Diverses méthodes d’essais de dureté
Par Julien Berçot, Responsable commercial France Innovatest
Le contrôle et la mesure regroupent de très nombreuses méthodes, que ce soit en contrôle non destructif ou en contrôle destructif. Parmi cela, les essais mécaniques sont essentiels aussi bien en amont pour le développement de nouveaux produits, qu’en contrôle de production ou en expertise dans le cadre d’analyse de défaillance. Le premier des essais mécaniques, le plus important sans doute, est l’essai de dureté. En fonction de la nature des matériaux, de leur dureté attendue, des caractéristiques mécaniques recherchées. Il existe diverses méthodes d’essai de dureté. Chacune de ces méthodes est régie par des normes afin d’encadrer les essais et garantir des résultats à la fois précis, répétables et exploitables.
La notion de dureté remonte au Moyen-Âge. La guerre et la chasse ont largement contribué au développement d’armes en acier, qui devaient être plus dures que la pierre, l’armure ou l’animal chassé.
C’est la minéralogie qui fournit l’échelle de Kvist en 1768 : Diamant 20, Topaze 15, Zéolite 13, Quartz 11, Fluorite 7, Calcite 6, Gypse 5 et Craie 2. Ce n’est qu’en 1822, que F. MOHS fournit une échelle basée sur la résistance à la rayure (tableau 1)
En 1900, le duromètre Brinell a été inventé par Dr. Johan August Brinell.
En 1907, A.F. Shore créé une méthode de mesure de dureté par rebond.
En 1920, S.R. Rockwell développe une méthode avec une force d’essai (Essai Rockwell)
En 1924, Smith and Sandland chez Vickers Ltd développe la méthode Vickers.
En 1926, la première norme ASTM sur la dureté Brinell est publiée.
En 1937, les premiers blocs de référence sont fabriqués en Allemagne et en Suède.
En 1940, première norme DIN sur la dureté Vickers.
En 1975, D. Leeb et M. Brandestini développe une machine de dureté par rebond.
Essais de dureté Vickers (HV)
La force d’essai (de 0,1 gf à 150 kgf) est appliquée sur le matériau avec un pénétrateur diamant à base pyramidale. L’empreinte obtenue est mesurée optiquement pour calculer la valeur de dureté. La méthode d’essai Vickers est la plus précise et est adaptée à tous les matériaux quelle que soit leur dureté (figure 1).
Distance minimale pour les empreintes : (figure 2)
Signification des caractères :
Le 1er chiffre correspond à la valeur de dureté mesurée, le second caractère à l’échelle, le dernier à la charge utilisée en kgf. Par exemple, pour 550HV10 nous avons : 550 Vickers sous 10 kgf :
550HV10
Charge utilisée en kgf
Échelle de dureté
Valeur de dureté mesurée
Essais de dureté Knoop (HK) (figure 3)
Diamant à base pyramidale allongée, dont la grande diagonale est sept fois plus longue que la petite diagonale. Par rapport au Vickers, la grande diagonale est environ trois fois plus longue et l’empreinte obtenue est deux fois moins profonde.
L’essai de dureté Knoop (HK) est une alternative à l’essai Vickers (HV), destiné aux essais de micro-dureté et principalement utilisé pour éviter les fissures dans les matériaux fragiles ainsi que pour faciliter les essais sur les couches et revêtements minces.
Distance minimale pour les empreintes (figure 4) :
Signification des caractères :
Le 1er chiffre correspond à la valeur de dureté mesurée, le second caractère à l’échelle, le dernier à la charge utilisée en kgf.
Par exemple, pour 400HK0,5 nous avons : 400 Knoop sous 500 gf :
400HK0,5
Charge utilisée en kgf
Échelle de dureté
Valeur de dureté mesurée
Essais de dureté Brinell (HBW) (figure 5) :
La méthode d’essai Brinell est la plus ancienne et communément utilisée en fonderie, majoritairement sur les matériaux ductiles et/ou dont la structure métallurgique est hétérogène. Le « billage » se fait aujourd’hui via des billes en carbure de tungstène (HBW) car plus dures qu’en acier (HBS), avec des charges d’essai de 1 à 3000 kgf (HBW1/1 à HBW10/3000). Les diagonales sont ensuite mesurées pour calculer la dureté.
Distance minimale pour les empreintes (figure 6) :
Signification des caractères :
Le premier chiffre correspond à la valeur de dureté, le second à l’échelle avec le type de bille utilisée, le troisième au diamètre de la bille et le dernier à la charge utilisée en kgf.
Par exemple, pour 600 HBW 2,5/31,25 nous avons : 600 Brinell avec bille carbure de tungstène de Ø2,5 mm sous 31,25 kgf :
600 HBW 2,5/31,25
- Charge utilisée
en kgf
- Diamètre de
la bille
- Échelle de dureté
et type de bille
- Valeur de dureté
mesurée
Essais de dureté Rockwell (HR) (figure 7)
Diamant conique d’angle au sommet de 120° ou billes en carbure de tungstène de différents diamètres : 1/16’’, 1/8’’, 1/4’’, ou 1/2’’.
La méthode d’essai Rockwell est la plus utilisée car rapide à mettre en œuvre et s’affranchit de la déformation élastique par la précharge afin de mesurer la déformation plastique du matériau.
La mesure comporte :
1. La mise en contact du pénétrateur à la surface grâce à la précharge avec mise à zéro de l’indicateur de mesure,
2. Application de la charge complémentaire de telle sorte que :
précharge + surcharge = charge totale,
3. Retour à la précharge et lecture de l’enfoncement («t») sur l’indicateur (comparateur ou dispositif numérique).
Signification des caractères :
Le 1er chiffre correspond à la valeur de dureté, le second à l’échelle utilisée.
Par exemple, pour 50 HRC nous avons : 50 Rockwell avec l’échelle C (précharge 10 kgf et charge totale 150 kgf) :
50 HRC
Échelle de dureté
Valeur de dureté mesurée
Essais Jominy
Méthode de détermination de la trempabilité de l’acier par trempe en bout (essai Jominy), à l’aide d’une éprouvette de 25 mm de diamètre et 100 mm de longueur.
Echelles et charges d’essais : HRC ou HV30
La trempabilité d’un alliage ferreux est la profondeur à laquelle un matériau est durci après traitement thermique et est mesurée par l’essai Jominy. Une barre de métal ronde de taille standard est transformée en 100 % d’austénite par traitement thermique.
Elle est ensuite refroidie à une extrémité avec de l’eau à température ambiante. La vitesse de refroidissement sera la plus élevée au niveau de l’eau et diminuera à mesure que la distance de ce point augmente. (Cf. figures 8 et 9, page suivante)
Après le refroidissement, une surface plane est rectifiée sur l’éprouvette et la trempabilité est déterminée en mesurant la dureté le long du barreau. La dureté est plus élevée au niveau de l’extrémité trempée que l’autre extrémité. Plus la dureté élevée est étendue loin de l’extrémité trempée, plus la trempabilité du matériau est élevée. Cette information est tracée sur un graphique de trempabilité.
(Cf. figures 10 et 11)
Mesure de la ténacité KIC
Pour en savoir plus sur le comportement des matériaux, en particulier en matière de fissure et de fatigue, la croissance de la fissure peut être prédite et mesurée. Les deux méthodes sont la fissure de type Palmqvist ou Médian / Radial.
Le procédé Palmqvist (ou test de ténacité Palmqvist) est une méthode courante pour déterminer la ténacité à la rupture des matériaux fragiles dont la rupture brutale se produit sans déformation plastique préalable lors d’essais de traction ou de compression (carbures cémentés, céramiques, verre, et les matériaux amorphes tels que les verres métalliques). Dans ce cas, la ténacité à la rupture des matériaux est représentée par le facteur d’intensité de contrainte critique KIC.
La méthode Palmqvist utilise les longueurs des fissures à partir d’une indentation Vickers pour déterminer la ténacité à la rupture. Le facteur d’intensité de contrainte critique est alors donné par la formule suivante :
Exemple d’empreinte Vickers avec mesure des longueurs de fissures (figure 12)
Évaluation de l’adhérence des revêtements céramiques
Méthode
La qualité de l’adhérence de revêtements céramiques jusqu’à 20 μm d’épaisseur est évaluée par indentation à l’aide d’un pénétrateur Rockwell cône diamant 120° (HRC, HRD ou HRA).
La formation de fissures après l’indentation peut également révéler une rupture cohésive. Les indentations sont réalisées à l’aide d’un instrument d’essai de dureté Rockwell (conforme aux normes ISO 6508-1 & ISO 6508-2).
L’essai n’est pas adapté aux revêtements élastiques sur des substrats durs. Une indentation est réalisée sur la surface revêtue de l’éprouvette à soumettre à essai de façon à ce que le revêtement au voisinage de l’indentation puisse être endommagé. L’empreinte laissée et la zone qui l’entoure sont examinées au microscope optique afin de détecter des fissures et/ou un écaillage.
(Cf. figures 13, 14,15 et tableau 2)
Vérification directe et indirecte
L’étalonnage et la calibration sont essentiels quant au bon fonctionnement d’un duromètre. Pour être fait conformément aux normes ISO et ASTM, il est nécessaire de procéder à une vérification directe et indirecte de la machine pour sa certification.
Principaux contrôles réalisés
La vérification directe vise à contrôler les paramètres liés aux fonctions de la machine (force appliquée, pénétrateur certifié de moins de 2 ans ou mesurage) après une première mise en service ou à la suite d’une intervention dans le circuit optique et/ou d’application de charge.
La vérification directe contrôle principalement :
- La force appliquée
- Les temps d’application de charge
- L’étalonnage des objectifs (sauf Rockwell)
- L’enfoncement du pénétrateur
et de l’hystérésis (Rockwell)
La vérification indirecte utilise des blocs étalon pour contrôler chaque échelle d’essai et peut être utilisée seule pour une vérification périodique de routine de la machine en service.
La vérification indirecte se fait principalement par :
- Tests sur des cales de dureté différentes par échelles
- Contrôle du niveau de la machine
- Vérification des empreintes de référence
- Mesure des diagonales (l’écart doit être inférieur à 5 %)
- Mesure des ½ diagonales (l’écart doit être inférieur à 5 % en Vickers et 10 % en Knoop)
Intérêt
Une machine certifiée permet de s’assurer que les essais réalisés sont conformes aux normes en vigueur avec des résultats fiables et répétables. Seuls les organismes accrédités (Cofrac, Ukas, DaKKs ou RvA) selon la norme ISO/IEC 17025 peuvent garantir que l’appareil d’essai de dureté est conforme aux standards.
Traitements thermiques
Le traitement thermique est un procédé permettant de modifier les propriétés physiques et chimiques des aciers. La première étape est une montée en température, puis un maintien avant un refroidissement lent ou rapide. La transformation de la structure de l’acier dans la masse ou en surface augmente la résistance à la rupture, la limite élastique, la ductilité et diminuent la fragilité d’un acier en supprimant les contraintes internes.
Trempe et revenu
La trempe est un traitement thermique qui transforme l’austénite de l’acier en martensite. Le but est d’utiliser le diagramme Fer-Carbone pour se placer dans le domaine austénitique. Ce diagramme permet de déterminer la température d’un traitement pour faire des transformations de phase. (Cf. figure 16)
L’opération de chauffe est suivie d’un refroidissement rapide (eau, huile ou gaz). Le diagramme TRC (transformation à refroidissement continu), permet de définir les conditions de refroidissements qui vont transformer l’austénite en martensite. Ce type de diagramme est propre à chaque nuance d’acier.
Le revenu est un traitement thermique après trempe pour libérer les contraintes présentes dans le matériau. Ce revenu va permettre d’ajuster la ductilité et la limite d’élasticité.
Trempe par induction
Le principe de la trempe par induction consiste à chauffer très rapidement et localement la pièce de façon superficielle pour que le métal soit dans un état austénitique et lors du refroidissement rapide, se transforme en martensite.
Un courant de moyenne ou haute fréquence parcourt la bobine de cuivre et induit un champ magnétique alternatif sur la pièce et va donc dissiper sa chaleur dans la pièce. Cette étape est suivie d’un refroidissement avec un fluide de trempe. L’opération de refroidissement peut être effectuée après le chauffage (trempe statique) ou bien à la suite du chauffage (on parle alors de trempe au défilé).
Avec cette technique, il est possible d’obtenir des zones superficielles traitées d’une profondeur de 0,5 mm à 5 mm. Ce traitement est adapté pour les pièces qui sont sollicitées en torsion et pour résister aux chocs. C’est un traitement qui se fait unitairement, contrairement à la cémentation qui peut se faire sur plusieurs pièces à la fois.
Cémentation (Cf. figure 17)
La cémentation est un traitement thermochimique. C’est-à-dire que le traitement va avoir lieu dans un milieu qui va créer une modification de la composition du métal de base après échange avec le milieu. Dans le cas présent, la cémentation est la diffusion du carbone dans la couche superficielle de l’acier.
Plusieurs procédés existent (cémentation en caisse, liquide ou gazeuse). C’est la cémentation en phase gazeuse qui est la plus utilisée aujourd’hui. C’est une atmosphère riche en carbone (à partir de gaz type CH4, propane ou butane) qui va enrichir la couche superficielle.
Elle s’effectue sur des aciers à bas carbone et permet d’enrichir superficiellement l’acier jusqu’à 0,6 à 0,9 % de carbone. Ce traitement thermochimique est suivi d’un refroidissement rapide qui donne le durcissement à la couche enrichie.
La profondeur de cémentation (CHD – Case Hardness Depth) est déterminée par la distance à la verticale de la surface vers la couche à une limite de dureté (usuellement à 550 HV). Elle varie généralement entre 0,5 mm à 3 mm.
Nitruration (Cf. figure 18)
La nitruration est un traitement thermochimique également. C’est donc la diffusion de l’azote en surface d’un acier allié (qui contient du chrome, de l’aluminium, tungstène…). Elle s’effectue généralement à une température entre 500 et 550 °C.
La nitruration se compose de deux couches :
• La couche de combinaison (« couche blanche ») : couche de nitrure en surface qui est constituée des composés chimiques présents dans l’atmosphère de traitement et du métal de base. L’épaisseur peut varier de 5 à 30 μm. Cette couche a une résistance à l’usure très élevée. Sa dureté va généralement de 950 à 1 100 HV.
• La couche de diffusion : Des nitrures des éléments alliés précipitent sous forme de particule fine et résistante. Cette couche peut varier de 0,05 à 0,8 mm d’épaisseur. Sa dureté peut varier de 400 à 1 200 HV selon l’acier utilisé.
Plusieurs procédés de nitruration existent, la nitruration en bain de sels, gazeuse ou encore plasma.
La profondeur de nitruration (NHD) est déterminée par la courbe de dureté selon la norme DIN 50190-3 ou ISO 18203. Après réalisation de trois empreintes de dureté à cœur, la profondeur de nitruration correspond à cette valeur HV cœur + 50 HV.
Carbonitruration
La carbonitruration est aussi un traitement thermochimique. C’est la combinaison du carbone et de l’azote dans l’environnement de traitement qui va donner une couche cémentée plus dure que lors d’une cémentation classique.
Méthode de mesure par essai de dureté
La profondeur de cémentation, la profondeur de nitruration et la profondeur de durcissement superficiel sont déterminées à partir du gradient de dureté dans une section transversale perpendiculairement à la surface.
Elles sont déduites graphiquement à partir d’une courbe représentant la variation de la dureté en fonction de la distance à la surface d’une pièce. L’épaisseur totale de la couche superficielle durcie est déterminée à partir de la variation de la structure observée par méthode micrographique ou par mesure de la variation de la dureté.
L’épaisseur de la couche composite est déterminée à partir de la couche de composé chimique observée par la méthode par coupe micrographique.
Réaliser des empreintes de dureté le long d’une ou plusieurs droites parallèles perpendiculairement à la surface et à l’intérieur d’une bande de largeur de 1,5 mm. (Cf. figure 19)
La distance séparant deux empreintes adjacentes ne doit pas être inférieure à 3 fois leur diagonale. La différence entre les distances successives entre empreintes à partir de la surface ne doit pas dépasser 0,1 mm et les distances cumulées à partir de la surface doivent être mesurées avec une exactitude de +- 25 µm. Les diagonales de l’empreinte doivent être mesurées avec l’exactitude spécifiée dans l’ISO 6507-2. Le centre de la 1ère impression doit être à une distance d1 de la surface d’au moins 2,5 fois sa diagonale.
Les essais au moyen d’empreintes Vickers ou Knoop sont réalisées pour des forces de 100 g à 1 kg (0,9807 N à 9,807 N). Les mesures des empreintes doivent être réalisées avec un éclairage approprié et un grossissement où les diagonales représentent entre 25 % et 75 % de l’oculaire ou de la largeur ou hauteur de l’écran, et que les contours de l’empreinte puissent être mis au point sans distorsion.
Contrôle de dureté des soudures
Le contrôle macroscopique et microscopique d’une soudure permet de connaître les longueurs du cordon, la profondeur de pénétration, la structure du matériau. Les duretés effectuées à des endroits précis de la soudure aident à déterminer la résistance mécanique de l’ensemble soudé.
(Cf. figure 20)
Les empreintes par série de trois, se situeront dans la zone fondue, dans les zones affectées thermiquement (ZAT) et dans le métal de base, à une distance du bord de pièce ≤ à 2 mm. Le nombre et l’espacement des empreintes doivent être suffisants pour définir les zones durcies ou adoucies par suite du soudage.
Pour les métaux qui durcissent en zone affectée thermiquement (ZAT) par suite du soudage, deux empreintes supplémentaires en zone affectée thermiquement doivent être réalisées à une distance ≤ 0,5 mm entre le centre des empreintes et la zone de liaison.
Normes
Les essais de dureté sur soudures sont régis par notamment par la norme ISO 9015 « essais destructifs des soudures sur matériaux métalliques - essai de dureté ».
La partie 1 : « essai de dureté des assemblages soudés à l’arc » spécifie les essais de dureté sur les assemblages soudés à l’arc de matériaux métalliques (hors aciers inoxydables), normalement sous des charges d’essai Vickers HV5 ou HV10 (49,03 N ou 98,07 N) ou Brinell HBW2,5/15,625 ou HBW1/2,5.
La partie 2 : « essai de microdureté des assemblages soudés » spécifie les essais de microdureté sur les assemblages soudés de matériaux métalliques à forts gradients de dureté, normalement sous des charges d’essai comprises entre HV0,1 et HV5 (0,98≤N à moins de 49≤N).
Duromètres à cellule de force
(Cf. figure 20)
Les appareils de dureté équipés de cellules de force sont de plus en plus répandus, l’expérience liée aux essais mécaniques a démontré que la fiabilité des résultats obtenus était meilleure qu’avec les masses mortes. Outre le fait d’avoir des plages de charges beaucoup plus étendues et donc de rendre ces appareils plus polyvalents, le principal intérêt est la maîtrise de l’application de la charge pour éviter les phénomènes de dépassement de charge, appelés « over-shoot ».
Exemple d’un duromètre (Cf. figure 21)
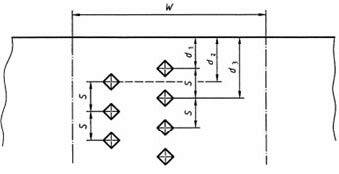
Figure 19
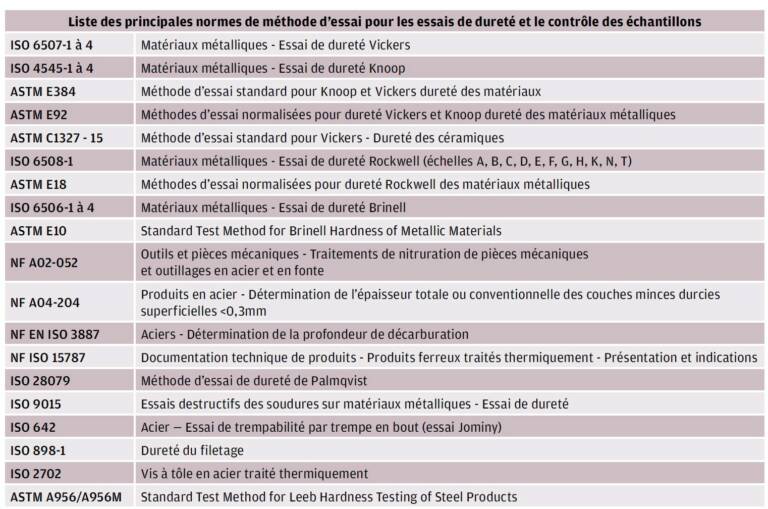
Tableau 3
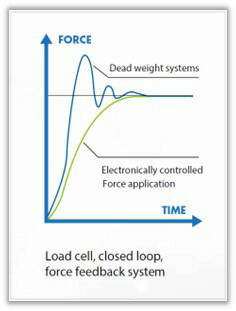
Figure 22
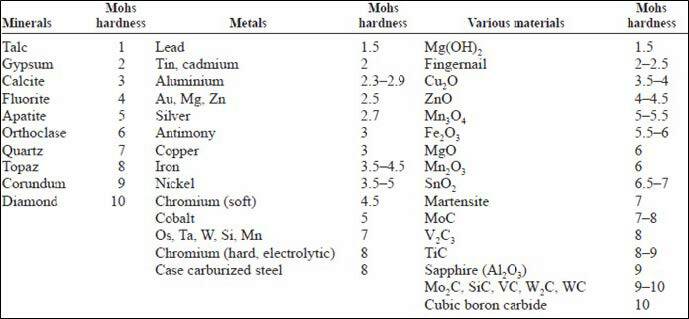
Tableau 1
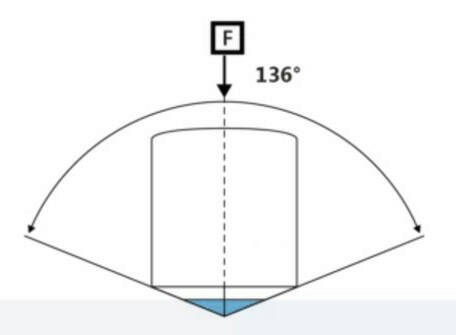
Figure 1
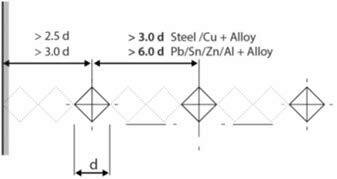
Figure 2
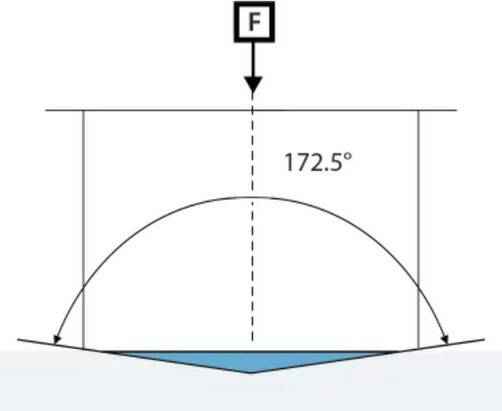
Figure 3
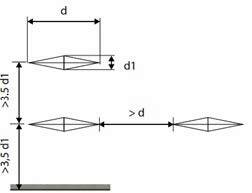
Figure 4
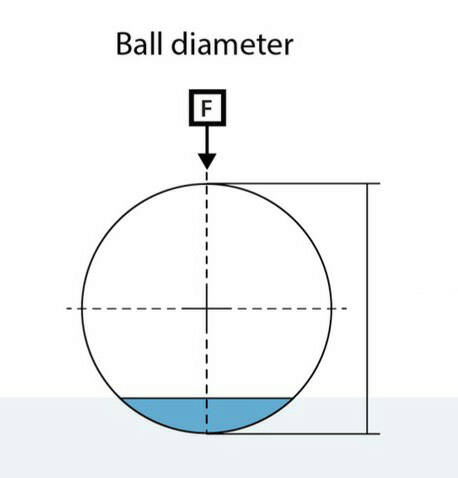
Figure 5
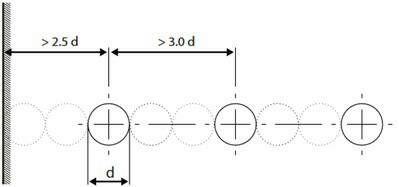
Figure 7
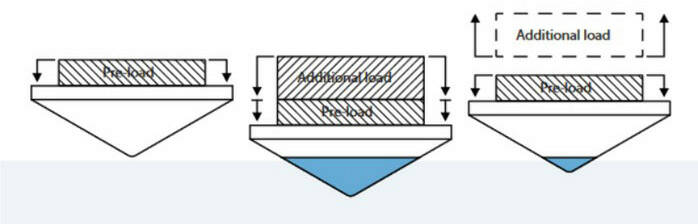
Figure 8
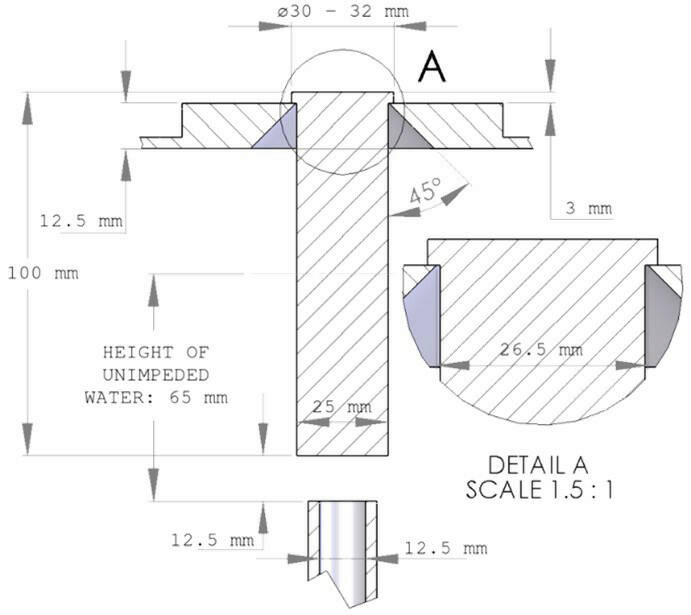
Figure 8 Dimensions de l’éprouvette Jominy
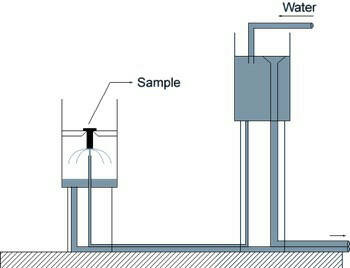
Figure 9 Schéma de l’appareillage Jominy

Figure 10 Éprouvette Jominy après rectification etmesure de la dureté
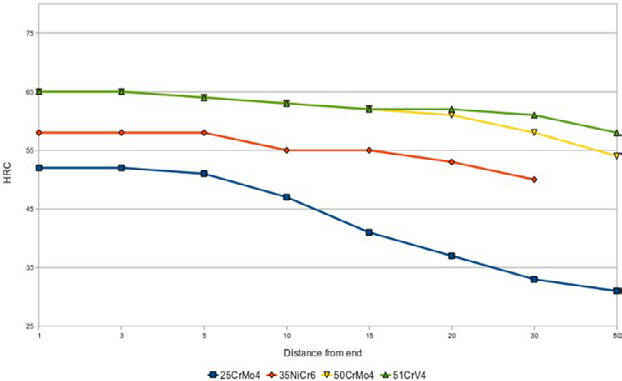
Figure 11 Exemple d’un graphique de trempabilité
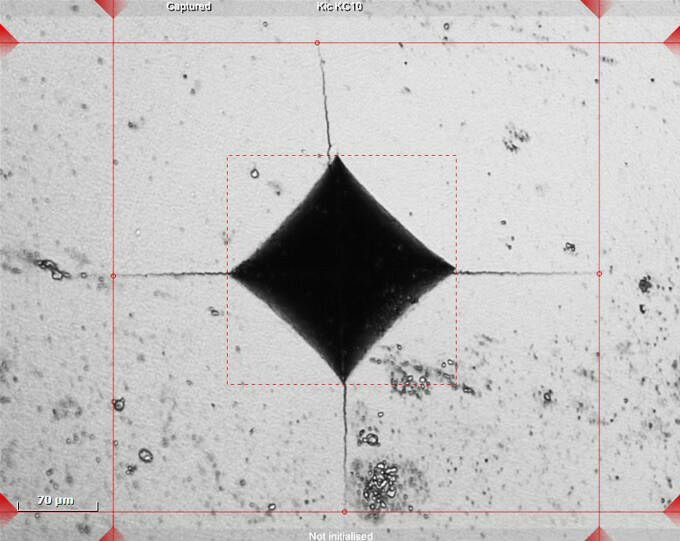
Figure 12
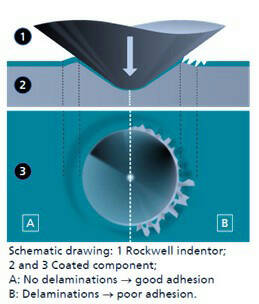
Figure 13
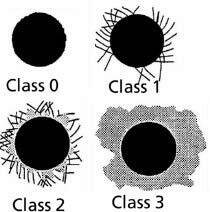
Figure 14 ISO 26443
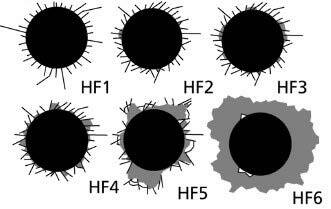
Figure 15 ISO 4856
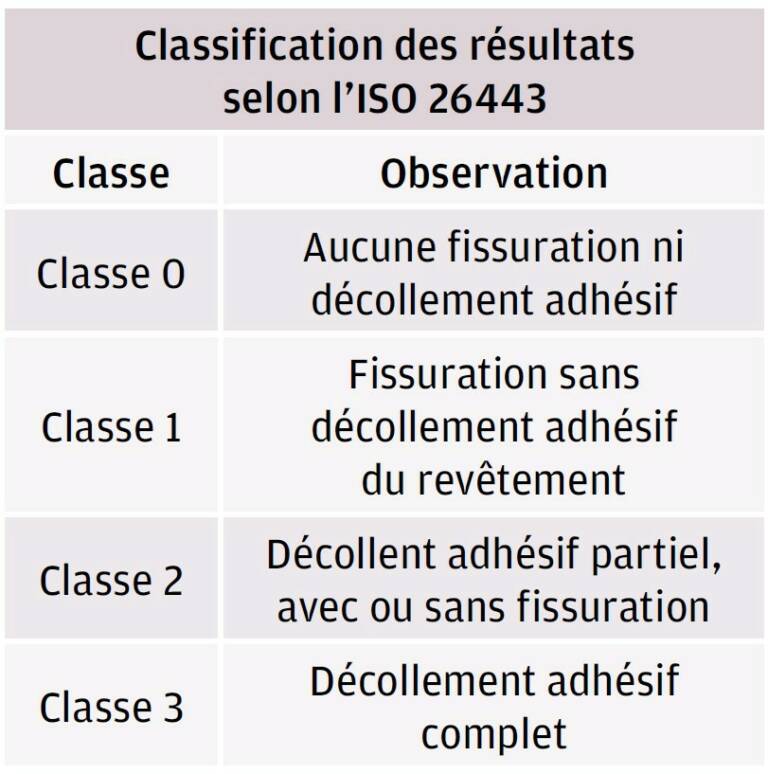
Tableau 2
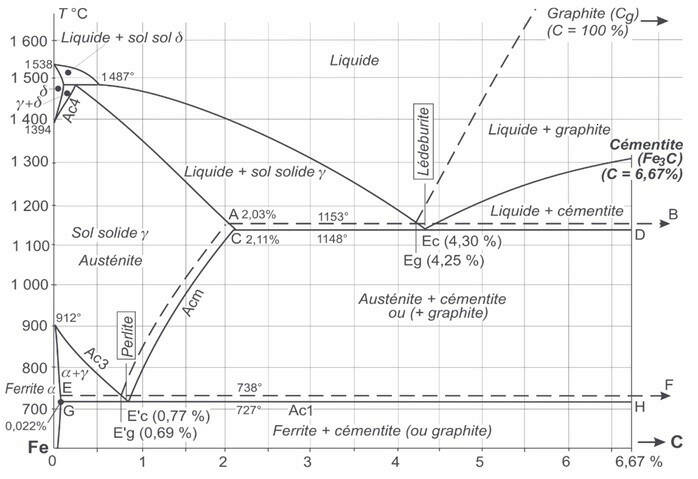
Figure 16

Figure 17
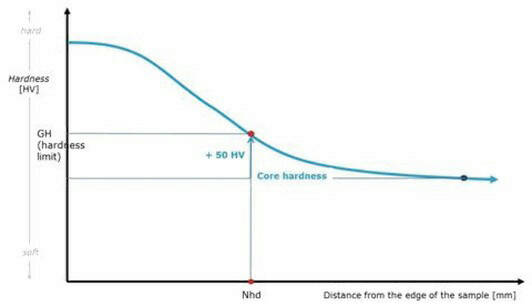
Figure 18
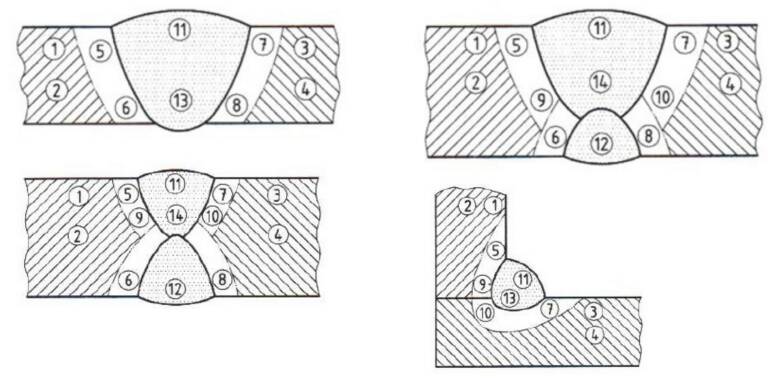
Figure 20. 1 à 4 : Métal de base
5 à 10 : Zone affectée thermiquement (ZAT). 11 à 14 : Zone fondue
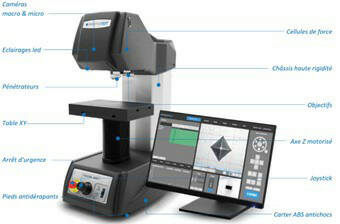
Figure 21