Compatibilité tribologique des traitements thermochimiques et lubrifiants pour applications mécaniques
Yan-Ming CHEN[1], Pierre-François CARDEY[1], Pauline RONFARD[1], David CAZE[1], Stephane CHOMER[2], et Quentin CONTREPOIS[2]
[1] Cetim, Pôle Matériaux Métalliques et Surfaces, Laboratoire Tribologie. [2] Thermi-Lyon
La lubrification est la méthode la plus utilisée pour augmenter l’efficacité énergétique d’un système mécanique en réduisant le frottement. Si les régimes avec de grandes épaisseurs de film sont bien maîtrisés aujourd’hui, ceux à faible épaisseur, comme les régimes limites et mixtes, ne le sont pas encore, notamment pour les mécanismes réactionnels entre des additifs et la surface. Des interactions entre lubrifiants liquides et surfaces solides peuvent être positives en formant un film d’adsorption adhérant qui protège la surface ou négatives en réduisant l’adhérence du lubrifiant à la surface [1 et 2].
L’application des nouveaux matériaux et des traitements de surface est un moyen efficace pour lutter contre la corrosion et pour réduire le frottement et l’usure. Mais ces matériaux et traitements peuvent modifier les réactions physicochimiques avec les additifs présents dans les lubrifiants, ce qui modifie le comportement au frottement. Ces préoccupations sont partagées par de nombreux industriels comme les fabricants de transmissions mécaniques, d’équipements agro-alimentaires, mais également des fournisseurs de lubrifiants.
Afin d’améliorer la fiabilité de ces pièces en frottement, le Cetim a mené une étude pour évaluer la compatibilité entre les matériaux, les traitements de surface et les lubrifiants. Cette étude permet de mieux comprendre les mécanismes d’interactions entre les surfaces de contact et les lubrifiants en régime mixte. Ainsi, le centre technique pourra fournir aux industriels des éléments de sélection et d’optimisation du couplage entre le lubrifiant, les matériaux et les traitements de surface.
1. Matériaux, traitements et lubrifiants testés
Pour avoir une bonne représentativité des applications industrielles, un acier faiblement allié type 42CrMo4 est sélectionné comme matériau de référence. Le contre-matériau est un acier de roulement 100Cr6 (tableau 1).
L’acier 42CrMo4 est testé dans l’état trempé dans la masse (trempé à l’huile à 840 °C. revenu à 675 °C pour un Rm de 1000 MPa (30 HRC) à coeur.
L’acier 100Cr6 est testé dans l’état trempé dans la masse (trempé à l’huile à 860 °C. revenu à 170°C pour une dureté de 62-64 HRC).
La plaque en 42CrMo4 après le traitement thermique subit quatre types de traitements en surface :
1. une nitro-carburation de type e poreux avec une couche de combinaison de l’ordre de 5 à 10 µm ;
2. une nitro-carburation du même type avec une post-oxydation ;
3. un dépôt de DLC type a-C :H par PE-CVD de l’ordre de 2 à 3 µm ;
4. un dépôt de CrN par PVD magnétron de l’ordre de 2 à 3 µm.
La microstructure des matériaux-traitements testés est présentée dans la figure 1.
Pour mieux représenter les applications dans l’industrie mécanique, quatre lubrifiants ont été sélectionnés. Les principales caractéristiques se trouvent dans le tableau 2 :
Deux huiles de transmission nommées respectivement huile Lub A, destinée à la lubrification des turbines, et l’huile Lub B, utilisée dans les équipements agricoles ;
Deux graisses nommées respectivement Lub C, une graisse alimentaire et classée NSF H3 (homologation pour le contact direct avec les aliments, et la graisse multiusage nommée Lub E), une huile minérale chargée d’additifs anti-usure et extrême pression.
2. Conditions des essais
Les essais ont été effectués sur le tribomètre alternatif Plint TE-77 avec la configuration bille / plan (figure 2). La bille en acier 100Cr6 frotte en mouvements alternatifs sur une plaque traitée. Cette configuration évitera des dispersions des résultats dues aux défauts d’alignement des éprouvettes[3]. Les conditions d’essais pour tester la compatibilité de ces traitements avec les lubrifiants sont les suivantes :
Bille 100Cr6 / plaque à tester ;
Température : 20°C ;
Charge appliquée : 200 N (P Hertz 2743 MPa, D contact 373 µm, rapprochement : 7 µm) ;
Fréquence : 10 Hz ;
Course : 10 mm ;
Durée d’essais 1 000 s.
Dans le but de mettre en évidence les interactions physicochimiques possibles à l’interface du contact, le mode de lubrification choisi est « égoutté ». En effet, dans le cas des huiles, les plaques revêtues sont trempées dans un bain puis égouttées pendant dix minutes, les excédents sont ensuite essuyés. De même, dans le cas des graisses, un fin film est étalé sur la plaque afin d’assurer la lubrification du contact. On note que 8 mg de graisse permettent d’avoir un film mince de 10 µm.
Deux essais ont été réalisés pour chaque lubrifiant. Le coefficient de frottement et le taux d’usure sont mesurés pendant les essais. Pour chaque traitement, des essais sont également effectués à sec afin de les comparer aux performances en milieu lubrifié. Des analyses post-mortem, telles que les observations des traces d’usure sur les billes et les plaques, sont réalisées à l’aide d’un profilomètre
3. Résultats des essais
3.1 Évolution du coefficient de frottement
Les figures 3 à 7 présentent les résultats obtenus avec les cinq configurations d’essais, à sec et avec les quatre lubrifiants.
Dans le cas des essais à sec, on note deux types d’évolutions :
1 : nitrocarburation avec et sans oxydation avec une évolution lente de 0.4 à 0.5 ;
2 : dépôts DLC et CrN avec un pic de 0.8-0.9 au début, suivi par une chute brutale avant une montée lente de 0.6 à 0.7.
Pour les cas de nitrocarburation, on note plus de perturbations pour le traitement sans oxydation. Le niveau est également plus faible en début d’essai pour le traitement avec oxydation.
Dans les cas des essais lubrifiés, on note trois types de comportement :
1 : Un coefficient de frottement faible (0.1) et stable tout le long des essais pour les lubrifiants B et C.
2 : Un coefficient de frottement variable et élevé avec le CrN pour l’huile A.
3 : Un coefficient de frottement très variable selon le type de matériaux/traitement avec la graisse E.
Avec l’huile A, le comportement du CrN est dispersé, avec un niveau élevé proche de celui à sec pendant 550 secondes avant la chute pour un essai, une petite montée pendant 100 secondes seulement pour l’autre. Cette dispersion semble importante, mais elle est assez répétable pour montrer l’incompatibilité du CrN avec l’huile A par rapport aux autres matériaux et traitements.
Pour la graisse E, on retrouve certains comportements similaires avec ceux à sec, un coefficient de frottement élevé pour CrN. L’oxydation joue un rôle très positif pour réduire le coefficient de frottement par rapport à la nitrocarburation sans oxydation. Mais le comportement du DLC est très différent de celui de CrN avec un niveau de coefficient de frottement très faible (0.15) tout le long de l’essai sauf dans les dernières 100 secondes pour l’un des deux essais. Cette montée correspond probablement à l’usure complète de la couche. Le DLC est donc très compatible avec la graisse E à condition que le dépôt ne soit pas complètement usé.
3.2 Usure de la bille et de la plaque
La figure 8 montre le diamètre de la trace d’usure de la bille. On note que l’usure de la bille est plus importante à sec qu’à l’état lubrifié.
Dans le cas à sec, l’usure des billes est plus faible avec les traitements de nitrocarburation qu’avec les dépôts minces. Pour la nitrocarburation, l’oxydation a permis de réduire encore l’usure de la bille. Comme ce paramètre indique l’abrasivité de la plaque vis-à-vis de la bille, on constate que l’oxydation rend la plaque nitrocarburée moins abrasive. Cette réduction de l’abrasivité est probablement due à la microstructure des oxydes, moins dure, moins dense et plus friable par rapport aux carbures et nitrures.
Dans le cas des lubrifiés, l’usure est plus faible avec l’huile B et la graisse C qu’avec l’huile A et la graisse E. L’usure est toujours importante avec CrN.
La figure 9 montre l’aire de la trace d’usure de la plaque. On note que l’usure de la plaque est plus importante avec DLC et CrN à sec et avec CrN dans la graisse E.
Si on dilate l’échelle de l’axe vertical (figure 10), on peut noter que l’usure de la plaque nitrocarburée avec l’oxydation est dix fois plus faible que celle de la plaque sans oxydation à sec. L’usure de cette plaque est la plus faible également dans les cas lubrifiés. Le rôle positif de la couche d’oxyde sur la tenue à l’usure dans le cas lubrifié peut être non seulement lié à la microstructure de l’oxyde comme dans le cas à sec, comme une meilleure rétention de l’huile grâce à la porosité, mais également lié à des interactions physicochimiques avec les lubrifiants, des réactions avec des acides gras dans les additifs.
4. Discussions
On note que le coefficient de frottement à sec avec les plaques revêtues de DLC et de CrN est de l’ordre de 0.6 – 0.7 après une montée très rapide. La pression appliquée de 200 N sur la bille de 10 mm de diamètre entraîne une pression de Hertz de 2743 MPa. Cette pression provoque déjà une déformation élastique verticale de 7 µm. Ces fortes contraintes de contact, plus les contraintes de cisaillement générées par le frottement, provoqueraient des endommagements très rapides de ces couches dans les conditions à sec. C’est la raison pour laquelle le coefficient de frottement monte très rapidement pour atteindre le niveau 100Cr6 / 42CrMo4 sans dépôt.
L’application des lubrifiants, notamment de l’huile B et de la graisse C, réduit le coefficient de frottement à un niveau de 0.1, ce qui confirme l’efficacité du film d’adsorption, donc une très bonne compatibilité de ces traitements avec les lubrifiants.
Les résultats des essais montrent que l’usure avec les quatre lubrifiants est toujours plus faible que celle à sec avec la nitrocarburation et le couple nitrocarburation + oxydation, ce qui confirme une bonne compatibilité entre ces lubrifiants et la nitrocarburation.
Mais l’usure avec la graisse E est très similaire à celle à sec avec le dépôt CrN, alors que cette graisse a permis de réduire l’usure de la plaque avec le DLC et avec la nitrocarburation. On peut donc en déduire que le film protecteur formé à la surface du CrN est peu efficace contre l’usure, même si on ne peut pas affirmer qu’ils sont incompatibles.
5. Conclusion
Pour ce qui concerne les lubrifiants, il est observé que le coefficient de frottement reste bas et stable avec l’huile B et la graisse C quels que soient les traitements ou dépôts testés. L’huile A présente un coefficient de frottement élevé uniquement lorsqu’elle est associée au dépôt de CrN. En ce qui concerne la graisse E, des niveaux de frottement très faibles sont constatés avec le DLC et la nitrocarburation oxydée. De plus, la résistance à l’usure de la plaque et de la bille est moins élevée avec l’huile B et la graisse C, tandis que l’usure est plus marquée avec le dépôt de CrN en association avec l’huile A et la graisse E.
En ce qui concerne les matériaux et les traitements, il est important de noter que la nitrocarburation oxydée s’avère particulièrement efficace pour réduire le coefficient de frottement et l’usure, y compris dans des conditions de lubrification limitée. De plus, le dépôt de DLC présente une meilleure compatibilité avec l’huile A et la graisse E par rapport au dépôt de CrN.
Ces résultats confirment l’efficacité notable de l’application de la nitrocarburation, en particulier lorsqu’elle est oxydée, pour réduire le coefficient de frottement et l’usure. De plus, ils mettent en évidence une performance supérieure de l’huile B et de la graisse C par rapport à l’huile A et à la graisse E.
Ces résultats réaffirment également la sensibilité du test par rapport aux types de lubrifiants et de traitements, démontrant ainsi que ce protocole de test est parfaitement adapté pour évaluer la compatibilité des traitements thermiques et thermochimiques avec différents lubrifiants.
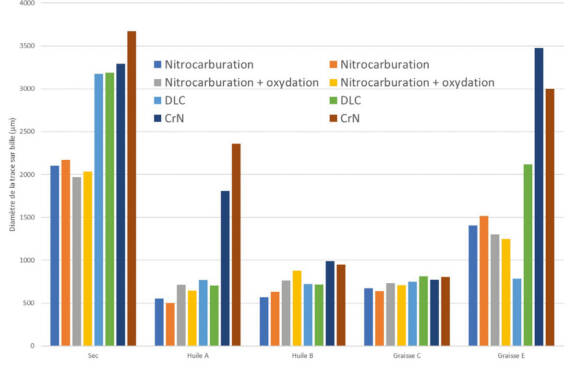
Figure 8 : Diamètre de la trace sur bille en µm.
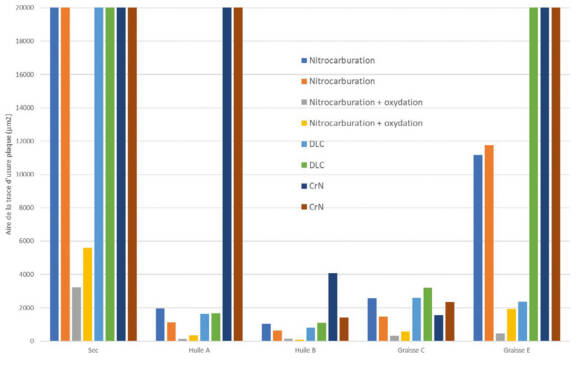
Figure 10 : Zoom sur l’aire de la trace d’usure de la plaque.

Tableau 1
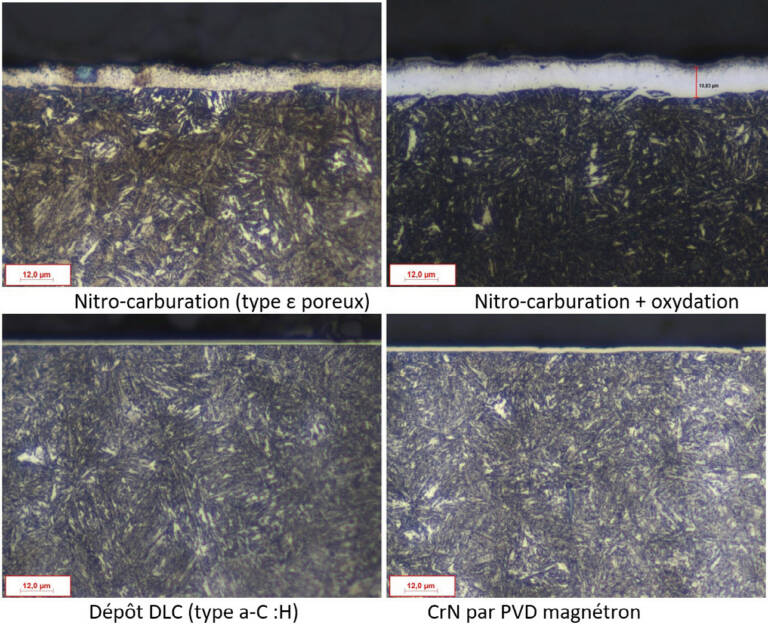
Figure 1 : vue en coupe de la structure traitée.
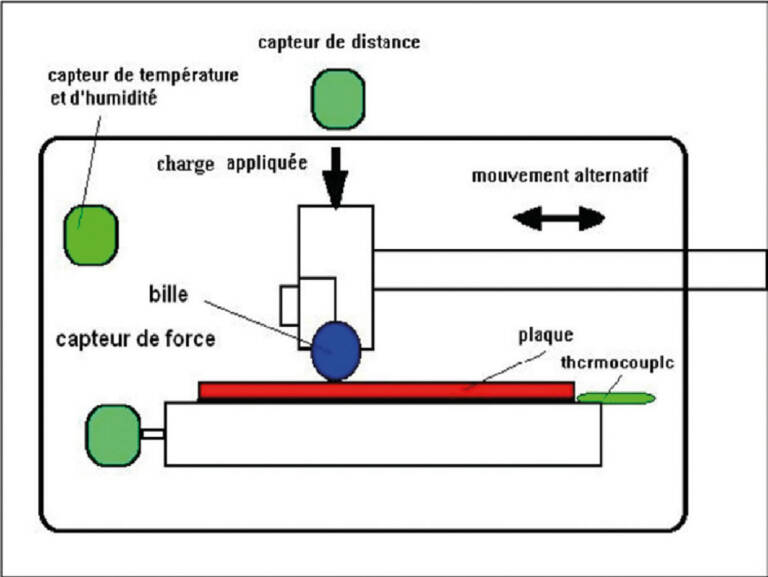
Figure 2 : schéma du tribomètre TE-77.
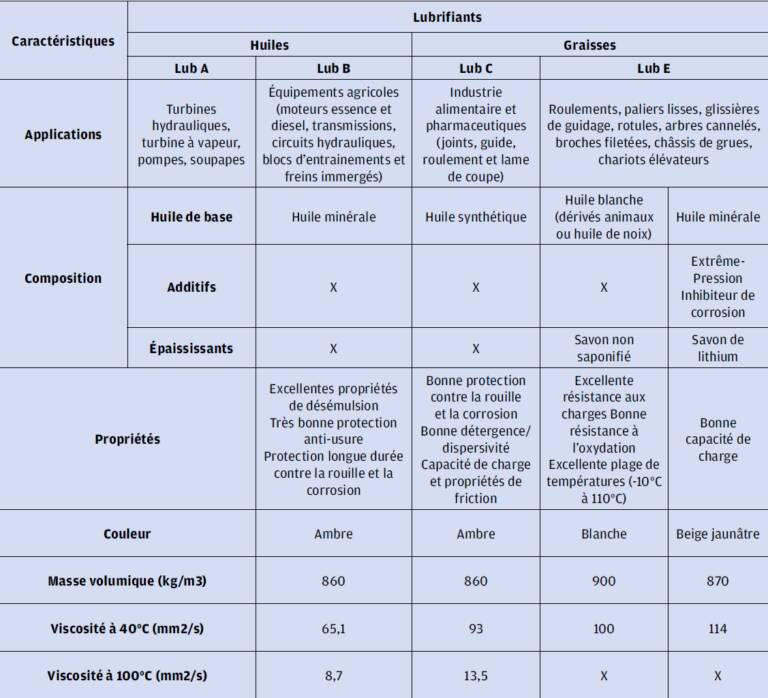
Tableau 2 : caractéristiques des lubrifiants testés.
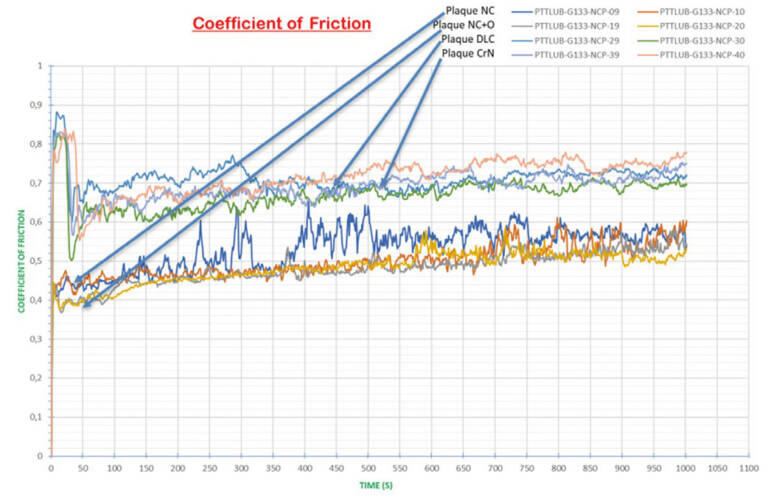
Figure 3 : évolution des coefficients de frottement à sec.
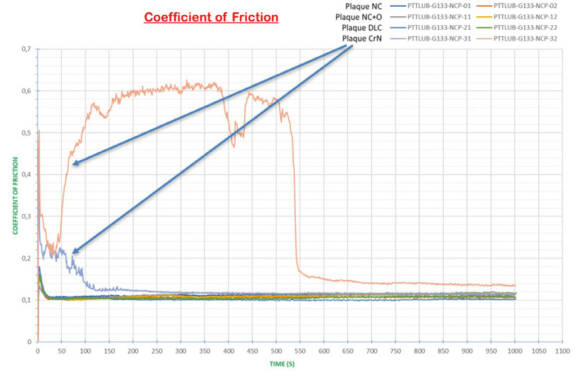
Figure 4 : évolution des coefficients de frottement en présence du Lub A.
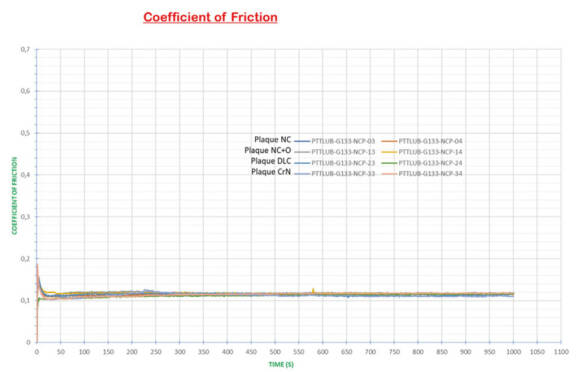
Figure 5 : évolution des coefficients de frottement en présence du Lub B.
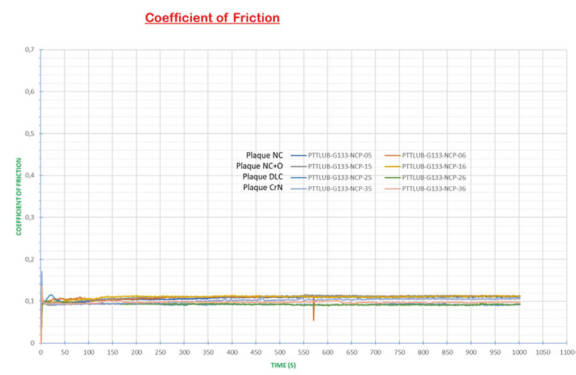
Figure 6 : évolution des coefficients de frottement en présence du Lub C.
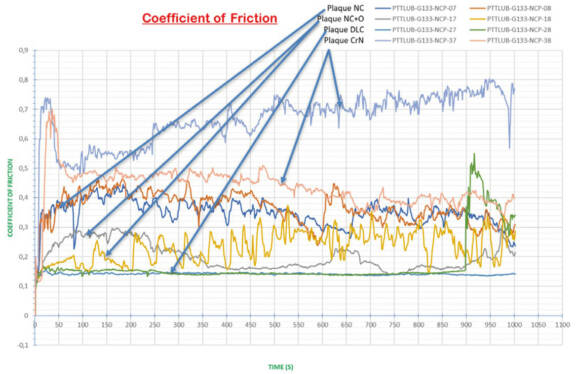
Figure 7 : évolution des coefficients de frottement en présence du Lub E.
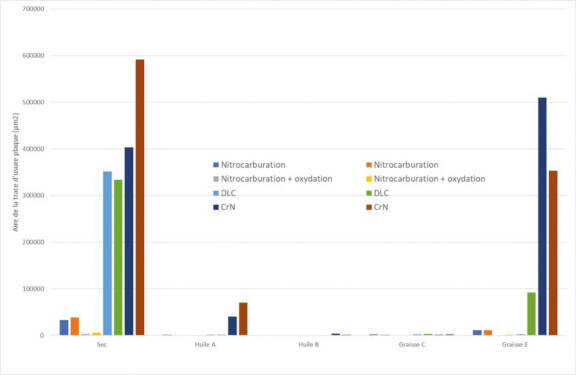
Figure 9 : Aire de la trace d’usure de la plaque.