Cold spray, l’outil industriel du futur (3/3)
Par Maurice Ducos, consultant Conseil Mornas Franc
Ce troisième et dernier volet, d’une série consacrée à ce procédé, traite des propriétés et classes d’application du procédé. La projection dynamique par gaz froid s’utilise, de plus en plus, dans de nombreux secteurs de l’industrie, grâce à sa capacité à déposer des poudres, le plus souvent métalliques, à haute vitesse (largement supersonique, en général), pour former des revêtements.
7 Autres propriétés (anti-corrosion, anti-usure)
Pour les deux propriétés, anti-corrosion et anti-usure, les paramètres d’influence prépondérants sont la rugosité superficielle et la porosité du dépôt. Comme il s’agit des deux paramètres majeurs de signature du procédé cold spray, leur connaissance par analyse préalable des dépôts est primordiale pour l’interprétation des résultats d’essais de corrosion ou d’usure.
Pour ce qui est de la corrosion, les essais de corrosion classiques, par exemple ceux (par voie humide) de polarisation et d’immersion dans différents milieux et celui (par voie sèche) de brouillard salin, sont appliqués aux pièces revêtues par cold spray et/ou sur éprouvettes dans le dépôt s’il est question de caractériser certains mécanismes relevant seuls de lui. Si le dépôt est maintenu sur l’éprouvette, il est utile, parfois, de protéger l’interface substrat-revêtement par un vernis, par exemple, pour empêcher une attaque préférentielle par les côtés et laisser significatifs les mécanismes de dégradation par la surface.
Moyennant cela, un processus caractéristique de dégradation de dépôt cold spray se déroule en deux étapes comme peut le révéler un essai d’immersion (éventuellement alternée) dans une solution alcaline : corrosion caverneuse à la surface du dépôt, favorisée par la rugosité, avec formation éventuelle d’oxydes suivie de la pénétration des agents corrosifs dans le dépôt via la porosité débouchant à la surface, cette dernière pouvant n’être constituée que de micro(nano)canaux aux anciens joints de particules. Ces deux étapes sont donc liées respectivement aux deux paramètres clés, déjà évoqués, que sont la rugosité et la porosité. La corrosion caverneuse conduit au « pelage » du dépôt par détachement des « splats », tandis que les produits de corrosion remplissant les porosités assurent la formation d’une barrière la ralentissant. En marge de ces deux principaux points, il peut être dit que les particules céramiques susceptibles d’avoir été ajoutées à la poudre de base du dépôt pour en améliorer la densification (Exemple : aluminium et alumine) ne jouent généralement aucun rôle sur la corrosion. En outre, toujours à la marge, de la corrosion par piqûration peut affecter certains « splats » pendant le processus. Ce qui vient d’être dit sur la corrosion a aussi valeur pour les propriétés tribologiques, à savoir, le recours aux essais classiques (qui ne seront pas décrits ici) et le rôle prépondérant de la rugosité et de la porosité du dépôt. On pourra, cependant, y ajouter que les propriétés mécaniques de base (dont elles dépendent aussi d’ailleurs) y ont une influence plus marquée que dans le cas de la corrosion où ce sont les propriétés physico-chimiques qui interviennent surtout. Pour ce qui est du comportement tribologique, le maître-mot est celui de composite. La force du cold spray est de pouvoir produire une palette infinie de microstructures composites grâce aux mélanges maîtrisés possibles entre constituants élémentaires sans risque de déstabilisation compte tenu du caractère « froid » de l’élaboration. Ces mélanges peuvent associer ainsi métaux, polymères, céramiques, lubrifiants solides, et porosité, en considérant cette dernière comme un élément constitutif de la microstructure.
La porosité joue classiquement le rôle de poche à lubrifiant et de piège à débris dans un contact. L’exploitation d’essais tribologiques (de type, par exemple, « pion-disque », « plan-plan », galet-plan », etc.), impliquant des matériaux cold spray, passera donc avantageusement par l’analyse des débris et des tribofilms formés à partir de leurs différents constituants.
8 Applications
Classes d’applications
Les applications du cold spray peuvent être catégorisées par classe en fonction des propriétés des dépôts qui lui sont accessibles du fait des particularités du procédé. Ces applications touchent tous les secteurs de l’industrie. Leur couverture s’est déroulée chronologiquement au fur et à mesure que les familles de matériaux projetables se sont multipliées. Il serait vain de les citer, de même pour les applications associées sachant que le lecteur pourra se reporter à des ouvrages généraux s’y rapportant (cf. § « Bibliographie » de cet article). Certaines parmi les plus emblématiques en seront seulement données ici (figure 30), en un raccourci allant de l’application fondatrice du cold spray industriel, en 2003, jusqu’aux premières pièces obtenues deux décennies plus tard environ, par fabrication additive (industrielle) (figures 30a et 30e, respectivement). Historiquement, la première application industrielle du cold spray portait, logiquement, sur le dépôt du matériau ductile par excellence, à savoir le cuivre, sur une géométrie simple, plane en l’occurrence (figure 30a). Les applications les plus récentes sont associées à des matériaux et des formes beaucoup plus complexes (par exemple, le cadre de vélo en titane réalisé en 25 minutes seulement, figure 30e) grâce au développement du cold spray depuis.
Les applications « intermédiaires » remarquables intéressent l’association de matériaux fortement dissemblables, métal-polymère ou métal-verre/céramique par exemple, qui, pourtant, étaient dites, au début du cold spray, irréalisables via ce procédé (figures 30b et 30d). Le caractère remarquable peut être lié aussi aux conditions d’élaboration. Ainsi, le revêtement en acier ferritique de poêle en aluminium pour chauffage induction montré en figure 30e est-il produit en 2x8 voire en 3x8, montrant ainsi la fiabilité et la robustesse du procédé et des installations.
En regroupant par propriété de dépôt, les principales applications du cold spray, parmi lesquelles se retrouvent celles présentées en figure 30, peuvent être présentées ainsi :
Propriétés électriques et magnétiques : Les jeux de barres (barres omnibus), sous la forme de barres plates ou tubes, bruts ou revêtus, en cuivre ou aluminium, ont constitué des applications privilégiées du cold spray dès son début. Une multitude d’autres applications électriques (et thermiques associées), magnétiques appelant des dépôts de cuivre, aluminium, ou à base d’argent sur différents composants existent aussi : cordons chauffants sur vitre, électrodes y compris sur substrats céramiques, contacteurs, capteurs, radiateurs ou encore casseroles et poêles ;
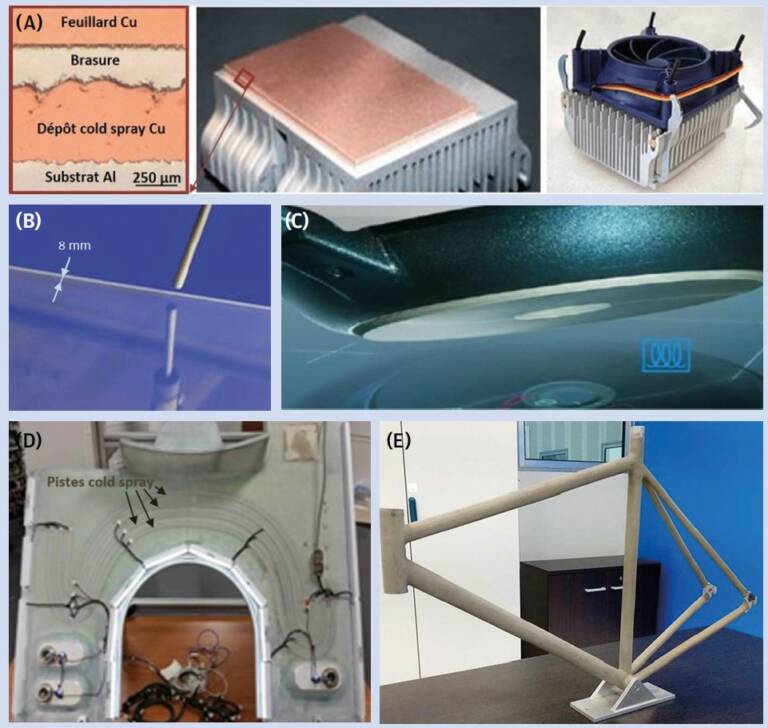
Figure 30 – Applications industrielles du cold spray, a) Plaque de radiateur de ventilateur d’unité centrale (CPU) /coupe micrographique du dépôt cold spray de Cu (à gauche) – radiateur seul (milieu) – ensemble avec ventilateur (à droite) / (doc. Verax P16Cu), b) Cordon d’électrode déposé par cold spray sur vitre (doc. CenterLine Windsor), c) Fond de poêle en acier ferromagnétique déposé par cold spray sur Al (doc. obz innovation gmbh), d) Pistes électriques déposées par cold spray (largeur de piste d’environ 1 cm) sur panneau supérieur en composite d’hélicoptère Super Puma (doc. Airbus Helicopters), e) Cadre de vélo en Ti issu de fabrication additive cold spray (doc. Titomic Ltd).
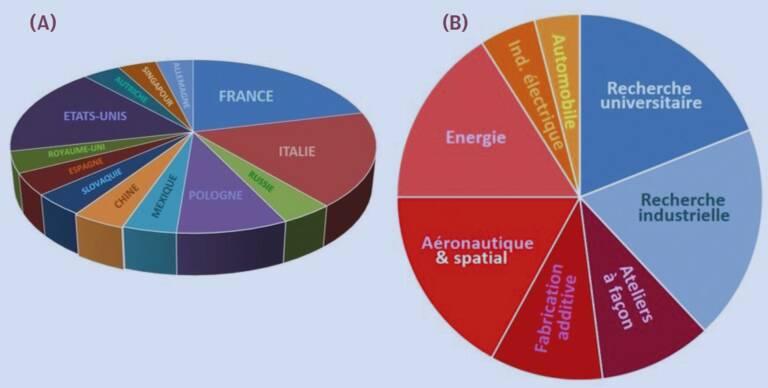
Figure 31 – Répartition des installations cold spray du premier de ses fabricants (Impact Innovations GmbH), a) par pays (données cumulées, actualisées en avril 2020), b), par secteur (situation au 31 déc. 2019) (doc. Impact Innovations).
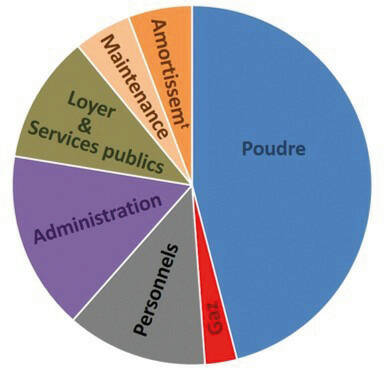
Figure 32
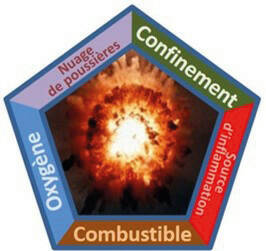
Figure 33 – Triangle et pentagone des risques,
a) de feu, b) d’explosion
Propriétés antimicrobiennes et bactéricides : Les propriétés, en la matière, du cuivre et de composites à matrice ductile (ZnO-Ti, HA-Ag/PEEK) ont incité à les déposer par cold spray pour le revêtement de matériels hospitaliers ou de composants alimentaires ;
Propriétés mécaniques, anti-usure et anti-corrosion : Selon la propriété visée, l’utilisateur exploitera telle ou telle caractéristique du procédé cold spray pour l’exploiter en vue de son application. Pour aboutir aux propriétés mécaniques souhaitées, c’est la possibilité d’emploi du cold spray à une large gamme de matériaux qui sera exploitée : aluminium et cuivre pour les applications déjà citées, en particulier, aciers (toutes pièces mécaniques), superalliages (composants aéronautiques et de turbine terrestre), aciers (automobile, par exemple), NiTi (pièces à mémoire de forme). Pour l’anti-usure, le cold spray sera apprécié pour sa capacité à réaliser du composite (Al, Mg ou Ag renforcés par céramiques voire du graphène, par exemple, pour l’aéronautique, l’automobile, ou l’énergie), l’une des « phases » du composite pouvant être de la porosité résiduelle, volontairement laissée dans ce cas, pour la rétention de lubrifiant (pièces mécaniques) ou l’accrochage des tissus (prothèses). Les matériaux durs anti-usure (stellite et dérivés) sont aussi utilisés. Le caractère anti-corrosion sera favorisé par la haute densification des dépôts cold spray (Zn et ses alliages, Al et ses alliages, Ta, MCrAlY, Ni/Al et NiAl, Ni-XCr, nanocristaux, … pour applications marine, papeterie, pièces d’étanchéité et autres) ;
Métallisation de polymères : La métallisation de polymères (et sur polymères) intéresse toutes les branches de l’industrie, en particulier pour l’allégement des structures dans l’aéronautique et l’automobile surtout, via l’apport d’une propriété superficielle au matériau polymère qu’il ne présente pas : résistance à l’usure/érosion, conductivité électrique, protection anti-foudre, esthétique. Son essor, cependant, n’est que récent ;
Réparation : Le rechargement et la réparation sont parmi les applications les plus porteuses du moment (dans l’aéronautique, en particulier : carters sur moteur d’hélicoptère, pièces de train d’atterrissage d’avion, par exemple), y compris avec usage de dispositifs de projection portatifs (sur piste d’aéroport) ;
Fabrication additive : L’expression « fabrication additive » s’entend ici dans le sens restreint de fabrication directe de pièce puisque, au départ, quel que soit le dépôt, le cold spray est, dans son principe même (apport de matière), de la fabrication additive. Il est certain que, ces dernières années, le cold spray se pose en prétendant sérieux parmi les procédés de fabrication additive dans cette acception. Il s’agit encore, cependant, d’un champ fortement ouvert au développement, faisant suite à de premiers résultats emblématiques relatifs à l’obtention de pièces complexes et/ou pièces hybrides (métal sur céramique). L’effort dans le domaine passe aussi par l’évolution vers de plus petites dimensions, tant pour les systèmes de projection (buses en premier lieu) que pour les dépôts, les deux pouvant être liés. Les perspectives s’y rapportant sont annoncées comme fortes. En 2016, de premiers dépôts dits « minces », c’est-à-dire d’une épaisseur de l’ordre de 14µm, homogènes et denses, ont pu être obtenus avec de l’argent.
Pour l’emploi du cold spray
Compte tenu de sa relative facilité d’installation, par rapport aux autres procédés de projection thermique notamment, le cold spray se répand de plus en plus dans l’industrie, du plus petit atelier à façon jusqu’au site de production de grand groupe, tout en restant fortement présent aussi dans les laboratoires pour la R&D associée (figure 31). La R&D est encore très active, compte tenu des perspectives industrielles offertes par le procédé et représente près de 40 % de l’activité, le reste étant dévolu à la production.
La prolifération du cold spray doit aussi à son coût d’investissement relativement réduit et à une visibilité assez nette sur ses coûts de fonctionnement. Même si une analyse économique doit être effectuée pour chaque type de production envisagée, en incluant des considérations conjoncturelles, une répartition caractéristique des coûts du procédé, pour une installation donnée, peut être avancée (figure 32), ne serait-ce que pour pouvoir le comparer aux autres procédés. En première approche, elle montre que le poste « poudre » est, de loin, le plus conséquent. Il compte pour une petite moitié de la dépense, tandis que le gaz (dans le cas, cependant, le plus courant de la projection avec l’azote) ne représente que quelques pourcents de la facture totale.
Le rendement de projection (influencé par les caractéristiques des poudres) joue fortement sur le coût de production par cold spray. Plusieurs études de cas ont montré que s’il doublait, le coût pouvait être divisé par deux, sachant que l’influence du rendement était d’autant moins marquée qu’il était élevé. Ce dernier point s’explique par le fait que le coût opératoire croît avec un objectif de rendement élevé puisque les conditions de projection (pression, température, débit, diamètre de buse) y sont plus sévères.
Le poste « gaz » peut varier considérablement selon la nature du gaz de projection employé. Par rapport au cas où l’azote est utilisé, figure 32, (il représente, de loin, le plus fréquent) le coût de projection peut être abaissé si l’air lui est préféré (dans le cas d’une projection du cold spray basse pression), à condition toutefois que la nature du matériau à déposer le tolère. En revanche, l’emploi d’hélium, s’il faut y recourir pour augmenter la vitesse des particules donc les propriétés du dépôt obtenu, peut se révéler être d’un coût prohibitif et représenter, au lieu d’environ 5 % du prix de la poudre comme dans le découpage caractéristique de la figure 32, plus de 5 fois celui-ci. La raison en est l’augmentation du débit de gaz requis, 4 à 5 fois plus élevée pour l’hélium que pour l’azote. Le coût global de fonctionnement peut alors s’en trouver multiplié par 3 ou 4. Pour y pallier, le recyclage de l’hélium de projection peut être adopté, sous réserve que le volume de projection/production/gaz l’exige. L’installation de recyclage, en effet, impose la projection en enceinte fermée et l’adjonction de réservoirs et systèmes de filtration, pompage et recompression de gaz supplémentaires donc des surcoûts.
Quelle que soit la nature du gaz, la façon dont il est disponible pour la projection doit être soigneusement réfléchie, en fonction du type de production par cold spray envisagé. Selon qu’il sera disponible en vrac ou en bouteille, le prix au m3 consommé pourra se trouver multiplié par un facteur 4 environ : sachant, cependant, que le vrac impose un investissement préalable en systèmes de cryogénie et de régulation pouvant dépasser les 120 k € HT (prix 2021).
De même que le gaz de projection peut être recyclé, la poudre peut l’être aussi. Là encore, l’investissement préalable en dispositifs de projection en mode confiné, de filtration, etc. doit être pris en compte. L’opération peut être rentable, cependant, si les poudres en question sont chères et/ou les rendements de projection faibles. D’autres raisons justifiant un éventuel recyclage et/ou, au moins, de captation des poudres, sont liées à la protection de l’environnement et de la santé.
Aujourd’hui, les considérations économiques constituent des arguments favorables à l’implantation et au développement industriel du cold spray qui devraient se trouver corroborés par des résultats d’enquête sur l’utilisation industrielle du procédé comme a pu en faire paraître jusqu’alors et périodiquement la « Thermal Spray Association » pour les autres procédés de revêtement. Ces éléments, malheureusement, n’ont pas été encore publiés, étant donné la jeunesse du cold spray et les enjeux économiques qu’il représente dans le secteur.
Règles d’hygiène et de sécurité dans l’emploi du cold spray
Les règles d’hygiène et de sécurité devant présider à l’emploi du cold spray tiennent au fait que le procédé est bruyant et utilise de fortes quantités de gaz et de poudres. L’utilisateur devra se reporter à la règlementation et aux normes en vigueur relatives à ces 3 points. Seuls seront soulignés, dans cette partie, des éléments propres au cold spray pour sa pratique. Pour le reste, les documents et informations sont disponibles à l’INRS (Institut national de recherche et de sécurité), en particulier.
Pour ce qui concerne les 3 points caractéristiques préalablement mentionnés, le cold spray peut être annoncé comme présentant, en fonctionnement, un niveau sonore pouvant atteindre les 125 dB(A) (en haute pression et 105 en basse pression), un débit d’écoulement de gaz (inerte) dans la buse de l’ordre de quelques m3/min, et des taux de dépôt à partir de poudre dans la gamme 2-12 kg/h pour un rendement situé, le plus souvent, entre 40 et 98 %. L’installation de base cold spray dont le cœur répond au principe décrit au § 1 et en figure 2 doit donc être complété d’équipements auxiliaires destinés à la faire fonctionner dans les conditions de sécurité optimale : cabines insonorisées, armoires, récupérateur de poussière, boîtes à gants, port du casque, etc.
L’application des règles de sécurité permet, incidemment, la distinction entre les 2 principales classes d’installations cold spray, celles à basse pression et celles à haute pression. Si un opérateur, sous réserve d’être protégé (masque, casque anti-bruit, chaussures de sécurité et habit adéquat), peut être présent dans le voisinage d’une installation « basse pression » pendant la projection, une installation « haute pression » doit projeter en cabine fermée, tout personnel devant en être sorti au préalable. Dans ce dernier cas, seuls des dispositifs de contrôle, par caméra par exemple ou autres capteurs divers, peuvent surveiller l’opération de projection en temps réel. C’est pourquoi les opérations de réparation par cold spray sur site (ligne de production, piste d’aéroport, par exemple) ne peuvent être envisagées qu’en basse pression. Il reste, cependant, une tendance à automatiser, y compris en basse pression, incluant des dispositifs de coupure ou de verrouillage de sécurité en cas de dysfonctionnement de systèmes essentiels (filtration, régulation de gaz), des barrières et autres protections de personnels.
Compte tenu de l’usage massif et intensif de poudres et de la possible génération de poussières dans un environnement de circulation de gaz (y compris l’air ambiant) et de sources d’énergie (électrique et chaleur) diverses, les règles de prévention des risques liés au feu et aux explosions doivent être rigoureusement respectées. Les risques sont d’autant plus importants que la conjonction de différents facteurs existe comme le classique triangle et le non moins classique pentagone de risques (figure 33) l’illustrent pour, respectivement, le feu et les explosions. Par rapport au risque de feu, celui d’explosion survient quand de la poussière métallique atteint un certain seuil de concentration dans l’air et quand un nuage de poudre se trouve dans un milieu confiné.
Par rapport au risque de feu, celui d’explosion survient quand de la poussière métallique atteint un certain seuil de concentration dans l’air et quand le nuage correspondant se trouve dans un milieu confiné. Pour y remédier, une installation cold spray sûre et conforme devra être équipée de moyens permettant d’abaisser la limite inférieure d’explosivité des poussières métalliques grâce à des systèmes d’extraction de poussière, de filtration et de ventilation. De même, l’infiltration de ces mêmes poussières dans les systèmes électriques doit être limitée par l’emploi de matériels isolés et ou sous pression régulée. En France (et en Europe), toute installation cold spray doit être reconnue conforme aux directives ATEX 94/9/EC en fonction de la zone dite ATEX dans laquelle elle doit se trouver. Par rapport aux autres procédés de projection thermique, l’atout en ce domaine du cold spray est d’être de tout processus de combustion et/ou d’arc électrique.
Plus généralement, en association aux aspects hygiène et sécurité, peuvent être considérées les questions d’impact du procédé sur la santé et l’environnement. Globalement, le cold spray, en tant que procédé par voie sèche, se situe favorablement par rapport aux procédés de dépôt par voie humique (électrochimie en particulier). Plus précisément et pour le situer par rapport aux autres procédés (par voie sèche) de projection thermique, il est nécessaire d’effectuer un bilan comparatif par type de production, passant notamment par une analyse du cycle de vie (ACV), selon normes ISO 14040 et 14044.
9 Cold spray et matériaux non métalliques
Comme dit précédemment, puisque la déformation plastique du matériau de dépôt (et, dans une moindre mesure, celui du substrat) est à la base du processus régissant le cold spray, le procédé a intéressé et intéresse toujours, en premier lieu, les métaux. Le contenu de cet article le reflète. Les autres classes de matériaux, en tête desquelles les polymères et les céramiques, ne sont pas écartés, cependant. Pour le dépôt, ils furent, tout d’abord, envisagés en tant que matériaux d’apport intervenant en mélange dans une phase métallique majoritaire pour la réalisation de composites. Le principe de base du cold spray n’en étant pas ainsi modifié.
En revanche, pour un dépôt homogène, la céramique pose question du fait de sa fragilité qui la rend inadaptée aux mécanismes de dépôt fondamentaux du cold spray. De prime abord, le cold spray de céramique est à considérer comme un sablage plutôt qu’un procédé de dépôt. Il faut donc invoquer d’autres mécanismes de densification pour pouvoir appliquer la projection à froid aux céramiques. En effet, jusqu’alors, seuls les rares exemples de dépôt de TiO2 et d’hydroxyapatite (éventuellement en mélange dans ce dernier cas, avec du graphène par exemple) ont expérimentalement donné quelque espoirs de réussite d’application du cold spray à ce type de matériaux.
Néanmoins, des matériaux composites de base nickel avec des additifs carbures WC et borures NB donnent des résultats intéressants.
Toujours pour l’obtention d’un dépôt homogène, le cold spray de polymères soulève moins de questions que celui de céramiques, puisque leur comportement (viscoélastique-viscoplastique) en déformation se prête au procédé. C’est pourquoi, la démarche de développement du cold spray pour cette classe de matériaux devrait s’inspirer de celle adoptée pour les métaux, aux différences près liées aux caractéristiques propres aux polymères. L’écart dans le temps entre leur développement respectif tient en particulier aux problèmes technologiques (collage, bouchage, instabilité) associé à l’emploi de polymères dans des installations où ils doivent circuler, sous forme de poudre, à température et vitesse élevées.
En tant que substrats, polymères comme céramiques furent et sont utilisés avec succès pour recevoir une métallisation par cold spray. Leur utilisation n’est pas à reconsidérer, de nombreuses applications les appelant existant, y compris pour la fabrication additive où des substrats amovibles peuvent avoir à être utilisée.
10 Conclusion et perspectives
Loin d’avoir jeté un coup de froid sur la projection thermique, le cold spray lui a, au contraire, insufflé un nouvel élan vital avec les années 2000 qui en ont vu le développement. Initialement écarté de la famille des procédés de projection thermique, il peut en être considéré maintenant comme le chef de file. Compte tenu des coûts d’investissement relativement bas et du fort potentiel de leur technologie, les installations cold spray semblent se multiplier inexorablement dans les ateliers à façon, les PME et les grandes entreprises, sans compter les dites universitaires, pour devenir aussi banales que des fours ou des lasers.
L’essence du cold spray reposant sur la déformation des particules projetées, le procédé, historiquement, a vu son développement « à partir du métal », c’est-à-dire majoritairement appliqué aux matériaux métalliques (d’où le traitement du sujet dans cet article) : tant pour le dépôt que pour le substrat (bande de base rouge en figure 36). Les tenants du procédé ont pu songer et songent encore « à partir du métal », mais dans l’autre acception du mot partir, c’est-à-dire, s’en éloigner pour se tourner, grâce aux performances de nouveaux matériels, vers d’autres classes de matériaux : polymères et céramiques. Ces derniers peuvent intervenir en mélange avec du métal, mais aussi seuls, pour le dépôt comme pour le substrat. L’évolution du cold spray peut donc, de manière appropriée, être tracée par les matériaux auxquels le procédé s’est appliqué (s’applique). Il en résulte une représentation chronologique en escalier, la diversification de matériaux étant cumulative. Chaque cas marque une étape/marche dans l’évolution du cold spray, très ascendante dans les dernières années.
Plus fondamentalement, l’avènement du cold spray a correspondu avec la concrétisation du rêve de métallurgistes avec l’élaboration de structures, souvent originales et à hautes propriétés, obtenues dans des conditions dynamiques, sans avoir à recourir à des procédés hors normes, par exemple ceux utilisant des explosifs. De plus, l’ouverture du procédé vers l’industrie, pour les mêmes raisons de facilité d’exécution, justifie largement son essor continu amorcé avec le XXIème siècle.
Le caractère multi-échelles et la complexité des phénomènes et mécanismes en jeu dans le procédé, qui, incidemment, en constituent la richesse, imposent de nombreuses recherches pour en améliorer encore la compréhension donc la maîtrise. Ces recherches, par là même, élargiront encore le champ des applications possibles. Les perspectives associées peuvent être mentionnées comme suit :
- Développement de poudres : La production de poudres aux caractéristiques (mécaniques, métallurgiques, morphologiques, et chimiques) adaptées au procédé constitue une perspective, sans cesse renouvelée au fur et à mesure que la connaissance de ces caractéristiques se précisera grâce aux études associées. Ces études incluent aussi les poudres composites, en mélange et/ou en agrégats nanostructurés. Pour ces dernières, l’intérêt serait d’exploiter au mieux le caractère « froid » et dynamique du procédé qui pourrait en conserver, dans le dépôt final, les propriétés ;
- Synthèse in situ de matériaux par la filière « cold spray + post-traitement », le cold spray y étant utilisé comme simple procédé d’apport de matière, les propriétés du matériau final étant conférées, si nécessaire, par traitement post-dépôt, thermique ou thermochimique ;
- Amélioration de la technologie des installations, pour augmenter encore la température du gaz de projection (quelques dizaines de degrés sont annoncés comme encore possibles) donc la vitesse des particules, pour augmenter le rendement matière et la productivité (multi-buse, multidistribution), et pour le dépôt dans de petites cavités (actuellement (2020) au mieux dans un alésage de diamètre 80 mm avec une buse tournante) ;
- Développer les procédés hybrides, y compris avec d’autres procédés que le laser ou le grenaillage déjà abordés, par exemple, le couplage avec l’usinage mécanique en une seule unité (associant ainsi fabrications additive et soustractive pour ce qui pourrait s’appeler « fabrication soustractive ») ;
- Poursuite du développement de la fabrication additive par cold spray, grâce à l’intégration de systèmes intelligents intégrant contrôle de paramètres de dépôt (dimensionnels, physiques) et pilotage machine associé (conditions cold spray et stratégie de robot voire de robots (un pour le pistolet et un autre pour la pièce)) ;
- Miniaturisation des dispositifs cold spray, pour la réparation locale et la fabrication additive directe de petits objets ;
- Développement du cold spray en enceinte sous pression réduite ;
- Développement du cold spray avec fluides supercritiques.
Bibliographie
Les auteurs ont rédigé cet article avec l’aide de la présentation : Projection dynamique par gaz froid (ou cold spray) des Techniques de l’ingénieur, réf. : M1648 V1.