Aheadd® CP1 : un alliage aluminium spécial fusion laser sur lit de poudre (L-PBF) performant en corrosion et traitements de surface
MILLOT Coraline(1), RENAUD Alexis(2), PEGUET Lionel(1), TARDELLI Joffrey(2), SHAHANI Ravi(1), LAMESLE Pascal(2).
(1) C-TEC, Constellium Technology Center, Parc Economique Centr’alp, CS 10027, Voreppe 38341 Cedex, France. (2) IRT M2P, Institut de Recherche Technologique Matériaux Métallurgie et Procédés, 4 rue Augustin Fresnel, Metz, 57070, France
Contrairement aux autres alliages qui requièrent une mise en solution, trempe et recuit après fabrication, l’alliage d’aluminium composé d’1 % de Fe et 1.2 % de Zr utilise la solidification rapide L-PBF pour atteindre un état stable avec des contraintes résiduelles faibles. Un simple traitement thermique de 4 h à 400 °C permet à cet alliage d’obtenir sa résistance finale[2][5], lui conférant un potentiel inédit pour l’industrialisation de la production de composants en fabrication additive.
1. Introduction
Aheadd® CP1, aussi connu sous la dénomination AA 8A61.50[1], est un alliage d’aluminium composé d’1 % de Fe et 1.2 % de Zr conçu pour la fabrication additive et en particulier pour la technologie fusion laser sur lit de poudre (L-PBF). Le CP1 possède des propriétés mécaniques, électriques, thermiques, en radio-fréquence, en stabilité thermique, en résistance à la corrosion et de compatibilité en traitement de surface (dont anodisation) intéressantes[2]. Ce champ de propriétés large et diversifié permet au CP1 d’être utilisé dans de nombreuses applications telles que les composants mécaniques, semi-conducteurs, échangeurs de chaleur, antennes RF, composants pour satellites, etc. Cet alliage ne contenant pas de magnésium, il est donc moins susceptible de former en surface des oxides de magnésium pouvant être néfastes en présence d’humidité[3]. Par ailleurs cette absence de magnésium ainsi que de zinc (éléments volatiles) dans la composition donne une meilleure stabilité au métal fondu (melt pool) et réduit la présence de fumée lors de l’utilisation de laser durant l’impression[4].
Contrairement aux autres alliages qui requièrent une mise en solution, trempe et recuit après fabrication, le CP1 utilise la solidification rapide L-PBF pour atteindre un état stable avec des contraintes résiduelles faibles. Un simple traitement thermique de 4h à 400 °C permet à cet alliage d’obtenir sa résistance finale[2][5], lui conférant un potentiel inédit pour l’industrialisation de la production de composants en fabrication additive.
La production de CP1, et de nombreux autres alliages destinés à la fabrication additive sur lit de poudre, se fait par la pulvérisation d’un flux de métal liquide à l’aide d’un gaz. L’IRT M2P dispose d’un atomiseur VIGA (Vacuum induction melting Inert Gas Atomization) capable de produire du CP1 selon ce principe. Les projets en lien avec l’IRT M2P et Constellium montrent déjà des résultats très satisfaisants sur la qualité du produit et les caractéristiques atteintes par le matériau.
Dans cette étude sont présentés l’état de surface après impression du CP1 (§2, travaux IRT M2P), sa résistance à la corrosion (§3, travaux C-TEC) ainsi que sa compatibilité avec de nombreux traitements de surface (§4.1 anodisations et §4.2.2 polissage chimique réalisés par C-TEC ; §4.2.1 autre polissage chimique issu des travaux IRT M2P).
2. État de surface après impression
Le procédé L-PBF permet l’obtention d’une pièce métallique par fusion de couches successives de poudre via une source laser. Le temps de fabrication, la santé matière (taille et nombre de porosités) et l’état de surface des pièces sont conditionnés notamment par l’épaisseur et la granulométrie des couches de poudre ainsi que par les paramètres laser (puissance, vitesse, trajectoire). En sortie d’impression, l’état de surface des pièces obtenues par L-PBF se caractérise par :
Une rugosité très importante et inhomogène inhérente à ce procédé d’élaboration (fusion de poudre couche par couche).
La présence en surface de nombreuses particules métalliques infondues ou mal fondues, même après dépoudrage. Leur détachement potentiel lors de la vie de la pièce peut alors poser de nombreux problèmes de santé et de sécurité.
Par ailleurs, la fabrication d’une pièce complexe impose l’utilisation de paramètres laser spécifiques pour les zones en porte-à-faux (zones dites downskin imprimées avec un angle compris entre 0 et 90° par rapport au plateau de fabrication) qui exacerbent les problématiques d’état de surface. En effet, comme démontré dans la figure 1a, la rugosité de surface évolue fortement selon l’angle d’impression en plus de paramètres machines telles que l’épaisseur de couche, la puissance du laser et autres paramétries.
Des éprouvettes en CP1 (couches de 60 µm ; traitement thermique : revenu 3 h à 400 °C) ont été étudiées et comparées avec des éprouvettes équivalentes fabriquées en AS7G06 (couches de 50 µm ; traitement thermique : revenu 6h à 170°C sous air sans mise en solution), l’impression ayant été faite selon un angle de 45° comme décrit figure 1b afin d’obtenir un comparatif upskin versus downskin (tableau 2 pour le facies). Les états de surface ainsi que la santé matière ont été caractérisés dans les mêmes conditions. Leur aptitude au parachèvement par voie chimique a également été évaluée et sera traitée au §4.2.1. La paramétrie du CP1 était en cours de définition lors de l’impression des éprouvettes ce qui, outre la différence d’épaisseur de couche d’impression entre CP1 et AS7, explique les écarts de rugosités surfaciques initiales entre les deux alliages (tableau 2).
Au-delà des problématiques d’état de surface, la santé matière et la microstructure des pièces issues de fabrication additive sont également des enjeux majeurs du déploiement de ces nouveaux moyens d’élaboration. Dans la figure 2, les différentes coupes micrographiques révèlent une microstructure typique des matériaux obtenus par L-PBF avec la présence de « melt pools » caractéristiques du procédé.
3. Résistance à la corrosion
Il est connu que la composition et la microstructure (phases intermétalliques, joint de grains, ségrégations…) d’un alliage d’aluminium influencent ses propriétés de résistance à la corrosion mais lorsque l’on parle de fabrication additive, d’autres paramètres liés aux procédés entrent aussi en jeu tels que porosité, rugosité de surface, zones de refusion (« melt-pool boundaries »), structures de grain et contraintes résiduelles notamment[7][8][9]. Un certain nombre d’études a déjà été réalisé pour les alliages de type AlSiMg [10] [11]. En revanche, ce n’est pas encore le cas pour le CP1. C’est pourquoi afin d’évaluer les performances en corrosion du CP1 « nu » des essais ont été réalisés suivant les normes ISO 11846B, ASTM G44 / EASA SIB 2028-04R2 et ASTM B117 en comparaison d’alliages de type AlSiMg mais aussi d’autres alliages conventionnels laminés. Des mesures d’impédance ont aussi été réalisés afin d’estimer de manière quantitative la cinétique générale de corrosion.
Il est par ailleurs important de rappeler les précautions d’élaboration suivantes à prendre s’agissant en particulier des caractérisations corrosion (et/ou traitements de surface) :
Utilisation privilégiée de machines d’impressions dédiées uniquement aux alliages Al et encore mieux CP1 : en effet dans le cas d’utilisation multi-matériaux, risque important de pollution avec des particules d’acier, occasionnant du couplage galvanique non représentatif du matériau testé
L’utilisation de l’usinage par électroérosion (généralement utiliser pour séparer les composants imprimés des plateaux de construction) est à éviter dans la mesure où les échantillons peuvent être pollués avec des résidus de fil de coupe (type laiton), entrainant des effets de couplage galvanique.
3.1. Méthodologie
Dans l’ensemble des études présentées, et afin d’être comparatif avec des alliages plus classiques, les surfaces ont été usinées afin de s’affranchir de la rugosité de surface, celle-ci pouvant influencer la corrosion. L’impact de cette rugosité de surface (pouvant par ailleurs être atténuée par des traitements de surface chimiques) est encore en cours d’étude sur le CP1 (néanmoins on peut s’attendre à un effet positif d’un polissage (mécanique type tribofinition ou chimique) comme dans le cas de AlSi10Mg[7]).
Mesure d’impédance
La spectroscopie d’impédance électrochimique (SIE) repose sur la détermination d’une fonction de transfert suite à une perturbation volontaire du système électrochimique étudié. Pour nos essais, la perturbation imposée en potentiel est sinusoïdale et les mesures se font à une mono-fréquence de 100 mHz ainsi qu’une amplitude de 10 mV. Un scan est réalisé toutes les 15 minutes pendant 3 jours dans une solution NaCl 0,1M aérée, l’idée étant de laisser l’échantillon majoritairement à son potentiel libre avec une période de sollicitation d’une durée réduite de 10 secondes à potentiel imposé.
ASTM B117
L’ASTM B117 est un test de brouillard salin neutre, faisant parti des tests standards les plus reconnus. Les échantillons « main courante » ont été exposés pendant un mois en brouillard salin neutre (NaCl 5 % pH 6.5-7.2) continu à 35°C.
Essai d’immersion en solution ISO 11846 B
Cet essai est habituellement utilisé pour comparer la résistance à la corrosion intergranulaire de divers alliages d’aluminium pour applications automobiles (6xxx majoritairement), en fonction de leur composition chimique et traitement thermique. L’essai est utilisé ici dans l’objectif de révéler différentes morphologies de corrosion pour chacun des échantillons et de les comparer.
Les échantillons sont immergés pour une durée de 24 h en bécher dans une solution contenant 30 g/L de NaCl, et 10 mL d’acide chlorhydrique concentré (1,19 g/mL)
à température contrôlée de 30 ± 3°C. En fin d’essai, les échantillons sont rincés à l’eau déminéralisée et laissés à sécher (air du laboratoire). Les produits de corrosion sont retirés à l’aide d’acide nitrique 70 % pendant quelques minutes (2 à 5 minutes selon la quantité à dissoudre), enfin ils sont rincés à l’eau déminéralisée. La détermination du type et de la profondeur de corrosion est faite via un examen en coupe micrographique du métal dans le sens TL-TC.
Corrosion sous contrainte : ASTM G44 / EASA SIB 2018-04R2
Ce test met en œuvre une sollicitation mécanique constante sur des éprouvettes cylindriques de 3,17mm de diamètre dans des montages anneaux qui permettent d’imposer une force constante (type ASTM G49), comme illustré dans la figure 5a. Ces montages sont ensuite placés dans deux environnement corrosifs différents : celui de l’ASTM G44 et celui de l’EASA SIB 2018-04R2.
Dans le cas de l’ASTM G44, les montages anneaux sont exposés à un test cyclique de 2 phases alternées pendant 40 jours (et jusqu’à 90 jours pour le CP1) :
10 min d’immersion dans une solution saline (3.5 % massique NaCl, tamponné à pH 6.5-7.2 à l’acide chlorhydrique ou à la soude dilué)
50 min d’émersion dans une pièce maintenue à 27°C et 45 % d’humidité (+/ – 10 %)
Après le test, les échantillons sont décapés 1min dans l’acide nitrique à 65 % puis observés à la loupe binoculaire pour vérifier l’absence de fissure.
Dans le cas de l’EASA SIB 2018, les montages anneaux sont exposés à un milieu constamment chaud et humide (enceinte contrôlée à 70 °C et 85 % d’humidité relative) pendant un an (366 jours).
3.2. Résultats
Les échantillons CP1 (sauf mention contraire) utilisés dans les études suivantes ont été imprimés sur une machine EOS M290 par couches de 60 µm et ont subi un traitement thermique de 4 h à 400 °C.
Mesure d’impédance
La cinétique de corrosion est estimée via la mesure du module d’impédance Z en milieu salé aéré, celle-ci étant proportionnelle à 1/Z. Ainsi, d’après la figure 3a, on peut noter que la vitesse de propagation de la corrosion la plus faible est celle du CP1. Par ailleurs, il existe une différence d’un facteur ≈5 à 10 entre le CP1 et l’alliage Al-Si (type AS7), et encore plus important avec un alliage conventionnel AA2024 T3 (typiquement utilisé en l’aéronautique). Il est probable que la teneur en cuivre soit de premier ordre pour explique le comportement du AA2024. Au contraire, l’alliage CP1 profite d’une composition exempte de cuivre ou de phase grossières. L’alliage Al-Si est intermédiaire ; sa teneur importante en Silicium, bien que cathodiquement moins actif que le cuivre peut être en cause pour expliquer son positionnement inferieur au CP1.
ASTM B117
Dans cette étude, les plaquettes imprimées n’ont subi ni revenu thermique ni usinage et sont donc brutes d’impression. Après un mois d’exposition, on constate une corrosion cosmétique plus développée et importante sur l’alliage AlSi10Mg que pour le CP1, comme montré dans la figure 3b. C’est sur ces critères de résistance à la corrosion que l’alliage CP1 a été choisi par la Deutsche Bahn afin d’équiper les mains courantes en braille des gares allemandes et aider les voyageurs malvoyants à circuler plus facilement.
ISO 11846 B
Le but des études réalisées selon l’ISO 11846 est de pouvoir caractériser la sensibilité à la corrosion intergranulaire de l’alliage CP1 en comparant différentes épaisseurs d’impression (60, 90 et 120 µm) à des alliages conventionnels (6005 T4+BH et 6061 T651) et à un alliage Al-Si imprimé (AlSi7G06, couche 50µm, VolumE).
Les résultats sont présentés dans la figure 4 et les observations suivantes peuvent être faites :
6005 et 6061 : présence de sites de corrosion intergranulaire
AS7G06 : présence de sites de corrosion par piqûres significatifs
CP1 : en fonction de l’épaisseur de la couche d’impression, les résultats diffèrent. En effet aucun site significatif n’est observé pour une impression à 60µm, en revanche à 120µm quelques sites de corrosion par piqures sont observés (quelques rares sites à 90µm).
Ainsi le CP1 ne présente pas de risque de corrosion localisée notable notamment aux joints de grains. Ce test permet aussi de faire une sélection rapide sur des études de paramètres tels que le choix de la composition d’alliages, traitements thermiques et paramètres d’impression.
Corrosion sous contrainte : ASTM G44 / EASA SIB 2018-04R2
Les contraintes appliquées sont données dans le tableau 1.
Après 90 jours d’exposition, les éprouvettes CP1 ne montrent aucune rupture ni signe de corrosion quelle que soit la contrainte, ce qui n’est le pas cas des alliages conventionnels, exposés eux pendant 40 jours uniquement, comme présenté dans la figure 5b et c (90 jours est la durée maximum recommandée concernant les solutions conventionnelles les plus performantes tels des alliages 6XXX en sens TL). Aucun signe de corrosion n’est aussi visible sur l’échantillon SC9 testé pendant 1 an, comme illustré figure 5b. Les résultats sont d’autant plus appréciables dans la mesure où la qualité d’impression n’avait pas été optimisée (présence de défauts au sein des éprouvettes révélés par USHR).
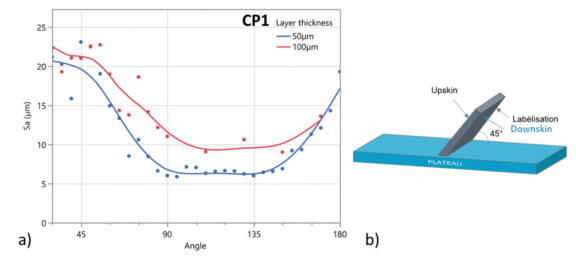
Figure 1 : a) Exemple d’évolution de la rugosité en fonction de l’angle d’impression pour deux épaisseurs de couches d’impression pour du CP1[6] ; b) Illustration de l’orientation des éprouvettes sur le plateau de fabrication.
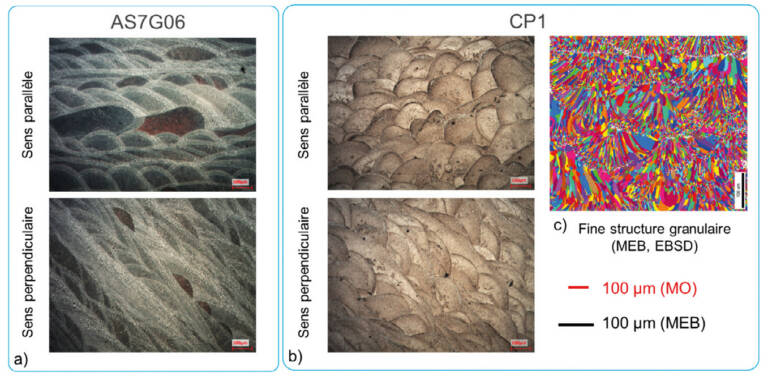
Figure 2 : Coupes micrographiques des éprouvettes en a) AS7G06 CP1 et en b) CP1 dans les sens parallèle et perpendiculaire au plateau de fabrication après attaque Keller (x100 et x 500) ; c) MEB, EBSD sur du CP1 [2] [5]
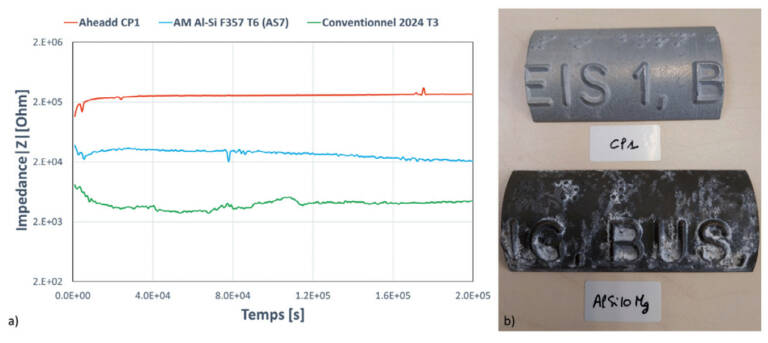
Figure 3 : a) Evolution du module d’impédance Z en fonction du temps en milieu NaCl 0.1M (solution aérée air) pour différents alliages ; b) Résultats de corrosion sur CP1 et AlSi10Mg après un mois de brouillard salin à 35°C (ASTM B117)
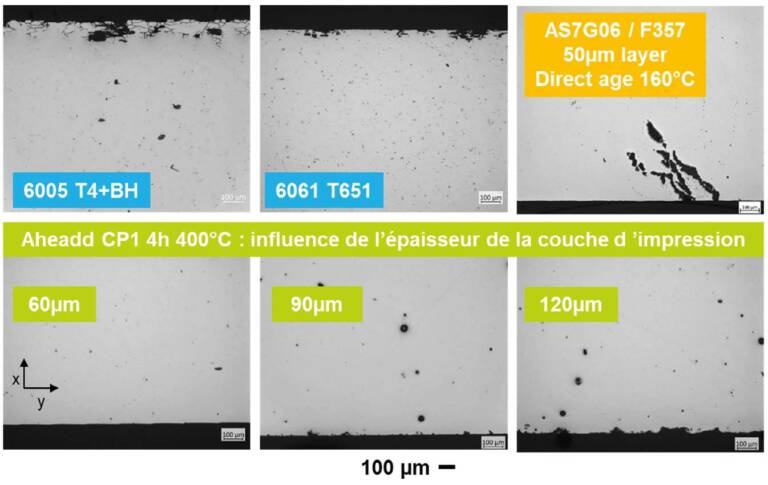
Figure 4 : Observations en coupe microscopique, brutes de polissage, après 24h de test ISO11846B
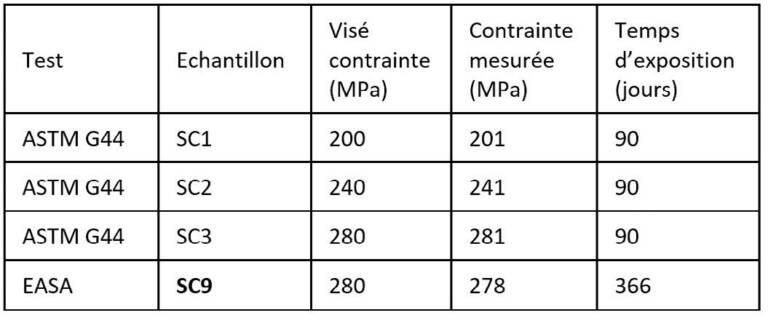
Tableau 1 : Conditions de contrainte, temps d’exposition et test appliqué aux différents échantillons CP1
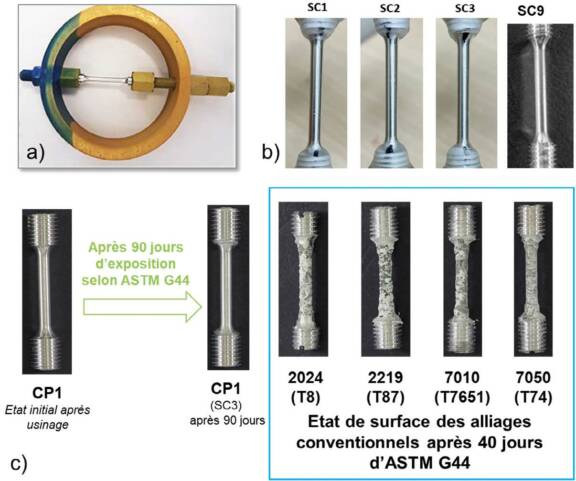
Figure 5 : a) Montage anneau permettant d’imposer une force constante sur une éprouvette cylindrique ;
b) Eprouvettes de CP1 après vieillissement ; c) Comparatif entre CP1 à 90 jours et alliages conventionnels à 40 jours selon exposition ASTM 44
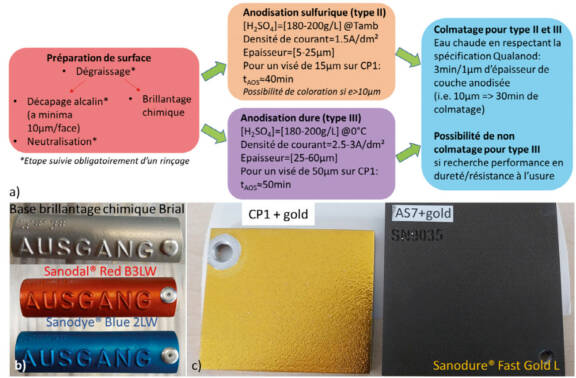
Figure 6 : a) Gammes d’anodisations sulfuriques pour CP1 ; b) Illustration utilisation brillantage chimique seul ou suivi d’anodisation colorée Rouge ou Bleu sur CP1); c) Exemple d’utilisation d’anodisation colorée Or sur CP1 et AS7G06
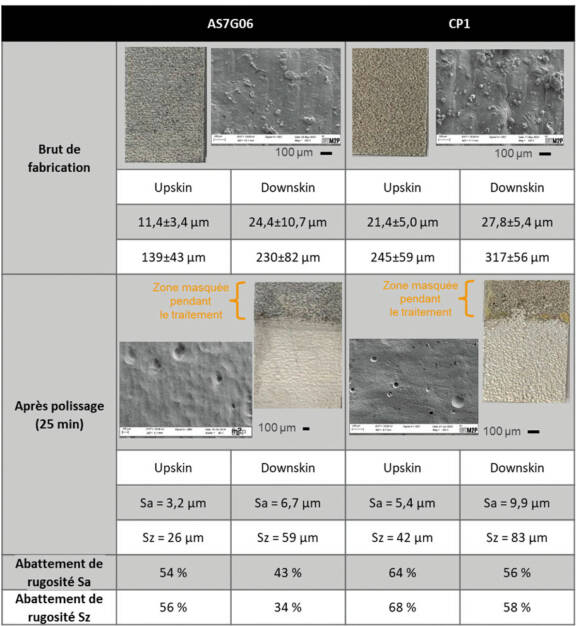
Tableau 2 : Données pré et post traitement (polissage IRT) pour éprouvettes en AS7G06 et en CP1
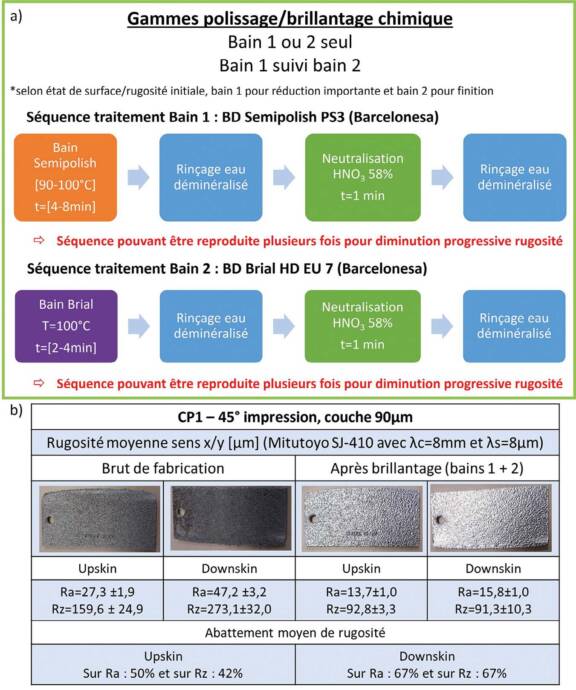
Figure 7 : a) Gammes de polissages chimiques compatibles CP1 ; b) Exemple d’application sur CP1 avec mesures de rugosité
4. Compatibilité traitements de surface
4.1. Anodisations
En raison de sa matrice proche d’un aluminium pur associée à des intermétalliques submicroniques, le CP1 peut facilement être anodisé selon des gammes standard tels que décrit dans la figure 6a. Il est tout de même recommandé de passer par un brillantage chimique (§4.2.2) préalable afin d’obtenir un meilleur aspect de surface pour la coloration mais aussi réduire la rugosité de surface comme exposé figure 6b. On notera au passage que l’AS7 n’est pas compatible avec une anodisation colorée comme démontré dans la figure 6c.
Il est par ailleurs possible de réaliser une anodisation dure classique sur CP1, ou l’anodisation propriétaire de Constellium, Endurance®[12] optimisé pour des 6XXX. Il a été observé que l’état de surface influençait grandement les caractéristiques de la couche anodique notamment la tension de claquage où un état usiné présentait systématiquement de meilleurs résultats qu’une surface brute. Des travaux doivent se poursuivre sur l’influence de l’état de surface mais aussi les corréler à d’autres types de performance (bubble test, tenue en corrosion…).
4.2. Polissage chimique
4.2.1. Formulation IRT
La qualité de surface après impression des pièces en fabrication additive ne permet pas toujours de les utiliser en l’état selon les applications visées et nécessite alors un traitement de surface type polissage chimique afin de réduire les fortes rugosités observées, éliminer les particules infondues ou mal fondues et, de manière plus générale, homogénéiser les surfaces en tout point des pièces.
Les travaux de l’IRT M2P se sont notamment concentrés sur le développement de bains de polissage chimique adaptés aux différents matériaux rencontrés dans l’industrie. Une formulation, à base de divers acides (phosphorique, sulfurique et nitrique) ainsi qu’un agent complexant fluorure, dédiée aux alliages d’aluminium a ainsi été mise au point et brevetée [13]. Elle est aujourd’hui opérationnelle à l’échelle industrielle chez plusieurs acteurs de l’aéronautique.
Cette formulation de polissage a été initialement développée pour des alliages de fonderie type Al-Si largement déployés dans les procédés de fabrication additive par L-PBF. Une vitesse d’attaque comprise entre 6 et 10 µm/min est attendue sur cette famille d’alliages. Une réactivité inférieure, plutôt comprise entre 2 et 5 µm/min, a été constatée pour le CP1. Cela ne traduit pas pour autant une moins bonne efficacité de la solution de polissage pour abattre la rugosité, comme démontré dans le tableau 2 (pourcentage d’abattement de rugosité calculé afin de pondérer l’efficacité du traitement par rapport à l’état de surface initiale des pièces).
Le traitement de polissage chimique permet d’abattre significativement la rugosité des éprouvettes aussi bien sur AS7G06 que sur CP1. Les valeurs de rugosité finales obtenues sur CP1 sont légèrement supérieures, ce qui s’explique par une rugosité initiale elle-même supérieure à celle des éprouvettes en AS7G06. En effet, les traitements de parachèvement permettent d’abaisser la rugosité de la surface à mesure que la matière est consommée jusqu’à atteindre une valeur asymptotique inhérente au procédé. Plus la rugosité initiale est importante, plus l’enlèvement de matière nécessaire à l’atteinte de cette asymptote est élevé.
L’alliage CP1 obtenu par L-PBF peut donc être poli efficacement par ce procédé chimique disponible à l’échelle industrielle.
4.2.2. Solutions commerciales pour le CP1
Le CP1 étant un alliage exempt de silicium, il est possible d’utiliser des solutions sans acide fluorhydrique. Une étude en ce sens a été fait à C-TEC en utilisant des solutions commerciales du groupe Barcelonesa, développées pour le brillantage chimique de l’aluminium, avec une composition chimique connue pour son efficacité sur l’aluminium [14] :
Bain 1 BD Semipolish PS-3 : mélange à base d’acides phosphonique, orthophosphorique et sulfurique
Bain 2 BD Brial HD EU7 : mélange à base d’acides phosphonique, ortophosphorique, sulfurique et sulfate de cuivre.
Outre l’amélioration visuelle (brillantage) il est ainsi possible de diminuer les rugosités de surface dans le CP1 comme l’illustre la figure 7. Dans le cas de l’étude, des échantillons avec une très mauvaise qualité de surface post impression ont été choisis (impression 45 °C, couche 90 µm). Il a été possible d’obtenir un abattement significatif (plus important sur downskin) permettant ainsi d’homogénéiser les rugosités des faces upskin et downskin de manière équivalente. Les valeurs finales obtenues résultent de la qualité initiale d’où l’importance de partir de la meilleure qualité d’impression possible.
5. Conclusions
Le CP1 présente des performances en corrosion supérieures aux alliages standards pour l’additive tel que Al-Si ou aux familles d’alliages conventionnels 2XXX, 6XXX et 7XXX selon les normes ASTM B117, ISO 11846B ou encore ASTM G44. Il est également compatible avec de nombreux traitements de surface permettant d’optimiser ses performances et pour lesquelles des études complémentaires doivent être poursuivies (diminution rugosité de surface, traitement des porosités, impact de l’anodisation…).
Références
[1] Designations and Chemical Composition Limits for Aluminum Powders and Aluminum Alloy Powders, Registration Record Series – Purple sheet : The Aluminum Association, December 2022.
[2] C. Pauzon, M. Buttard, A. Després, B. Chehab, J.-J. Blandin et G. Martin, « A novel laser powder bed fusion Al-Fe-Zr alloy for superior strength-conductivity trade-off, » Scripta Materialia, vol. 219, p. 114878, 2022.
[3] C. Vargel, Corrosion of Aluminium, Elsevier, 2004.
[4] F. Palm, M. Bärtl, D. Schimbäck et A. Maier, « New tailored high strength & ductile Al-alloys for laser powderbed fusion (LPB-F), » chez 11th CIRP Conference on Photonic Technologies [LANE 2020], 2020.
[5] C. B. M. Pauzon, A. Després, F. Charlot, M. Fivel, B. Chehab et J.-J. M. G. Blandin, « Direct ageing of LPBF Al-1Fe-1Zr for high conductivity and mechanical performance, » Acta Materialia, vol. 258, p. 119199, 2023.
[6] Velo 3d, « Aheadd CP1, » [En ligne]. Available : https ://velo3d.com/material-aheadd-cp1/. [Accès le Juin 2024].
[7] G. Sander, J. Tan, P. Balan, O. Gharbi, D. Feenstra, L. Singer, S. Thomas, R. Kelly, J. Scully et N. Birbilis, « Corrosion of Additively Manufactured Alloys : a Review, » Corrosion, vol. 74, n° %112, pp. 1318-1350, 2018.
[8] R. Revilla, D. Verkens, T. Rubben et I. De Graeve, « Corrosion and Corrosion Protection of Additively Manufactured Aluminium Alloys—A Critical Review, » Materials, vol. 13, p. 4804, 2020.
[9] A. Biserova-Tahchieva, M. Biezma-Moraleda, N. Llorca-Iserne, J. Gonzalez-Lavin et P. Linhardt, « Additive Manufacturing Processes in Selected Corrosion Resistant Materials : A State of Knowledge Review, » Materials, vol. 16, p. 1893, 2023.
[10] J. I. G. G. J. Ahuir-Torres, G. West, A. Das et H. R. Kotadia, « Understanding the corrosion behaviour of Al-Mg alloy fabricated using a Laser Powder Bed Fusion (L-PBF) Additive Manufacturing (AM) process, » Journal of Alloys and Compounds, vol. 969, p. 172300, 2023.
[11] A. Gatto, C. Cappelletti, S. Defanti et F. Fabbri, « The Corrosion Behaviour of Additively Manufactured AlSi10Mg Parts Compared to Traditional Al Alloys, » Metals, vol. 13, p. 913, 2023.
[12] J. M. .. Van Kappel, C. Gasqueres, K. Pippig Schmid et M. B. Davo Gutierrez, « PROCÉDÉ DE FABRICATION D’UN ÉLÉMENT DE CHAMBRES À VIDE EN ALLIAGE D’ALUMINIUM ». Brevet EP 2 909 351 B1, 15 Octobre 2013.
[13] J. Frayret, J. Tardelli et L. Exbrayat, « Bain de polissage chimique pour aluminium et alliages d’aluminium, et procédé utilisant un tel bain ». France Brevet WO2021234001 A1, 25 Novembre 2021.
[14] P. G. Sheasby et R. Pinner, The Surface Treatment and Finishing of Aluminium and its Alloys, Sixth edition éd., Finishing Publications, 2001.