Fonctionnalisation d’un composite époxy/fibre de verre par projection thermique
Par Geoffrey DARUT ICB PMDM UMR 6303, CNRS, Université de Bourgogne Franche-Comté, UTBM, Belfort, Franc
Les polymères thermoplastiques présentent des propriétés attractives, telles que la légèreté et la résistance à la corrosion qui constituent un avantage significatif par rapport à d’autres classes de matériaux comme les métaux[1]. Cependant, les propriétés des matériaux métalliques sont nécessaires pour l’application initiale de la pièce dans son environnement de fonctionnement, comme sa résistance à l’usure.
1. Introduction
Afin de combiner les avantages des polymères avec les propriétés des métaux, la possibilité de les métalliser a ouvert la voie à de nouvelles applications[2]. Les principales techniques de métallisation actuellement utilisées sont des procédés par voie humide telle l’électrodéposition ou le placage chimique, et des procédés par voie sèche comme le dépôt physique en phase vapeur (PVD) ou la projection thermique[3,4]. Les procédés plasma, arc fil et cold spray sont les plus impliqués[2]. Cette étude a consisté à étudier la faisabilité d’un revêtement céramique (Cr2O3) et un cermet (NiCr-Cr3C2), respectivement par projection plasma APS et flamme HVOF, sur un substrat composite époxy / fibre de verre.
2. Contexte de l’étude
Le cahier des charges impose l’utilisation des deux procédés possédés par l’industriel : une torche plasma APS et un pistolet HVOF de type « gas fuel ». Les matériaux considérés comme couche fonctionnelle sont donc Cr2O3 (par APS) et NiCr-Cr3C2 (par HVOF). Ces deux bases de matériaux ont des points de fusion supérieurs à 1 400 °C et des duretés élevées. C’est une contrainte pour la projection sur des thermoplastiques de faibles résistances mécaniques à l’impact et de température de fusion faible entre 100 et 350 °C dans l’ensemble. Également, la nécessité d’utiliser des procédés de projection à haute énergie, comme le plasma et la flamme supersonique HVOF, qui apportent un flux de chaleur important au substrat à revêtir est une contrainte supplémentaire. Lorsque les particules sont injectées dans le plasma, elles ont des températures pouvant être supérieures à leur température de fusion lorsqu’elles impactent et s’étalent sur le substrat. Le flux de chaleur provenant de ces particules est transmis au substrat. Si ce dernier possède une faible température de fusion, il va se dégrader, empêchant la formation d’un revêtement. Concernant le procédé HVOF, les particules sont proches de la température de fusion mais inférieure. Elles ne vont donc pas s’étaler à proprement dit, mais se déformer à l’impact à haute vitesse. Il en résulte que si les propriétés mécaniques du substrat sont faibles comme les thermoplastiques, la surface va être érodée par les particules à grande vitesse comme pour la projection Cold Spray[5].
La littérature scientifique aborde une solution permettant la réalisation de revêtements par projection thermique à partir de particules fondues sur les thermoplastiques. Le point clé est la température de fusion des matériaux utilisés. L’utilisation d’une sous-couche intermédiaire, faite d’un matériau à bas point de fusion, montre des résultats concluants. En effet, différents métaux ont été testés comme sous-couche intermédiaire entre un substrat polyimide/fibre de graphite et un revêtement final par projection APS et arc fil : Al, Zn, Ni3Al ou Cu(6). Même si les revêtements obtenus par arc fil sont plus homogènes et moins poreux, les essais d’adhérence menés montrent un meilleur résultat pour les sous-couches Al et Zn réalisés par projection plasma. Huang et al. ont mené plusieurs études de réalisation de sous-couches par projection plasma d’Al, Zn et CoNiCrAlY sur des substrats polyimide / fibre de quartz[7/9]. Les revêtements Zn et Al sont denses. En revanche, pour le CoNiCrAlY, des porosités sont observées à l’interface avec le composite. Cela est dû à la plus haute température de fusion de ce matériau comparée à Al et Zn. Les particules fondues détériorent alors la surface créant ces porosités fragilisant l’adhérence du revêtement sur le polyimide. Dans cette étude, le zinc est privilégié à l’aluminium, car sa température de fusion est inférieure (419 °C contre 660 °C), mais aussi par sa plus faible conductivité thermique (116 contre 237 W / m.K). La chaleur sera transmise de façon moins efficace au substrat, le préservant davantage. Les études précédentes l’ont mis en évidence. Dans le cas de l’aluminium, des fibres brisées avec des zones endommagées thermiquement entre le substrat et la sous-couche en aluminium ont été observées. Alors que pour les sous couches en zinc, aucun dommage évident n’a été relevé.
Dans la lignée de ces travaux de recherche, des revêtements de zinc ont donc été développés par projection plasma APS pour servir de sous- couche intermédiaire entre le substrat thermoplastique et un revêtement fonctionnel de Cr2O3 par APS et NiCr-Cr3C2 par HVOF.
3. Développement des revêtements
3.1 Matériaux et procédés
Le substrat est un composite époxy / fibre de verre (cf. Figure 1). Sa préparation de surface soulève certaines questions concernant l’adhérence de la sous-couche de Zn sur sa surface. Les surfaces des substrats métalliques à revêtir sont habituellement sablées afin de créer une accroche aux particules incidentes et assurer l’adhérence finale du revêtement. Également, la préparation de surface par texturation laser en remplacement du sablage peut être une alternative. La création de motifs aux géométries contrôlées en surface a démontré la possibilité d’obtenir des adhérences supérieures au sablage en fonction des couples matériaux substrat/revêtement mis en jeu. Le laser permet aussi de préparer des surfaces de matériaux de haute dureté comme les céramiques qui ne peuvent être rendues rugueuses par sablage[10]. Dans le cas des thermoplastiques, le sablage est une méthode agressive susceptible d’éroder le matériau, de le fissurer sous l’impact du corindon, et notamment affectant les structures composites de matrice thermoplastique contenant des tissages de fibres. C’est pour cela que plusieurs types de sablage à différentes pressions et tailles de corindon sont étudiés : par pression (1 et 3 bar) avec des grains F36, 425–600 µm, et dépression (1 et 3 bar) avec des grains F60, 212-300 µm. Outre le sablage, le polissage au papier SiC avec deux gammes d’abrasif (P80 et P220) est testé pour créer une rugosité.
Des poudres de zinc (20-90 µm), de Cr2O3 (15-45 µm) et de NiCr-Cr3C2 (10-38 µm) sont sélectionnées. Le procédé plasma atmosphérique utilisé comporte une torche de type PTF4 (Oerlikon Metco) tandis que le procédé HVOF utilise le pistolet Diamond Jet (Oerlikon Metco) de type « gas fuel » fonctionnant au méthane. Ils sont montés sur un bras de robot IRB 2400 (ABB) afin de permettre la précision et la reproductibilité des trajectoires et des vitesses de projection.
3.2 Optimisation de la sous couche de Zn par projection plasma APS
Le procédé plasma APS est utilisé pour réaliser la sous-couche de zinc du fait du cahier des charges imposant les procédés possédés par l’industriel ; le procédé HVOF étant inadapté pour les matériaux à bas point de fusion. Le zinc ayant une température de fusion de 419 °C, le traitement thermique des particules ne doit pas être trop important pour ne pas vaporiser ce matériau. Habituellement, le procédé arc fil est utilisé pour le zinc. Dans ce cas présent, le plasma qui est approprié aux matériaux à haut point de fusion, comme les céramiques, doit être adapté en termes de paramètres opératoires. Notamment il ne doit pas être trop chaud pour ne pas éviter de vaporiser et oxyder le zinc. Plusieurs réflexions se présentent alors : travailler avec un plasma de faible puissance et/ou limiter le temps de séjour des particules dans le jet thermique. C’est pourquoi différents paramètres sont testés :
• le débit d’argon : qui influence le temps de résidence des particules dans le jet ;
• le débit d’hydrogène : qui influence la conductivité thermique du plasma et donc le transfert de chaleur aux particules ;
• l’intensité du courant : qui influence la puissance du plasma, l’énergie disponible pour fondre les particules ;
• la distance de projection : qui influence le flux de chaleur venant du plasma et reçu par le substrat, mais aussi le temps de vol des particules (vitesse à l’impact et déformation, temps d’oxydation) ;
• l’angle d’injection des particules dans le plasma en sortie de la tuyère de la torche : qui influence la zone atteinte par les particules dans le plasma (zones à gradient de température)
Le tableau 1 présente les paramètres étudiés tandis que la figure 2 montre les substrats composites avant et après projection APS de zinc. L’évolution du choix des paramètres de projection est dictée dans un premier temps par la mesure de l’épaisseur obtenue, essai après essai. C’est un choix acté, car un revêtement épais n’est pas forcément synonyme d’un bon revêtement. Cette épaisseur dépend du rendement de projection (proportion massique des particules injectées dans le plasma par rapport à celles se retrouvant dans la construction du revêtement), de la présence de porosités, de croissances d’oxydes.
Les microstructures des revêtements sont présentées sur la figure 3. Les modifications des paramètres sont indiquées entre chaque cliché. Le revêtement 1 est le premier obtenu. Comme évoqué prudemment, une forte épaisseur ne coïncide pas forcément avec une bonne qualité de revêtement. Le revêtement 1, le plus épais (comparé à 2 à 6), se caractérise par de nombreux oxydes et porosités. En revanche, le revêtement 2 de plus faible épaisseur est le moins oxydé, par la baisse du débit d’hydrogène et une accélération du plasma par le débit d’argon. En augmentant le courant (2→3), l’oxydation augmente, et inversement si le courant baisse (1→5). L’oxydation diminue également en augmentant l’argon (1→4). La diminution de la distance de projection réduit l’oxydation (1→7), avec moins de temps d’échange/réactivité avec l’oxygène de l’air dans l’environnement du jet de particules. L’augmentation de l’angle d’injection des particules diminue les oxydes également (1→8), avec une injection dans une zone moins chaude du plasma. Enfin, l’augmentation du débit massique de poudre injectée (1→9), par le biais de la vitesse de plateau d’alimentation, augmente de surcroît l’épaisseur, mais diminue l’oxydation (moins d’énergie pour chaque particule, moins de réactivité). Les différents essais menés montrent qu’en diminuant l’intensité du courant et le débit d’hydrogène ou en augmentant le débit d’argon, l’oxydation est diminuée, car les particules sont moins chauffées. D’autres essais ont suivi pour aboutir à un revêtement de zinc faiblement oxydé et dense (cf. Figure 3-b).
Par suite de ces observations, les revêtements 1 et 2 sont choisis pour effectuer des tests d’adhérence et observer une éventuelle influence de la microstructure du revêtement sur l’accroche à l’interface (avant optimisation finale du revêtement de zinc postérieure). Dans les deux cas, la sous-couche est réalisée sur des substrats de différentes préparations (brute, rayée, sablée). Les essais d’adhérence sont faits avec le dispositif PAThandy (DFD® INSTRUMENTS). Des pions de tractions sont collés à la surface des sous-couches (cf. figure 4). La tête du dispositif est ensuite clipsée sur le pion. Avec une manivelle, une pression est exercée sur les pieds de la tête pour tirer le pion. La valeur de la force d’arrachement est lue directement sur le cadran. Les valeurs d’adhérence atteignent 7 MPa. Il y a peu d’influence de la microstructure sur les valeurs pour une même préparation de surface des substrats. En revanche, l’état de surface du composite doit être intermédiaire : ni brut (a) car surface trop lisse, ni trop dégradé (g) car les fibres deviennent trop apparentes et endommagées. Un sablage par dépression, préparation plus douce que par pression, avec une pression de 3 bar est actée.
3.3 Adaptation de la projection aux revêtements finaux de Cr2O3 par projection plasma APS et Cr3C2-NiCr par HVOF
Association de la sous-couche de zinc avec un revêtement Cr2O3 par APS
La sous-couche ayant été optimisée, la réalisation du revêtement fonctionnel peut être réalisée. Les paramètres importants vont être :
• l’épaisseur de la sous-couche de zinc nécessaire à protéger le substrat : gradient thermique dans la sous-couche ;
• la cinématique de projection : vitesse de balayage de la torche plasma, fréquence de passage qui dictent le flux thermique soumis au substrat ;
• le débit massique de poudre céramique : chaleur transmise par le refroidissement des particules en fusion à l’impact.
Si le flux thermique (par convection/conduction) est trop important à la surface de la sous-couche de Zn puis par conduction thermique à la surface du substrat, le thermoplastique va se dégrader et la sous-couche va se désolidariser de l’interface. La première étape consiste en la réalisation des sous-couches de zinc sur des substrats (cf. figure 5). Des épaisseurs de 50 à 130 µm sont préparées avant la projection paramétrique de l’oxyde de chrome.
Le tableau 2 présente les différents essais menés avec l’oxyde de chrome. Les paramètres opératoires étudiés sont la vitesse de translation de la torche plasma projetant l’oxyde de chrome, la vitesse d’alimentation en poudre (débit massique) et l’épaisseur de la sous-couche de zinc, le nombre de passes réalisées. Tout d’abord, 4 passes de revêtements Cr2O3 sont effectuées sur un substrat revêtu de 50 µm de Zn(1). Un faible débit massique de poudre (vitesse plateau de 5 %) est choisi pour ne pas transmettre trop de chaleur à l’ensemble substrat/sous-couche. Mais le revêtement s’est détaché (cf. figure 6 - 1). La chaleur transmise au revêtement de Zn, puis à la surface du substrat, a fragilisé l’interface (détérioration du thermoplastique) : à cause d’un flux de chaleur du plasma trop important (vitesse de projection trop lente) et/ou par une protection insuffisante (épaisseur de Zn trop faible) pour résister à ce flux de chaleur et aussi au gradient thermique du au refroidissement des particules fondues de Cr2O3. Ensuite un deuxième essai avec seulement 2 passes est réalisé. Une détérioration est à nouveau observée sur certaines zones, mais d’autres sont intactes comme le montre la figure 6-2. Le troisième essai se caractérise par une seule passe effectuée mais avec 4 fois plus de poudre injectée. Par rapport au premier essai, la même quantité de Cr2O3 est projetée sur la sous-couche (4 passes à vitesse plateau de 5 % contre 1 passe à vitesse plateau de 20 %). À nouveau le revêtement est dégradé. L’épaisseur de la sous-couche est donc en cause. Alors, des sous-couches de Zn, plus épaisses de 90 et 130 µm, sont testées pour protéger davantage l’interface en atténuant le gradient thermique (flux plasma + refroidissement des particules) lors de la réalisation du revêtement céramique. Également, la vitesse de projection est augmentée à 800 mm/s. Des revêtements de 2 puis 4 passes (essais 4 et 5 respectivement) sur une sous-couche de Zn de 90 µm, puis 10 passes (essai 6) sur 130 µm de Zn sont réalisés. Le résultat donne dans les 3 cas une conservation de l’intégrité des revêtements sur l’ensemble de la surface des substrats recouverts. Les observations de la section de ces revêtements montrent une parfaite cohésion à l’interface. La sous-couche est toujours bien adhérente au composite. La cinématique de projection est ensuite affinée afin de réaliser des revêtements Cr2O3 plus épais afin de convenir à l’application industrielle cible comme le présente la Figure 7.
Association de la sous-couche de zinc avec un revêtement NiCr-Cr3C2 par HVOF
La même démarche est ensuite appliquée pour le second procédé de projection à utiliser pour revêtir le substrat. Il s’agit du procédé HVOF associé au matériau NiCr-Cr2C3 (cf. figure 8). Pour donner suite aux essais précédents, une épaisseur de sous-couche Zn de 100 µm est choisie (cf. tableau 3). La vitesse de projection de 800 mm/s est conservée. Un premier essai est mené avec 35 passages de la torche devant le substrat revêtu de Zn (A). Le revêtement obtenu est intact ; ce qui montre que cette épaisseur est suffisante cette fois-ci pour le procédé HVOF (cf. figure 9). Un deuxième essai identique confirme le résultat précédent (B). Afin de se rapprocher des conditions de travail de l’industriel sur ses pièces, la vitesse de projection est augmentée à 1,5 m/s. En augmentant le nombre de passes à 70, le revêtement de NiCr-Cr3C2 croit en épaisseur (C). Puis en doublant et quintuplant encore le nombre de passes (D puis E), le revêtement atteint 250 µm sans montrer de détérioration à la fois dans sa microstructure très dense et la cohésion à l’interface avec le substrat. L’adhérence des revêtements est testée toujours avec le dispositif PAThandy. Les valeurs obtenues se positionnent entre 4 à 7 MPa. Il apparaît que la vitesse de projection n’influe pas sur les valeurs d’adhérence. En revanche, l’augmentation de l’épaisseur du revêtement se traduit par une légère diminution de l’adhérence.
Un transfert technologique a été effectué par suite de cette étude pour une application sur site chez l’industriel afin de lancer sa production de pièces. La figure 10 présente un des revêtements issus de leur production. Un choix d’une sous-couche de zinc plus épaisse a été fait (200 µm) sur laquelle la couche fonctionnelle de NiCr-Cr3C2 a été réalisée.
4. Conclusion
Cette étude a permis de réaliser la fonctionnalisation de surface d’un substrat composite de base thermoplastique avec des revêtements de Cr2O3 par projection plasma APS et NiCr-Cr3C2 par projection HVOF. Compte tenu de la sensibilité à la température de ce matériau et de sa faible résistance mécanique à l’impact, une sous-couche de zinc a été préalablement déposée pour servir d’interface entre le substrat et le revêtement final. En effet, dans le cas du dépôt de particules à hautes températures de fusion, accompagnées par le flux de chaleur produit par le jet thermique (plasma ou flamme), une dégradation localisée du substrat polymère peut se produire. Dans ces circonstances, la fabrication d’un revêtement métallique intermédiaire avec des particules à basse température de fusion est nécessaire.
La préparation de surface du composite ne doit pas être trop agressive. Le sablage d’une surface métallique permet de créer facilement de la rugosité. Mais cette technique est plus contraignante pour des substrats thermoplastiques contenant des fibres fragiles et susceptibles de se dégrader sous l’impact des abrasifs. Un sablage par dépression sous une pression de 3 bar a été retenue.
L’utilisation du matériau Zn en tant que sous-couche intermédiaire assure une protection thermique du substrat thermoplastique face au flux thermique du jet et de la chaleur libérée lors du refroidissement des particules chaudes incidentes. La surface du composite n’est pas endommagée lors de la projection de zinc par plasma APS. Lors de la réalisation des couches fonctionnelles, une épaisseur de Zn de 100 µm permet de construire un revêtement épais de Cr2O3 par projection plasma APS et NiCr-Cr3C2 par projection HVOF. Un transfert technologique a ainsi été effectué chez l’industriel pour mettre en place ces procédures de fonctionnalisation de surface d’un thermoplastique.
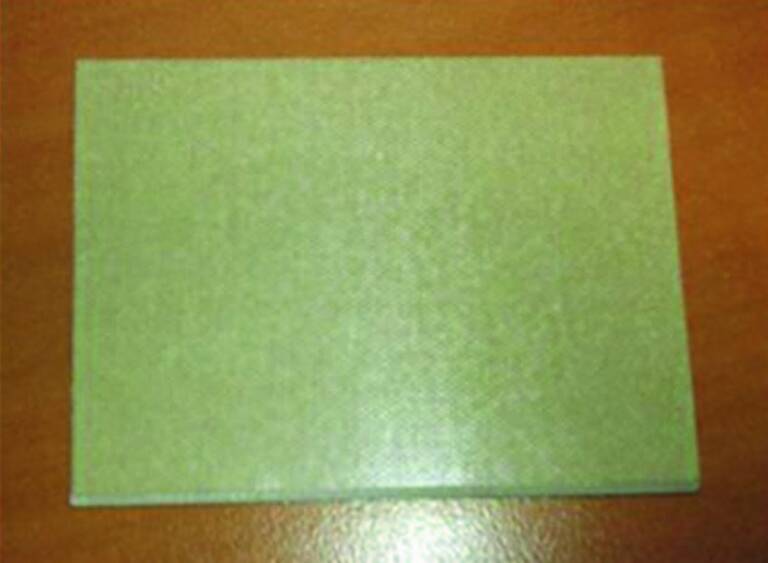
Figure 1. Substrat thermoplastique
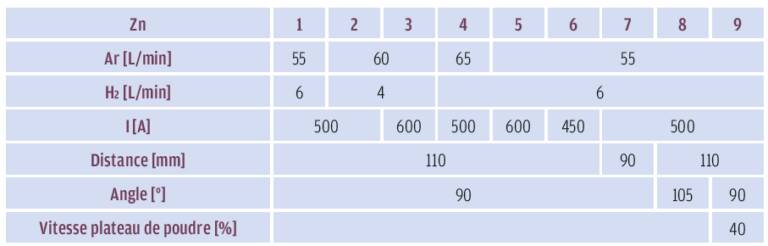
Tableau 1. Paramètres de projection de Zn par APS
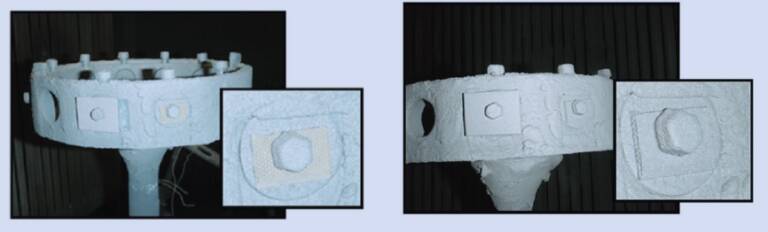
Figure 2. Substrats composites avant et après projection de Zn par APS
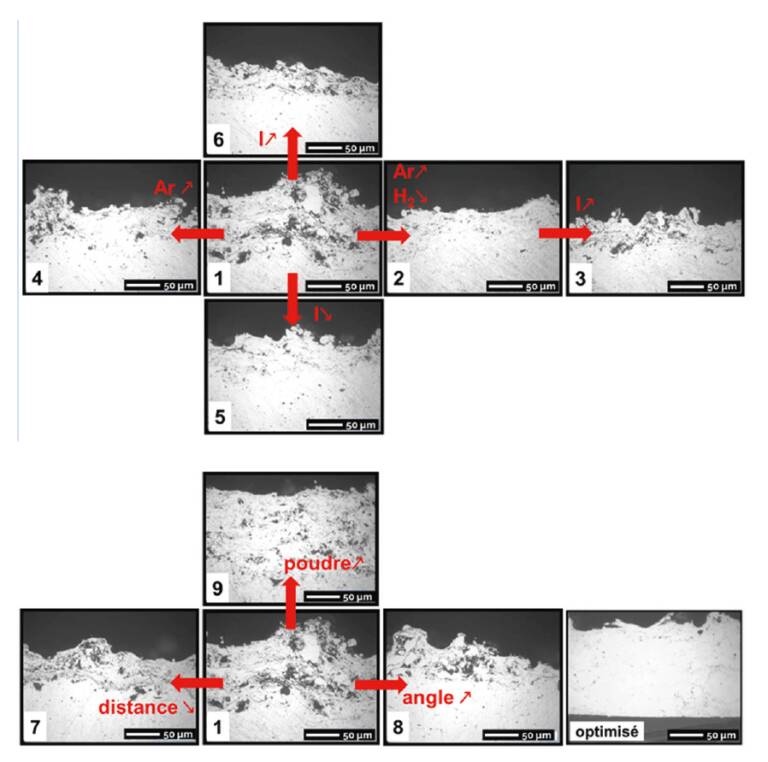
Figure 3. Étude paramétrique de l’élaboration de la sous-couche de Zn par projection plasma APS :
a) influence des gaz plasmagènes et de l’intensité du courant,
b) influence de la distance de projection, de l’angle d’injection et du débit massique de poudre ; revêtement final optimisé
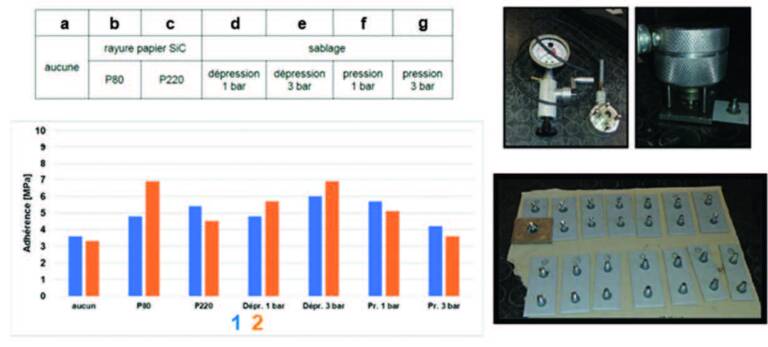
Figure 4. Étude paramétrique de l’adhérence de la sous couche de Zn sur le substrat composite
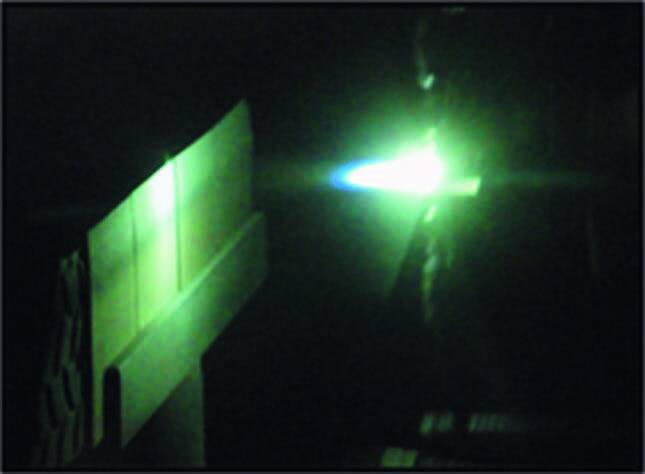
Figure 5. Projection APS des sous couches de Zn avant la fonctionnalisation par Cr2O3
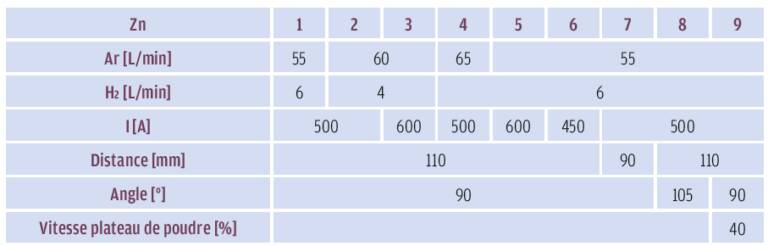
Tableau 2. Paramètres opératoires de l’étude de la faisabilité du revêtement Cr2O32 sur le substrat composite préalablement revêtu de la sous couche de Zn
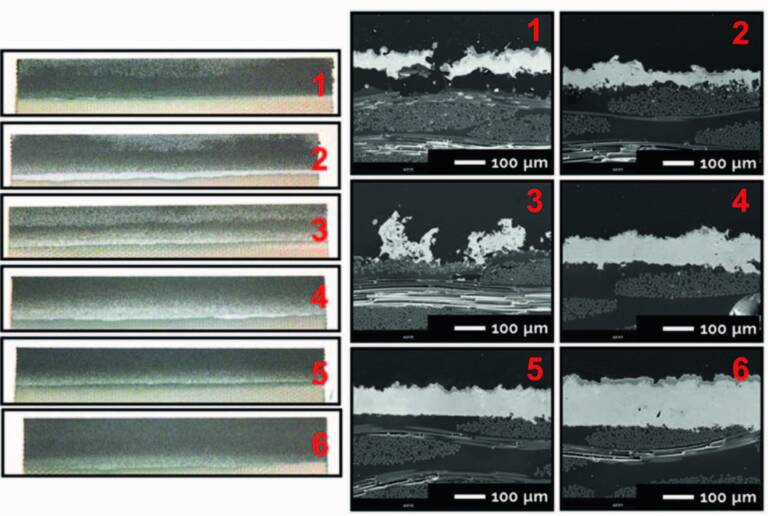
Figure 6. Étude de l’épaisseur de la sous-couche de Zn pour adapter la construction de la couche fonctionnelle Cr2O3
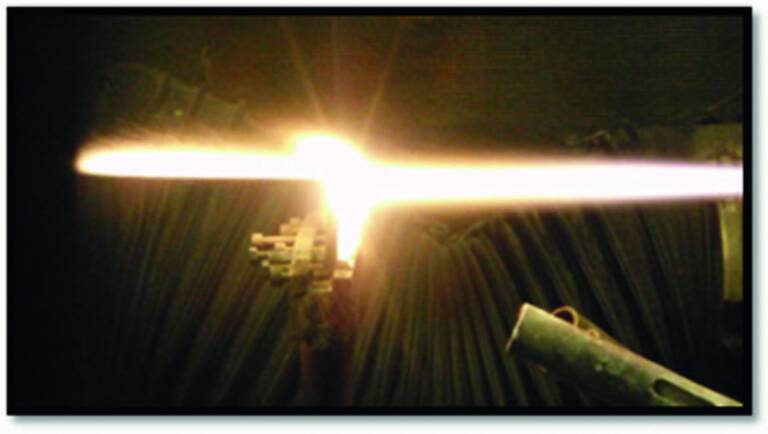
Figure 8. Projection HVOF des couches fonctionnelles de NiCr-Cr3C2
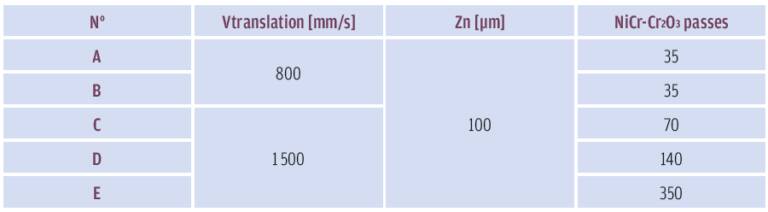
Tableau 3. Paramètres opératoires pour étudier la faisabilité du revêtement NiCr-Cr3C2 sur le substrat composite préalablement revêtu de la sous-couche de Zn
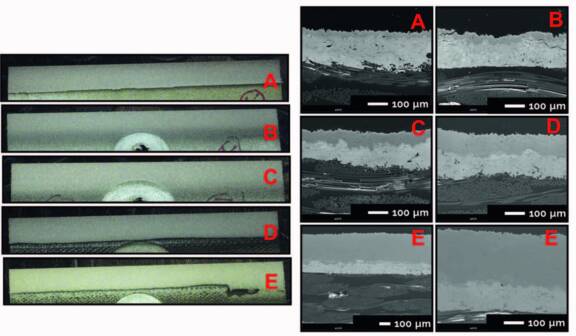
Figure 9. Étude de l’épaisseur de la couche fonctionnelle NiCr-Cr3C2
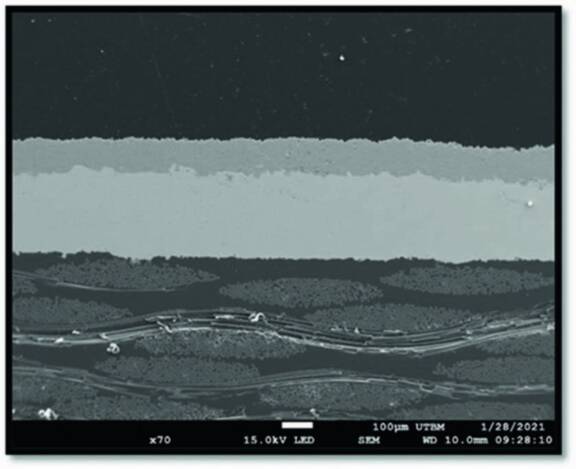
Figure 10. Revêtement HVOF NiCr-Cr3C2 réalisé par l’industriel à la suite du transfert technologique
Bibliographie
[1] M. Liu, Y. Guo, J. Wang, and M. Yergin, Corrosion Avoidance in Lightweight Materials for Automotive Applications, Npj Mater. Degrad., Nature Publishing Group, 2018, 2(1), p 1–4.
[2] R. Gonzalez, H. Ashrafizadeh, A. Lopera, P. Mertiny, and A. McDonald, A Review of Thermal Spray Metallization of Polymer-Based Structures, J. Therm. Spray Technol., 2016, 25(5), p 897–919.
[3] K. Bobzin, W. Wietheger, and M.A. Knoch, Development of Thermal Spray Processes for Depositing Coatings on Thermoplastics, J. Therm. Spray Technol., 2021, 30(1), p 157–167.
[4] R. Melentiev, A. Yudhanto, R. Tao, T. Vuchkov, and G. Lubineau, Metallization of Polymers and Composites: State-of-the-Art Approaches, Mater. Des., 2022, 221,
p 110958.
[5] H. Che, P. Vo, and S. Yue, Metallization of Carbon Fibre Reinforced Polymers by Cold Spray, Surf. Coat. Technol., 2017, 313, p 236–247.
[6] A. Liu, M. Guo, J. Gao, and M. Zhao, Influence of Bond Coat on Shear Adhesion Strength of Erosion and Thermal Resistant Coating for Carbon Fiber Reinforced Thermosetting Polyimide, Surf. Coat. Technol., 2006, 201(6), p 2696–2700.
[7] W. Huang, Y. Zhao, X. Fan, X. Meng, Y. Wang, X. Cai, X. Cao, and Z. Wang, Effect of Bond Coats on Thermal Shock Resistance of Thermal Barrier Coatings Deposited Onto Polymer Matrix Composites Via Air Plasma Spray Process, J. Therm. Spray Technol., 2013, 22(6), p 918–925.
[8] W. Huang, H. Cheng, C. Zhang, Y. Zhou, and X. Cao, Thermal Ablation of Stabilized Zirconia/Metal Coated Polyimide Matrix Composites Via Plasma Spray Process, Plasma Chem. Plasma Process., 2015, 35(4), p 587–603.
[9] W. Huang, X. Fan, Y. Zhao, X. Zhou, X. Meng, Y. Wang, B. Zou, X. Cao, and Z. Wang, Fabrication of Thermal Barrier Coatings onto Polyimide Matrix Composites via Air Plasma Spray Process, Surf. Coat. Technol., 2012, 207, p 421–429.
[10] R. Kromer, S. Costil, C. Verdy, S. Gojon, and H. Liao, Laser Surface Texturing to Enhance Adhesion Bond Strength of Spray Coatings – Cold Spraying, Wire-Arc Spraying, and Atmospheric Plasma Spraying, Surf. Coat. Technol., 2018, 352, p 642–653.