PROJET CAMFRE : Vers le développement ambitieux de couches d’alumine conductrices élaborées par oxydation micro-arc pour des applications connectiques en environnement sévère.
Par le consortium CAMFRE
Matériau à fort enjeu économique, l’aluminium nécessite néanmoins des traitements de surface lors de l’incorporation d’éléments d’alliage qui le sensibilisent fortement à la corrosion localisée. Ses propriétés mécaniques peuvent également s’en trouver altérées. L’interdiction du cadmium constitue un défi pour les industriels qui doivent imaginer de nouveaux procédés de traitement des alliages d’aluminium.
Dans de nombreux secteurs industriels, l’aluminium est un matériau à forts enjeux économique et écologique, notamment du fait de sa faible densité, synonyme d’allègement des structures métalliques. C’est particulièrement le cas dans le secteur du transport pour lequel allègement est synonyme de gain en consommation énergétique et par conséquent de réduction des émissions de gaz à effet de serre. Ainsi, la production mondiale d’aluminium a presque triplé en 15 ans(1). Dans le secteur plus particulier de la connectique (voir encadré), ses excellentes propriétés de conduction électrique, sa ductilité ou encore son effet barrière en font également un matériau de choix pour la réalisation des boîtiers de connecteurs (figure 1). Cependant, si l’aluminium non allié présente une excellente résistance à la corrosion grâce au film superficiel d’oxyde passif (1-3 nm), dont il se couvre naturellement en présence d’oxygène, l’incorporation d’éléments d’alliage le sensibilise fortement à la corrosion localisée. De même, les propriétés mécaniques des alliages d’aluminium peuvent être insuffisantes pour certaines applications (e. g. usure, frottement). En conséquence, des traitements de surface sont souvent nécessaires pour étendre les domaines d’application de ces alliages. Ces modifications de propriétés de surface sont le plus souvent réalisées par des traitements chimiques et/ou électrochimiques, souvent contraints par les réglementations en matière d’environnement et de protection des travailleurs (REACH(2) notamment)
Dans le domaine particulier de la connectique, ces contraintes concernent notamment l’utilisation et la mise en œuvre du cadmium. En effet, historiquement, la gamme de protection est un traitement des boîtiers en aluminium par un revêtement électrolytique de cadmium passivé au chrome VI.
Cependant, depuis 2017, l’utilisation du cadmium passivé au chrome (VI) est interdite en Europe. Le cadmium est, en effet, classé dans la liste européenne SVHC(3) de l’ECHA(4), et intégré à la « candidate List » de REACH (donc potentielle future obsolescence). L’utilisation du cadmium dans les équipements électriques et électroniques est également limitée par la directive européenne RoHS (2002/95/CE). L’arrêté interministériel du 23 mai 2019 introduit également une valeur limite d’exposition professionnelle (VLEP) pour le cadmium et ses composés à 0,004 mg/m3. De même, le chrome hexavalent ne peut plus être utilisé dans les procédés de fabrication, il est intégré à l’« annexe XIV » de REACH.
Le groupe CMG (Connectors Manufacturers’ Group, rattaché au syndicat des acteurs industriels de l’électronique ACSIEL), créé en 2014 par les principaux connecticiens français, a obtenu en 2018 de la CE une autorisation d’utilisation de cette solution conventionnelle jusqu’en 2029 (lettre d’autorisation d’utilisation de l’ECHA n°C (2018) 3734 final, et parution au Journal officiel) avec, en contrepartie, l’engagement de mener des travaux de substitution.
Cette dérogation a pour objectif de disposer du temps nécessaire au développement d’une gamme de traitements novateurs aux multiples ambitions :
satisfaire à l’ensemble des propriétés fonctionnelles remplies par la gamme actuelle de cadmiage passivé ;
être intégrables et industriellement mâtures pour assurer la continuité de l’activité ; il est à noter que les traitements de surface sont des opérations totalement intégrées et font partie d’un environnement industriel comprenant en amont l’usinage des boîtiers et en aval l’assemblage des connecteurs complets ;
protéger la santé des personnes qui doit être une priorité avant d’être déployée au niveau mondial (les opérateurs de production sont en effet en contact avec les bains de sels de Cr(VI) lors des opérations de prélèvements, d’ajouts de mélange, de drains et de contrôles visuels) ;
optimiser le cycle de fabrication des connecteurs en limitant la consommation de ressources énergétiques et matériaux tout en réduisant les rejets, pour intégrer la filière industrielle dans une démarche vertueuse ;
limiter les risques majeurs de dégradation potentielle des performances des connecteurs avec de possibles implications opérationnelles, la perte de maîtrise de la conception en France, et la fabrication hors de France et de l’UE de systèmes critiques, notamment pour le secteur de la défense.
Développer de nouveaux procédés de traitement des alliages d’aluminium pour le secteur industriel de la connectique est donc un défi qu’il est nécessaire et indispensable de relever afin de prévenir ces futures interdictions et de maintenir une industrie performante, compétitive et durable en France.
Quelle que soit son utilisation, le connecteur doit satisfaire à des exigences techniques propres au domaine d’application. Ces exigences sont d’autant plus drastiques pour ce qui concerne les connecteurs industriels utilisés en environnements sévères et pour des applications de haute sécurité telles que l’aéronautique et le spatial, les utilisations militaires et de défense et, de manière plus prospective, le nucléaire, les mines/offshore, le ferroviaire et le naval.
Pour ces applications très contraignantes, les boitiers de connecteurs doivent satisfaire à certains critères dont :
respect des normes de référence MIL-DTL-38999 (USA) et EN-3645 (Europe) ;
excellente tenue à la corrosion ;
aspect sombre et non réfléchissant ;
excellente conductivité électrique ;
excellente tenue à l’usure et durée de vie ;
tenue à la foudre ;
immunité aux perturbations électromagnétiques ;
maîtrise du procédé industriel et performance économique.
Pour répondre à la problématique du cadmium tout en satisfaisant aux exigences de la connectique, l’ambition du projet CAMFRE, soutenu par l’ANR, est d’élaborer, sur des alliages d’aluminium, des couches d’alumine à conductivité électrique significative par le procédé d’oxydation micro-arc (OMA). Outre le fait d’être un procédé propre, il est aussi novateur et prometteur, permet d’élaborer, rapidement et en une seule étape, des couches d’oxyde d’aluminium cristallines aux propriétés mécaniques et de résistance à la corrosion accrues[2, 3]. L’idée centrale du projet CAMFRE est d’incorporer dans les couches en cours de croissance des micro ou nanoparticules d’éléments conducteurs (carbone, métaux) en concentration suffisante pour atteindre le seuil de percolation électrique et créer ainsi des chemins de conduction dans les couches d’alumine formées. Les couches OMA possèdent en effet un réseau de porosité dans lequel les particules conductrices dispersées dans l’électrolyte peuvent s’insérer.
Le procédé d’Oxydation micro-arc (OMA)
L’Oxydation micro-arc (OMA) ou oxydation en plasma électrolytique (PEO[5]) est un procédé alternatif à l’anodisation et qui permet d’élaborer, sur des alliages métalliques légers (e. g. Al, Mg, Zr, Ti), des couches d’oxyde céramique possédant d’excellentes propriétés mécaniques et de résistance à la corrosion[4]. A l’instar de l’anodisation, l’OMA est réalisée dans un bain électrolytique dans lequel sont immergées les pièces à traiter et des contre-électrodes. Dans les deux cas l’oxydation des pièces se produit sous l’effet de la tension appliquée à celles-ci. Toutefois, les similarités entre les deux procédés se limitent à ces quelques considérations. Contrairement à l’anodisation, les électrolytes OMA sont uniquement alcalins, faiblement concentrés et ne contiennent ni composés CMR[6] ni polluants, ce qui fait de l’oxydation micro-arc un procédé propre tout en réduisant les coûts des traitements d’effluents. De plus, les pièces traitées par OMA sont moins sensibles à la préparation de surface préalable réduisant ainsi les étapes de traitement et par conséquent les installations nécessaires. L’OMA diffère également de l’anodisation par l’amplitude de la tension et du courant appliquée aux électrodes. Alors qu’en anodisation, la densité de courant est de l’ordre de quelques A / dm² (pour des valeurs de tension de l’ordre de quelques dizaines de volts), la densité de courant en OMA est de l’ordre de quelques 10 A/ dm² (pour quelques 100 V). La valeur élevée de la tension appliquée conduit au claquage localisé de la couche diélectrique en cours de croissance. Les micro-décharges qui en résultent sont alors les principales contributrices à la croissance de la couche d’oxyde. On peut noter enfin que l’OMA relève en grande partie de la physique des plasmas de décharge. L’oxydation se produit donc dans des conditions fortement hors d’équilibre thermodynamique favorisant une cinétique de croissance nettement plus rapide (~ 50 fois plus
élevée).
Les couches d’oxyde OMA sont généralement formées de deux sous-couches (figure 2) :
Une couche superficielle très poreuse riche en éléments provenant de l’électrolyte, constituée principalement d’alumine γ avec de l’alumine amorphe. Sa structure poreuse est due à des cycles de fusion et de solidification liés aux décharges électriques[5] ;
Une couche interne plus dense caractérisée par une structure compacte composée en partie de corindon (α-Al2O3) et qui peut contenir des éléments provenant de l’alliage à traiter, mais aussi des espèces de l’électrolyte.
Les couches élaborées par OMA consistent généralement en des oxydes cristallins[7] où coexistent plusieurs phases cristallographiques selon les matériaux et les conditions de traitement. Ces couches contiennent également des éléments de l’électrolyte (anions et cations) qui s’incorporent dans la porosité de la couche en cours de croissance sous l’effet des micro-décharges[6]. Ainsi, des micro ou nanoparticules ajoutées dans l’électrolyte peuvent également s’insérer et être piégées dans la porosité, conférant alors des propriétés exacerbées voire de nouvelles propriétés à la couche élaborée[7, 8].
Selon les fonctionnalités recherchées, il existe une gamme très étendue de particules pouvant être mises en suspension dans les électrolytes afin de les incorporer dans les couches OMA. On peut cependant identifier quatre principaux domaines d’applications (voir par exemple la revue de Lu et al.[7] sur l’incorporation de particules dans les couches OMA) :
stabilité chimique et protection contre la corrosion. Cette fonctionnalité est une caractéristique des couches OMA sans ajout de particules, ces dernières venant renforcer cette propriété barrière. Les particules ajoutées sont alors des oxydes métalliques (e. g. ZrO2, Al2O3, TiO2, CeO2), des nitrures ou des carbures ;
propriétés mécaniques et tribologiques. Il s’agit alors de conférer aux pièces traitées une dureté plus élevée, une tenue à l’usure améliorée, une diminution du coefficient de frottement ou encore de modifier la tension de surface (mouillabilité). On retrouve l’incorporation d’oxydes, de sulfures, de carbures, de nitrures, de métaux et métalloïdes et de matériaux carbonés ou organiques ;
applications biomédicales, qu’il s’agisse de biocompatibilité, de stérilisation, de propriétés antibactériennes voire d’ostéo-intégration et de reconstruction osseuse. Les particules métalliques (Ag, Cu) sont alors les additifs les plus utilisés pour des applications fongicides ou antibactériennes alors que des particules d’hydroxyapatite sont ajoutées pour répondre à des problématiques essentiellement d’implantologie ;
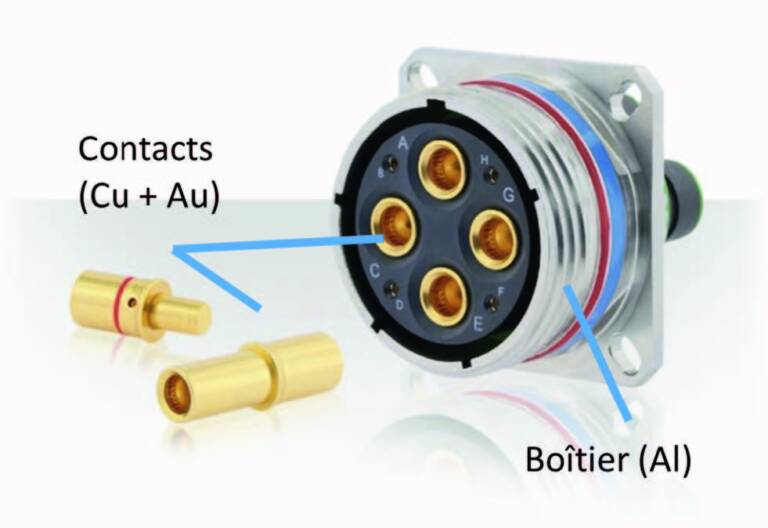
Figure 1. Image d’un connecteur circulaire
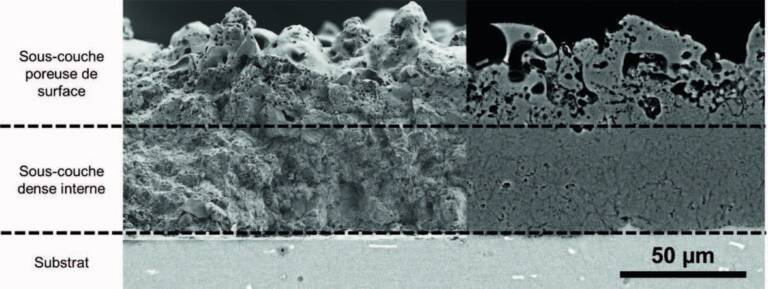
Figure 2. Images par microscopie électronique à balayage (MEB) d’une fracture (à gauche) et d’une coupe transverse (à droite) d’une couche OMA sur un alliage d’aluminium 6061.
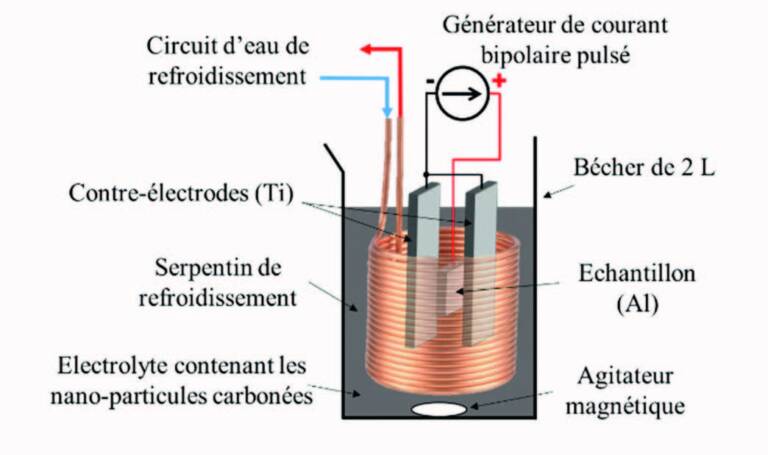

Figure 4. Images MEB de coupes transverses d’échantillons Al 1050 traités OMA avec des concentrations en noirs de carbone variant de 0 g/L (CB0) à 6 g/L (CB6). Les zones spongieuses (S-L) et les zones dites en plaques (P-L et DP-L) sont clairement visibles.[10]
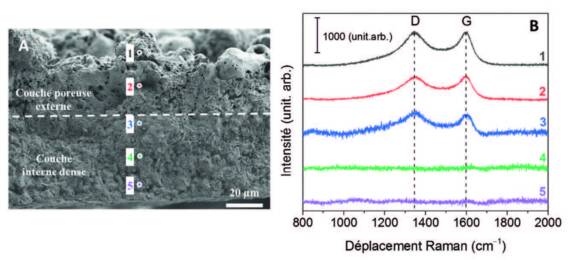
Figure 5. (A) Image MEB d’une fracture de la couche OMA réalisée avec une concentration en noirs de carbone de 6 g/L. (B) Spectres Raman (λ = 532 nm) enregistrés le long de la fracture (points 1 à 5) et montrant les bandes D et G caractéristiques des matériaux carbonés[10].
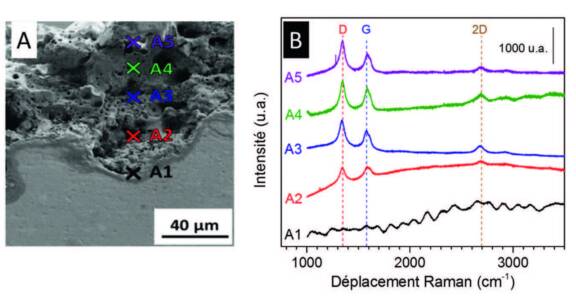
Figure 6. (A) Image MEB d’une fracture de la couches OMA réalisée avec une concentration en nanotubes de carbone de 3 g/L. (B) Spectres Raman enregistrés (λ = 532 nm) le long de la fracture (points A1 à A5) et montrant les bandes D, G et 2D caractéristiques des matériaux carbonés [11].
La connectique, un secteur à 15 milliards d’euros
Le domaine de la connectique englobe les solutions qui permettent de réaliser la connexion physique de liaisons électriques ou optiques, ainsi que la transmission de données. Le marché de la connectique, où la France dispose de compétences industrielles de premier plan, appartient au segment « composants » de la filière de l’électronique, socle industriel incontournable de la révolution numérique et de la transition énergétique.
Ce secteur représente aujourd’hui 15 Mds€ de chiffre d’affaires annuel en France, 1 100 entreprises pour 350 000 emplois directs et indirects. Les traitements de surface des boîtiers de connecteurs représentent 110 emplois chez les 4 premiers connecticiens français, membres du CMG et partenaires du projet CAMFRE (Amphenol Socapex, Radiall, Eaton-Souriau, TE Connectivity).
Les acteurs du projet CAMFRE
S. Cahen, C. Da Silva Tousch, S. Fontana, G. Henrion, C. Hérold, L. Magniez, J. Martin, C. Noël
Université de Lorraine, CNRS – Institut Jean Lamour. Campus ARTEM, F-54011 NANCY
L. Arurault, A. Hugou, P. Lenormand, J. Roche
CIRIMAT, Université de Toulouse, CNRS, UT3 Paul Sabatier, Bat CIRIMAT,118 Route Narbonne, F-31062 Toulouse 9
L. Cassayre, C. Laskar
LGC, Université de Toulouse, CNRS, INP, UT3 Paul Sabatier, ENSIACET, 4 rue Emile Monso, F-31342 Toulouse
R. Leroy, G. Trédan
Radiall
Rue Emile Romanet, F-38340 Voreppe
O. Gavard, R. Montpellaz Amphenol-Socapex
948 Promenade de l’Arve, BP 29, F-74311 Thyez
S. Demarthon, T. Pichot, L. Savary, Souriau-Eaton
89 route de Saint Hubert, F-72470 Champagné
M. Ladiré, F. Raoul
TE Connectivity 17 rue Lavoisier, F-27091 Evreux
applications liées au domaine de l’énergie. Ces applications restent assez marginales par rapport aux trois domaines précédents. On voit toutefois se développer depuis quelques années des travaux portant sur les couches OMA pour des applications à la photo-catalyse et la photoluminescence par ajout de particules métalliques (Ni, Cu, Mn, Fe, Co), d’oxyde ou de terres rares (Sm, Ce, Eu). L’ajout de particules de fer ou de cobalt confère des propriétés magnétiques aux couches d’oxyde ou peuvent jouer un rôle d’absorbant hyperfréquence. L’ajout de particules de silicium ou d’oxydes métalliques confère des propriétés de barrière thermique aux couches élaborées.
De cette littérature abondante sur l’incorporation de particules dans les couches OMA, quatre conclusions essentielles peuvent être tirées qui sont à l’origine du projet CAMFRE.
la plupart des études réalisées jusqu’alors sont focalisées sur les propriétés fonctionnelles des couches ainsi élaborées selon la nature des particules incorporées ; le rôle des particules sur la physique et la chimie du procédé OMA lui-même n’est pas abordé avec une profonde attention ;
la plupart des particules incorporées sont des oxydes, des nitrures ; seules quelques rares études traitent de l’incorporation de particules métalliques ou de particules carbonées, et aucune étude ne reporte l’influence de la variété allotropique de ces dernières ;
les mécanismes d’incorporation sont mal connus et toujours en débat dans la communauté OMA ;
de toutes les propriétés fonctionnelles abordées, quasiment aucune ne traite de la conductivité électrique.
Ainsi, l’originalité du projet CAMFRE réside dans l’appréhension de l’ensemble de ces problématiques au travers d’un projet unique couplant étude fine du procédé ; étude et caractérisation des particules en suspension ; caractérisation structurale ; texturale et physico-chimique des couches OMA élaborées et caractérisation fonctionnelle en termes de résistivité électrique, de résistance à la corrosion et de propriétés tribologiques.
Pour relever ces défis, plusieurs équipes de recherche industrielles et académiques, aux compétences complémentaires se sont associées au sein du projet CAMFRE :
les équipes plasmas – procédés – surfaces et matériaux carbonés de l’Institut Jean Lamour (UMR CNRS - Université de Lorraine), spécialisées en physique des procédés plasmas froids pour l’une, et en élaboration et caractérisation de matériaux carbonés pour l’autre ; l’équipe revêtements et traitements de surface du CIRIMAT (UMR CNRS – Université de Toulouse 3 – INPT) reconnue pour son expertise en traitements de surface par voie humide et en électrochimie ; l’équipe procédés et systèmes industriels du LGC (UMR CNRS – Université de Toulouse 3 – INPT), dont le domaine d’expertise porte notamment sur la modélisation thermodynamique pour la simulation des procédés ; quatre industriels du domaine de la connectique regroupés au sein du Connector Manufacturers’ Group (CMG), tous utilisateurs finaux pour des applications liées à la connectique : Amphenol-Socapex, Eaton-Souriau, Radiall et TE Connectivity.
Des premiers résultats encourageants
Les traitements OMA sont réalisés dans un bécher de 2 litres contenant un électrolyte alcalin composé de KOH + Na2SiO3 en faibles concentrations dans lequel sont dispersées des nanoparticules de carbone, noirs de carbone ou nanotubes de carbone selon les cas. L’électrode de travail (différents alliages d’aluminium : Al 1050 ou Al 6061 ou Al 2017) et deux contre-électrodes (Ti) électrodes sont immergées dans le bain électrolytique et alimentées par un générateur de courant bipolaire pulsé (Ceratronic®). Un serpentin (Cu), dans lequel circule de l’eau de refroidissement, assure le maintien de la température du bain à ~ 40 °C (fig. 3). Les détails complets du dispositif expérimental sont décrits dans les références[9, 10]. Nous avons pu montrer que la concentration en particules carbonées dans l’électrolyte influence notablement la morphologie des couches d’alumine ainsi élaborées qui présente une sous-couche externe d’autant plus spongieuse que la concentration en particules est élevée (fig. 4). La porosité des couches a ainsi pu être mise à profit pour y incorporer des nanoparticules. Toutefois, l’incorporation n’est pas totale et reste pour l’instant limitée à la couche externe poreuse, qu’il s’agisse d’incorporer des noirs de carbone (figure 5) ou des nanotubes de carbone (figure 6). Cette incorporation, partielle à ce jour, ne permet donc pas de modifier la conductivité électrique des couches par rapport à celles formés dans un électrolyte ne contenant pas de particules carbonées. De récents travaux ont cependant permis d’augmenter la porosité à travers la couche en modifiant le signal de courant utilisé pour le traitement, et des particules carbonées ont pu être observées en profondeur. Ces résultats sont encourageants et des pistes sont en cours d’exploration pour optimiser le procédé afin d’augmenter la quantité de particules dans ces pores avec pour objectif d’atteindre le seuil de percolation électrique et de rendre les couches d’alumine ainsi formées conductrices.
Conclusion
L’oxydation micro-arc avec addition de particules carbonées s’avère être un procédé prometteur pour pallier les contraintes environnementales auxquelles les traitements de surface actuels de l’aluminium, notamment le cadmiage passivé, font face tout en visant à satisfaire le cahier des charges des industriels de la connectique en matière de protection contre la corrosion, contre l’usure tout en assurant une continuité électrique des boîtiers de connecteurs. Les premiers travaux menés dans le cadre du projet CAMFRE (ANR21-CE08-0029) ont montré la faisabilité d’incorporer des particules conductrices (carbone) dans la porosité des couches OMA. Si cette incorporation reste encore limitée à la couche externe très poreuse, des pistes sont d’ores et déjà en cours d’exploration afin d’étendre ce type de morphologie des couches dites spongieuses à toute l’épaisseur de la couche. D’autres orientations sont également à l’étude au sein du projet, notamment avec l’incorporation de particules métalliques qui pourraient également améliorer la conductivité électrique transversale de telles couches OMA, élaborées sur boîtiers de connecteurs.
(1) Croissance d’AluMine à Faible Résistivité Electrique par oxydation micro-arc. ANR21-CE08-0029
(2) Registration, Evaluation, Authorisation and Restriction of Chemicals. Règlement européen n° 1907/2006
(3) Substance of very high concern – Subtances très préoccupantes
(4) European Chemicals Agency