation d’éléments chauffants optimisés et d’une isolation thermique améliorée pour réduire les pertes de chaleur et augmenter l’efficacité énergétique globale du four.
Diminution des coûts des consommations d’énergie et de l’empreinte écologique associés aux traitements thermiques. Débits de gaz faibles.
• Flexibilité et adaptabilité
Capacité à traiter une large gamme de matériaux et de tailles de lots grâce à des réglages flexibles et des programmes personnalisables. Adaptabilité aux besoins spécifiques des différentes industries, notamment l’aéronautique, l’automobile, la construction, l’électronique, l’horlogerie et le médical.
• Qualité et performances des matériaux
Amélioration des propriétés mécaniques et physiques des matériaux traités, telles que la dureté, la ductilité et la résistance à la corrosion, grâce à des traitements thermiques plus précis et mieux contrôlés.
Réduction des défauts et des variations dans les caractéristiques des matériaux finis. Les fours à pot sont idéals pour le traitement thermique d’une variété de matériaux, principalement les métaux et leurs alliages.
Voici une liste des principaux types de matériaux qui peuvent être traités dans un four à pot :
► Les aciers et alliages d’acier :
• Aciers au carbone.
• Aciers alliés.
• Aciers inoxydables.
• Aciers à outil.
• Phynox
► Les fontes :
• Fontes grises.
• Fontes ductiles (fontes nodulaires).
• Fontes blanches.
► Les métaux non ferreux :
• Aluminium et alliages d’aluminium.
• Cuivre et alliages de cuivre (bronze, laiton).
• Titane et alliages de titane.
► Les métaux précieux :
• Or.
• Argent.
• Platine.
5. Description du four à pot automatisé
Les dimensions standards.
TURBINED M1 (photo 1) : dimensions extérieures 1 380 à 2 050 mm de largeur, 1 020 mm de profondeur et 1 275 mm de hauteur (manuel).
Ce four de base peut être utilisé avec le palan du client et peut être évolutif, avec l’ajout d’un deuxième refroidisseur, d’un deuxième four ou d’un palan.
TURBINED M2 (photo 2) : Dimensions extérieures 1 380 à 2 050 mm de largeur, 1 040 mm de profondeur et 2 010 mm de hauteur (semi-automatique).
Cette version est équipée du palan multiaxe de base.
TURBINED M3 (photo n°3) : Dimensions extérieures 2 200 mm de largeur, 1 250 mm de profondeur et 2 300 mm de hauteur (entièrement automatisé).
Deux pots de traitement thermique :
L’installation est équipée de deux pots distincts, dans lesquels les pièces ou les matériaux à traiter sont placés pour subir différents types de traitements thermiques. Chaque pot est contrôlé individuellement pour maintenir les conditions thermiques spécifiques nécessaires au processus de traitement. L’homogénéité du chauffage et des gaz à l’intérieur du pot, est assurée, d’une part, par une turbine, dans son enceinte, ainsi qu’une seconde placée dans la partie extérieure du pot, au niveau des corps de chauffe.
Transfert automatique des pièces :
En fin de traitement thermique des pièces dans le pot, un mécanisme de mouvement automatique déplace ce dernier vers une station de refroidissement. Ce processus robotisé permet un transfert sans l’assistance d’un opérateur, minimise le temps d’immobilisation des équipements et optimise l’efficacité de la production en éliminant les retards causés par le transfert manuel des pièces.
Station de refroidissement :
La station de refroidissement est conçue pour refroidir efficacement les pièces après leur traitement thermique afin de figer les structures cristallines et d’assurer les propriétés mécaniques désirées. Sur la photo n°4, nous pouvons distinguer les deux pots, placés sur les deux stations de refroidissement et le four au centre.
Système de contrôle et d’automatisation :
Un système avancé de contrôle et d’automatisation gère le flux de travail entre les pots et la station de refroidissement (photo n°5). Il surveille en temps réel les paramètres de traitement comme les températures, les durées et les vitesses de refroidissement pour garantir la qualité et la reproductibilité des traitements.
6. Les gaz
Les fours à pot Solo Turbined peuvent être dotés d’une variété de gaz pour créer des atmosphères contrôlées adaptées aux différents types de traitements thermiques. Voici une explication de certains des gaz couramment employés et de leurs applications dans ces installations :
Ammoniac Craqué (NH3) :
L’ammoniac craqué est destiné à fournir de l’azote, de l’hydrogène 2 NH3 ® N2 + 3H2.
La dissociation se fait au moyen d’un catalyseur au nickel intégré dans le craqueur Elle se produit à des températures comprises entre 850 °C et 1 000 °C.
Le mélange ainsi obtenu est appelé ammoniac craqué il est composé de 75 % H2 et de 25 % N2.

Photo 1. TURBINED M1 : dimensions extérieures 1 380 à 2 050 mm de largeur, 1 020 mm de profondeur et 1 275 mm de hauteur (manuel). @ SOLO Swiss
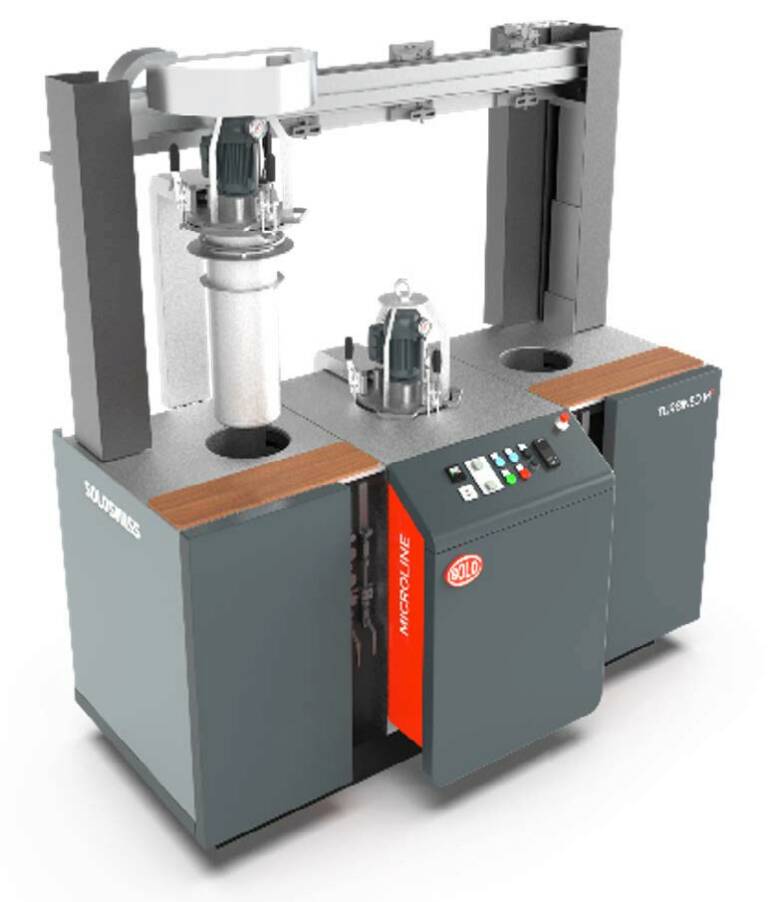
Photo 2. TURBINED M2 : Dimensions extérieures 1 380 à 2 050 mm de largeur, 1 040 mm de profondeur et 2010 mm de hauteur (semi-automatique). @ SOLO Swiss
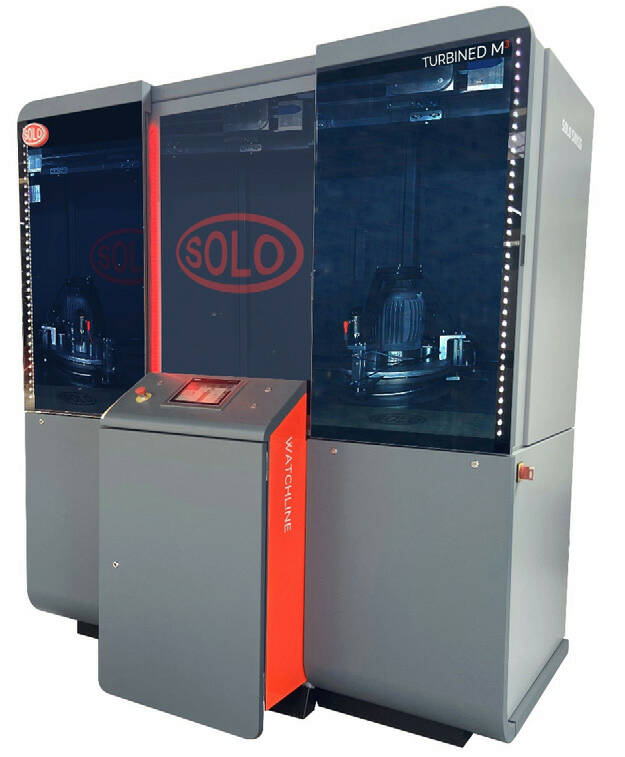
Photo 3. TURBINED M3 : Dimensions extérieures 2200 mm de largeur, 1250 mm de profondeur et 2300 mm de hauteur (entièrement automatisé). @ SOLO Swiss
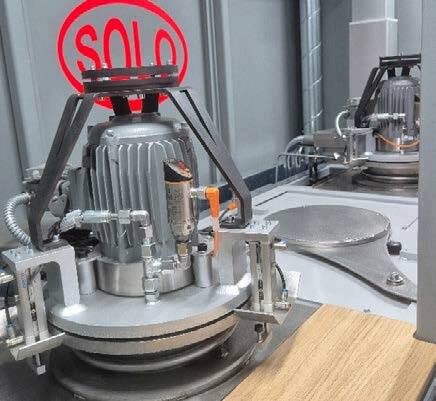
Photo 4. station de refroidissement @ SOLO Swiss
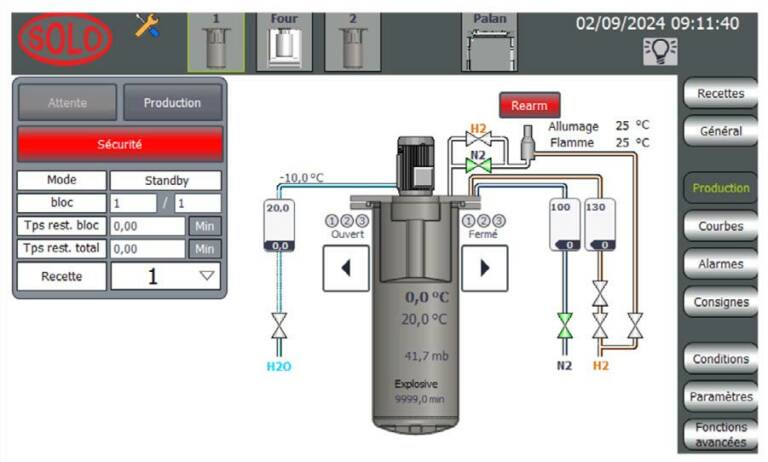
Photo 5. Interface utilisateur intuitive et de dernière génération. @ SOLO Swiss
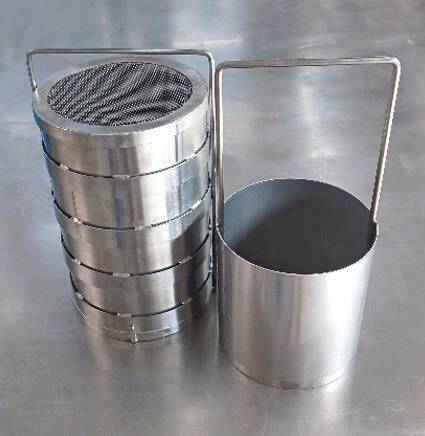
Exemple de paniers. @ SOLO Swiss
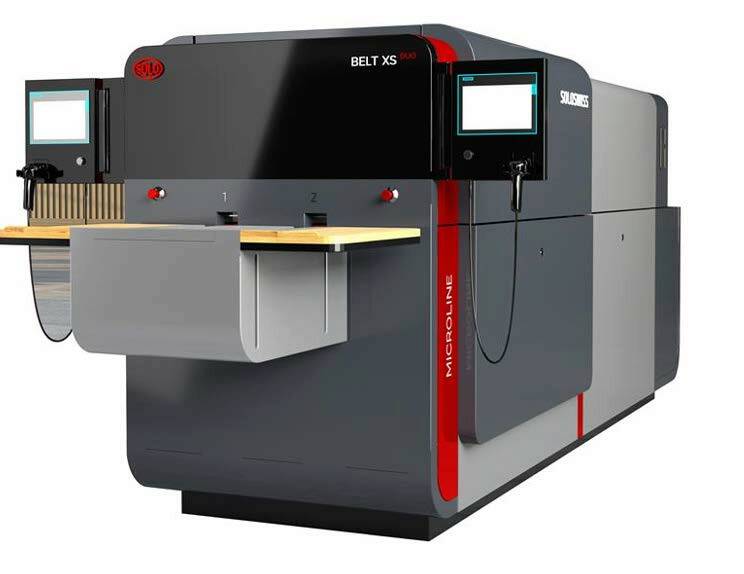
Photo 6. Des paniers adaptés sont fabriqués sur mesure pour le traitement spécifique des pièces. @ SOLO Swiss
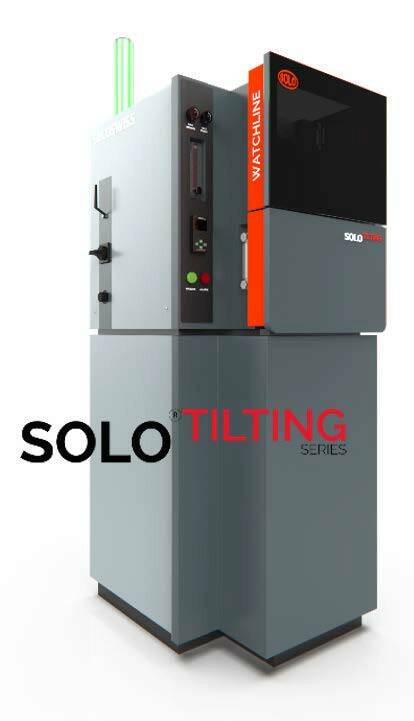
Photo 7. SOLO Swiss a développé un four basculant SOLO TILTING ainsi qu’un nouveau four double bande SOLO BELT permettant d’effectuer tous les
traitements thermiques in situ. @ SOLO Swiss
Hydrogène (H2) :
On se sert de l’hydrogène pour divers processus tels que la réduction des oxydes métalliques à haute température, ce qui améliore la propreté des surfaces métalliques. Il est également appliqué dans les traitements thermochimiques pour modifier la composition chimique des matériaux.
Mélange N2/H2 :
Ce mélange est couramment employé pour créer des atmosphères réductrices ou inertes. Il est particulièrement utile pour les traitements thermiques des aciers inoxydables et autres matériaux sensibles à l’oxydation. Le rapport entre l’azote et l’hydrogène peut être ajusté en fonction des exigences spécifiques du processus.
Azote (N2) :
L’azote est largement adopté pour créer des atmosphères inertes dans les fours à pot. Il aide à prévenir l’oxydation des matériaux métalliques à haute température, assurant ainsi des traitements thermiques sans contamination par l’oxygène atmosphérique.
Argon (Ar) :
L’argon est un gaz inerte souvent utilisé dans les applications pour lesquelles une atmosphère stable et non réactive est nécessaire. Il est parfaitement adapté pour le traitement thermique des métaux non ferreux et des alliages sensibles à l’oxydation.
Air :
Bien que moins fréquent dans les applications nécessitant des atmosphères contrôlées, l’air peut servir dans certains processus comme le traitement d’oxydation.
Formiergaz :
Le formiergaz est une composition d’azote (N2) et d’hydrogène (H2) obtenue directement en bouteille de 5 à 25 % de H2.
Hydrargon :
L’hydrargon, ou plus précisément l’hydrogène argon, est un mélange gazeux utilisé dans divers procédés de traitement thermique des métaux et des alliages. Ce mélange gazeux combine les propriétés de l’hydrogène et de l’argon pour offrir plusieurs avantages dans les processus industriels.
Débitmétrie :
L’intégration de divers gaz protecteurs, tels que l’ammoniac craqué, l’hydrogène, les mélanges N2/H2, l’azote, l’argon et l’air, est contrôlée par des débitmètres massiques. Cela permet de gérer avec précision les débits de gaz et de conserver une traçabilité complète des flux gazeux archivés, assurant ainsi un contrôle rigoureux des conditions de traitement.
7. Composition de la ligne type M3
L’ensemble de la ligne est constitué de plusieurs stations qui sont reliées entre elles par un manipulateur multiaxe.
Elle est composée d’un four équipé de deux pots et de deux stations de refroidissement, d’un manipulateur multiaxe, d’une armoire gaz, le tout connecté à un système informatique de dernière génération.
Cheminements des charges sur la ligne
L’opérateur prépare la charge et l’accroche au couvercle du pot sur la station de préparation n°1. Le tout vient se positionner sur le pot. Un système de fermeture, actionné par des vérins, s’assure que le pot est bien scellé. Un test de pression est réalisé pour vérifier l’absence de fuites. Le pot est ensuite mis sous atmosphère protectrice selon les besoins du cycle. Puis ce dernier est déplacé et introduit automatiquement dans le four.
Après une phase d’homogénéisation, le pot est transféré du four vers la station de refroidissement n°1. Un autre pot venant de la station de préparation n°2 peut alors être introduit dans le four. Une fois le cycle de refroidissement n°1 terminé, le bouchon se détache du pot afin de pouvoir décharger et l’opérateur peut alors récupérer sa charge. Tout est automatisé : la charge transite de station en station selon les étapes de traitement. Le transfert entre le four et le poste de refroidissement s’effectue en déplaçant le pot directement sur la station, permettant à la charge de voyager sans perte de chaleur et sous protection gazeuse, sans passer par des sas intermédiaires.
Avantages :
Dans de nombreux secteurs, la production se fait souvent en petites séries. Les temps de montée en température, de maintien et de refroidissement sont généralement longs, ce qui limite le volume de production possible sur une journée de travail. Un four entièrement automatisé permet de traiter deux charges supplémentaires pendant la nuit, doublant ainsi la capacité de production quotidienne. Un thermocouple placé à l’intérieur du pot et un autre à l’extérieur permettent une régulation en cascade avec une grande précision et assurent une homogénéisation optimale des températures. Il existe différentes versions, allant du manuel au tout automatique, avec la possibilité d’utiliser un ou deux pots sur un four.
Nouveau design :
Design moderne et innovant, pour une parfaite intégration dans vos ateliers de fabrication.
Poste de travail ergonomique pour l’opérateur.
Nouvelle conception :
Faible encombrement au sol.
Accessibilité et maintenance facile.
Modularité du poste de travail.
Nouvelles fonctionnalités : :
Ouverture, fermeture et manipulation du pot complétement automatique.
Gestion intelligente de la consommation électrique, gaz et fluides.
Interconnexion au système informatique de votre usine.
8. Les options
Pour des raisons de traçabilité ou de sécurité des procédés, il est possible d’adapter plusieurs options aux fours à pot telles que :
Des analyseurs, tels qu’un oxymètre, un capteur de point de rosée ou un détecteur d’hydrogène, pour surveiller les conditions atmosphériques à l’intérieur du four.
Une pompe à vide pour des traitements nécessitant une atmosphère contrôlée.
Un système de vaporisation pour l’oxydation des pièces, permettant de créer des couches protectrices ou décoratives.
Des paniers adaptés et fabriqués sur mesure pour le traitement spécifique des pièces (photo n°6).
Un ordinateur pour contrôler et enregistrer les paramètres du four.
Un craqueur d’ammoniac SOLO pour des applications nécessitant de l’ammoniac craqué.
Des modèles de type S spécifiques aux besoins de faible capacité de production.
Un palan pour faciliter la manipulation des fours manuels.
Des gaz inflammables pour certains procédés de traitement thermique.
Conclusion
Le développement d’un nouveau four à pot automatisé représente une avancée significative dans le traitement thermique industriel. Grâce à sa capacité à gérer deux pots simultanément et à automatiser le transfert des charges, cette technologie permet non seulement de maximiser la productivité en traitant des charges supplémentaires pendant la nuit, mais aussi de garantir une qualité et une uniformité optimales des traitements.
L’intégration de gaz protecteurs variés et la gestion précise des conditions atmosphériques offrent une flexibilité accrue pour traiter une large gamme de matériaux, répondant ainsi aux besoins spécifiques de divers métiers, telles que l’horlogerie et le secteur médical entre autres. En somme, cette innovation technique se traduit par une production plus efficace, des coûts réduits et une amélioration significative des performances des matériaux traités, établissant de nouveaux standards dans le domaine du traitement thermique.
Dans la même lignée, SOLO Swiss a aussi développé un four basculant SOLO TILTING ainsi qu’un nouveau four double bande SOLO BELT, offrant les équipements nécessaires pour effectuer tous les traitements thermiques in situ sur diverses petites pièces.